Next-generation Service agreements
Tailored to meet your needs
Our commitment to customer service means that we stand by our deliveries throughout their lifetimes. By selecting the support elements that you require, our planned service agreements are tailored to meet your needs. They are applicable for dry bulk handling equipment including ship unloaders, loaders, conveying systems and terminal operations.
Inspections
Inspections are a critical first step in maintaining asset performance. Their purpose is to identify any problem areas and damaged parts, and improve overall operation. Our experts check wear patterns, any abnormalities are further investigated, and remedial measures are suggested.
Inspections include dialogues with an expert, machine performance evaluation of logged historical data including capacities, availability, and downtime, and the consideration of previously carried out maintenance work. Following each inspection, a report is made available. One-off, on-demand inspections are available upon request.
Mechanical inspections are centred on the machine’s condition and how the asset can be fine-tuned to best meet operator needs. During an inspection visit, all essential unloader functions and movements are tested, along with sequences for the conveyor system. A review of any maintenance undertaken by the operator and the alarm history is also carried out, as well as an analysis of recurring alarms and trends.
Main features:
• OEM expertise
• Comprehensive inspection report
Within this service level, the machine’s electrical and instrumentation systems are checked. This includes motors, electrical power and signal supply, radio system, cables, and sensors. Systems are assessed for condition and also fine-tuned to best meet operator needs. Electrical inspections include a test-run during operation, the assessment of limit switches, and a visual and sound condition check of the main drives.
Main features:
• Certified third-party expertise
• Comprehensive inspection report
During an inspection, our specialist surveyor will carry out a visual assessment of the steel structure, with a detailed focus on stress-exposed areas. Any sections that have suspected damage can be checked using a dye penetrant. If further non-destructive testing is required, such as ultrasonic techniques and/or magnetic particle tests, Bruks Siwertell will arrange for additional specialist involvement. This might include testing weld joints, outer and inner hinge shafts, and the luffing/pendulum hydraulic cylinder attachments.
Main features:
• Certified third-party expertise
• Comprehensive inspection report
The designed capacity of your ship unloader can be different from the one it currently achieves. Our experts can study your unloading process and provide information on how efficient your unloading process is, and what can, and should be done, to increase this.
Main features:
• Capacity data & analysis
• Improvement recommendations
Customer undertakings (Requirements for Live unloading efficiency study)
• Ensure available ship in harbour for Live unloading
Main benefits
Enhanced operational outlook and equipment knowledge
Performance improvements
Sound decision-making
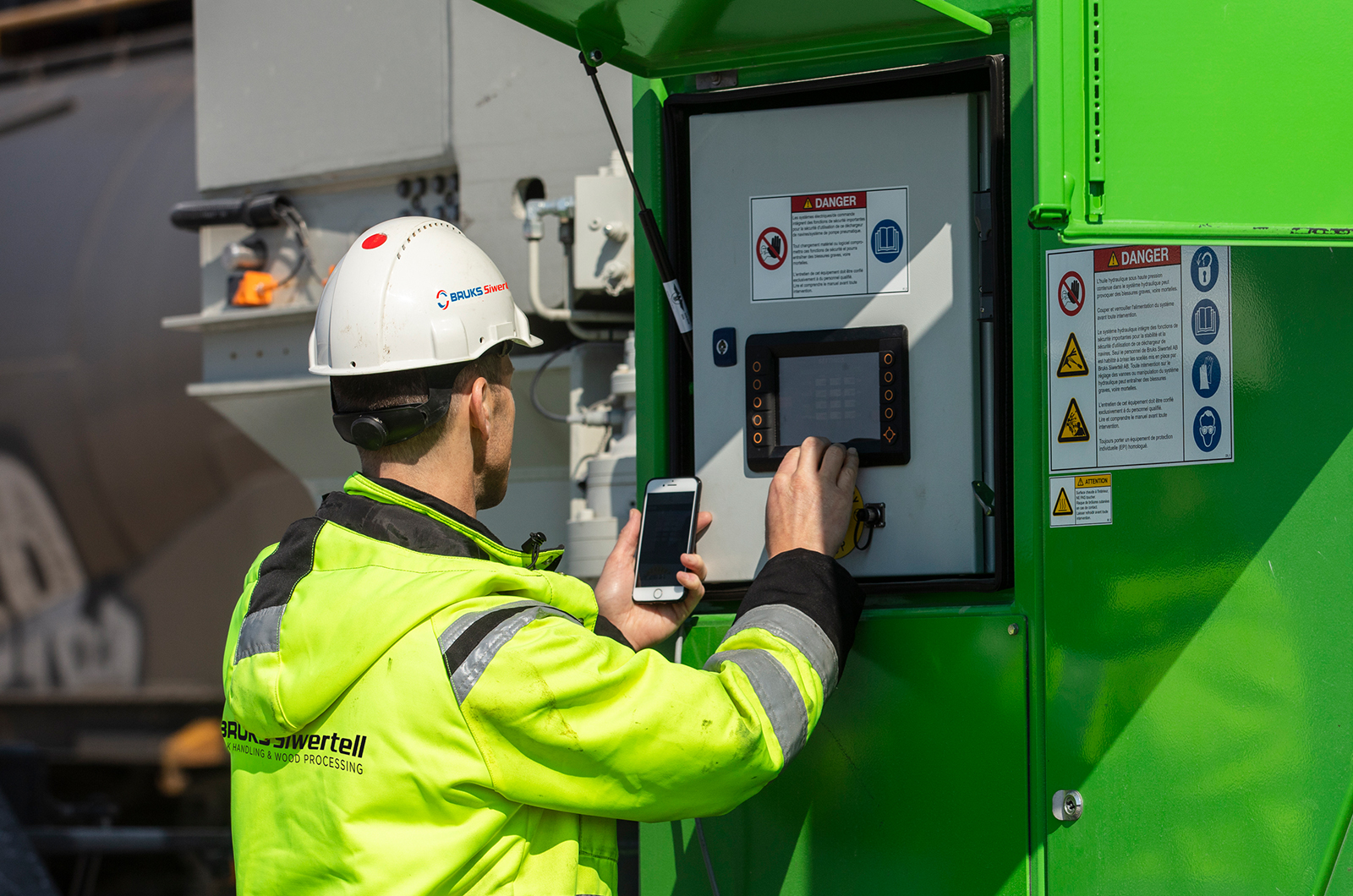
Main benefits
Enhanced operational outlook and equipment knowledge
Performance improvements
Sound decision-making
Main benefits
Enhanced operational outlook and equipment knowledge
Performance improvements
Sound decision-making
Maintenance
A proactive approach to maintenance is key to ensuring long-term equipment reliability and safety, while minimizing through-life operational costs. Our experts can provide guidance on the best approach to service, and offer tailored recommendations for maintenance, spare parts and inventory management, and remedial measures.
