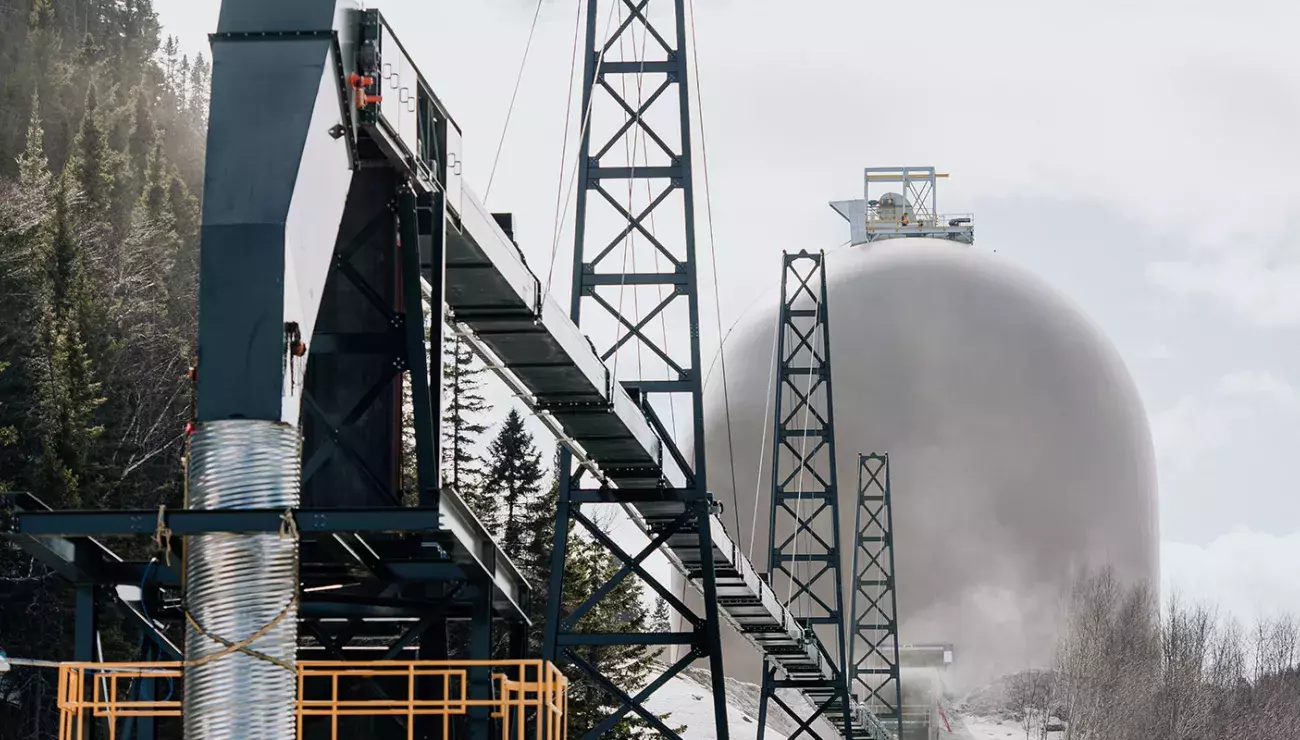
Installation is one thing, upkeep is another
15 Nov 2021Belt conveyors are some of the most widely used and relied upon material transfer systems in the world. They made their debut in ports in around 1795 and, in one guise or another, remain ubiquitous today.
Different developments have seen them adapted to various industries, from the first roller conveyor patent, filed for in 1908 by Hymle Goddard, to Henry Ford incorporating them into automobile assembly lines in 1913, today’s conveyor belts are an industrial mainstay. So, why look again at their design?
For all their amazing qualities, such as high-capacity conveying, robustness and relatively inexpensive installations, they are incredibly maintenance heavy. They rely on a flat, rubberized belt stretched over unpowered rollers, or idlers, positioned at intervals of about 1.2m. When these are scaled up, spanning huge facilities, there may be thousands of rollers, each requiring oiling and maintenance to ensure that it does not seize up, cause friction, and therefore potentially lead to a fire.
