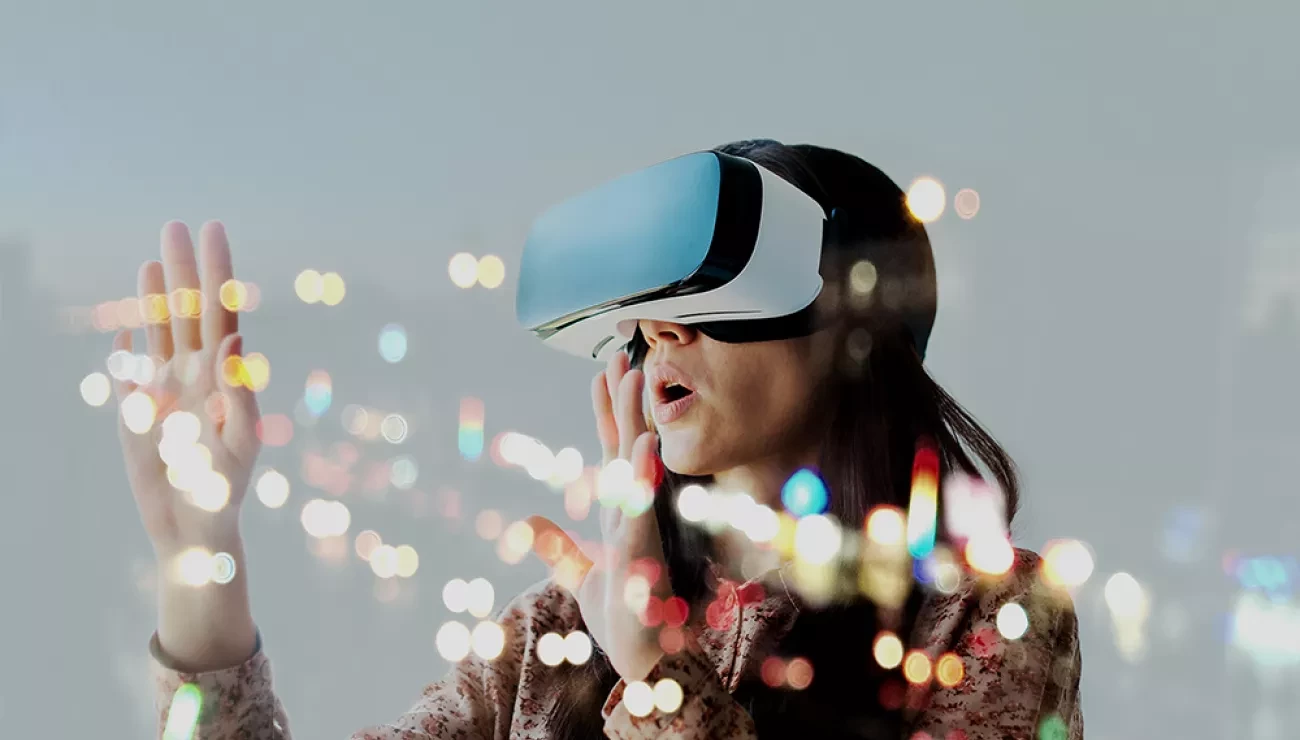
Simulation-based design and training sets new safety and efficiency standards
16 Sep 2019From structural analyses and operation planning to equipment installations and service personnel training, Siwertell is creating value through simulation and virtual reality
The changing nature of the dry bulk handling industry has created an environment that demands innovative and flexible design and training solutions. To meet these demands, Siwertell combines long-standing industry knowledge with the latest advances in simulation-based technology to deliver a complete package of market-leading equipment, cutting-edge training techniques and troubleshooting tools.
A new perspective
For example, during the design phase of all new installations, as well as to ensure successful outcomes in upgrade projects, Siwertell carries out structural and flow simulations.
“The main advantage of using simulation in the design process is the ability to identify and fix any potential problem areas to prevent real-life operational issues,” explains Zoltan Habony, Calculation Engineer at Siwertell. “In recent years, the development of new technology has provided the tools necessary to simulate and analyze the strength properties of larger machine components.”
Fatigue and corrosion are key factors in the deterioration of ship unloaders, which can lead to equipment failure and costly repairs. A crack in the structural steel can be fixed in a vast number of ways, but if it is not carried out correctly, the fix itself could cause even greater damage than the original problem.