Our technicians supervise pre-agreed proactive and preventative maintenance tasks with experts and personnel of your choice. A supervising engineer or surveyor will make sure that the work is performed to an optimal level by guiding contractors. After the maintenance work has been completed, a maintenance report is issued with detailed descriptions of the actions taken. The report entails all, if used, spare parts and may provide recommendations for further action.
Main features
• OEM expertise guidance
• Comprehensive report
• Coordination support
This approach is ideal for proactive, preventive, or corrective measures. Tailormade scheduling of maintenance planning for the asset or terminal is calculated and timetabled according to equipment use, including the number of running hours and cargo handled, and equipment condition. All scheduling is arranged in close cooperation with the owner and operating personnel.
Main features
• Maintenance and shut-down planning
• OEM competence
Available upon special reguest. Our maintenance management program takes full responsibility for maintenance activities and personnel allocation. As a strategic partner for outsourcing, you can focus on your core business, while we ensure the highest levels of safety, reliability and availability. Our input maximizes equipment service lives, and delivers optimized productivity, and profitability of your terminal.
Main features
• Maintenance scheduling
• OEM competence
• 24/7 assistance with local presence with pre-defined response time
• Corrective maintenance
Main benefits
Reduced costs
Planned, predictable service
Continuing equipment performance
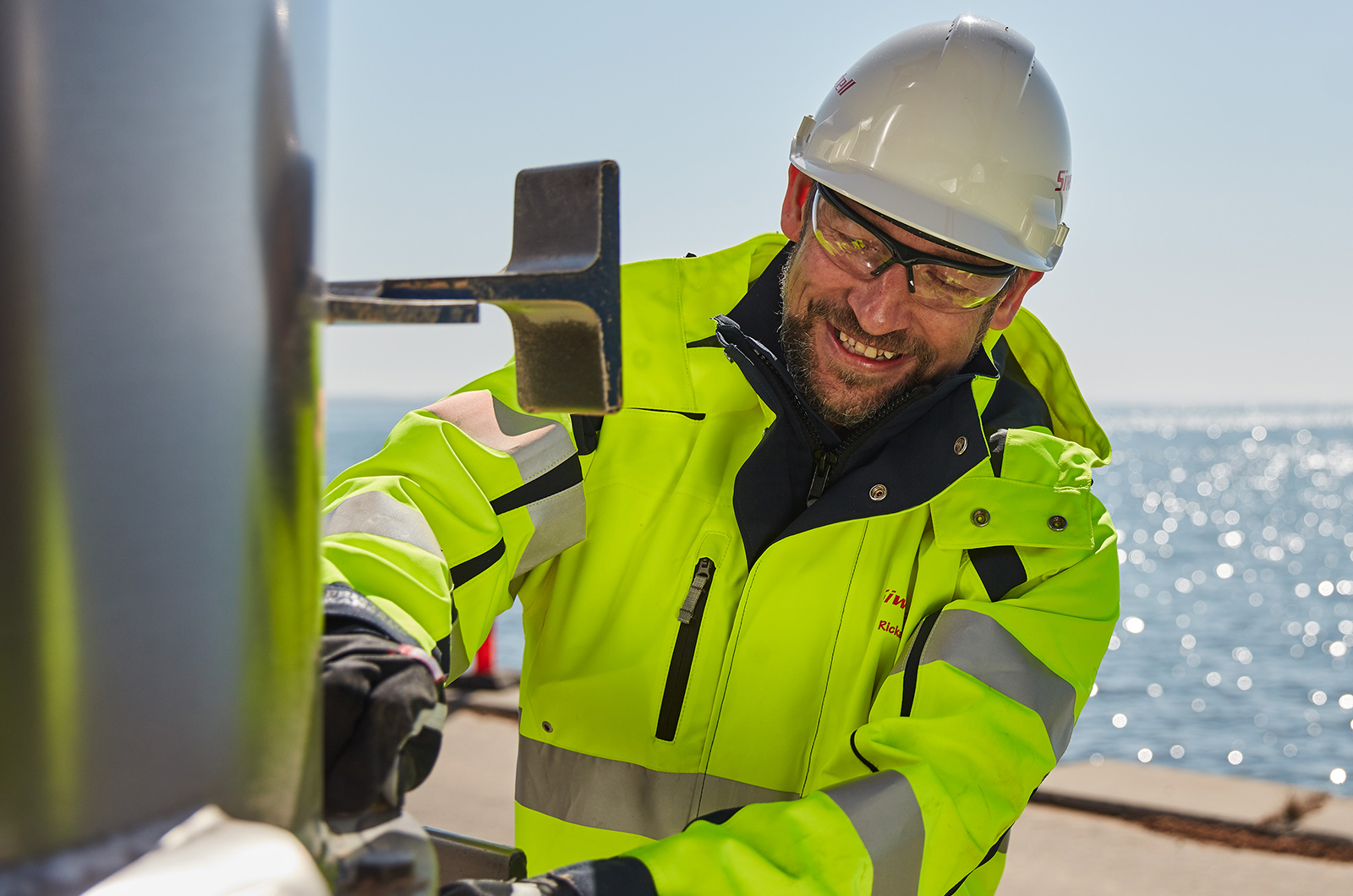
Main benefits
Reduced costs
Planned, predictable service
Continuing equipment performance
Main benefits
Reduced costs
Planned, predictable service
Continuing equipment performance
