Vibrating conveyors
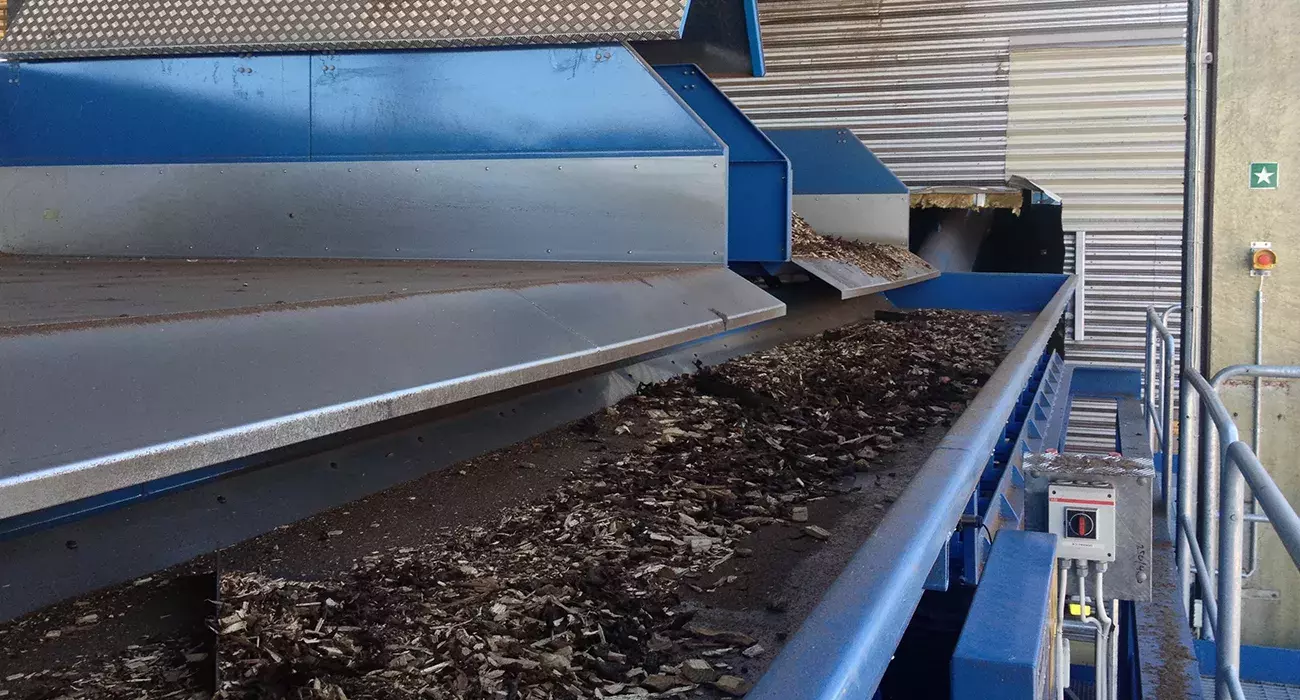
Back to Conveying
Vibrating conveyors ensure efficient, multi-functional material handling
Our modular vibrating conveyors offer an extremely efficient, multi-functional method of conveying and processing different sized bulk materials, including larger and longer pieces of processed wood. Their design ensures consistently high conveying speeds even under high loads.
Vibrating conveyors can form part of complex processing facilities and are easily customized to meet varying needs. They are ideally paired with our Bruks screening systems. Integral screens are often incorporated into a conveying system and can efficiently separate over-sized or fine particles during material transfer. In some cases they eliminate the need for separate screening units entirely.
Vibrating conveyors are particularly popular for use with horizontal drum chippers and can be specified for use with gravity-fed versions. They can also be fitted with a built-in metal detector or heating rods for operation in extremely cold environments.
Long and short wood handled with ease
Most often used in sawmills, pulp and board mills as well as in bio-fuel applications, Bruks’ vibrating conveyors are available in a light, medium and heavy-duty design. They can easily accommodate long and short wood such as logs, slabs, edgings, trim-ends, chips, sawdust and bark, and can transport materials in parallel without mixing them.
Tailored for each application
Vibrating conveyors are tailored for each application to deliver the best possible operational performance.
Guide fins in the trough bottom help to orient material so that short wood waste, for example, has a better chance of being chipped properly, improving chip quality. Infeed conveyors can be equipped with a capacity control that reacts to the chipper’s motor load.
Minimal maintenance requirements
Vibrating conveyors require very little maintenance. Their troughs are supported by springs that vibrate as a result of a crank shaft with single or multiple connecting rods. These steel or fiber-glass springs provide a long service life and low maintenance requirements. They also have flexible, tough attachments for smooth starts and stops.
