Hammer mill (green materials)
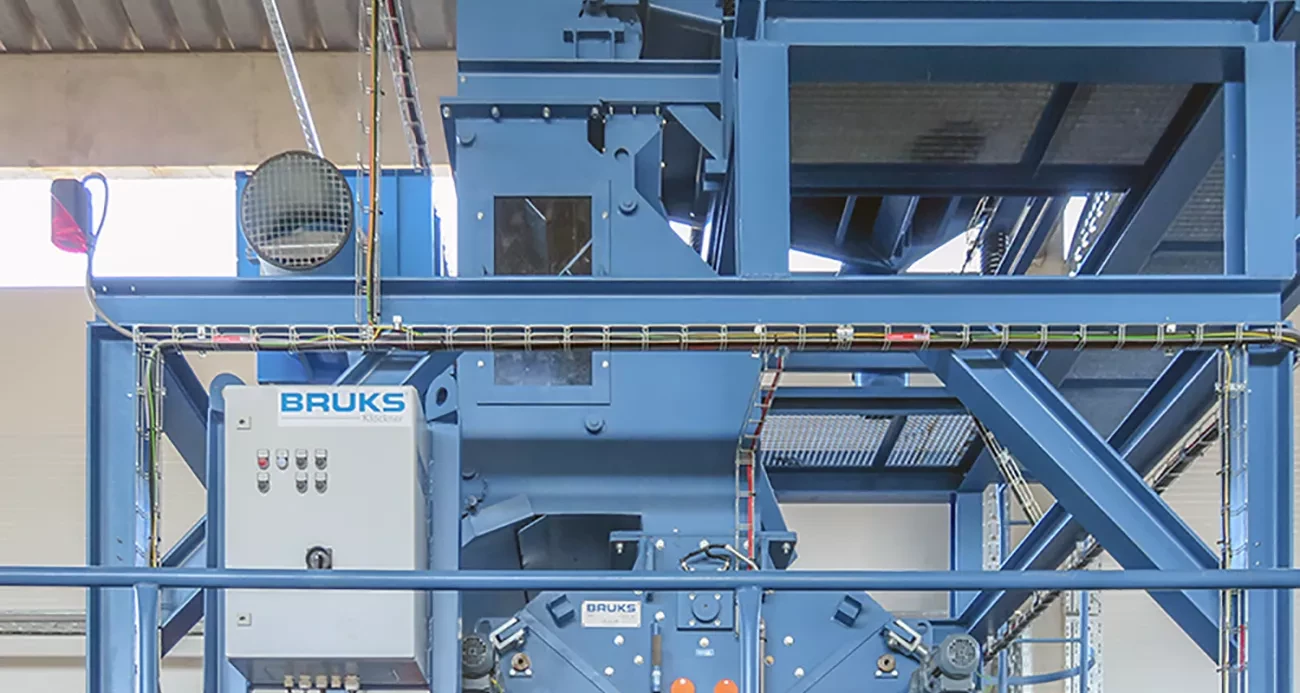
Back to Grinding & Milling
Green wood grinding machinery handles high-moisture content wood with ease
The history of the industrial hammer mill dates back thousands of years, and through industrial revolutions, from water-powered mills, the technology has been refined into the milling machinery recognizable today. Their introduction into industrial processes has transformed industries, initially in mining, but has subsequently been adopted across many more, including the processed wood sector.
Today’s industrial hammer mills offer improved energy savings and efficiency, over their water-driven counterparts, while increasing productivity and making work environments safer.
Our heavy-duty industrial hammer mill grinders and machinery deliver fine-grind processing performance and low maintenance costs thanks to quality construction and robust components. Whether grind wood fiber, bark, or feed products are required, our Bruks and WSM high-volume industrial hammer mills deliver the exceptional performance needed to meet a range of processing goals.
Both Bruks and WSM high-capacity hammer mills for green wood grinding have been specially designed to handle the increased moisture content of these wood products.
Their heavy-duty construction effectively and efficiently grinds green wood particles, as well as most other waste wood materials, into a valuable fiber commodity for the wood-processing market. This includes the particle board industry, pellet production and other biofuel producers.
Our industrial hammer mill units have a flexible configuration of screen modules to meet a wide variety of customer specifications. The type and number of beaters, as well as screen perforation details, are dimensioned according to requirements.
Even wear, low maintenance
A single Bruks green wood industrial hammer mill has a rated capacity of up to 60t/h. The counter-clockwise and clockwise rotation of the Bruks hammer mill means that it is not necessary to turn the beaters, screens and milling segments to ensure an even wear pattern. This delivers reduced maintenance costs. These low costs are further supported by the highly-robust, wear-resistant properties of the beaters.
If a part does need to be serviced or changed, we have designed these units to be as easily accessible as possible, so that wear parts can be replaced quickly and downtime is kept to an absolute minimum. For example, screens are clamped in position by bolted milling segments.