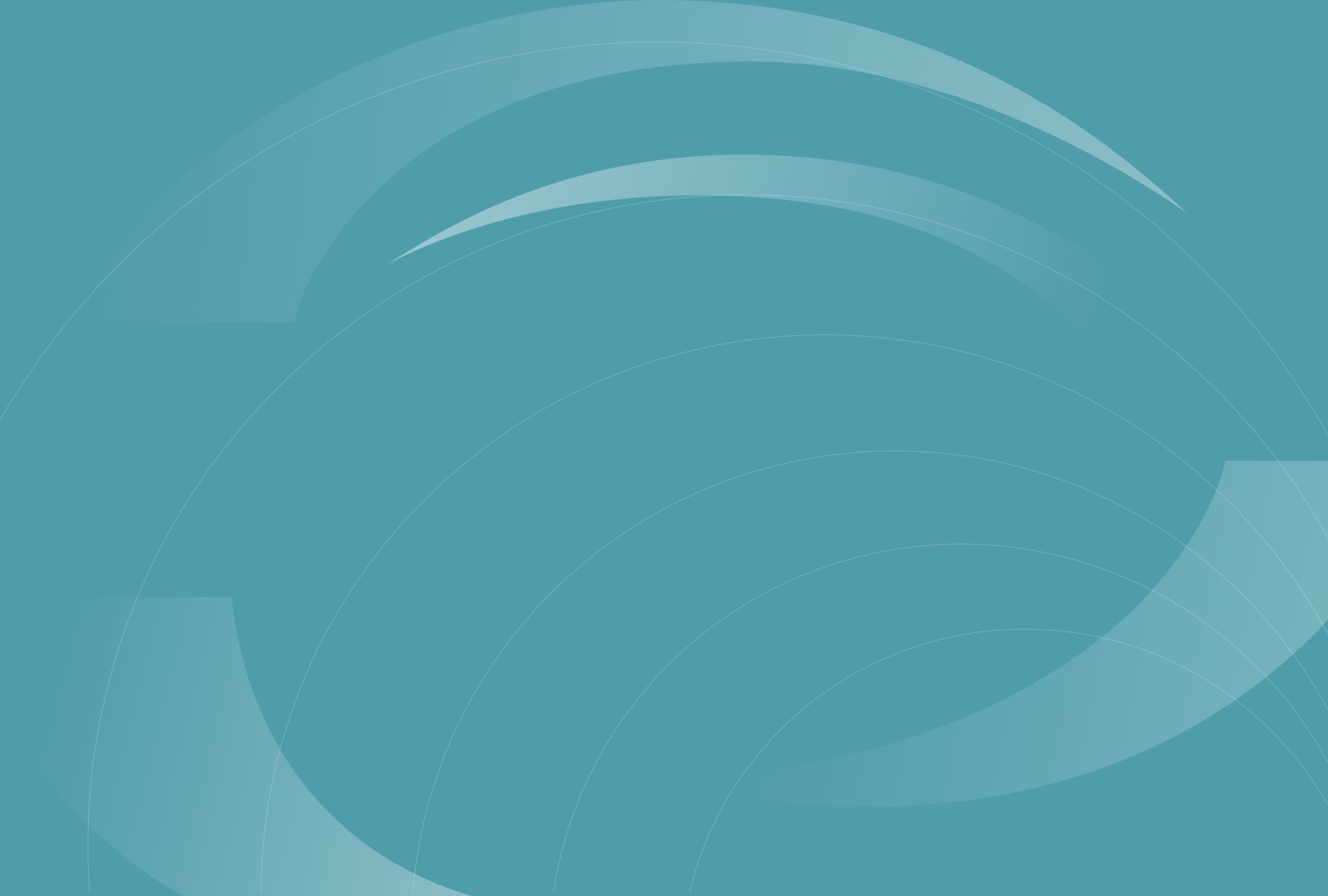
Our commitment: to support you with service, maintenance and related administration, so that you can focus on your core business.Daniel Frostberg, Service Director, Bruks Siwertell
Our commitment: to support you with service, maintenance and related administration, so that you can focus on your core business.Daniel Frostberg, Service Director, Bruks Siwertell
Remote assistance
We are at your service anywhere, anytime. Remote assistance enables us to use today’s advanced technologies to deliver service support to you whenever you need it. Remote support often removes the need to travel to your site, enabling us to more rapidly provide assistance, increasing equipment uptime and securing the performance of ongoing operations.
Case consultation provides global access to a network of dry bulk handling experts and specialists, who offer guidance for case resolutions. Our expert consultants handle both urgent and strategic cases. They can assess current performance against target performance in specific key areas, such as health and safety, productivity, quality, reliability, and efficiency, and identify underperforming areas, with root-cause analysis. Drawing upon vast technological and engineering experience, our experts then provide tailored recommendations for improvements to continuously enhance your terminal’s performance.
Main features
• Case management
• Direct access to Bruks Siwertell departments
Access to Bruks Siwertell service department 24/7/365 via a telephone hotline for the initiation of case management, and when possible, the provision of guidance for case progress.
The case hotline service is aimed at keeping your terminal running, with minimal downtime and the swift handling of unforeseen, urgent problems. To aid swift resolutions, our specialists are available to support you at the first point of contact.
