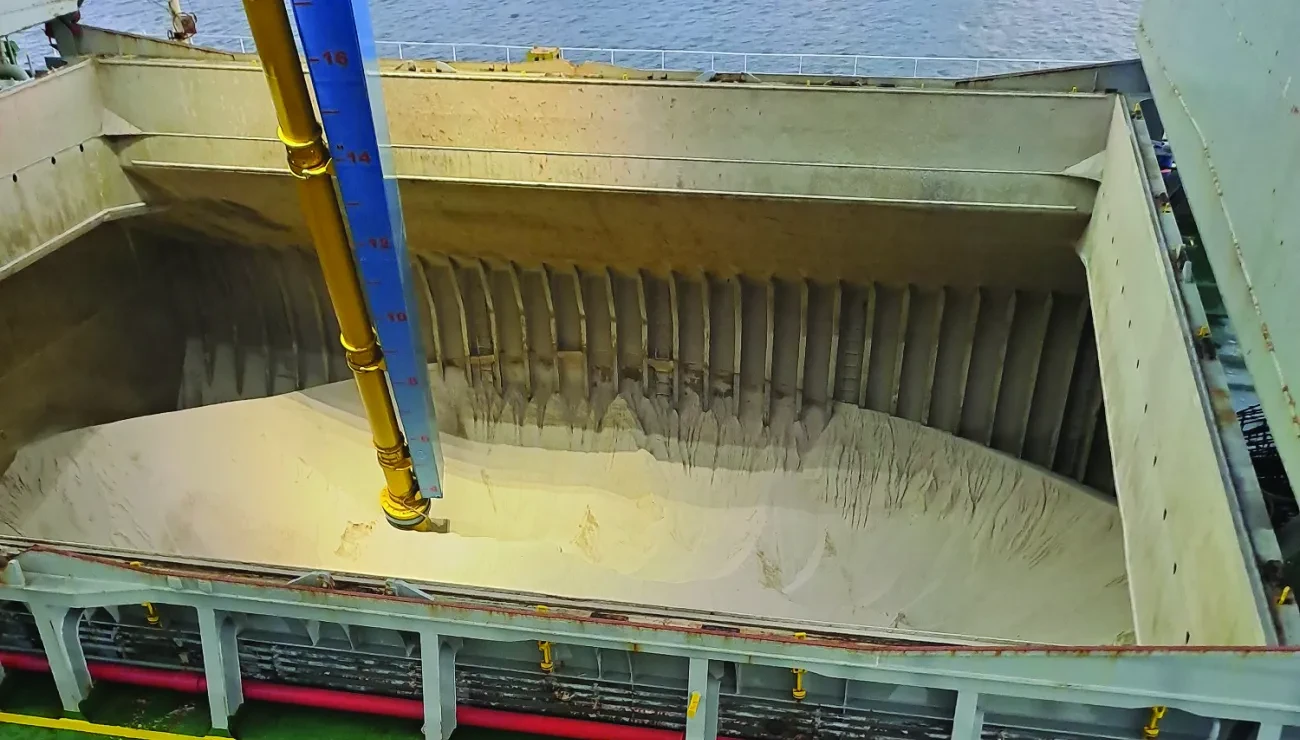
Revolutionizing sulfur handling with Siwertell technology: an Indian success story
7 Apr 2025The transformation of bulk sulfur handling at Paradeep in India, is testament to the impact of adopting innovative solutions; with each new installation, Siwertell ship unloading technology is not just handling sulfur, it is handling a sustainable future
As the sun rises over India’s bustling ports, a quiet revolution is taking place in how operators handle one of the world’s most critical, but challenging, commodities: sulfur. Vital for the production of fertilizers that sustain India’s agricultural heartlands, along with numerous other essential industrial processes, the efficient, environment-friendly, and safe handling of sulfur is paramount to sustainable growth.
Enter enclosed, screw-type Siwertell ship unloading technology, a name synonymous with innovation and reliability in dry bulk handling, including its capability to transform a port from an environmental, safety and efficiency perspective.
One of its most evident impacts is on the global import of bulk sulfur. Highlighting a notable success story, is the revolutionized sulfur import operations of Paradeep Phosphates Limited (PPL), part of the K K Birla Group and the OCP Group of Morocco.
PPL is one of India’s leading private-sector stakeholders in phosphatic fertilizers. It currently has a total capacity of three million metric tons, of which 2.60 million metric tons are phosphates, with urea as the balance. The company has two large manufacturing units at Paradeep, Odisha and at Zuarinagar, Goa.
PPL’s Paradeep terminal is in the Mahanadi River delta. Here, it takes deliveries of sulfur, muriate of potash (MOP) and rock phosphate, constituents of high-performing fertilizers. Key materials for boosting productivity in India’s enormous centers of food production, which provide direct and indirect support for 70 percent of its population, according to the World Bank.