Aside from equipment wear, there are also other elements that often need addressing with traditional idler belt conveyors, including material degradation, spillage, and dust emissions.
Advantages worth considering
Bruks Siwertell has one of the most comprehensive range of conveyor systems available to the market, and each is specified depending on their application, from very high-capacity traditional belt conveyors, to totally enclosed robust screw conveyors and those that employ the use of pressurized air. Our air-supported conveying systems are gaining industry interest because they are offering some unique advantages to operators.
In a nutshell, low-friction, air-cushion conveyors eliminate rollers, and therefore deliver huge benefits in terms of operational and maintenance costs. On top of this, they offer high-capacity conveying with no material degradation and minimal equipment wear.
Bruks Siwertell’s air-supported conveyor range comprises the Tubulator™ and The Belt Conveyor™. In addition to the significant reduction in maintenance and operational costs, by eliminating rollers, the ‘bumpy ride’ caused by the belt passing over the idlers and idler sag – the dip in the belt between rollers – is also removed, along with material degradation.
Idler sag can also lead to material roll back at greater inclines. Both systems, but especially Tubulators, can reach angles that would not be possible using traditional idler conveyors.
Tubulators were introduced to the market several years ago, and now have over 620 installations worldwide. They are extremely effective at handling lower density materials, such as cement, shredded waste, grain, and sugar, and especially those liable to degrade easily and therefore generate more dust.
The Tubulator and The Belt Conveyor are closed systems ensuring no spillage or dust emissions. They both use pressurized air beneath the belt, but this is delivered in different ways for each conveyor type.
For the Tubulator, sectioned into 12m-long steel tubes, enabling them to fit into a 40ft standard shipping container, a rubber belt runs at high speed on top of an air cushion created by a series of in-line fans.
Because of their structural integrity and significantly reduced weight, they require fewer supports and are easier to install over existing equipment when compared with traditional conveyor frames, so can, in fact, be installed at considerable heights. Tubulator conveyors are self-supporting up to 25m, and have a free-span of up to 80m when using cable towers, or up to 30m between standard supports.
The Tubulator is an ideal enclosed conveyor system for very specific applications that need some or all of its unique capabilities of low-friction, idler-free conveying in addition to high, long, and potentially steeply inclined installations.
Expanded conveying capabilities
The Belt Conveyor, does deliver something commercially different. Customers were asking for an air-supported conveyor that could carry a wider variety of materials and incorporate features of both the Tubulator and conventional conveyor design. These were the reasons that Bruks Siwertell embarked on its development program.
Instead of using a pipe enclosure, The Belt Conveyor uses a central air manifold to provide the air pressure to suspend the belt. Each three-meter section of the belt has access to a common header of pressurized air, and under the carry-side pan is a three-meter pressurized air enclosure system, otherwise known as a plenum. Air pressure sensors and flow meters along the length of the belt ensure the optimum amount of air is delivered for the weight of the given cargo, reducing running costs.
The Belt Conveyor offers flexibility, and can handle higher-density materials using standard belts and standard parts, which reduces costs. It has a simple modular design with a cradle that supports a formed carrying trough and covers. This is the same shape as a 35-degree idler conveyor, so that it still meets industry-standard calculations for the USA’s Conveyors Equipment Manufacturers Association (CEMA).
Basic components include the head and tail unit and three meter-long intermediate sections. The only moving parts are the head and tail pulleys. Third-party components, like weigh-scales, metal detectors, magnets and material sensor areas, can all be incorporated as well.
A commercial reality
In 2020, one of the largest manufacturers of containerboard and corrugated packaging in the United States took The Belt Conveyor into use at its highest-volume mill in Tennessee. The conveyors were added as part of a new log-line to increase the capacity of the plant.
At this mill, the same system is being used for three different types of material, bark, unhogged bark and wood chips. The requirements of these three materials are similar, but still distinct. Hogged bark, for example, contains high levels of dust.
