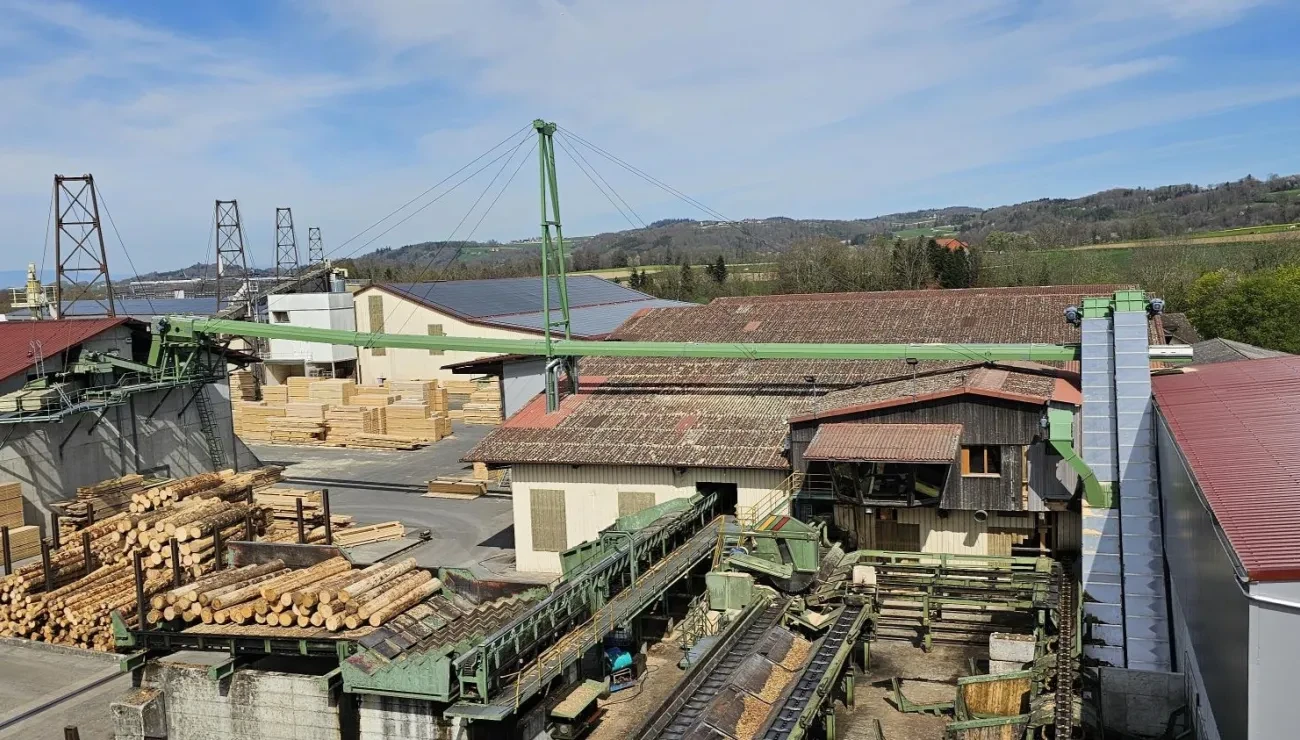
Byproduct handling at Swiss sawmill boosts sustainability and capacity
23 Apr 2025Industrial sawmills are highly efficient process-driven facilities. But even for cutting-edge installations, processing boards or planks results in as much as half of a log being classified as byproduct. The sawmill wood residue market has provided a bioeconomy stream that has grown significantly in recent years as global eyes look for renewable energy sources.
According to the European Sawmill Industry’s annual report 2024, with the ongoing energy transition, sawmill residues are expected to experience increased demand in the coming years. It also stressed that: “Policy makers should take account of the potential of the bioeconomy, mapping their resources and evaluating the economic potentials. This includes supporting and facilitating industrial symbioses, where wastes and residues from one sector/company can be a resource for other producers.”
