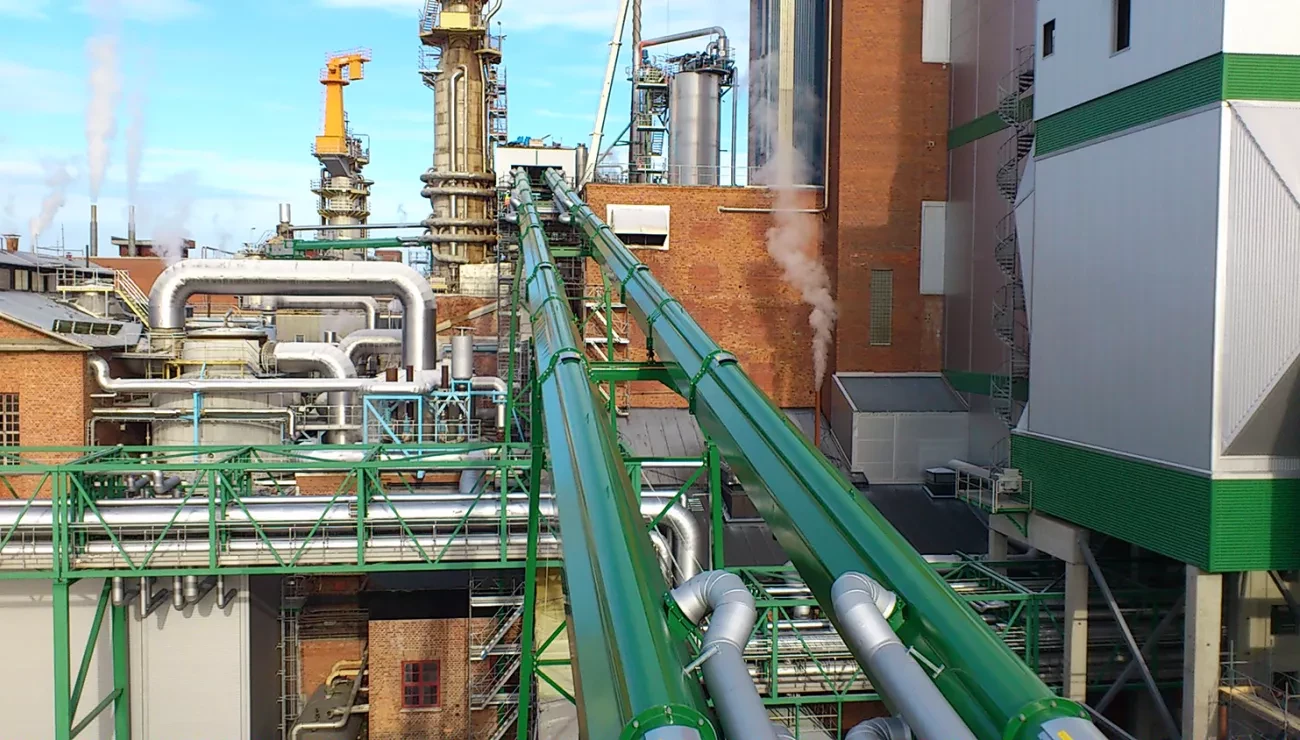
Waste takes flight: securing the path to sustainable aviation
11 Mar 2024To meet demand for sustainable aviation fuel (SAF), new types of manufacturing plant and very high-capacity wood-processing technology will be needed for the task; fortunately, Bruks Siwertell is on hand with the expertise already.
Within the broad scope of changes to be implemented to achieve decarbonization targets, there are a number of so-called ‘hard-to-decarbonize’ sectors. Prominent candidates, among others, are cement and steel production, and aviation.
Aviation contributes to greenhouse gas emissions at a higher rate, compared to its output, than other forms of transportation, accounting for approximately three to four percent of total greenhouse gas (GHG) emissions, according to United Nations (UN) figures. This is roughly equivalent to the collective emissions of all cargo ships. Some studies, such as those conducted by the Netherlands’ Technical University Delft, even suggest that aircraft’s contribution to climate change might reach as high as five percent, owing to the intricate interactions of aircraft fuels in the atmosphere.
The importance of decarbonizing aircraft cannot be ignored. But this is also extremely challenging. While battery-electric planes are proving feasible on short-hop intercity routes, there is little prospect of recharging them in midair, ruling them out for long-haul flights. Aircraft will need to use jets, not propellers, if the industry is to avoid a backward step in technology. This means using large amounts of pure, light, compact, high-octane liquid fuel, with vast chemical energy content.
