Drum chipper (horizontal)
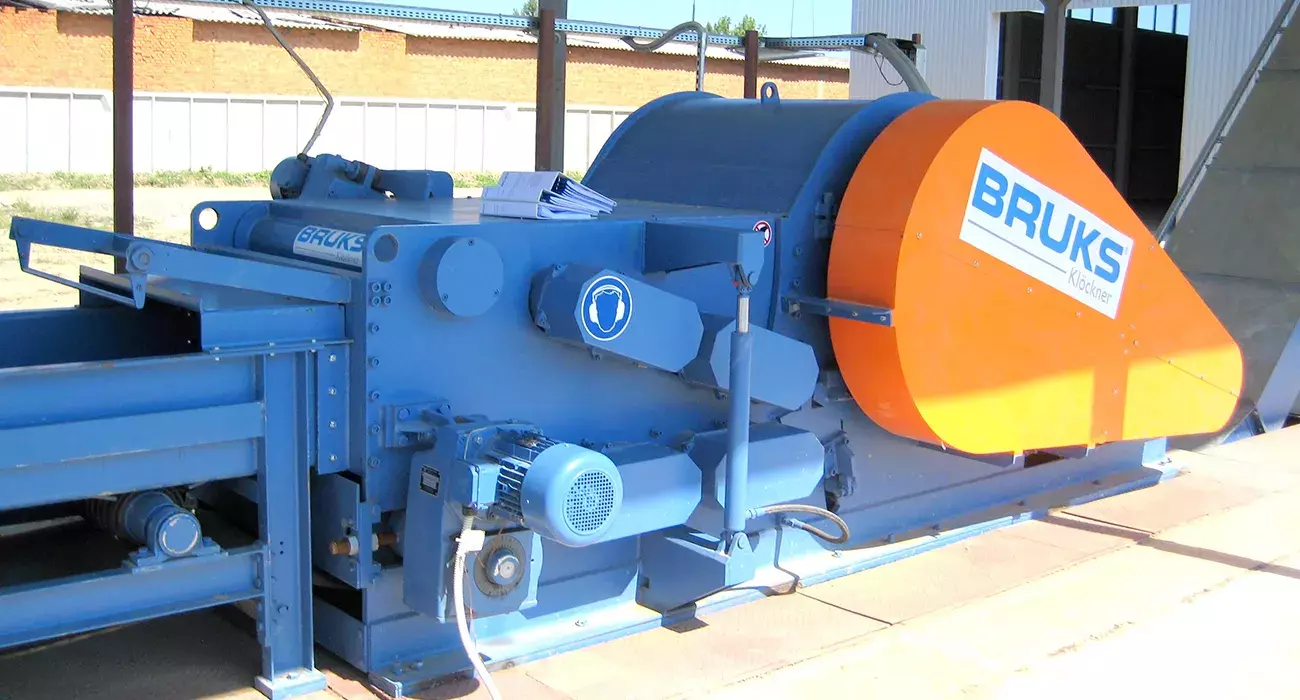
Back to Chipping
Market-leading machines that process any waste wood product.
We manufacture complete chipping lines that meet the highest performance and reliability criteria. Our heavy-duty machinery can handle the toughest conditions and Bruks’ horizontal-fed drum chipper is no exception.
Our drum chippers, with their large in-feed openings, lead the market and are capable of processing any waste wood product. Logs or bundles of wood with a diameter of over a meter can be reliably processed in Bruks’ larger chippers.
With the ability to produce up to 300t/h of high-quality pulp mill chips, or smaller microchips for use in the biofuel industry, our drum chippers have flexible arrangements to produce even large chips of up to 200mm in length.
With more than 50 years of experience and over 10,000 drum chippers installed, you can depend on a well-tested product that will deliver a long, economic life with low maintenance costs.
Wear resistant, proven technology
Our drum chippers have heavy-duty, self-aligning bearings that are centered in steel housings and bolted to the side walls of the machine. These deliver a long and effective service life.
In addition, their feed rollers have special ‘teeth’ that are surface-hardened by a heat treatment process, resulting in a particularly high wear resistance. We can deliver rollers with the option to have exchangeable wear segments.
Hydraulic or pneumatic cylinders are used to regulate the pressure of the upper feed rollers and to open the upper feed rollers for maintenance and easy cleaning. Hydraulic cylinders are also used for maintenance functions and easy access for cleaning and knife change.
Image: For quick, easy and safe knife change, the clamping plate is secured in the rotor body
Image: To secure even and continuous feed to the cutting system, the in-feed system with lower and upper in-feed rollers are designed to allow left-lifting up to maximum in-feed height
Image: The operating unit is equipped with safety and maintenance functions
Image: The drum chipper includes a service platform, to allow for easy and safe access, and for facilitating knife change
Image: The wear plates on the counter knife are bolted and replaceable, as well as partly extractable
Image: The wear plates on the rotor are replaceable and able to turn, and they are placed underneath the chipping knives to reduce wear in the chip pockets.