Looking to the future
Established in 1904, family-run Scierie Zahnd, situated in Rueyres, in the canton of Freiburg, is the largest sawmill in the French-speaking part of Switzerland and the country’s second largest softwood sawmill. In 2023, Scierie Zahnd made the decision to modernize and increase the capacity of its sawline, replacing its entire sawmill disposal system; comprising a package of long-serving Bruks Klöckner sawmill byproduct handling technology.
Many years of reliable service from its existing equipment led Scierie Zahnd back to Bruks Siwertell company, Bruks Klöckner, for its technology and expertise in sawmill waste wood residue handling and processing. Over this time, Scierie Zahnd and Bruks Klöckner have worked well together, establishing a trusting, effective long-term partnership.
The new sawline became operational in 2023, with a total annual cutting volume of 180,000m³. As the plan was to increase this to 200,000m³ a year by 2025, the machinery had to be designed to accommodate this capacity increase, which it does.
A good result
“We are very satisfied with both the quality of the material used and the service provided by Bruks Siwertell,” says Damien Zahnd, Manager, Scierie Zahnd. “Bruks Siwertell understood our needs and requirements and implemented them in an excellent way. The results met our expectations. The machines are running reliably and efficiently, and our collaboration was professional and efficient.”
Bruks Klöckner carried out the installation and commissioning of the completely new disposal system within four months. “Clear agreements were made, and all the deadlines were met. Despite the limited time available, everything went very well,” Zahnd adds.
Central to the sawmill’s byproduct processing and handling system is a horizontal Bruks DH400 (550) drum chipper with an infeed width of 1,000mm. A powerful 315kW motor enables the industrial chipping machine to process more than 50m3 (stere) of sawmill byproducts an hour.
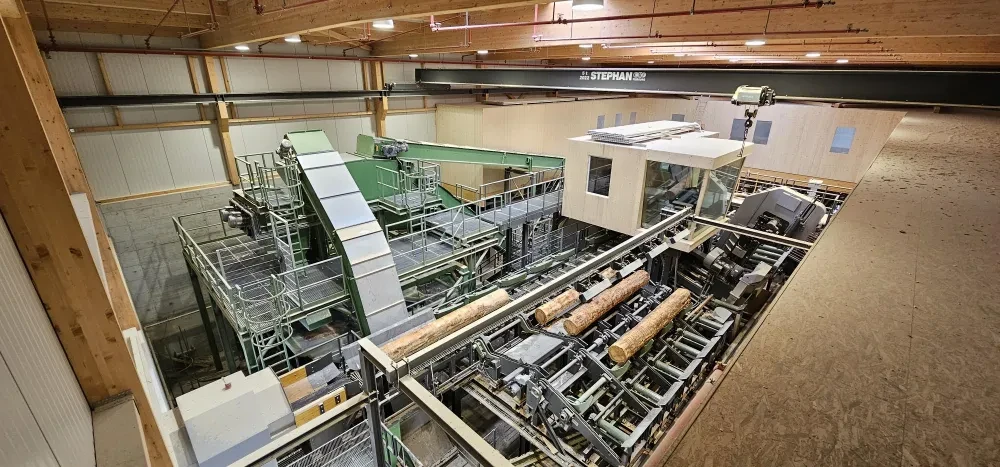
Advanced, proven technology
“As part of the mill’s capacity increase, the entire waste disposal system was modernized and is now state-of-the- art,” explains Josef Keßler, Project Manager, Bruks Klöckner. “Our collaboration during the project was excellent and based on professional trust from the outset. For example, the entire sawmill was filmed with drones so that the 3D data could be used by us in the planning phase.
“The new system is very similar to the original, but the technology has advanced, and includes new features with maintenance and wear-reducing benefits,” Keßler adds.
For example, the chipper features replaceable metal strips under the chopping blades and replaceable metal sheets near the counter blades. This ensures that when they have worn or become damaged, it is not necessary to replace the entire rotor, only individual parts, increasing the service life of the rotor and minimizing maintenance downtime.
Efficient conveying connections
In addition to the drum chipper, the delivery also included scraper chain conveyors, conveyor belts, vibrating conveyors, hanging screens and two air-supported Tubulator conveying systems, positioned alongside each other.