“By using simulation, Siwertell can evaluate the options and employ the best solution,” Mr Habony notes. “We can also test the dynamic load resistance of a machine exposed to fast loads for short periods of time, such as during an earthquake.”
Smoothing material flows
“Flow simulations are not new to Siwertell, but we have traditionally used manual and other skilled methods, for estimating elements such as engine effects and chute material flow transitions. We have now begun to simulate flows numerically using the discrete element method (DEM).
“Predominantly used as a research and development tool to get a better understanding of material flow in conveyors, transfer points and chutes for the design of standard equipment, numerical flow measurements also help us determine the cause of equipment problems. These can include plugged chutes or inefficient conveyors, and provide a clear solution.
“Using DEM, we can rule out designs that are not effective, saving time and money in the long-run, making it possible for engineers to peer into the material flow in ways that are not possible in real life,” Mr Habony adds.
Data quality dictates outcomes
When it comes to simulation, selecting the correct input parameters for replications is crucial. “Input data for simulation models is simply the details entered into the system for analysis, such as equipment problems, geometry, material properties, boundary conditions and loads. The quality of the input data is the greatest influencing factor on the quality of the output; the questions we ask in the simulation,” he stresses.
“Experience is very important to correctly interpret the results from a simulation, but if the simulation is based on incorrect input data, no amount of experience can salvage the simulation. In short, you only get out what you put in. Therefore, it is vital to collect data from the actual material handled on site.”
Currently, there is no open database for DEM simulations. To ensure the input data is correct, Siwertell has a specialized laboratory where it gathers input data from material samples from live sites.
Wider potential of VR
Siwertell is also planning to introduce virtual reality (VR) training for its service personnel and for operators. This is designed to enhance knowledge and thereby improve safety and efficiency.
Using VR headsets, users will be able to explore a simulated ship unloader, which is positioned in a realistic 3D landscape almost 30m above ground level. “Advanced simulation provides invaluable training opportunities,” says Mr Habony. “By imitating real-life working scenarios, users learn how to operate equipment safely without the risk of damaging the machine or the ship.
“We also see that VR has much wider benefits besides training and design simulations. Other uses could include virtual commissioning, used, for example, by our electrical engineers to verify the functions of a machine, and customer demonstrations. These could really show a machine’s potential to meet any number of customer needs,” concludes Mr Habony.
PLEASE CONTACT US FOR MORE INFORMATION
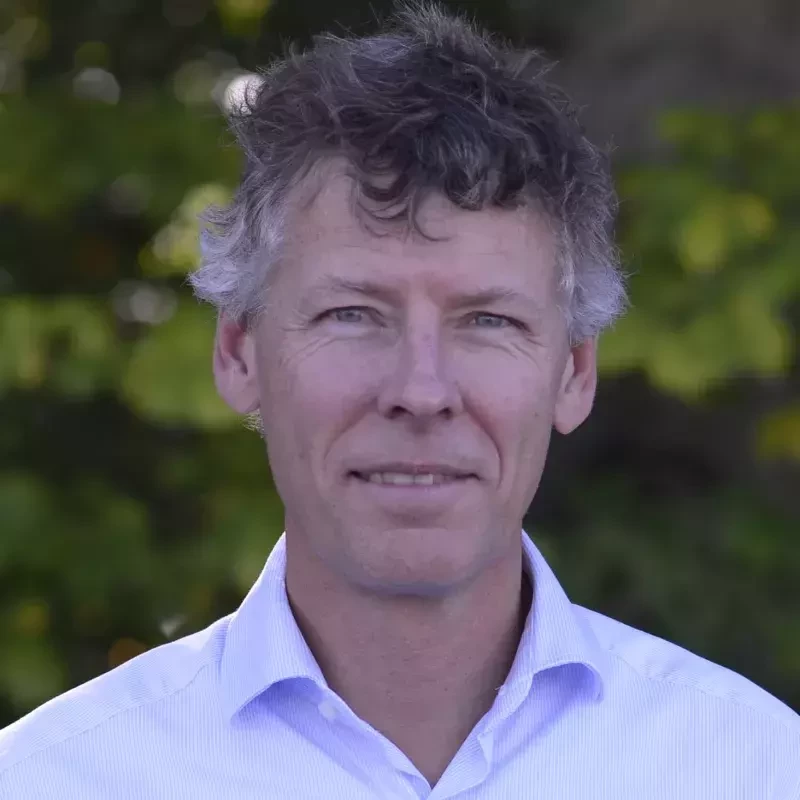