Like many, India is a country with growing agricultural needs, heavily reliant on these materials, and with consumption expected to rise significantly, efficient fertilizer import and handling processes are critical.
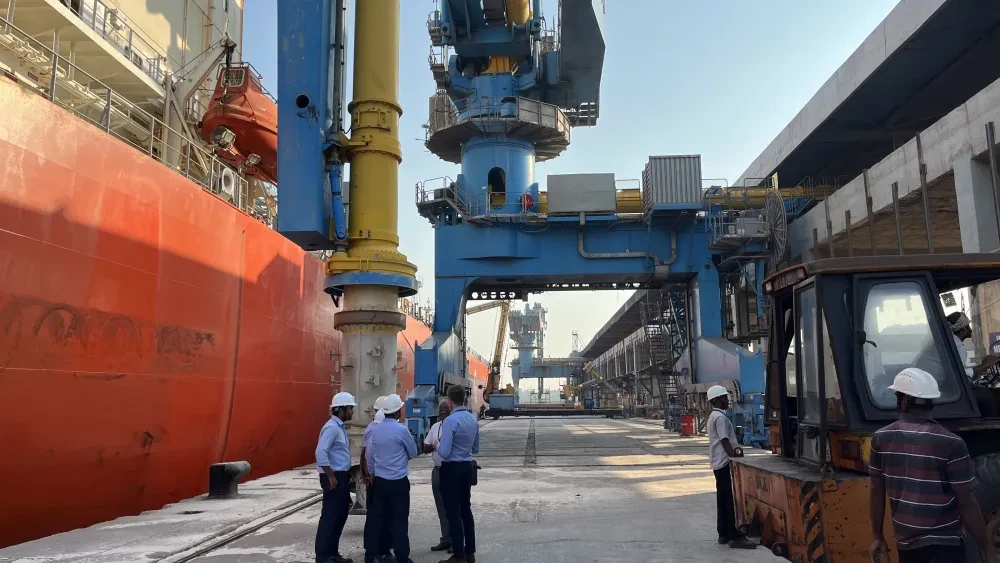
The need for change
Traditional methods of sulfur handling, often involving grab cranes and bucket chains, have numerous drawbacks, including exposure to the elements, potential for environmental contamination, pollution and health hazards from the inhalation of sulfur dust.
The corrosive impact of sulfur on dry bulk handling equipment can also be hugely problematic, along with its volatility and explosive tendencies once confined. In response to these challenges, PPL embarked on a research project to identify a solution that would not only enhance efficiency, but would also mitigate the risks associated with sulfur handling. Its journey led the company to Bruks Siwertell, and a customer partnership that would lead to the total transformation of one of India’s major ports, Paradeep.
PPL did its homework. It visited a Siwertell sulfur-handling installation in Fremantle, Australia, where an operator had successfully been using a Siwertell ST 640-D ship unloader for discharging vessels of up to Panamax size.
The system is fully enclosed, submerging the counter-rotating inlet feeder beneath the level of the cargo, and enabling it to discharge entire shipments of sulfur without spillage, or dust clouds from avalanches within the ship’s hold. Transfer points within the conveyor are also sealed to prevent fugitive sulfur dust.
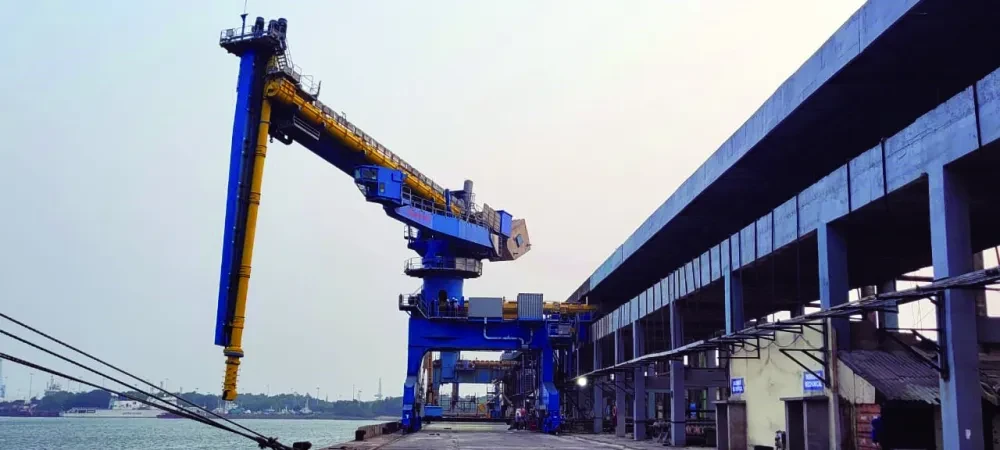
Benefit hard to ignore
PPL saw the benefits of the use stainless-steel components throughout the dry bulk handling equipment to prevent corrosion and formation of ferrous oxide within the unloader. Furthermore, critical to all sulfur handling Siwertell ship unloaders, is the Siwertell Sulfur Safety System (4S); developed by Bruks Siwertell from decades of proven industry installations.