Main features
• Case initiation 24/7/365
• Case management
Main benefits
Reduced downtime
Rapid troubleshooting
Expert guidance
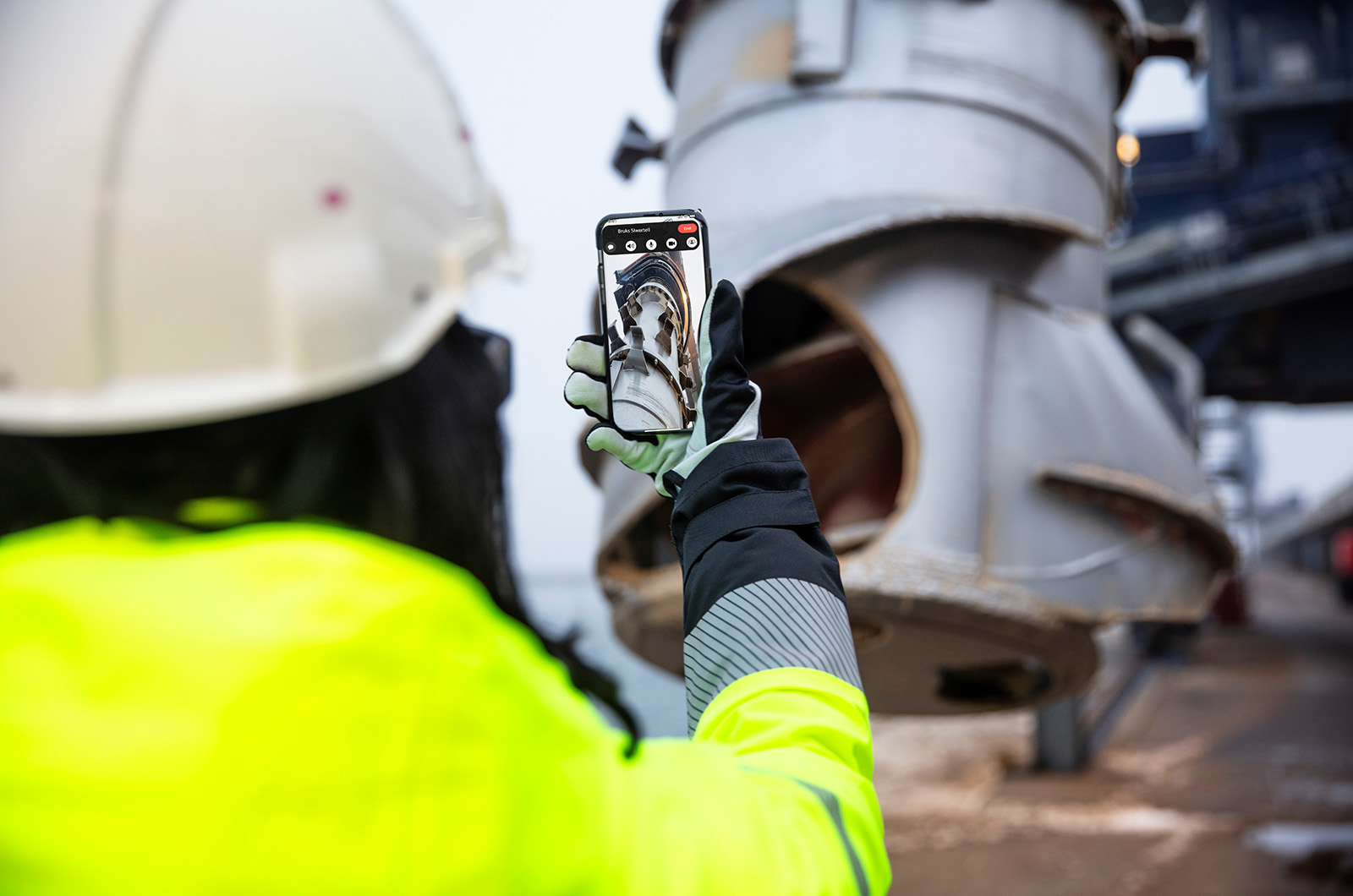
Main benefits
Reduced downtime
Rapid troubleshooting
Expert guidance
Main benefits
Reduced downtime
Rapid troubleshooting
Expert guidance
Siwertell Smartview
Our advanced digital technology grants you unlimited, global access, via web browsers, to your asset’s data. With a private log-in to Bruks Siwertell’s Industrial Internet of Things (IIoT), Siwertell SmartView, users are able to view, store and track live and historic data. Siwertell SmartView enables the analysis of asset and port terminal performance, reliability and efficiency, providing insight into stoppages, availability and volumes of cargo handled. Accurate, expert evaluations mean that improvements can be identified and solutions offered.
Please note: these elements provide an overview of potential data points. The availability of explicit data is always dependent on, and defined by, the capabilities of specific equipment.
Live data
Monitor a live operation from anywhere. With an account and internet access, it is possible to monitor many real-time operational elements such as capacity trends, stoppages and estimated completion times.
Performance analysis
Quick access and review. Advanced systems enable access to key performance indicators such as equipment capacity, efficiency and availability.
Historical data
Direct access to historical data. With access to historical data, which details the types and sizes of vessels handled, it is possible to assess operational performance and conduct a shift analysis to identify bottlenecks and potential maintenance requirements.
Report generation
Export data to Excel. Various data points can be exported, generating tailored weekly or monthly reports on the terminal’s performance. These can highlight parameters such as availability, efficiency, stoppages, and volumes of cargo handled.
System functionality
Instant access to a view of a live operation and the status of key components, as well as performance.
Component monitoring
Monitor component performance and health. Component monitoring enables predictive maintenance and forward planning. Equipment data and components that can be monitored include: bearing temperatures, hydraulic systems, gearboxes, functionality of dust filters, and power consumption.
Remote assistance
A number of assistance capabilities are available using the remote support function. Services are instigated by the customer and include: troubleshooting, PLC and HMI changes, uploading revised manuals, and assistance with equipment performance analysis.
