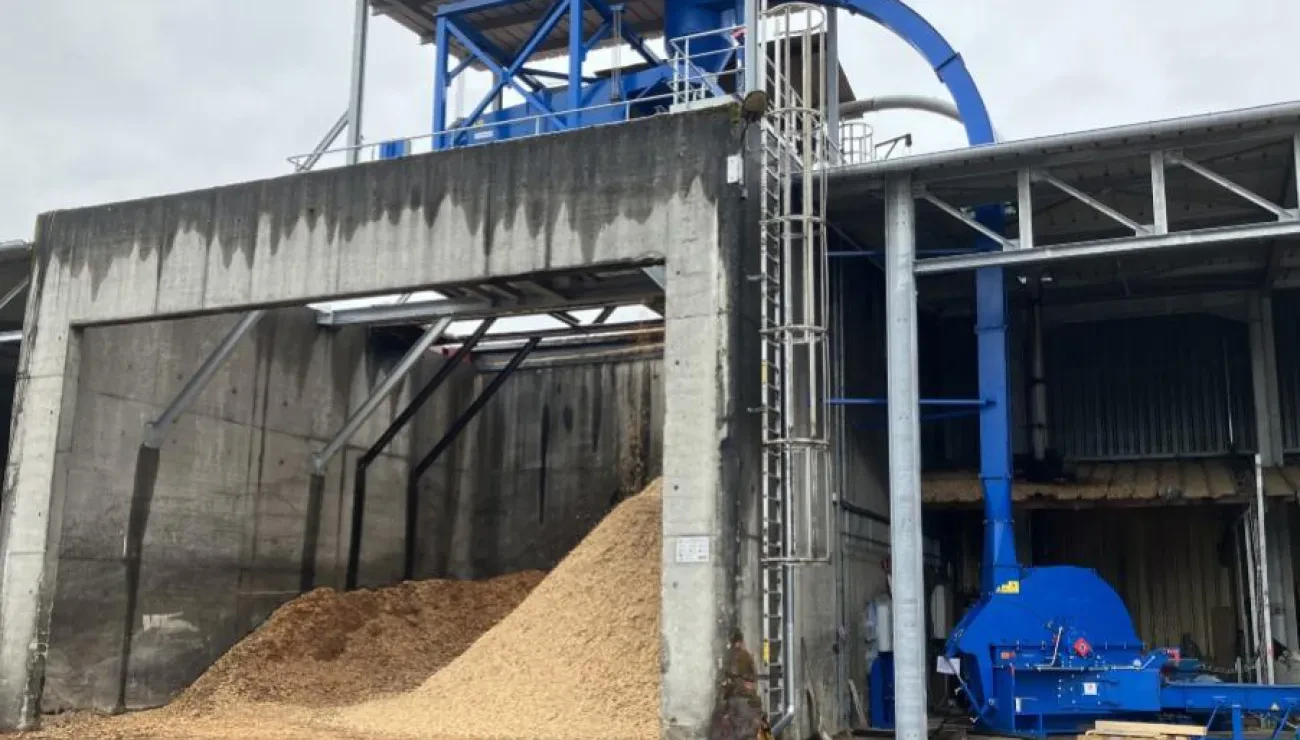
Integrated chipping line increases reliability and efficiency at French sawmill
24 Mar 2025Modern sawmills are highly efficient, process-driven facilities, where unplanned interruptions to operations can have a significant impact on production yields. A critical part of their process efficiency is the byproduct handling and processing system.
The Steinbourg sawmill, Scierie et Caisserie de Steinbourg, in northeast France, which has specialized in beech wood for over fifty years, needed a new chipping solution to enhance its byproduct handling and processing efficiency and mitigate unplanned downtime.
As a long-standing customer, Steinbourg turned to Bruks Siwertell Group company, Bruks Klöckner, for an integrated industrial disc chipper installation to bring increased reliability, efficiency, and operational flexibility; essential for its future sustainability and capacity ambitions.
Exceeding operational expectations
“The new Bruks line didn’t just meet our expectations, it exceeded them,” says Francois Schnepf, Managing Director, Steinbourg sawmill.
“For our wood chip production, we need consistently high quality, which can only be achieved with a machine like the one from Bruks Klöckner,” continues Schnepf. “After more than ten years of collaboration, we see Bruks as a European reference for such technologies. We were particularly impressed by the machine’s ability to easily process even challenging materials, such as pieces of dry or fresh beech wood in different sizes.”
For the Steinbourg installation, which was completed at the beginning of 2024, Germany-based Bruks Klöckner supplied a horizontal-fed RH 2000 disc chipper, designed specifically for chipping hardwood, particularly beech, with a 470mm infeed and a powerful 160kW main drive motor. Equipped with five precision-engineered knives, the chipping disc has a substantial diameter of 1,990mm.