The 4S system aims to minimize the risk of explosions during sufur unloading. If an explosion does occur, it ensures the safety of operating personnel and the integrity of the machine by mitigating any potential damage.
The 4S comprises various safety functions such as fire prevention, detection, suppression, and extinguishment. It reduces the occurrence of an explosive atmosphere by minimizing dust generation. Also, sensors within the unloader stop its operation if hot and/or glowing material is detected within the conveying line. A suppression system relieves any pressure in the conveyors and at the same time, a fire-extinguishing system activates to put out any fire.
PPL also decided that a rail-mounted ST 640-D unloader would be the right tool for the job, and in 2005, took delivery of its own, installed on the quayside at Paradeep.
What followed was the elimination of pollution both to air and sea, yielding a marked transformation for workers at the terminal, and a new era of port operations, consigning the clouds of yellow dust to the past.
The screw-type ship unloader is able to seamlessly switch between its three essential dry bulk cargoes, handling sulfur at a continuous rated capacity of 1,600t/h, rock phosphates at 1,300t/h, and MOP at 1,000t/h, without requiring any additional measures to be taken between shipments.
Not long after PPL’s initial order, neighboring terminal, the Indian Farmers Fertilizer Co-operative Limited (IFFCO) took note, and put in an order for a Siwertell ship unloader. Commissioned in 2011, it has replaced a grab crane previously used at the terminal, and now imports sulfur using its own ST 790-D unloader. This larger model handles bulk sulfur at a rate of 1,800t/h, and rock phosphate at a rate of up to 2,100t/h. Dust collectors at the unloader’s transfer points further prevents the emission of dust to the surrounding environment.
A sustainable future
The successful transformation of the port does not end there. In 2021, responding to yet further increases in demand, Paradeep became home to a third Siwertell ship unloader when PPL placed its second order for a Siwertell ST 640-D. This was commissioned in 2023 and now, PPL has the ability to unload sulfur at a rate of some 2,900t/h, enough to empty a 60,000 dwt bulk carrier in less than a day.
With the third endorsement of Siwertell unloading technology in Paradeep within the space of a decade, thanks to the state-of-the-art cargo handling technology, Paradeep and PPL can now meet its safety and environmental requirements, while leveraging ample additional capacity to support not only India’s continuing role as an agricultural powerhouse, but its exciting future growth prospects.
The transformation at Paradeep is a testament to the impact of adopting innovative solutions. For port operators across India and beyond, following PPL’s lead with Siwertell technology is a step towards a safer, more efficient, and environmentally sustainable dry bulk handling. With each new installation, Siwertell technology does not just handle sulfur; it is handling the future of dry bulk operations.
PLEASE CONTACT US FOR MORE INFORMATION
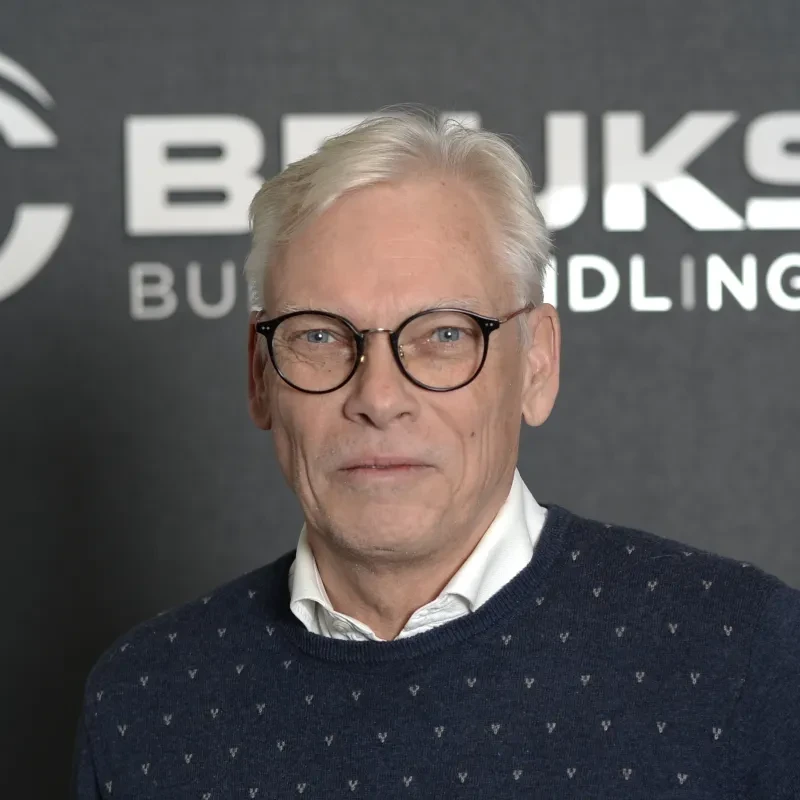