These demanding requirements have been challenging to meet even by refiners of conventional fossil fuels. Although the aviation industry has demonstrated a willingness to radically alter aircraft designs to suit different types of fuel – notable among them, various design proposals for hydrogen aircraft by Airbus and Honey-well – challenges related to storage and payload capacity have tempered expectations. The large tanks required for hydrogen would leave room for only a few passengers or limited cargo. A number of e-fuel alternatives such as methanol and ammonia are also under consideration, but ultimately will be unlikely to make the grade, for the same reasons.
This leaves fuels which are close to like-for-like replacements for fossil fuels. In fact, such fuels do exist; they are high-purity, dense compounds, liquid at room temperature, and refined from existing waste products. They are similar enough to existing fuels that they can be ‘dropped-in’ to replace existing air-craft fuel with a minimum of fuss, ensuring a smooth transition, and are known as sustainable aviation fuel (SAFs). Derived from waste and residue streams, supply of these fuels is developed with a focus on ecological sustainability and minimal GHG impact.
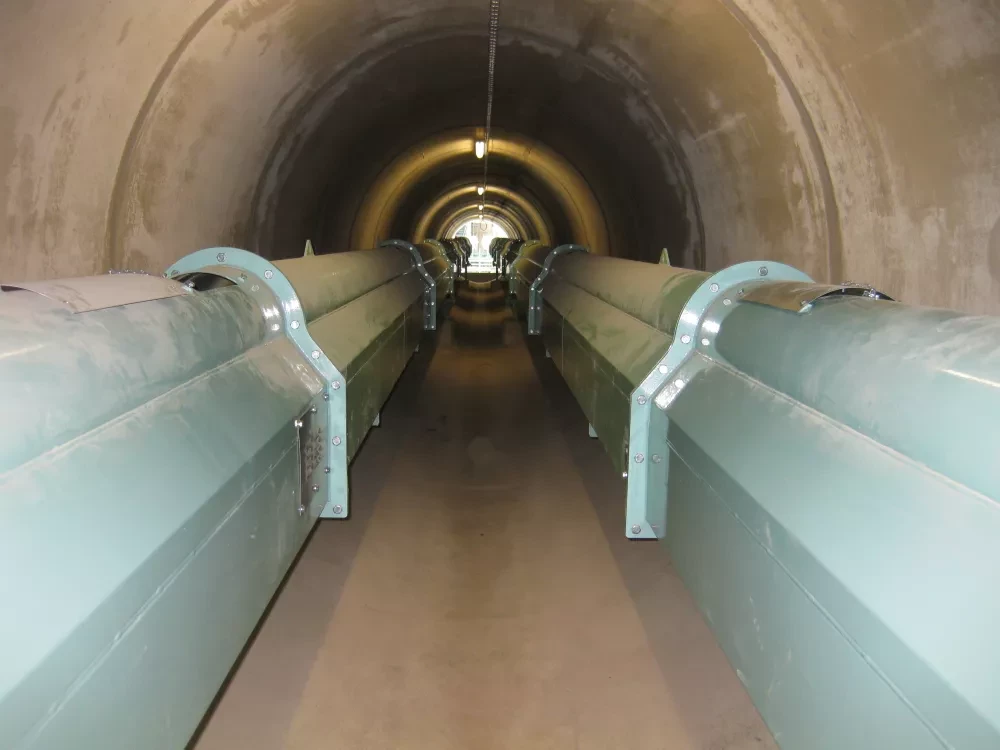
Green sky thinking
In September 2023, the European Union (EU) Council passed a law mandating that SAF should make up 34 percent of all aircraft fuel supplied at EU airports by 2040, and 70 percent by 2050. Included within the ‘ReFuelEU aviation’ package was a further provision banning aircraft from ‘tankering’ – carrying extra fuel into European airspace to avoid having to refuel with SAF at an EU airport.
The measure underscores the increasing recognition of SAF’s potential to drive decarbonization within the aviation sector, and the limited viable alternatives. Even airlines seem relieved with the decision to favor SAF. “Ryanair believes using SAF is the most realistic and effective method for aviation to reduce emissions in the coming decades,” the Irish low-cost airline said in a statement. “We welcome the European Parliament’s decision to adopt SAF mandates under the ReFuelEU regulation, which will apply to all flights departing a Union airport and follow the ‘polluter pays’ principle.”
