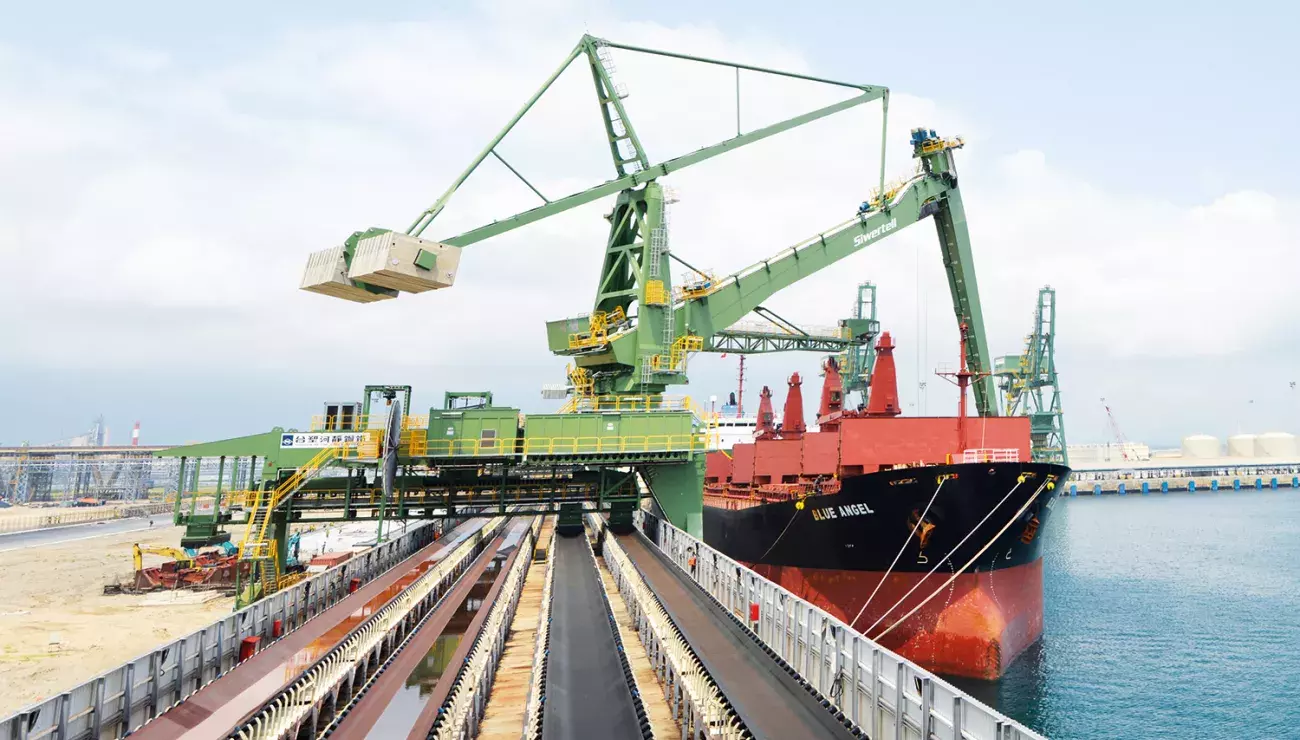
Successful start for dedicated coal intake at Vietnamese steel plant
12 Jul 2018Setting a new industry standard, Formosa Ha Tinh Steel Corporation (FHS), owned by Formosa Petrochemical Corporation (FPC), is the first steel producer to operate separate, dedicated unloading systems for coal and iron ore; key commodities required for the production of steel. This capability is debuted at its world-class Ha Tinh steel plant in Vietnam’s Son Duong Port.
Operational achievements
Meeting the plant’s coal demands for the past two years is a pair of rail-mounted Siwertell ST 940-DOB coal unloaders. They were commissioned in 2016 and in addition to their primary function handling the steel plant’s coking coal demands, are also used to discharge thermal (steam) coal for Ha Tinh’s 2,150 MW power-generating plant.