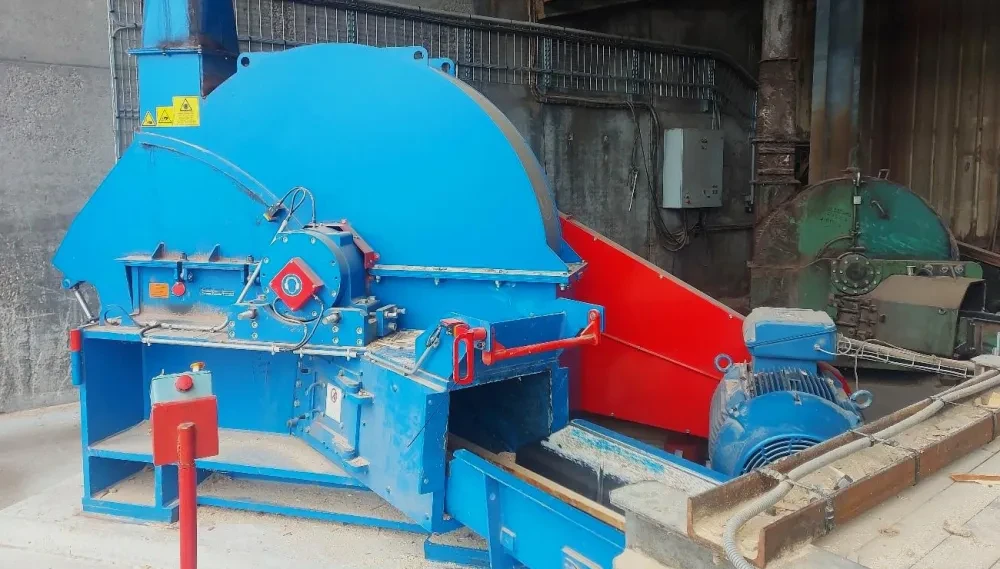
Overcoming hardwood challenges
The industrial chipping machine efficiently processes and shreds sawmill waste, including splinters, bark, and beech cuttings. It has a rated capacity of up to 20t/h and enables the plant to simultaneously chip residual wood generated during the sawmilling process.
Chipping short, dry hardwood pieces to achieve consistently high-quality output presents a notable challenge for many machines, mostly because of the wood’s density, coupled with the variation in feedstock size.
To deliver precise control over wood chip size, Bruks Klöckner’s design solution included the integration of an SH 8/2 free-swinging chip screen, which separates oversized pieces, and an additional DG 200 x 400 secondary drum chipper for processing them.
Additionally, a key hurdle to overcome in the system’s design was the height difference between the chipper and the screening system. Structural conditions dictated that the chip screen and secondary drum chipper needed to be installed on top of an 8m-high concrete wood chip silo. This required a precise assessment of static and dynamic loads.
The Bruks Klöckner solution incorporated the use of fan blades mounted on the chipping disc to propel the wood chips up to the vibrating screen at a discharge height of 12m, eliminating the need for an additional blower.
Long-term efficiency and flexibility
The system also prioritizes energy efficiency, with frequency converters for the main drive motors optimizing power consumption. The refined knife geometry further enhances energy savings, making the operation as cost-effective as possible.
Furthermore, chipping lengths can be adjusted on the disc chipper, within defined size ranges, to meet developing market demands. This flexibility enables the Steinbourg sawmill to expand its customer base and adapt to changing requirements, as and when different wood chip lengths are required.
To maintain redundancy and operational continuity, the new machine was installed alongside the sawmill’s existing disc chipper. The flexible infeed technology allows residual wood to be processed through either system without requiring extensive modifications, ensuring a seamless transition to the new line and enhanced reliability.
Customer-centric solutions
Bruks Siwertell works closely with customers to ensure that projects can be undertaken with minimal disruption to daily operations. For this installation, the existing chipping line remained operational, requiring very careful planning.
“Communication with Bruks was outstanding from day one,” notes Schnepf. “The team was highly flexible in implementing necessary adjustments and overcoming structural challenges. Their efficiency and reliability ensured that the project was completed on time, which was a key factor for us.”
Prior to the new installation, unplanned downtime was causing production issues. A combination of advanced chipping capabilities and a state-of-the-art integrated Bruks Klöckner solution now enables the Steinbourg sawmill to meet its capacity demands, but also secure the operational reliability, efficiency and future market agility that it required.
PLEASE CONTACT US FOR MORE INFORMATION
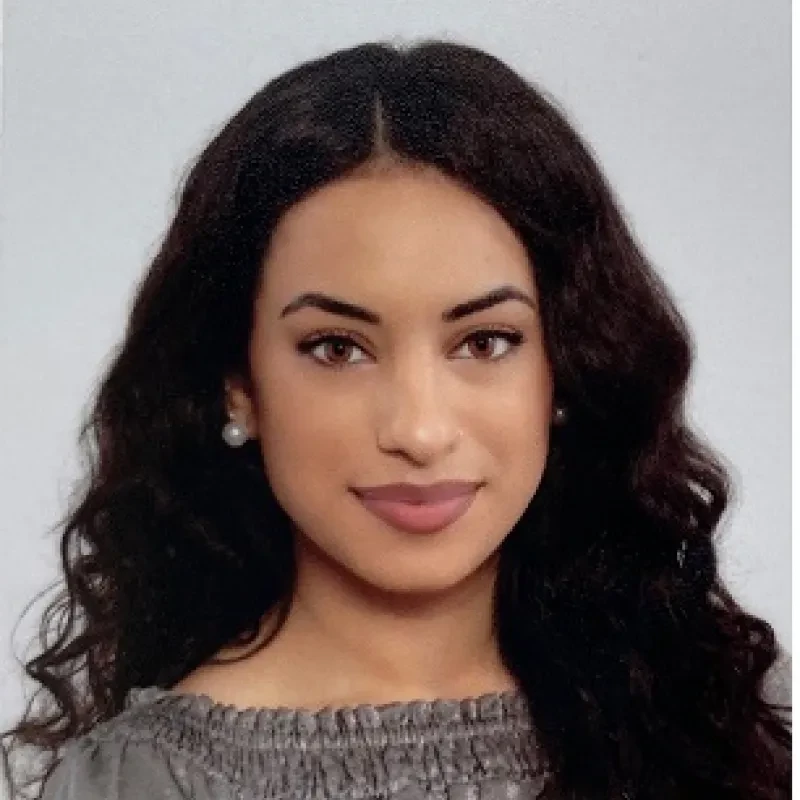