Rotom hammer hog (drop fed)
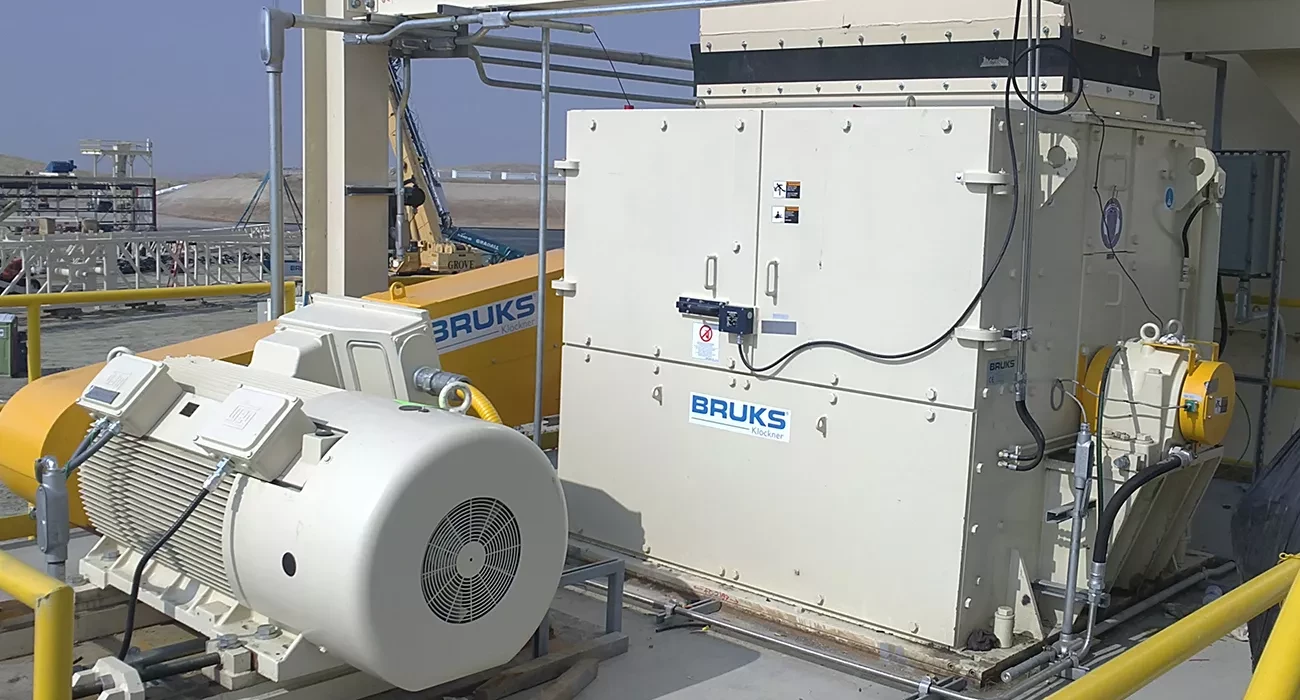
Back to Wood residue processing
Drop-fed rotom hammer hogs ensure high-capacity waste wood processing
The Bruks Rotom hammer hog is an incredibly robust, reliable waste wood processing machine, offering a long service life even under high-use, demanding conditions. Hammer hog machinery components can be easily accessed for maintenance and can be turned to ensure maximum wear before replacement. It is also possible to tailor hammers and tips to individual waste wood processing applications.
If an operator can benefit from natural forces, such as gravity, during manufacturing processes, this can be a valuable asset. Drop-fed wood waste-processing units, such as our Rotom hammer hogs, are no exception, and in addition to durability are highly energy efficient as well.
Sharing many of the same proven design characteristics as its horizontal-fed counterpart, the drop-fed hammer hog unit is available in a range of standard sizes and is capable of processing wood waste up to a capacity of over 375 (standard) m³/h.
Drop-fed hammer hog units can easily process many different types of materials like bark, forest residues, industrial wood waste and sawmill waste. They have a compact, robust design, which is easy to service and maintain, and offer reliable performance.
The hammer design and configuration depends on each individual hammer hog; this rotor includes fixing and flying hammers.
Hammer hog screens, included in the screening and milling segments, can be designed in various ways, in accordance with each customer’s specific applications. Screening segments are easily accessible for maintenance and can be turned, maximizing their use.
Wear plates inside the hammer hog machine housing are also replaceable, ensuring the hammer hog’s long-life operation.
Technical table
-
Type -
8-8 -
Rotor ø mm -
800 -
Weight Hammer kg -
13 -
Thickness Sidewall mm -
20 -
Thickness Wear Plates mm -
30 -
Motor Power kW -
90-132
-
Type -
8-10 -
Rotor ø mm -
800 -
Weight Hammer kg -
13 -
Thickness Sidewall mm -
25 -
Thickness Wear Plates mm -
30 -
Motor Power kW -
110-160
-
Type -
10-10 -
Rotor ø mm -
1000 -
Weight Hammer kg -
20 -
Thickness Sidewall mm -
25 -
Thickness Wear Plates mm -
30 -
Motor Power kW -
132-200
-
Type -
10-12 -
Rotor ø mm -
1000 -
Weight Hammer kg -
20 -
Thickness Sidewall mm -
25 -
Thickness Wear Plates mm -
30 -
Motor Power kW -
160-250
-
Type -
12-12 -
Rotor ø mm -
1200 -
Weight Hammer kg -
25 -
Thickness Sidewall mm -
30 -
Thickness Wear Plates mm -
40 -
Motor Power kW -
200-315
-
Type -
12-16 -
Rotor ø mm -
1200 -
Weight Hammer kg -
25 -
Thickness Sidewall mm -
30 -
Thickness Wear Plates mm -
40 -
Motor Power kW -
250-315
-
Type -
12-18 -
Rotor ø mm -
1200 -
Weight Hammer kg -
25 -
Thickness Sidewall mm -
30 -
Thickness Wear Plates mm -
40 -
Motor Power kW -
250-315
-
Type -
15-12 -
Rotor ø mm -
1500 -
Weight Hammer kg -
55 -
Thickness Sidewall mm -
40 -
Thickness Wear Plates mm -
50 -
Motor Power kW -
250-400
-
Type -
15-16 -
Rotor ø mm -
1500 -
Weight Hammer kg -
55 -
Thickness Sidewall mm -
40 -
Thickness Wear Plates mm -
50 -
Motor Power kW -
355-560
-
Type -
15-20 -
Rotor ø mm -
1500 -
Weight Hammer kg -
55 -
Thickness Sidewall mm -
40 -
Thickness Wear Plates mm -
50 -
Motor Power kW -
400-710
Type | Rotor ø mm | Weight Hammer kg | Thickness Sidewall mm | Thickness Wear Plates mm | Motor Power kW |
---|---|---|---|---|---|
8-8 | 800 | 13 | 20 | 30 | 90-132 |
8-10 | 800 | 13 | 25 | 30 | 110-160 |
10-10 | 1000 | 20 | 25 | 30 | 132-200 |
10-12 | 1000 | 20 | 25 | 30 | 160-250 |
12-12 | 1200 | 25 | 30 | 40 | 200-315 |
12-16 | 1200 | 25 | 30 | 40 | 250-315 |
12-18 | 1200 | 25 | 30 | 40 | 250-315 |
15-12 | 1500 | 55 | 40 | 50 | 250-400 |
15-16 | 1500 | 55 | 40 | 50 | 355-560 |
15-20 | 1500 | 55 | 40 | 50 | 400-710 |