The two 61m-long Tubulator conveyors require only one structural support each, and allow for the integration of efficient conveying systems within limited spaces. They transport wood chips and sawdust from the sawmill hall to containers and silos. Previously, this was undertaken using a scraper chain conveyor.
“Thanks to the air-cushion technology and a belt speed of up to 130 m/min, the new Tubulators achieve an extremely high conveying capacity with low drive power, which reduces the overall energy consumption of the plant. Compared with high-maintenance, mechanical conveyor technology, the lack of abrasion in the conveyor channel saves the customer a lot of maintenance time,” says Patrick Wicharz, Area Sales Manager, Bruks Klöckner.
The entire package of technology was manufactured from Bruks Siwertell Group companies, showcasing the range of wood-processing and handling capabilities available to its customers.
A textbook plant
“Bruks Klöckner was responsible for the entire planning, delivery, assembly and commissioning of this textbook plant, with the exception of the control system,” notes Wicharz. “Our system is linked to the higher-level control system. With plants of this size, we usually also supply the control system and offer various services as well as maintenance. In this project though, Zahnd took on this task because the sawmill has its own technical department.”
The system has now been operational for almost two years and is meeting the sawmill’s planned capacity increases. All Scierie Zahnd byproducts, amounting to around 250,000m³ of bark, wood chips and sawdust a year, are transported to the neighboring Enerbois biomass power plant and pellet production mill.
Once at the mill, they are either processed into ENplus-certified wood biomass pellets or used to generate electricity. In 2023, the mill’s pellet production output was 20,000 metric tons, making a positive contribution to the renewable energy market.
Sawmill byproducts and secondary wood residues currently account for around a third of wood harvests destined for energy use and the growing bioeconomy. The importance of effective byproduct handling and processing machinery within modern sawmills is therefore essential, underpinning their overall efficiency, capacity and sustainability, much like the Bruks Klöckner installation at Scierie Zahnd.
PLEASE CONTACT US FOR MORE INFORMATION
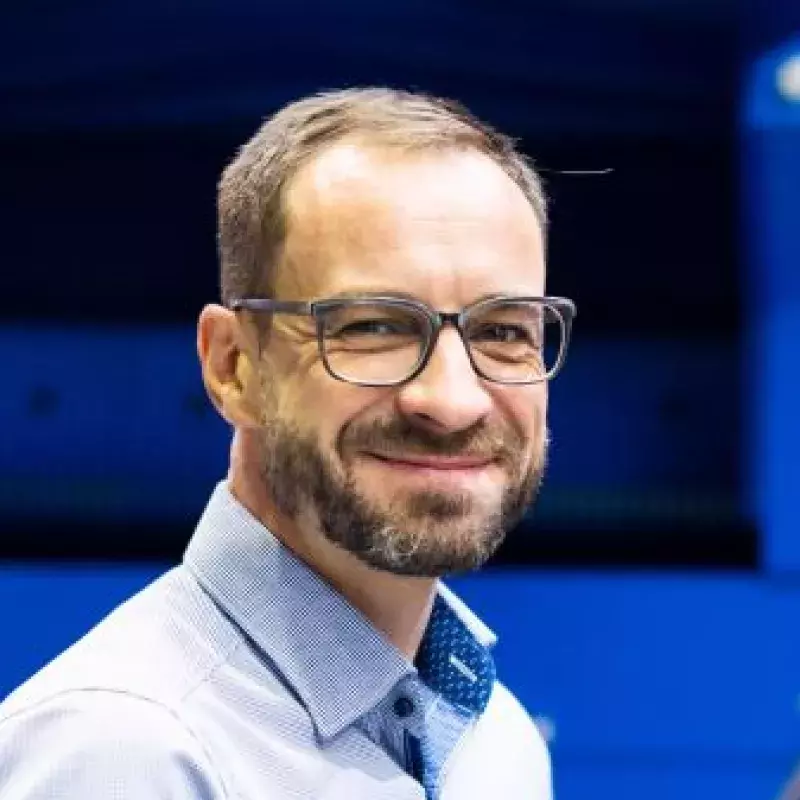