Rotom hammer hog (horizontal fed)
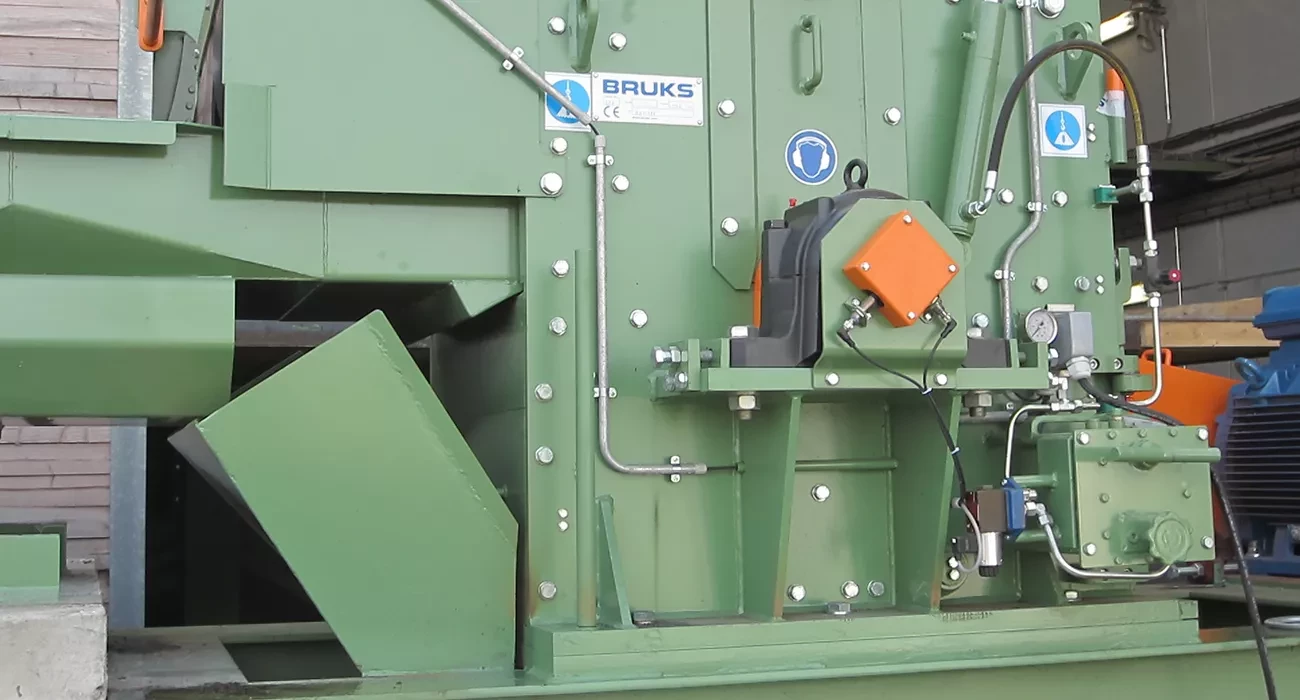
Back to Wood residue processing
Space-saving horizontal-fed rotom hammer hogs can be tailored to each application
Our horizontal-fed Rotom hammer hogs can be designed to fit individual applications. Depending on the position of the machine in the wood-processing plant and the size of the material handled, a Bruks hammer hog unit can be configured with various components to ensure maximum efficiency.
A horizontal-fed hammer hog is an ideal choice for level operations and for when the waste wood processing feedstocks are generally longer. Our horizontal-fed Rotom hammer hogs can be fitted with an optional infeed spike roll and can processing round logs and timber up to around 2m in length.
The space-saving horizontal-fed model can be equipped with an integrated screen, which ensures that only pre-defined oversized materials are processed within the hammer hog unit. This tailors the end product to meet operational requirements and adds value to the size reduction hammer hog process.
To make horizontal-fed hammer hog units ideally suitable for materials other than bark, such as industrial timber waste and sawmill waste, the unit can be specified with extremely powerful oversized hammers and anvils.
