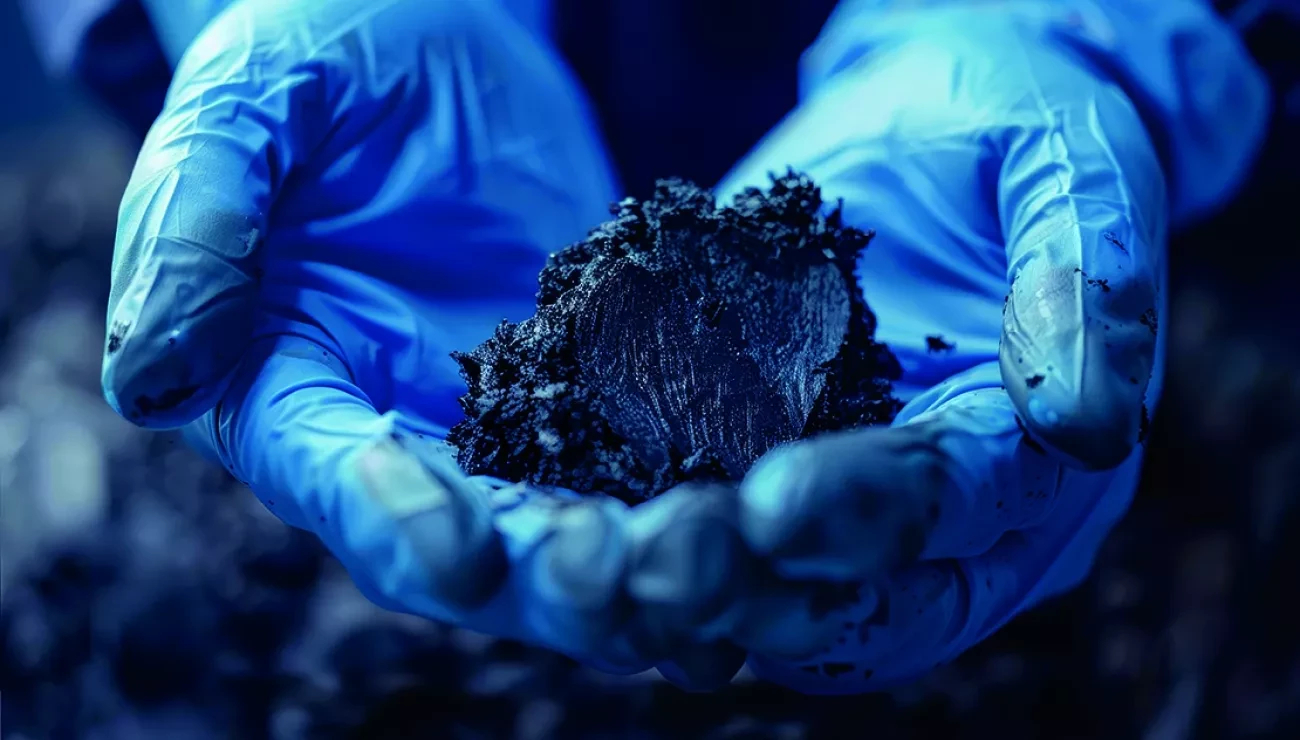
We are ready for the biofuel revolution
26 Aug 2024Even if humanity woke up tomorrow to find every kilowatt of fossil fuel energy replaced with wind, hydroelectric, solar and nuclear, there would still be work to do. Reversing the effects of climate change will be a matter of reducing the CO2 already in the atmosphere, as well as preventing more. Any realistic decarbonization scenario will necessarily include both.
Fortunately, this is possible. Originally, carbon capture was thought of as a way of stripping CO2 from ambient air. But now in the early stages of commercialization, it looks a little different. Power plants want to use the technology to continue providing energy without contributing to greenhouse gas emissions, and are in the process of developing carbon capture, utilization and storage (CCUS) mechanisms to enable them to do it.
Returning atmospheric carbon
Biochar is one. An interesting new notion, its uses could be various, being chemically and physically identical to charcoal. But one of the most exciting of these is the prospect of using biochar to put carbon back in the ground, burying it as a sequestration mechanism. Plants turn atmospheric carbon into solid mass, hence biomass, which could, in due course, be turned into biochar, and buried, as fossil fuels once were. If this process could be performed using renewable energy, it could be a very efficient way of returning atmospheric carbon to the Earth.
Though various strategies for burying CO2 have emerged recently, including pumping the gas into disused oil wells in the North Sea, burying biochar could be much more straightforward logistically and could solve many environmental problems at once. Biochar can even assist the growth of crops in some climates, though the mechanisms are not yet well understood.
If there is to be a biochar revolution, it need not happen from scratch. This is because Bruks Siwertell has pioneered technologies that are very effective at handling various grades of coal, charcoal, wood, and other forms of biomass. In fact, Bruks Siwertell is able to offer these emerging decarbonizing, biofuel and bioenergy industries decades of expertise by being able to efficiently handle, process, convey, store and reclaim virtually any type of dry bulk; and the largest material that the company handles is wood.
Decarbonizing transport
As a means of reducing emissions, the hard-to-decarbonize shipping industry is making moves toward green e-methanol as a fuel, which will require a bio-based feedstock. Methanol is manufactured by combining hydrogen made with renewable energy, with a source of carbon – in the case of green methanol, a non-fossil ‘biogenic’ one. This means that biomass would be a feedstock for yet another industry sector, adding additional pressure for stakeholders to make the best possible use of what raw material supply is available.