Main benefits
Global, easy access to live and historical data
Data management
Remote troubleshooting
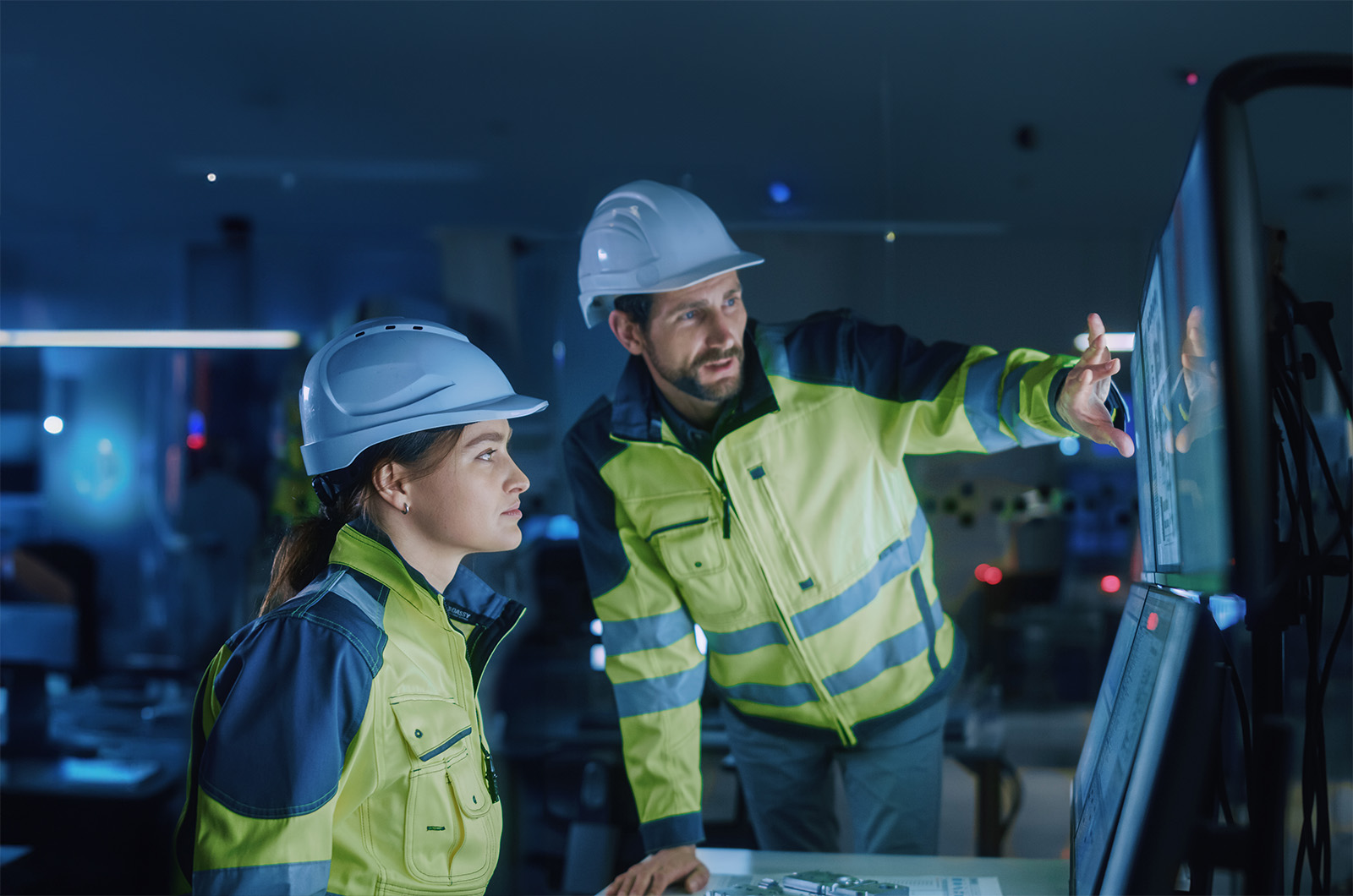
Main benefits
Global, easy access to live and historical data
Data management
Remote troubleshooting
Main benefits
Global, easy access to live and historical data
Data management
Remote troubleshooting
Spare parts management
Having the right spare part to hand can mean the difference between the business-related risks of unplanned downtime and uninterrupted operations. Based on reports, equipment installed, and dry bulk materials handled, our experts perform a review of your current spares inventory and a replacement policy for relevant spare and wear parts. From this, and all other relevant information, a spare parts management strategy is developed and tailored to best meet your needs.
Bruks Siwertell representatives can provide a comprehensive report detailing important recommendations for spare- and wear-parts based on expert knowledge about the installed equipment. This can include stock quantities, current stock status and component lead times. Our spare parts packages include both strategic and wear parts as well as an option to include investment components such as motors, gearboxes, and inverters.
Main features
• Part and Stock level recommendations
• PO scheduling for in-time orders
Available upon special request. Inventory management allows for the outsourcing of spare parts to the supplier. A supplier can take full responsibility for the entire process of managing, maintaining and organizing the spare parts inventory, ensuring that the right parts are available at the right time, and in the right quantities.
Main features
• Procurement and sourcing
• Inventory optimization
• Warehousing strategy
• Distribution, logistics & supply
Main benefits
Continuing equipment performance
Decreased risk of unplanned downtime
Increased cost-efficiency
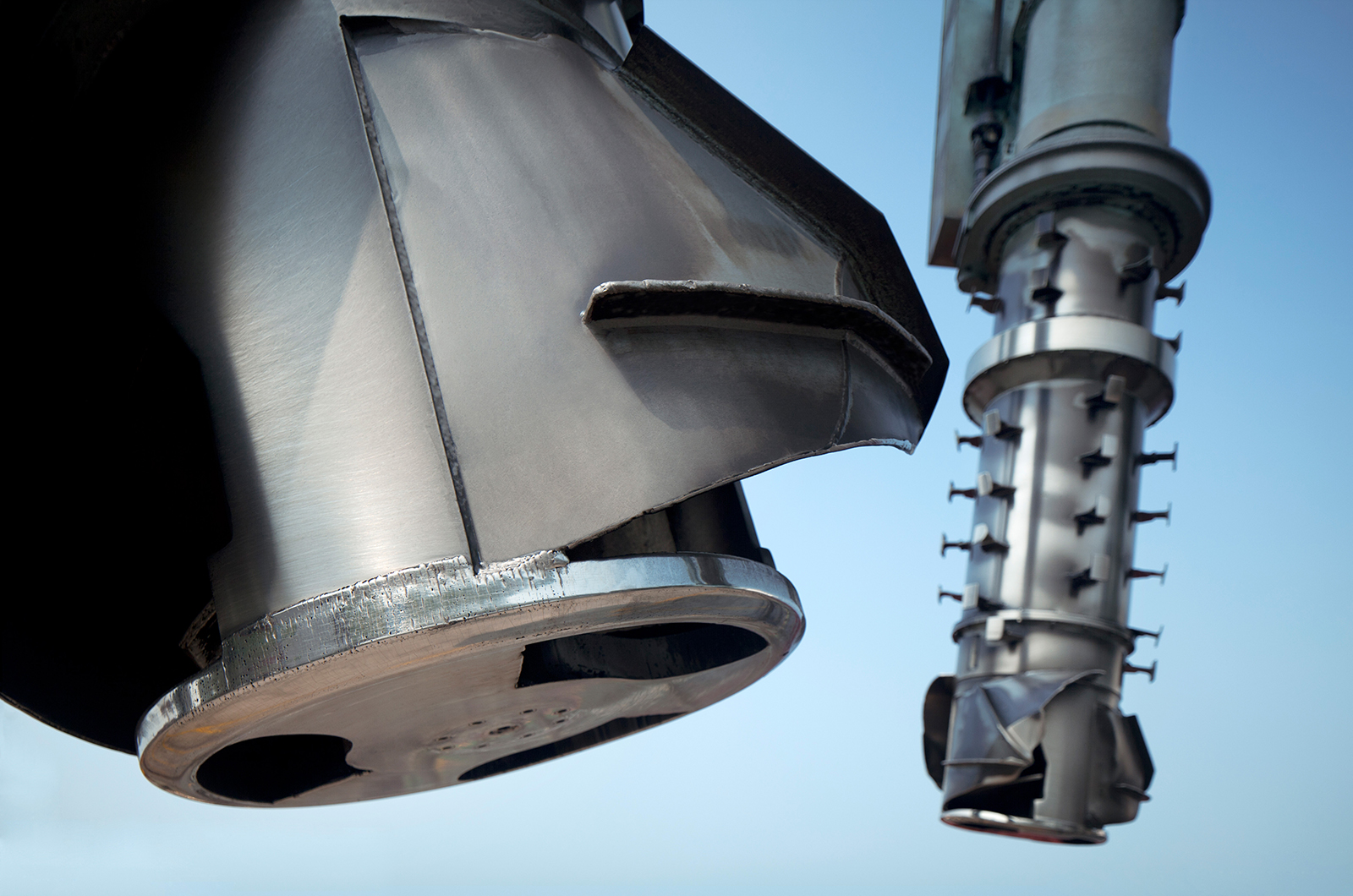
Main benefits
Continuing equipment performance
Decreased risk of unplanned downtime
Increased cost-efficiency
Main benefits
Continuing equipment performance
Decreased risk of unplanned downtime
Increased cost-efficiency
Training & Education
