
Cutting-edge developments in mobile chipper range
24 Nov 2021Bruks Siwertell has upgraded its series of 806 ST/STC model chippers to new specifications, allowing for better chipping mechanics as well as more sparing use of consumables like fuel and hydraulic oil, and contributing to the goal of improving sustainability across the Bruks Siwertell product range.
Converting atmospheric CO2 into a building material, namely wood, and in some cases even a circular-economy as fuel, the forestry industries already have great potential for improving humanity’s environmental footprint, something under discussion at the recent COP26 conference in Glasgow, Scotland.
Some wood biomass is created by turning logs, offcuts, and forestry residues into chips, and then processing these further into pellets. This relatively new type of fuel is in the process of replacing coal in power plants across the world, performing a vital role in improving countries’ CO2 emissions using existing energy infrastructure. It also provides an answer to the question of grid-balancing, something that will become more important as humanity moves away from fossil fuels.
As this segment expands in the coming decades, Bruks Siwertell is ready for the increase in demand for its range of mobile chippers. With this, there is an understanding that our products must maintain their cutting-edge, and this is why, back in 2018, Bruks Siwertell introduced the 806.2 model, after working through an 83-point improvement action list. This included quality enhancements related to the chipper unit, feed table, and chip bin.
But we have not stood still. Since then, Bruks Siwertell has decided to revisit the real nuts-and-bolts of the system, concentrating efforts on the genset, realizing new efficiencies via digitalization, as well as updating the hydraulic system. This has yielded the 806.3 model.
Working in the woods
For chipping that takes place in remote locations, and within the forest, reliability is key. Power sources must be compact and robust, capable of providing the high-torque properties that chipping requires, while making the best use of the fuel supply available on-site, both from an environmental and operating cost perspective.
Fortunately, engine manufacturers are getting very good at squeezing the maximum energy from a specific quantity of fuel. The new Scania DC13 313A, launched in late 2020, develops 500 horsepower while meeting with EU Stage V regulations; the most stringent emissions requirements for non-road engines. Its brake-specific fuel consumption of 189g/KWh puts the unit among the highest-efficiency engines of its type in the world. For the 806.3, Bruks Siwertell has updated the installation to support the maintenance and service of this engine.
Meanwhile, the 806.3 is governed by a new electrical control system, which uses the proprietary software system Intelligent Mobile Chipping (IMC). From a large 25cm (10 inch) touchscreen, an operator is able to adjust the chipping settings based on the variables of the material types, the weather conditions, and the performance of the engine; optimizing both the input of material and the output of chips based on the engine’s optimal curves. Using these techniques, operators can save fuel and reduce maintenance costs for the engines. The user screen also displays reversing cameras. Cab controls are minimal and easily accessible and the cabling is well protected with all interfaces designed for easy installation and maintenance.
Reducing carbon footprints
Bruks Siwertell has also designed a new hydraulic system for the 806.3. Its hydraulic oil tank now has a patented CycloneConcept insert, which vents the return oil and allows the necessary volumes of hydraulic oil to be vastly reduced, and therefore the size of the tank. As a result, environmental impact is minimized, along with operating costs, and the overall carbon footprint of the system is reduced.
The hydraulic valve for the chipping unit’s cylinder functions has also been moved from the engine cage to a position behind the chipper, which enables the cylinder hoses to be shorter and a larger space in the engine cage enables easier access during servicing.
With all these changes, we have worked to future-proof a product that is already working hard to deliver the best value to our customers in the forestry and wood-processing sectors and offer enhanced environmental benefits. Our customers will find that this approach is common to all Bruks Siwertell equipment, across our entire range.
PLEASE CONTACT US FOR MORE INFORMATION
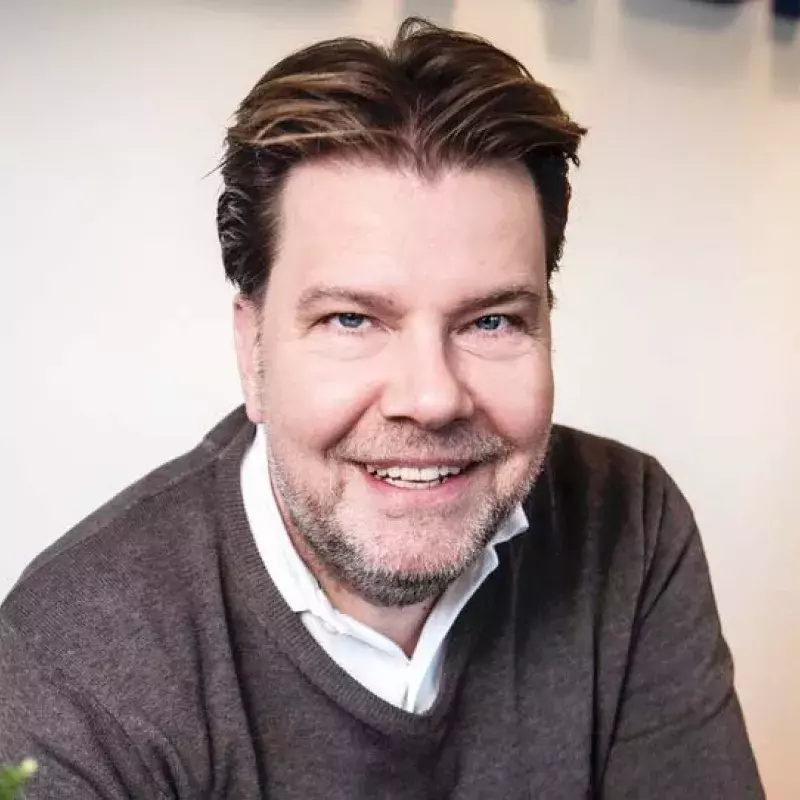
Sales & Market Manager Forest • Mobile Chippers
Christian Ehn
+46 706993110