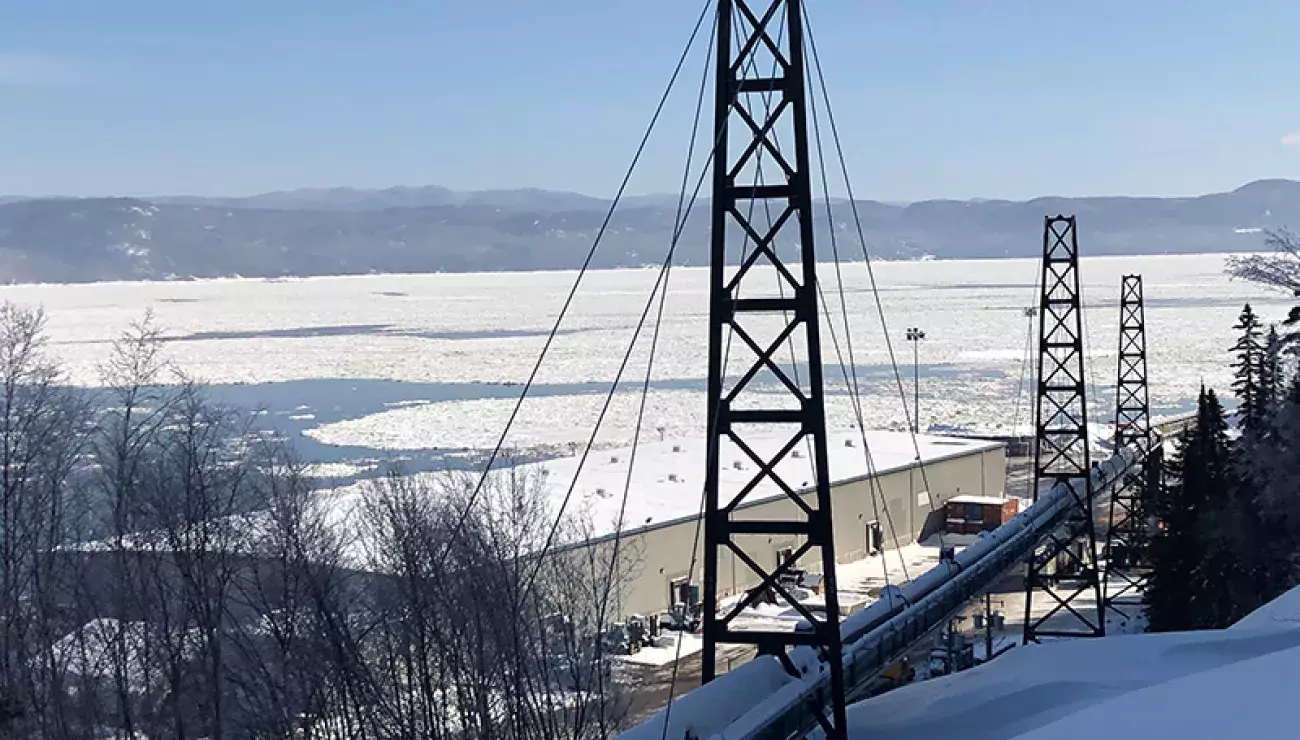
Timely inroads into Canadian market delivers wide-reaching rewards
17 Jun 2022The Canadian Government cites that its Canada Port Authorities (CPAs) handled over 340 million tons of cargo in 2020, traded with more than 170 nations, generated billions of dollars in economic output and supported hundreds of thousands of jobs. This is an impressive record, but the current global scrutiny of supply chains has magnified Canada’s attention on its Ports Modernization Review (PMR).
Canada’s PMR was launched in 2018, with the intention to assess the structure and operating environment of 17 CPAs, and it is against this backdrop that Bruks Siwertell’s technology is making its mark.
Air-cushion conveying in Québec
One of the 17 CPAs is the Saguenay Port Authority (SPA), also known as the port of Saguenay. Located in the Saguenay-Lac-St-Jean industrial region, the port is a gateway to northern Québec, and is home to the Grande-Anse marine terminal. Used primarily for the transhipment of general cargoes, dry bulk and bulk liquids, the terminal is also fed material via innovative air-cushion conveying technology from Bruks Siwertell.
The conveyors were brought online in 2020 for forestry industry operator Barrette-Chapais. They are a feature at its 210,000 metric tons/year wood pellet production plant, Granule 777, located near to the port. The facility converts processed wood offcuts and residuals from its sawmills into biomass pellets, which are then used as a renewable energy source, offsetting the use of fossil fuels at power stations.
Integral to Granule 777’s operation is its air-supported conveyor system. With a rated capacity of 800t/h for carrying wood pellets, it comprises a 100m-long Bruks The Belt Conveyor™ and a 250m-long Tubulator™. The Belt Conveyor carries material from the facility’s two pellet storage domes, before transferring it to the Tubulator system which feeds it to the dock where the pellets are loaded onto bulk carriers bound for Europe.