Indeed, there is a limit to what amount of carbon could be captured and recirculated in this way. There are only so many feedstocks which can truly be considered ‘residual’ from other production processes, and raising production over this level would generate more unnecessary carbon, and defeat the purpose of the exercise, yielding fuel which is just as polluting and more expensive to refine than conventional fossil fuels.
As well, the initiative will only work if the world’s agricultural sector gets involved. Research published by the UK’s Royal Society recently finds that as much as 68 percent of UK agricultural land would have to be devoted to production of sustainable aviation fuel (SAF), to provide the 12.3 million metric tons of fuel needed by UK airlines alone.
However, investigations are underway in the US, Asia, and in much of Europe, to explore the extent to which biomass might be able to stand in for various fossil fuels. If large amounts of plant biomass can be grown, harvested, and converted into SAF, in a way that does not threaten ancient forests or food production, it would absorb CO2 from the atmosphere while it is grown, and return it when burned, creating a circular carbon economy.
We understand biomass
The largest material that Bruks Siwertell handles and processes is wood. Its equipment portfolio spans every stage of biomass logistics chains, from harvesting through to processing and transportation within global port terminals.
Cellulose fiber, found in plant-based biomass material such as corn stalks, is a mainstay for biofuel production. Bruks wood processing equipment can easily turn to processing, handling and storing these materials. Bruks screening equipment can separate different grades and sizes of wood fractions; debarking systems and butt-flare reducers on cut tree trunks can make use of waste wood and leave products in a prime condition for onward processing; and heavy-duty chipping, and milling and grinding machines, designed to handle tough, valuable raw materials like tree stumps and offcuts, already operate globally.
Machinery such as this operates across the processed wood industries from paper mills to particleboard plants. These facilities are very accustomed to making the most of limited raw materials, and using what fractions of wood waste are available.
“Situated at paper mills, sawmills, engineered board plants and biomass pellet manufacturers, our equipment is already widely participating in and offering benefits to the wood handling and processing supply chain,” says Ken Upchurch, Vice President, Sales and Marketing, Bruks Siwertell. “Innovation in this area has always been vitally important, but it becomes even more so when what raw material is available is shared between a greater number of stakeholders.”
The next link in the chain
If done right, biochar could take over from many of the applications for which charcoal is used today. But, as well, Bruks Siwertell has been supporting the transition away from using coal at power plants, instead using biomass pellets.
At facilities around the world, Bruks wood processing equipment is used both in biomass plant production processes and in the biomass supply chain. Systems such as the Tubulator™ and The Belt Conveyor™ are used to carry biomass pellets from one part of the manufacturing plant to another. “These air-supported conveying systems offer huge advantages to the biomass sector,” continues Upchurch. “They eliminate rollers, which not only ensures minimal material degradation, but they are very cost-effective operationally and dramatically reduce maintenance costs in comparison to idler belt conveyors.”
In the port, biomass expertise continues with both ship unloading and loading systems ideally placed for handling delicate volatile cargoes such as biomass. To date, Siwertell ship unloaders have clocked-up around 100,000 hours of safely unloading biomass in ports.
“These systems are just one of a number of ways Bruks Siwertell has adapted to new bulk cargoes that have come to prominence as a result of the green shift,” says Upchurch. “We have been on this journey for some time, and we already know the particulars of handling biomass and wood. The message with respect to these emerging industries is clear: we are ready and we can handle it.”
PLEASE CONTACT US FOR MORE INFORMATION
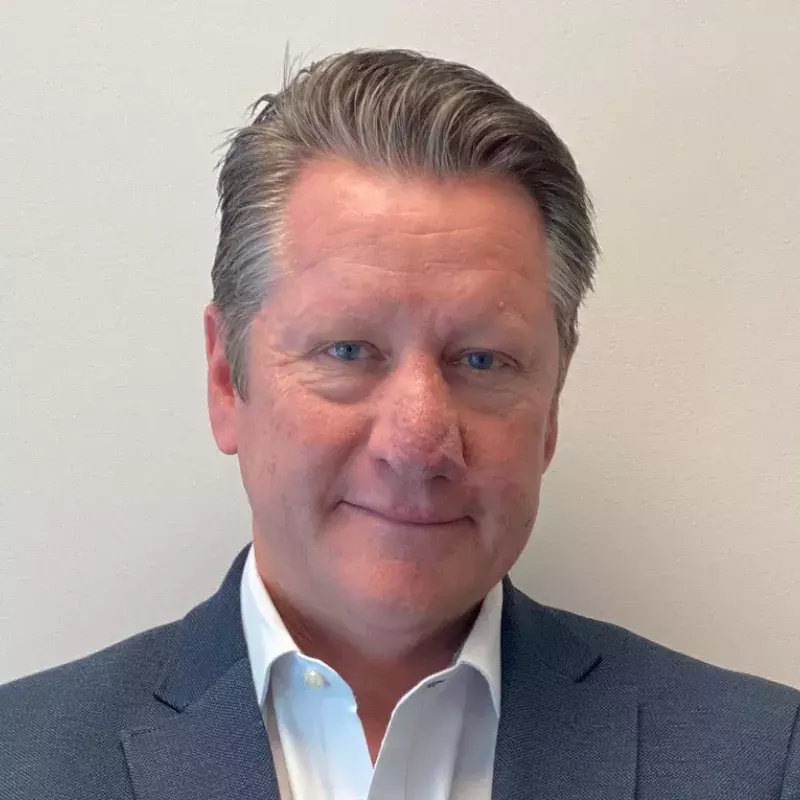
Senior VP, Sales & Marketing, Bruks Siwertell Inc.
Ken Upchurch
+17709056023