Discharging vessels up to 205,000 dwt, the unloaders handle coal at a maximum rated capacity of 2,400t/h, giving Ha Tinh a combined capacity of 4,800t/h. In a separate arrangement, iron ore is handled by two bucket-type continuous ship unloaders and a grab crane.
Since they began operating, the units have unloaded coal with significantly different properties in terms of moisture levels, fines and calorific values; certain factors have created more of a challenge. For example, coal with a high water content, in combination with clay inclusions, makes the cargo sticky and causes build-ups of material at transfer points and chutes.
“This is nothing that we didn’t factor for,” says Per Hansson, Siwertell Contract Manager. “During the equipment’s design phase, we considered all the factors that could affect handling and used computer-modelling to assess any potential problems. We took great care when choosing component materials; an approach that has proven invaluable. The unloaders have demonstrated their ability to handle all types of coal excellently and we have received very positive feedback from FPC.”
Contract promises fulfilled
At the time of the contract, Siwertell guaranteed a through-vessel capacity equal to 70 percent of the rated capacity, meaning a discharge rate of 1,680t/h per unloader, or 3,360t/h for both, meaning that it takes about 60 hours, on average, to unload a 200,000 dwt Capesize vessel.
The unloaders have undergone a series of performance tests to confirm these contract promises. The first two tests, designed to look at energy consumption and the rated capacity of the unloaders, produced excellent results.
“The tests undertaken so far demonstrate that a 70 percent through-ship capacity is fully achievable,” highlights Mr Hansson.
Quick turnarounds generate huge cost savings
The screw-type unloaders achieve these high efficiency rates because unlike grab cranes, they maintain a steady discharge rate, regardless of the level of cargo in the hold, right up to the hold clean-up stage. At the beginning of operations using a grab crane, the grab only travels a very short distance to reach the cargo; however, as more bulk material is unloaded, the distance the grab must travel into and out of the hold increases, gradually reducing efficiency. Performance is decreased further when the cargo drops to the point that the grab cannot pick up the material.
“So if a steel producer uses a grab crane with the same-capacity as a Siwertell unloader, it only offers an efficiency factor of about 55 percent and would take about 75 hours to unload a similar vessel; 15 hours more than a Siwertell unloader,” explains Mr Hansson.
Figures in 2016 anticipated that Siwertell’s high discharge rates could deliver cost savings of around USD 2.5 to USD 3 million per year, because of the significant reduction in the time vessels spend on the jetty. “Savings on the scale that we estimated proved difficult for FPC to ignore,” says Mr Hansson.
Sensitive approach for a green-field giant
The Ha Tinh plant is a significant industrial milestone for Vietnam. FPC, part of Taiwanese conglomerate Formosa Plastics Group, recognised that Southeast Asia had become one of the most significant iron- and steel-consuming areas of the world, but did not have the necessary capabilities to meet this demand. Therefore, the Ha Tinh facility was specifically developed to reduce the region’s dependency on imported raw steel.
Under construction since 2008, the facility was built on a green-field site under strict environmental regulations. For its part in minimising the environmental impact, the Siwertell coal unloaders are totally-enclosed all the way from the inlet device, which transfers coal from below the cargo surface in the vessels’ holds, to the transfer points on the steel plant’s three coal-handling jetty conveyors. This ensures minimal atmospheric pollution and no spillage. Three more conveyors handle the iron ore intake.
Ha Tinh will ultimately have six blast furnaces, making it one of the largest steel plants in the world. It will have a number of planned expansion capabilities, initially designed for a maximum steel production capacity of 7.8 million tonnes/year; this will rise to 10 million tonnes/year and eventually could be as high as 20 million tonnes/year.
Decisions based on experience
FPC has experience of three types of ship unloaders – screw, bucket and grab – at its Mailiao Plant in Taiwan, says Wei Yu, Siwertell’s representative in Taiwan, who has worked closely with the company throughout the project. It has found that the Siwertell machines have higher efficiencies than their counterparts and since taking delivery of its first unit, FPC has procured Siwertell machines for plants all over the world.
Mr Yu adds that the dual-intake arrangement adopted at Ha Tinh is most suitable for green-field plants that produce large amounts of steel.