Technical data
-
Type -
DH 100 -
Infeed width [mm] -
300,500 -
Rotor diameter [mm] -
300 -
Infeed rollers [pcs] -
2 -
Motor power [kW] -
18,5-37
-
Type -
DH 120 -
Infeed width [mm] -
400, 500, 650 -
Rotor diameter [mm] -
450 -
Infeed rollers [pcs] -
2 -
Motor power [kW] -
22-55
-
Type -
DH-V 120/250 -
Infeed width [mm] -
650 -
Rotor diameter [mm] -
450 -
Infeed rollers [pcs] -
3 -
Motor power [kW] -
22-55
-
Type -
DH 150 -
Infeed width [mm] -
400, 500, 650 -
Rotor diameter [mm] -
500 -
Infeed rollers [pcs] -
2 -
Motor power [kW] -
30-75
-
Type -
DH 200 -
Infeed width [mm] -
400, 500, 650 -
Rotor diameter [mm] -
580 -
Infeed rollers [pcs] -
2 -
Motor power [kW] -
55-132
-
Type -
DH-V 200/300 -
Infeed width [mm] -
650, 800 -
Rotor diameter [mm] -
580 -
Infeed rollers [pcs] -
3 -
Motor power [kW] -
55-132
-
Type -
DH 180 -
Infeed width [mm] -
540 -
Rotor diameter [mm] -
600 -
Infeed rollers [pcs] -
2 -
Motor power [kW] -
45-75
-
Type -
DH 240 -
Infeed width [mm] -
500, 650, 800 -
Rotor diameter [mm] -
700 -
Infeed rollers [pcs] -
4 -
Motor power [kW] -
55-132
-
Type -
DH-V 240/350 -
Infeed width [mm] -
650, 800 -
Rotor diameter [mm] -
700 -
Infeed rollers [pcs] -
5 -
Motor power [kW] -
55-132
-
Type -
DH 365 -
Infeed width [mm] -
560, 825 -
Rotor diameter [mm] -
800 -
Infeed rollers [pcs] -
6 -
Motor power [kW] -
55-2x132
-
Type -
DH 300 -
Infeed width [mm] -
650, 800 -
Rotor diameter [mm] -
1000 -
Infeed rollers [pcs] -
6 -
Motor power [kW] -
110-250
-
Type -
DH 300(400) -
Infeed width [mm] -
800, 1000 -
Rotor diameter [mm] -
1000 -
Infeed rollers [pcs] -
8 -
Motor power [kW] -
110-250
-
Type -
DH-V 300/400 -
Infeed width [mm] -
800, 1000, 1200 -
Rotor diameter [mm] -
1000 -
Infeed rollers [pcs] -
5 -
Motor power [kW] -
110-250
-
Type -
DH 400 -
Infeed width [mm] -
650, 800, 1000, 1200 -
Rotor diameter [mm] -
1300 -
Infeed rollers [pcs] -
8 -
Motor power [kW] -
160-500
-
Type -
DH 400(550) -
Infeed width [mm] -
1000, 1200 -
Rotor diameter [mm] -
1300 -
Infeed rollers [pcs] -
10 -
Motor power [kW] -
160-500
-
Type -
DH 500 -
Infeed width [mm] -
800, 1000, 1200 -
Rotor diameter [mm] -
1600 -
Infeed rollers [pcs] -
11 -
Motor power [kW] -
315-630
-
Type -
DH 500(700) -
Infeed width [mm] -
1000, 1200 -
Rotor diameter [mm] -
1600 -
Infeed rollers [pcs] -
12 -
Motor power [kW] -
315-630
-
Type -
DH 700 -
Infeed width [mm] -
1000, 1200, 1450 -
Rotor diameter [mm] -
2000 -
Infeed rollers [pcs] -
13 -
Motor power [kW] -
630-1500
-
Type -
DH 850 -
Infeed width [mm] -
1200, 1450 -
Rotor diameter [mm] -
2000 -
Infeed rollers [pcs] -
15 -
Motor power [kW] -
630-1500
-
Type -
DH 1000 -
Infeed width [mm] -
1200, 1450 -
Rotor diameter [mm] -
2000 -
Infeed rollers [pcs] -
15 -
Motor power [kW] -
630-1500
-
Type -
DH 1050 -
Infeed width [mm] -
1450, 1850 -
Rotor diameter [mm] -
2400 -
Infeed rollers [pcs] -
14 -
Motor power [kW] -
1250-2500
-
Type -
DH 1200 -
Infeed width [mm] -
1450 -
Rotor diameter [mm] -
2800 -
Infeed rollers [pcs] -
18 -
Motor power [kW] -
1250-2500
Type | Infeed width [mm] | Rotor diameter [mm] | Infeed rollers [pcs] | Motor power [kW] |
---|---|---|---|---|
DH 100 | 300,500 | 300 | 2 |
18,5-37 |
DH 120 | 400, 500, 650 | 450 | 2 | 22-55 |
DH-V 120/250 | 650 | 450 | 3 | 22-55 |
DH 150 | 400, 500, 650 | 500 | 2 | 30-75 |
DH 200 | 400, 500, 650 | 580 | 2 | 55-132 |
DH-V 200/300 | 650, 800 | 580 | 3 | 55-132 |
DH 180 | 540 | 600 | 2 | 45-75 |
DH 240 | 500, 650, 800 | 700 | 4 | 55-132 |
DH-V 240/350 | 650, 800 | 700 | 5 | 55-132 |
DH 365 | 560, 825 | 800 | 6 | 55-2x132 |
DH 300 | 650, 800 | 1000 | 6 | 110-250 |
DH 300(400) | 800, 1000 | 1000 | 8 | 110-250 |
DH-V 300/400 | 800, 1000, 1200 | 1000 | 5 | 110-250 |
DH 400 | 650, 800, 1000, 1200 | 1300 | 8 | 160-500 |
DH 400(550) | 1000, 1200 | 1300 | 10 | 160-500 |
DH 500 | 800, 1000, 1200 | 1600 | 11 | 315-630 |
DH 500(700) | 1000, 1200 | 1600 | 12 | 315-630 |
DH 700 | 1000, 1200, 1450 | 2000 | 13 | 630-1500 |
DH 850 | 1200, 1450 | 2000 | 15 | 630-1500 |
DH 1000 | 1200, 1450 | 2000 | 15 | 630-1500 |
DH 1050 | 1450, 1850 | 2400 | 14 | 1250-2500 |
DH 1200 | 1450 | 2800 | 18 | 1250-2500 |