The simple operation of these conveyors provides a smooth, leveled-out material distribution due to the vibrations. Material enters the conveyor and spreads evenly without high-impact forces.
Balanced and unbalanced designs are available, depending on cost and foundation requirements. A robust, concrete foundation or on-board counterweight balances the dynamic forces generated by the vibrating equipment.
Technical data
-
Type -
CV330 -
Trough bottom width (mm) -
330 -
LL* -
70 -
M* -
85 -
H* -
85 -
N* -
- -
LL** -
20 -
M** -
25 -
H** -
25 -
N** -
-
-
Type -
CV450 -
Trough bottom width (mm) -
450 -
LL* -
90 -
M* -
110 -
H* -
110 -
N* -
- -
LL** -
20 -
M** -
25 -
H** -
25 -
N** -
-
-
Type -
CV600 -
Trough bottom width (mm) -
600 -
LL* -
110 -
M* -
140 -
H* -
140 -
N* -
- -
LL** -
20 -
M** -
25 -
H** -
25 -
N** -
-
-
Type -
CV750 -
Trough bottom width (mm) -
750 -
LL* -
135 -
M* -
170 -
H* -
170 -
N* -
- -
LL** -
20 -
M** -
25 -
H** -
25 -
N** -
-
-
Type -
CV900 -
Trough bottom width (mm) -
900 -
LL* -
160 -
M* -
- -
H* -
200 -
N* -
- -
LL** -
20 -
M** -
25 -
H** -
25 -
N** -
-
-
Type -
CV1200 -
Trough bottom width (mm) -
1200 -
LL* -
210 -
M* -
- -
H* -
- -
N* -
- -
LL** -
20 -
M** -
- -
H** -
- -
N** -
-
-
Type -
CV400 -
Trough bottom width (mm) -
400 -
LL* -
- -
M* -
- -
H* -
- -
N* -
7 -
LL** -
- -
M** -
- -
H** -
- -
N** -
8-12
-
Type -
CV500 -
Trough bottom width (mm) -
500 -
LL* -
- -
M* -
- -
H* -
- -
N* -
9 -
LL** -
- -
M** -
- -
H** -
- -
N** -
8-12
-
Type -
CV650 -
Trough bottom width (mm) -
650 -
LL* -
- -
M* -
- -
H* -
- -
N* -
13 -
LL** -
- -
M** -
- -
H** -
- -
N** -
8-12
-
Type -
CV800 -
Trough bottom width (mm) -
800 -
LL* -
- -
M* -
- -
H* -
- -
N* -
16 -
LL** -
- -
M** -
- -
H** -
- -
N** -
8-12
-
Type -
CV1000 -
Trough bottom width (mm) -
1000 -
LL* -
- -
M* -
- -
H* -
- -
N* -
20 -
LL** -
- -
M** -
- -
H** -
- -
N** -
8-12
-
Type -
CV1200 -
Trough bottom width (mm) -
1200 -
LL* -
- -
M* -
- -
H* -
- -
N* -
24 -
LL** -
- -
M** -
- -
H** -
- -
N** -
8-12
Type | Trough bottom width (mm) | LL* | M* | H* | N* | LL** | M** | H** | N** |
---|---|---|---|---|---|---|---|---|---|
CV330 | 330 | 70 | 85 | 85 | - | 20 | 25 | 25 | - |
CV450 | 450 | 90 | 110 | 110 | - | 20 | 25 | 25 | - |
CV600 | 600 | 110 | 140 | 140 | - | 20 | 25 | 25 | - |
CV750 | 750 | 135 | 170 | 170 | - | 20 | 25 | 25 | - |
CV900 | 900 | 160 | - | 200 | - | 20 | 25 | 25 | - |
CV1200 | 1200 | 210 | - | - | - | 20 | - | - | - |
CV400 | 400 | - | - | - | 7 | - | - | - | 8-12 |
CV500 | 500 | - | - | - | 9 | - | - | - | 8-12 |
CV650 | 650 | - | - | - | 13 | - | - | - | 8-12 |
CV800 | 800 | - | - | - | 16 | - | - | - | 8-12 |
CV1000 | 1000 | - | - | - | 20 | - | - | - | 8-12 |
CV1200 | 1200 | - | - | - | 24 | - | - | - | 8-12 |
* Max Capacity m3/h (loose chips)
** Feed speed (m/min.)
For type LL, M and H, the capacity is calculated with a material height of 100mm and for type N 40mm, deviations possible