Both conveyor types do not use idlers under the belt, instead they rely on pressurized air to deliver low-friction, high-capacity conveying with minimal equipment wear and very low operating costs.
Barrette-Chapais opted for a system that capitalized on the distinct advantages that both types of air-supported conveyors offer. For example, the Tubulator uses suspension cable tower technology, reducing foundation requirements and minimizing construction costs. For this application, the conveyors had to span a distance of around 250m down to the dock over very difficult terrain; only three cable tower supports were needed over the entire length.
Transporting biomass pellets over long distances can be difficult without causing material degradation. The Belt Conveyor and Tubulator minimize this and also, as they are enclosed, control any dust emissions. They are proving to be an ideal solution for Barrette-Chapais and secure efficient and environment-friendly material transfer to the port.
Material flows on the Great Lakes
Further south, on the shores of Lake Ontario, is another CPA, the Hamilton-Oshawa Port Authority (HOPA). The port of Oshawa, accessed from the Gulf of St Lawrence through the St Lawrence Seaway, handles dry and liquid bulks, and project and break bulk cargo; the largest, by a considerable margin, is dry bulk, including grain and salt.
The terminal unloads material from smaller vessels from various sources to storage and then loads combined shipments onto larger vessels for export. Handling a significant proportion of the grain transfers for the port’s export facility is an air-supported conveyor system from Bruks Siwertell.
Grain is a particularly delicate cargo, prone to degradation if not handled carefully. The Belt Conveyor, installed in 2021, is able to preserve the quality of grain shipments, transferring grain from storage silos, to the ship loading system.
Like the system in Saguenay, it delivers highly efficient material transfers, with very low operating and maintenance costs.
Siwertell inquiries just keep coming
One of the aims of Canada’s modernization review is to strengthen the ability of its commercial ports to make critical investments for growth, resiliency, and global competitiveness within a low-carbon future. Therefore, in addition to the dry bulk export trade, Canada’s import terminals are also gaining attention.
“Many ports in Canada still unload bulk material with grab cranes,” explains Joanne Turnell, Bruks Siwertell’s new Canadian representative. “These have a cargo spillage rate of up to three percent, leading to huge material losses and increasingly unacceptable levels of environmental impact.
“It is no surprise then, that I am receiving a lot of interest in Siwertell screw conveyor ship unloading technology,” she adds.
Bruks Siwertell’s enclosed high-capacity Siwertell screw-type unloaders not only offer market-leading through-ship capacities, which reduce unloading times and therefore vessel costs, but they also save all the material losses from spillage and keep the jetty clean and dust-free. Furthermore, the shorter the unloading time, the greater the possibility for the terminal to increase its annual through-put and by that, also increase its profitability. Bruks Siwertell is ready to transform Canada’s ship unloading operations.
All Siwertell ship unloaders champion environmental credentials. They have a totally enclosed conveying line from the hold, where the inlet feeder draws material into the vertical screw conveyor from beneath the surface, to the receiving facility, offering close-to-zero dust emissions and eliminating any wasteful spillage. “This is essential for environmental protection, and particularly advantageous for systems that operate within urban environments,” notes Turnell.
Timber trade already benefiting
In addition to serving Canada’s growing appetite for dry bulk material handling technology in the port, the country is also no stranger to Bruks Siwertell’s wood-processing systems, with its buoyant and wide-spread timber trade already benefiting from our market-leading technology.
The majority of Canada’s lumber is exported. According to IBISWorld’s market research report, Canada’s sawmills and wood production industry, with a net worth of US 19 billion, is expected to grow steadily over the next five years, with most industry revenue expected from export sales, primarily to the US and China.
Canada’s British Columbia region produces around two-thirds of the country’s softwood, which drives the main plywood manufacturing industry. Bruks Siwertell has been serving various processed wood facilities throughout the country, including numerous sawmills. In fact, some Bruks chippers have been in operation for twenty to thirty years. Bruks cold weather stacker reclaimers are also delivering efficient material handling in Canada’s extreme climate.
Opportunities to meet
To further develop industry dialogues, network face-to-face and strengthen its presence in the country, Bruks Siwertell is attending several upcoming shows in Canada. In June, from 20th to 23rd Bruks Siwertell will attend the Association of Canadian Port Authorities conference in Toronto. Later in the year, it will be attending the Wood Pellet Association of Canada’s conference and annual general meeting between 20th and 21st September.
Turnell will be present at the events and ready to help with any inquiries about new or existing installations. Bruks Siwertell is always on-hand to offer ongoing aftersales support including spare parts, maintenance and modernizations.
If you are a Canadian operator and think Bruks Siwertell can be of any assistance to you, why not get in touch? Joanne Turnell can be reached at joanne.turnell@bruks-siwertell.com and for aftersales service support you can drop us a line at service.atlanta@bruks-siwertell.com.