In the long-term, the efficiency and condition of any asset depends on how well the user operates and maintains it. We offer training opportunities that enable owners and maintenance personnel to maintain and operate equipment safely and skilfully, optimizing performance and extending the service life and efficiency of the asset. Our training programs consist of both theoretical, classroom-based learning and practical hands-on training on site. They deliver faster, smoother operational start-ups, improve competency levels, and maximize an operator’s return on investment.
The main purpose of the operator training program is to train personnel to operate ship unloading and ship loading machinery in a safe, qualified way to ensure peak efficiency and extend equipment service life. Through the analysis of current operations, suggested improvements can also be made. For example, the position and operating angles of the vertical conveyor arm, unloading schedules, use of final-stage clean-up vehicles and troubleshooting, can all have an impact on operational efficiency and asset condition.
Main features
• Comprehensive training report
• Qualification certificates
Location: On-site or Remote (upon request)
Duration: Five (5) days
Group size: 1-8 participants (Trainees)
Customer undertakings (Requirements for training)
• Ensure available ship in harbour for Live unloading
• Ensure availability of equipment/asset
• For on-site, ensure availability of classroom
• Nominated and invite participant
The condition of a ship unloader depends on how well its maintenance schedule is followed, and on the operating personnel having a good working knowledge of critical parts and wear parts, their service life expectancy, and their timely replacement.
The main purpose of our mechanical maintenance program is to train personnel so that they are qualified to follow the recommendations in the machine’s maintenance manual correctly. This ensures that the asset is maintained in an optimum way, extending its service life and ensuring peak efficiency.
Main features
• Comprehensive training report
• Qualification certificates
Location: On-site or Remote (upon request)
Duration: Five (5) days
Group size: 1-8 participants (Trainees)
Customer undertakings (Requirements for training)
• Ensure availability of equipment/asset
• For on-site, ensure availability of classroom
• Nominated and invite participant
Our electrical maintenance training program focuses on the key service strategies for electrical systems and troubleshooting. Also included are instructions on how to use the Siwertell monitoring system (SiMon), if applicable. In all areas of training, safety is a key concern and is discussed throughout our programs.
