Optimized, automated stacker reclaimers deliver exceptional operational efficiency
We offer one of the most comprehensive stacker reclaimer portfolios on the market. Our customer-driven automated storage solutions can be exactly tailored to meet the needs of stockyards, woodyards and dry bulk storage facilities.
Bruks Siwertell delivers stacker reclaimers that form linear, semi-circular and fully circular piles in a range of sizes and capacities. Each stacker reclaimer has an optimized design taking into consideration the material being stored and the density and angle of repose. The geometry of circular stacking means that significant volumes of materials can be stored at a much lower cost than linear systems. However, when mega volumes are needed, the extent and expandability of a linear system cannot be beaten.
SETTING THE INDUSTRY STANDARD FOR AUTOMATED STORAGE
Woodyards supplied by Bruks Siwertell are seen as the industry model for high-volume wood processing, expertly and safely managing vast quantities of wood chips and various other organic materials. One of our most popular automated storage solutions is the Bruks circular blending bed stacker reclaimer (CBBSR), which is helping operators keep pace with growing market demands for containerboard and renewable energy.
The Bruks CBBSR lays down successive layers of material in a continuous 360-degree rotational pattern using a stacking conveyor that pivots through a complete circle. At ground level, a reclaim bridge moves into the pile with a harrow simultaneously agitating and fluidizing the material on its reclaiming face. A large diameter screw catches all the falling material and transfers it to the center where it drops onto the reclaim belt. This passes under the pile and emerges beyond its edge, leaving the base undisturbed.
They have a true first-in first-out (FIFO) mechanism, with the oldest material in the pile always being reclaimed first and blending reducing any variation to a minimum. For organic feedstock, this is key to preventing material degradation and the risk of ‘hot spots’ from microbial action.
STACKER RECLAIMERS OFFER SUSTAINABILITY BENEFITS
Automated storage systems have a fraction of the carbon footprint of a manually managed pile and offer much improved emissions control. These environmental gains stem from eliminating the continuous use of diesel-powered machines used to manage the piles. Fugitive dust emissions are also reduced in comparison to them, as the gentle nature of stacker reclaimers, such as CBBSRs, mean that they do not ‘stir up’ fines and dust.
All our stacker reclaimers are designed for maximum wear life. For example, the harrow and carriage are mounted on a robust rail system located on top of the bridge, allowing the unit to reliably travel alongside the pile. The bridge is fitted with a dedicated control room that houses critical electrical engineering components. Stacker reclaimers are fitted with similar insulated motor control units that have an isolated cabinet complete with industrial environmental controls. Control rooms are shipped to site pre-tested and fully assembled.
HELPING OPERATORS SELECT THE MOST SUITABLE SOLUTION
Automated stacker reclaimers all follow the same principles of piling and then retrieving dry bulk materials for onward conveying in a very efficient, controlled way. They can also blend material, which is particularly important for organic commodities such as wood chips, bark or sawdust, to reduce fiber losses from microbial action and heat build-up in the pile.
Blending is also important to consider when raw material sources that feed the storage pile are different in some way, such as size distribution or moisture content. Manual pile management keeps these different materials together on the pile so they are reclaimed sequentially.
Automated storage, pile stacking and reclaiming produces layers of materials on the pile, then effectively blends them as they are reclaimed. Spikes of variability are smoothed as the materials are homogenized.
We deliver stacker reclaimers that can handle a wide range of materials from aggregates, coal and iron ore to grains, sulfur and wood products. With so much choice, it can be difficult to know how to optimize a stacker reclaimer solution that perfectly meets your needs. Our experts ensure that the combination of stacking, storage and reclaiming technology that you select works seamlessly together and delivers the highest possible operational efficiency for the lowest possible lifecycle costs.
COST BENEFITS ENSURED
Automated storage has brought considerable benefits to operators of woodyards, stockyards and dry bulk storage facilities. Fully automated stacker reclaimers minimize the number of personnel-hours required for daily operations, delivering significant cost savings. They have a unique design that improves inventory control, as well as maintaining consistent quality. The also reduce material degradation by eliminating the use of mobile machines damaging sensitive materials as they drive over the pile.
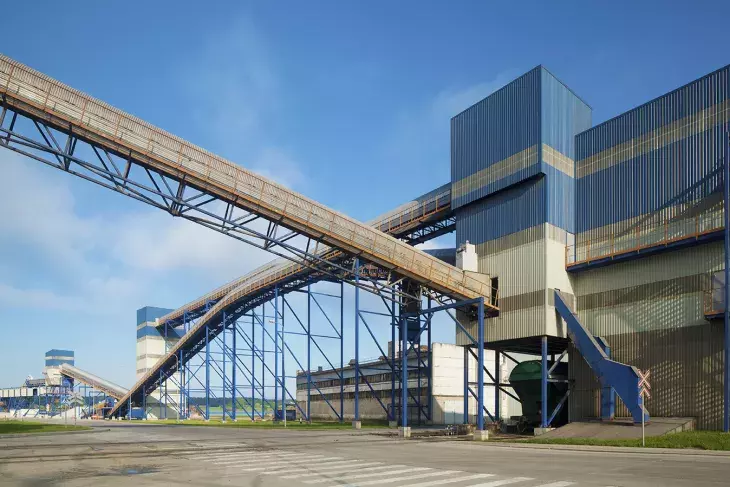
Complete bulk terminal solutions
Bruks Siwertell designs solutions for complete bulk terminals. We will work closely with you to make sure our solutions fit with your specific needs. Our high-capacity, high-efficiency unloaders, loaders, conveying systems and stacking and reclaiming systems stand to provide you with substantial cost savings from reduced operating times.