Reputation for reliability
To safeguard the long-term success of FPC’s investment, Siwertell delivered a comprehensive training program to ensure that the unloaders perform at their maximum operational efficiency.
Since commissioning, the units have been characterized by seamless operational performance and high coal outputs. They only require wear part maintenance every second year, as long as regular maintenance recommendations are followed. Wear parts are those that need to be replaced after a certain number of running hours. Wear part lifetime is influenced by the way the equipment is used. With skilled personnel operating the unloaders and a good maintenance regime, the lifetime of components can be extended. For example, Siwertell predicts that the vertical conveyors will easily last four-to-five years at the planned operational pace. With proper maintenance and correct operating practices, their lifetime will be increased.
The unloaders are equipped with a number of sensors indicating the operational health of the equipment. They also have important redundancy and safety systems.
For example, the rail-travelling machinery is designed to function if one or more drives should fail and if the power supply should fail during unloading operations, the machines have an emergency operation system that allows the operator to manoeuvre the machine out of the vessel and safely park it. Anti-collision systems eliminate collisions between the unloaders as well as unloader impacts on vessels.
A watchful eye
Securing this contract with FPC was particularly important to Siwertell as it ignited the interest of steelmakers around the world, eager to assess the benefits that its dedicated coal unloaders could offer their new or existing steel plants.
“We are not the only ones that are watching the success of Ha Tinh with great interest,” says Mr Hansson. “Other operators are also keeping a watchful eye on the success of this facility to assess the level of benefits dedicated intake systems could offer their new steel plants; or even their existing ones.
“For so many years, the steel industry has been hesitant to invest in separate intake systems and has traditionally used the same unloading equipment for coal and iron ore; grab cranes or bucket chain unloaders. We are hopeful that Ha Tinh will continue to showcase what a change in technological approach can deliver to this industry,” he concludes.
PLEASE CONTACT US FOR MORE INFORMATION
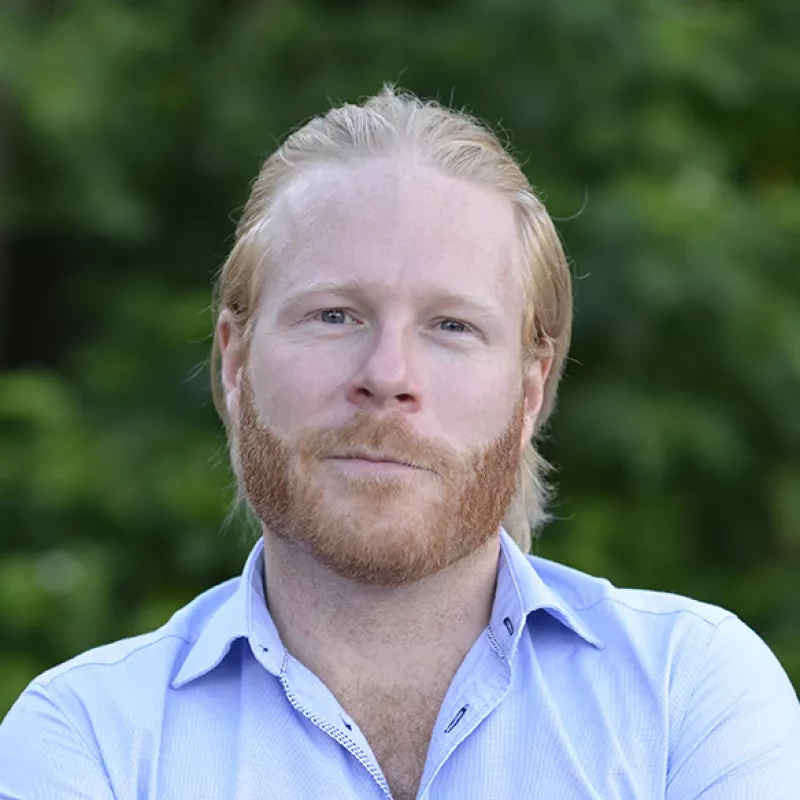
Categories: Bulk unloading