The new fully-enclosed conveying system comprises a 1,400 mm (54 in) belt-width x 122m (400 ft) long conveyor, which handles wood chips at 550t/h; and two further conveyor units, one 1,000 mm (36 in) x 39.6m (130ft) and one 1,000 mm (36 in) x 91.4m (300ft), for handling hogged and unhogged bark at a rate of 60t/h. The belt conveyor systems were manufactured at Aztek Technologies in Monterrey, Mexico.
Also in 2020, Barrette-Chapais’ new 210,000 metric tons/year wood pellet production plant, Granule 777, in Quebec, Canada, commenced operations using a combination of both Tubulator and The Belt Conveyor technologies.
With a rated capacity of 800t/h for carrying wood pellets, its air-supported conveying system comprises a 100m-long The Belt Conveyor and a 250m-long Tubulator. The Belt Conveyor carries material from the facility’s two pellet storage domes, before transferring it to the Tubulator system, which feeds it to the dock where the pellets are loaded onto bulk carriers, bound for Europe. The combination offers the plant extraordinary levels of efficiency, environmental protection, and through-life operational and maintenance savings.
Interested?
Bruks Siwertell has a test facility in Whitesburg, Georgia, USA, specially built to showcase the performance capabilities of The Belt Conveyor against other commercially available designs. It is open to the public upon request.
Located near Atlanta Hartsfield International Airport, about one and a half hours from Bruks Siwertell’s Alpharetta, Georgia, office, operators are able to bring their own materials to run at the facility. Through live demonstrations, Bruks Siwertell is able to answer questions and it is a very practical way for customers to test The Belt Conveyor’s capabilities using materials they handle on a daily basis.
The facility is also used for continuing research and testing products in various applications with different materials.
PLEASE CONTACT US FOR MORE INFORMATION
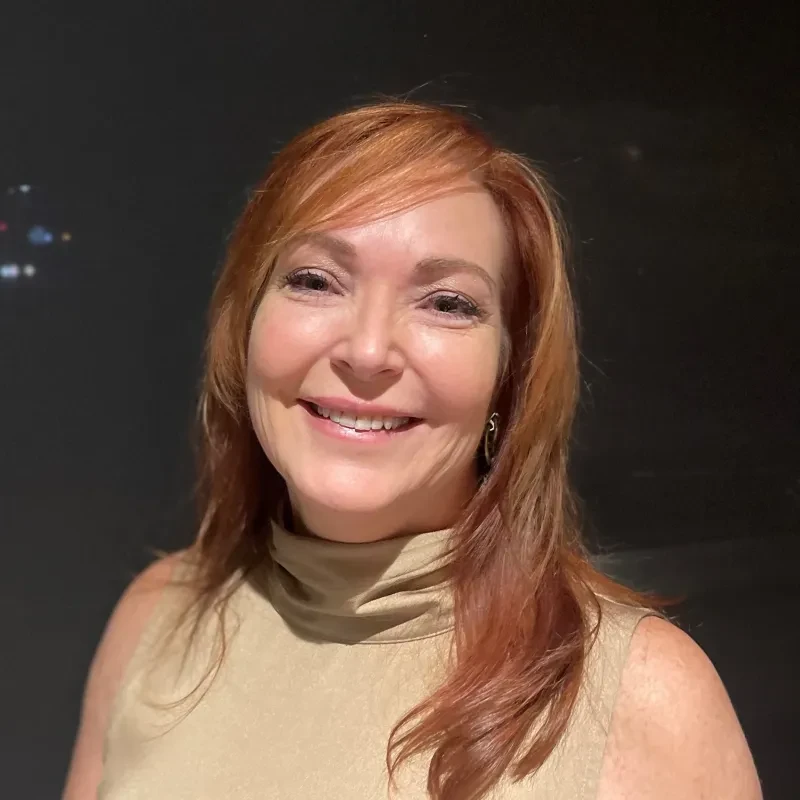