Also, both of the lateral housing parts including screens and milling segments can be folded away using hydraulic cylinders. This ensures quick and easy access to all machinery parts. Optional magnetic drums, as well as pneumatic heavy-particle separators, are also available to protect operations from ferrous or other contaminants.
Exceptional fine grind performance
From wood fiber and bark to agricultural waste fibers and feed products, the WSM high-volume industrial hammer mill delivers exceptional processing performance with high-capacity uniform particle sizing. Its rugged design and construction provide reliable operation, low maintenance, and long machine life.
The WSM hammer mill is available in a range of styles, sizes, and capacities to meet any challenge, including various rotor configurations, screen sizes and types, hammer styles, and discharge options.
Large diameter hammer circle and throat widths range from 0.51m (20 inches) to 1.52m (60 inches) enabling processing capacities of up to 100t/h. Custom control features are also available, including motor starters and controls, auto-reversing, and load sensing feed control.
Why are tip speeds important?
Tip speeds, or otherwise referred to as peripheral velocity, essentially determine the velocity of a hammer’s impact on a surface at the outer edge of its rotor disk. In milling, tip speeds are important because the hammer’s velocity directly influences the amount of force applied to the particles being milled. In general, faster tip speeds generate smaller particles and can increase material throughput.
In WSM hammer mill machinery, a rotor operation at 1,800 rpm provides a high tip speed milling action for superior product sizing. The nearly full circle sizing screens maximize production in fine-grind applications, delivering higher capacities and consistent product sizing.
WSM green wood hammer mills can process a wide range of raw materials such as agricultural fiber such as straw and stover, animal feed, bark, citrus peel, sawdust and shavings, and wood chips.
Image: Rotor with hammers for right and left rotation
Image: The machine housing has an integrated cleaning device
Image: The screen is clamped with milling segments
Image: Operating unit for safety and maintenance functions
Technical data
-
Type -
HH 300x850 -
Rotor Diameter [mm] -
700 -
Infeed Opening[mm] -
300 x 850 -
Number of Hammers [pcs.] -
144 -
Screening Surface [m²] -
1,2 -
Capacity [t/h]* -
2 - 4 -
Motor Power [kW] -
75 - 110 -
Weight [kg]** -
1 400
-
Type -
HH 300x1.200 -
Rotor Diameter [mm] -
700 -
Infeed Opening[mm] -
300 x 1.200 -
Number of Hammers [pcs.] -
216 -
Screening Surface [m²] -
1,6 -
Capacity [t/h]* -
3 - 6 -
Motor Power [kW] -
110 - 160 -
Weight [kg]** -
1 600
-
Type -
HH 400x1.500 -
Rotor Diameter [mm] -
1 000 -
Infeed Opening[mm] -
400 x 1.500 -
Number of Hammers [pcs.] -
216 -
Screening Surface [m²] -
2,9 -
Capacity [t/h]* -
5 - 10 -
Motor Power [kW] -
160 - 250 -
Weight [kg]** -
5 500
-
Type -
HH 500x1.800 -
Rotor Diameter [mm] -
1 300 -
Infeed Opening[mm] -
500 x 1.800 -
Number of Hammers [pcs.] -
316 -
Screening Surface [m²] -
4,6 -
Capacity [t/h]* -
8 - 18 -
Motor Power [kW] -
250 - 400 -
Weight [kg]** -
9 500
-
Type -
HH 600x2.000 -
Rotor Diameter [mm] -
1 600 -
Infeed Opening[mm] -
600 x 2.000 -
Number of Hammers [pcs.] -
480 -
Screening Surface [m²] -
7,6 -
Capacity [t/h]* -
15 - 25 -
Motor Power [kW] -
400 - 630 -
Weight [kg]** -
15 000
Type | Rotor Diameter [mm] | Infeed Opening[mm] | Number of Hammers [pcs.] | Screening Surface [m²] | Capacity [t/h]* | Motor Power [kW] | Weight [kg]** |
---|---|---|---|---|---|---|---|
HH 300x850 | 700 | 300 x 850 | 144 | 1,2 | 2 - 4 | 75 - 110 | 1 400 |
HH 300x1.200 | 700 | 300 x 1.200 | 216 | 1,6 | 3 - 6 | 110 - 160 | 1 600 |
HH 400x1.500 | 1 000 | 400 x 1.500 | 216 | 2,9 | 5 - 10 | 160 - 250 | 5 500 |
HH 500x1.800 | 1 300 | 500 x 1.800 | 316 | 4,6 | 8 - 18 | 250 - 400 | 9 500 |
HH 600x2.000 | 1 600 | 600 x 2.000 | 480 | 7,6 | 15 - 25 | 400 - 630 | 15 000 |
*depending on kind and dimensions of material, moisture content and screen size
**only hammermill without a motor/cleaning/feeding device