Main features
• Comprehensive training report
• Qualification certificates
Location: On-site or Remote (upon request)
Duration: Five (5) days
Group size: 1-8 participants (Trainees)
Customer undertakings (Requirements for training)
• Ensure availability of equipment/asset
• For on-site, ensure availability of classroom
• Nominated and invite participant
Main benefits
Extended equipment lifetimes
Optimized peak asset performance
Improved in-house competency levels
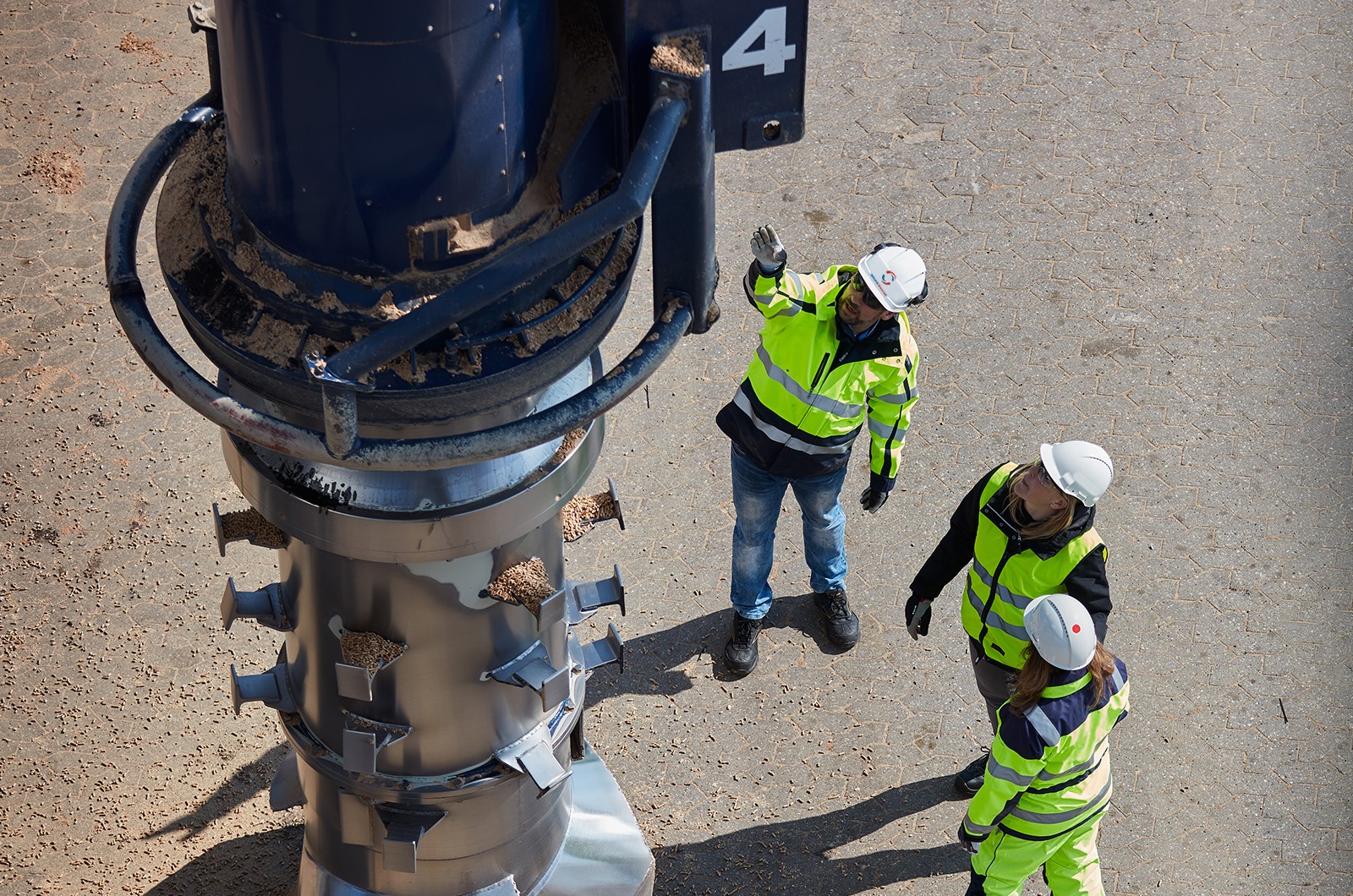
Main benefits
Extended equipment lifetimes
Optimized peak asset performance
Improved in-house competency levels
Main benefits
Extended equipment lifetimes
Optimized peak asset performance
Improved in-house competency levels
Operational management
Our quality equipment delivers long, effective service lives, which can be enhanced further with our operational management support. As your strategic partner, we can manage equipment operators and assist with expert, on-site presence to support your personnel to deliver and continuously improve your port terminal’s high levels of efficiency, safety, reliability, availability, and productivity. We can also take full responsibility for the operation of your equipment.
Expert original equipment manufacturer (OEM) supervision and the coordination of a terminal’s operating personnel can be undertaken by Bruks Siwertell, delivering an on-site presence to support efficient unloading and loading operations. OEM supervision ensures optimized operations, rapid adjustments and problem-solving, and capacity improvements.