Our robust, reliable hammer hogs have large service hatches and exchangeable, reversible wear parts, making them easy to maintain, further adding to their trouble-free operation.
Hammer designs can be tailored to each application and configured differently on each individual hammer hog; this rotor includes fixing and flying hammers.
Hammer hog screens, included in the screening and milling segments, can be designed in various ways, in accordance to each customer’s specific applications. Screening segments are easily accessible for maintenance and can be turned, maximizing their use.
Upper infeed rollers are optional for horizontal-fed hammer hogs. All our infeed rollers have a robust design, allowing each hammer hog to handle challenging raw materials.
Wear plates inside the hammer hog machine housing are replaceable, ensuring the hammer hog’s long-life operation.
Technical table
-
Type -
8-8 -
Rotor ø mm -
800 -
Weight Hammer kg -
13 -
Thickness Sidewall mm -
20 -
Thickness Wear Plates mm -
30 -
Motor Power kW -
90-132
-
Type -
8-10 -
Rotor ø mm -
800 -
Weight Hammer kg -
13 -
Thickness Sidewall mm -
25 -
Thickness Wear Plates mm -
30 -
Motor Power kW -
110-160
-
Type -
10-10 -
Rotor ø mm -
1000 -
Weight Hammer kg -
20 -
Thickness Sidewall mm -
25 -
Thickness Wear Plates mm -
30 -
Motor Power kW -
132-200
-
Type -
10-12 -
Rotor ø mm -
1000 -
Weight Hammer kg -
20 -
Thickness Sidewall mm -
25 -
Thickness Wear Plates mm -
30 -
Motor Power kW -
160-250
-
Type -
12-12 -
Rotor ø mm -
1200 -
Weight Hammer kg -
25 -
Thickness Sidewall mm -
30 -
Thickness Wear Plates mm -
40 -
Motor Power kW -
200-315
-
Type -
12-16 -
Rotor ø mm -
1200 -
Weight Hammer kg -
25 -
Thickness Sidewall mm -
30 -
Thickness Wear Plates mm -
40 -
Motor Power kW -
250-315
-
Type -
12-18 -
Rotor ø mm -
1200 -
Weight Hammer kg -
25 -
Thickness Sidewall mm -
30 -
Thickness Wear Plates mm -
40 -
Motor Power kW -
250-315
-
Type -
15-12 -
Rotor ø mm -
1500 -
Weight Hammer kg -
55 -
Thickness Sidewall mm -
40 -
Thickness Wear Plates mm -
50 -
Motor Power kW -
250-400
-
Type -
15-16 -
Rotor ø mm -
1500 -
Weight Hammer kg -
55 -
Thickness Sidewall mm -
40 -
Thickness Wear Plates mm -
50 -
Motor Power kW -
355-560
-
Type -
15-20 -
Rotor ø mm -
1500 -
Weight Hammer kg -
55 -
Thickness Sidewall mm -
40 -
Thickness Wear Plates mm -
50 -
Motor Power kW -
400-710
Type | Rotor ø mm | Weight Hammer kg | Thickness Sidewall mm | Thickness Wear Plates mm | Motor Power kW |
---|---|---|---|---|---|
8-8 | 800 | 13 | 20 | 30 | 90-132 |
8-10 | 800 | 13 | 25 | 30 | 110-160 |
10-10 | 1000 | 20 | 25 | 30 | 132-200 |
10-12 | 1000 | 20 | 25 | 30 | 160-250 |
12-12 | 1200 | 25 | 30 | 40 | 200-315 |
12-16 | 1200 | 25 | 30 | 40 | 250-315 |
12-18 | 1200 | 25 | 30 | 40 | 250-315 |
15-12 | 1500 | 55 | 40 | 50 | 250-400 |
15-16 | 1500 | 55 | 40 | 50 | 355-560 |
15-20 | 1500 | 55 | 40 | 50 | 400-710 |