Vibratory Screens
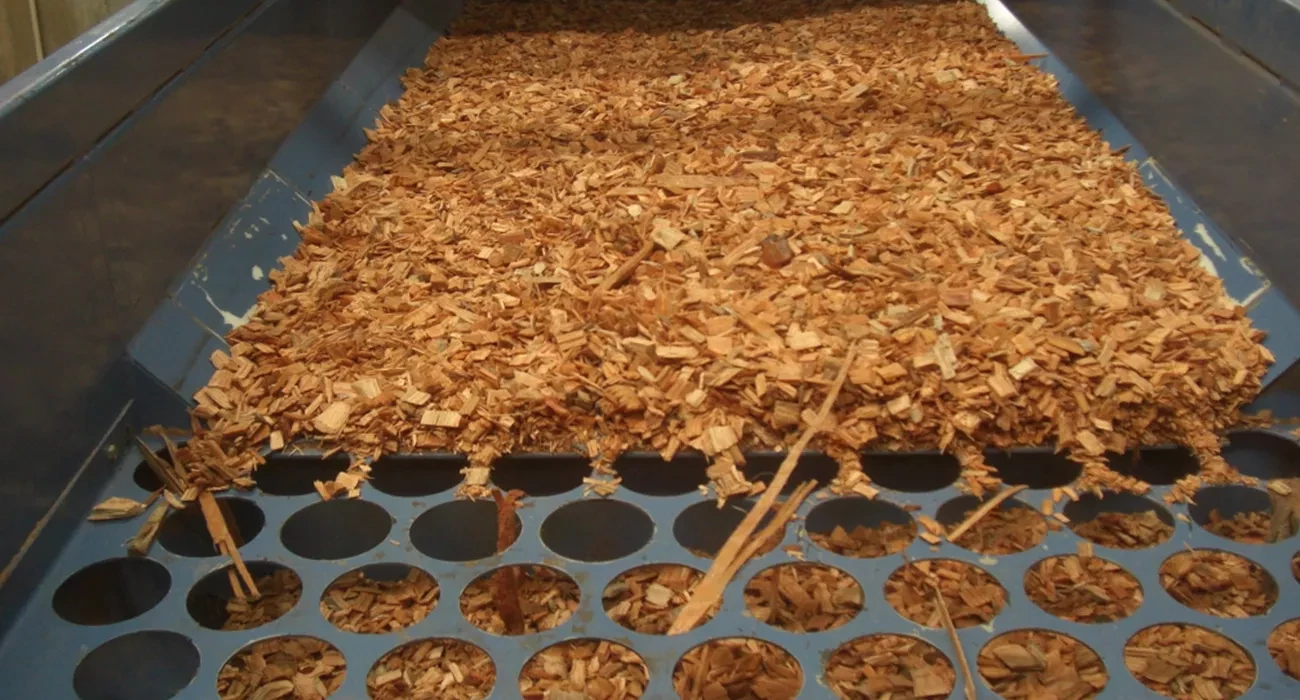
Back to Screening
Virtually maintenance-free vibratory screener solutions
Like all Bruks Siwertell and WSM screening systems, our vibratory screens, vibratory screener solutions and WSM vibrating screens and conveyors, have been expertly designed to sort particle sizes and to level and orient material as it is conveyed, reducing surges to downstream equipment.
Unlike our gyratory free-swinging and oscillating screening systems, vibratory screens oscillate in the vertical plane, rather than the horizontal. Vibrations move and accelerate material particles until they become airborne and then settle and fall through the screen mesh or plate. Until the introduction of gyratory free-swinging and oscillating screening systems, vibratory screens and vibratory screening equipment were often the only choice for more intense screening. Vibratory screens are particularly useful to separate small, frozen lumps of sawdust, for example.
Our vibratory screens and vibratory screener solutions can be delivered as standalone units, mainly for handling smaller volumes of wood products, but are often delivered as an integrated system of vibratory screens and industry-leading range of vibrating conveyors.
Bruks Siwertell vibratory screens and WSM vibrating screens and conveyors are energy-efficient, and have a natural-frequency design which uses power springs to reduce energy requirements and operating costs. Because they are not exposed to any significant forces, they are virtually maintenance-free, and their robust construction ensures reliable, long operating lives, with minimal downtime.
Our vibratory conveyors and screens are used in a wide variety of applications, from simple transfer conveyors, to high-capacity screening of particleboard furnish, to heavy-duty chipper infeed units.
Typical applications see these highly-efficient screens separating out oversized sawdust fractions, for example. In our vibratory conveyors, they frequently act as a ‘pre-screening’ system to ensure that sawdust is removed from a load before it is fed into a chipper.
Sized and configured to fit individual screening requirements
Bruks Siwertell and WSM vibratory screens and conveyors are available in a variety of configurations and sized to fit any application.
WSM vibrating screens have pan sizes ranging from between 0.3m (12 inches) to 1.88m (72 inches) wide and lengths up to 45.72m (150ft). They are available with a range of mesh sizes and wire diameters, making them ideal for screening smaller particles. An optional ball deck can be added to enhance material agitation and screen cleaning.
Perforated plate screens are typically used in larger separation point applications. They are stronger and generally offer even longer wear lives than our mesh screens. WSM vibrating screens are available in a counter-balanced and unbalanced design, specified depending on the material to be conveyed, the installation location, and the availability of foundations.
Optional top covers for dust containment, can be supplied, when necessary, along with a removable transition section when feeding into grinders and chippers, for example. An optional fiberglass section with metal detection can also be fitted to help prevent damage to downstream equipment from tramp metal.
WSM vibratory screen pans are formed from a thick steel plate as standard, and thicker pans and other materials can be specified for more abrasive applications. Pans have flanges along the top edge for added structural support. Other features of WSM vibratory screening equipment include heavy-duty drive assemblies, constructed using the highest quality components; an eccentric drive shaft is precision-machined from alloy steel.
The entire vibrating screen is mounted on a heavy structural frame, with steel spring mounts on coil springs. Optional steel coil springs are available, which are heated-treated for long wear lives. Our fiberglass springs are made of uni-directional fiberglass for lighter-duty application, and our fiberglass spring mounts are fabricated from steel angle; all coils are readily accessible for maintenance.