Main features
• OEM competence
• Operational improvements
Available upon special request, we can take full responsibility for the operation of your equipment. As a strategic partner for outsourcing, we are able to ensure efficient equipment operation and deliver the highest levels of safety, reliability, and availability. Our full-scale operation service enables terminals to focus on their core business. It maximizes equipment service life, and productivity, and optimizes efficiency and profitability.
Main benefits
Ensured long-term, efficient operations
Expert dry bulk handling input
Enhanced levels of equipment availability and reliability
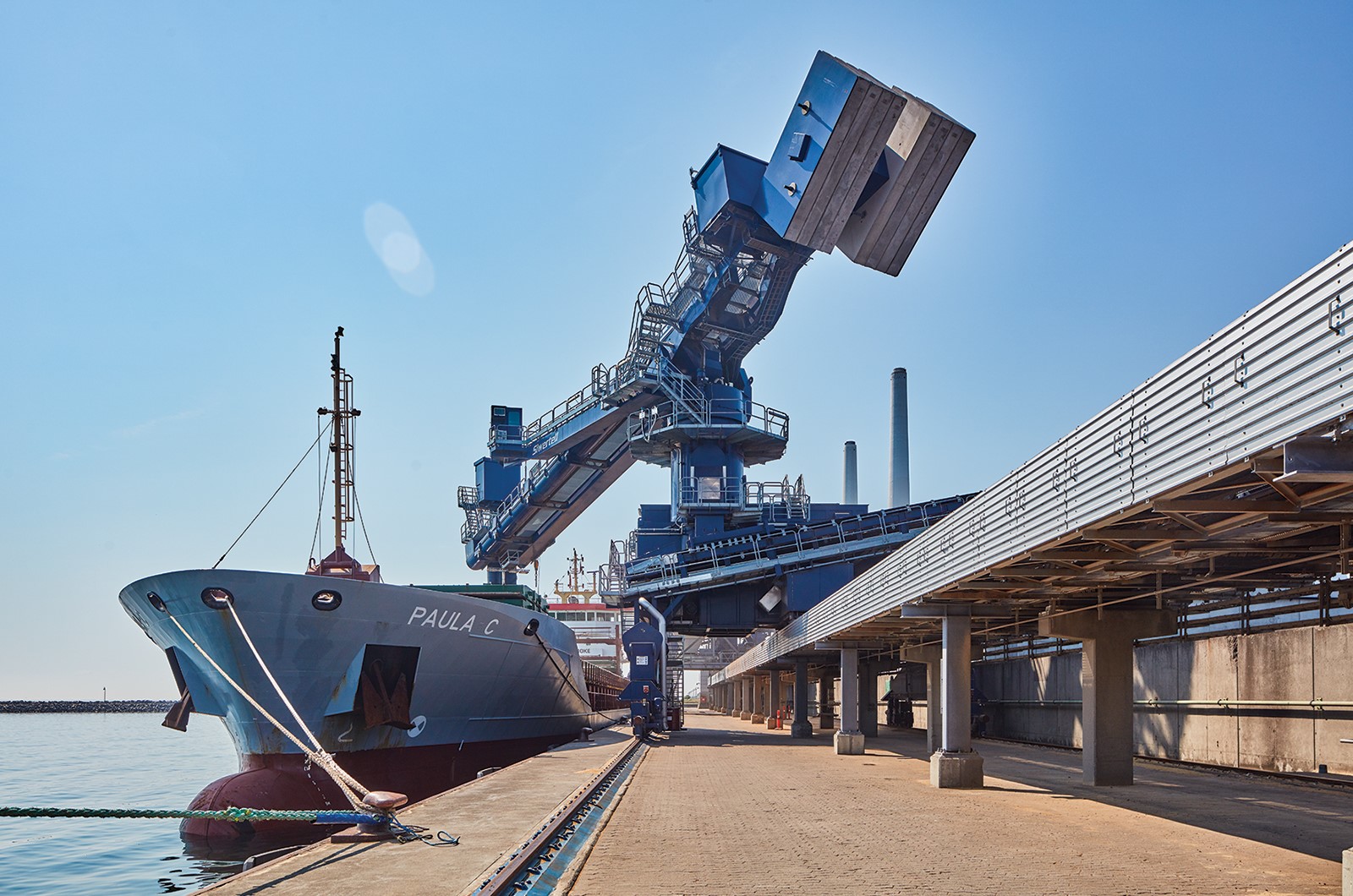
Main benefits
Ensured long-term, efficient operations
Expert dry bulk handling input
Enhanced levels of equipment availability and reliability
Main benefits
Ensured long-term, efficient operations
Expert dry bulk handling input
Enhanced levels of equipment availability and reliability
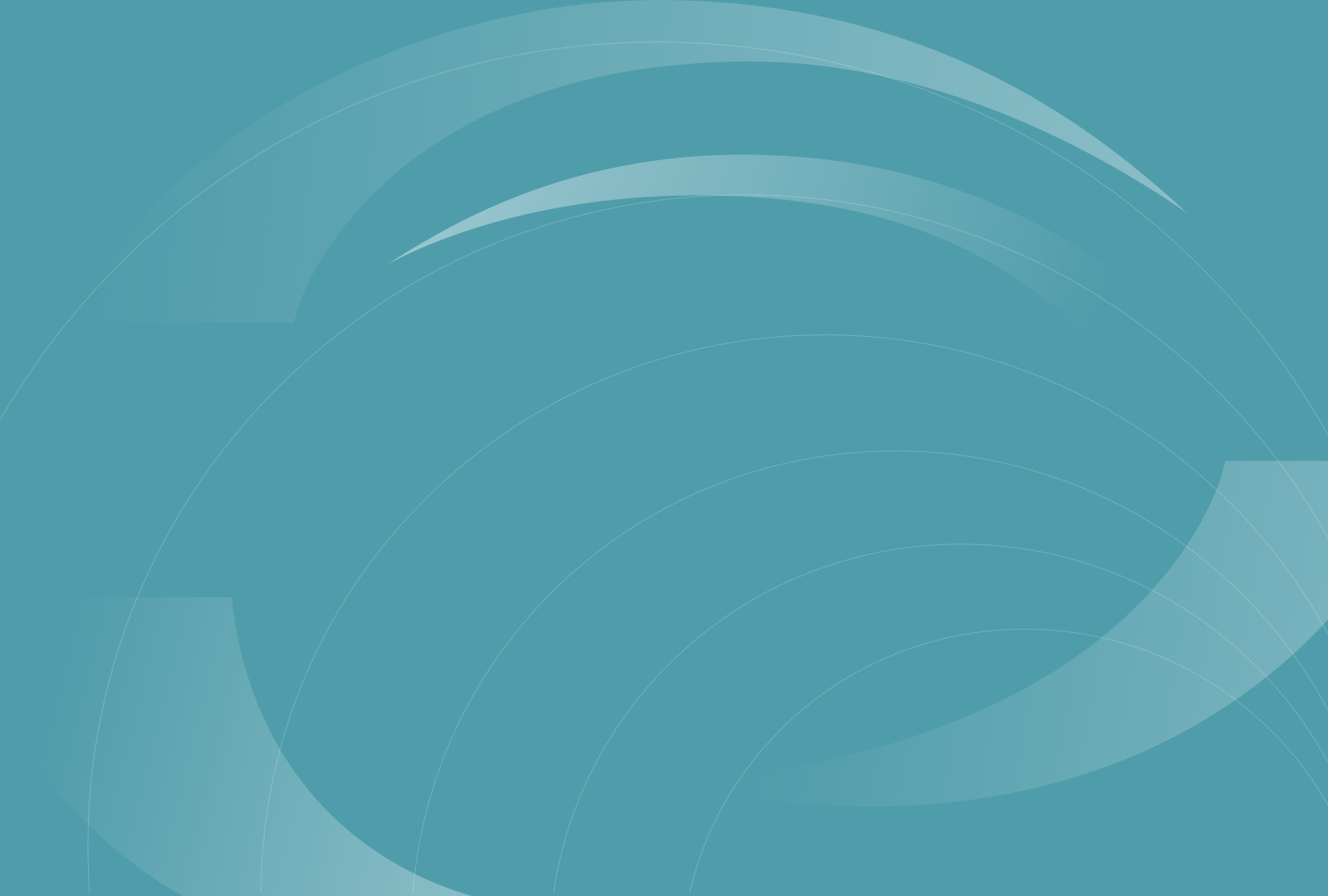
Partnering for success: your bulk, our promise, service agreements that work.Daniel Frostberg, Service Director, Bruks Siwertell
Partnering for success: your bulk, our promise, service agreements that work.Daniel Frostberg, Service Director, Bruks Siwertell