SAF is not one fuel but an umbrella of new ones, based on different grades of biomass. The feedstocks of SAF are various, but one of the most important criteria for long term success in decarbonization is that they should not be reliant on virgin cropland, thanks to the risk of competition with global grain supplies, as well as concerns over the carbon cost of agricultural cultivation and deforestation. Instead, feedstocks for SAF should be made from waste products like corn stalks, used cooking oil, algae, and sewage. Potentially adding to this are forestry residues, sawmills and wood mill waste from managed forests.
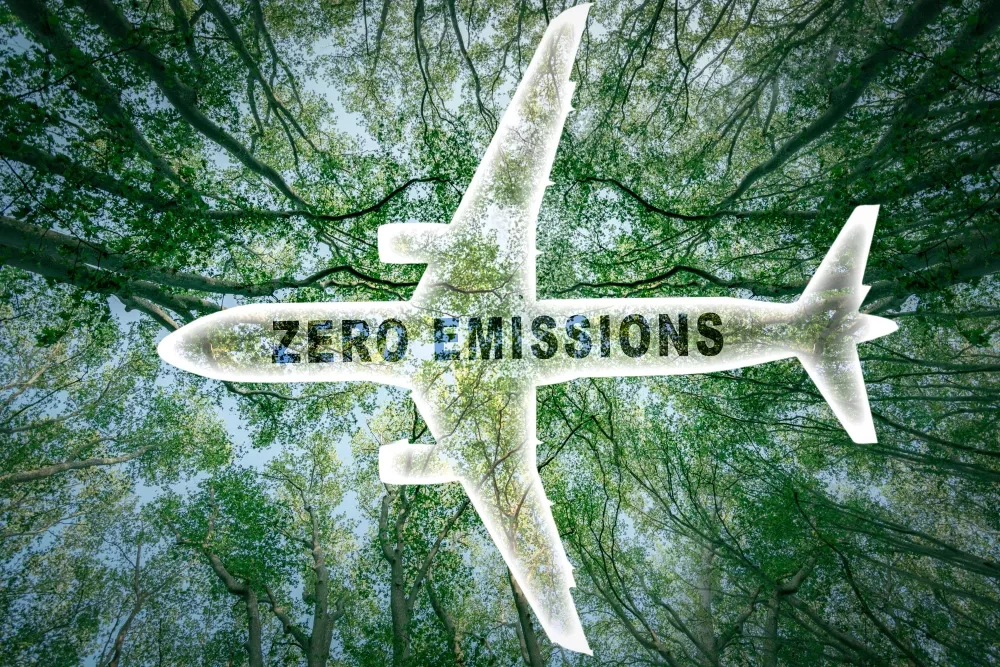
Hardest sector targets
ReFuelEU legislation states that existing supplies of biomass feedstock should be targeted at the aviation industry, one of the hardest-to-decarbonize sectors, for maximum climate effectiveness. The EU even explicitly endorses discouraging biofuel uptake in road and sea transportation, in order to prioritize air.
According to the US Office of Energy Efficiency and Renewable Energy, some 3.8 billion liters of biomass could be collected domestically each year, providing 227 billion liters of low-carbon biofuels, which is enough to completely replace fossil fuels in US aircraft.
Another projection by Dutch SAF specialists, SkyNRG, in its SAF Market Outlook May 2023, estimates that there could be as many as 454 billion liters of SAF production up and running by 2050. “SAF is increasingly accepted as the most effective measure to significantly reduce aviation emissions,” note the report’s authors. “With key policies in place or underway, the industry now needs solid partnerships to deliver on the momentum we see today and realize the dramatic increase in production capacity needed to reach net-zero.”
But aviation is not the only contender in the biomass race, with stakeholders vying for raw materials for heat and energy generation and fiber-based packaging, for example. Maintaining high capacity demands and keeping any material losses to a minimum are therefore vital.
Bruks Siwertell’s capability in this sector is well-known, which is why the company has received a figurative ‘tap on the shoulder’ from the fledgling SAF industry, during its participation at the first ever North American SAF Conference & Expo 2023. Here, Ken Upchurch, Bruks Siwertell SVP Sales and Marketing, answered questions about handling and processing SAF feedstocks. “We are very excited to be part of the SAF movement as we continue to see increased interest in our solutions as it relates to handling and processing organic materials that will ultimately become the source for advanced SAF.”
Much of the biomass produced in the US consists of corn stalks and husks, or the small branches that are shaved off in the process of cutting timber; in Asia, palm kernel shells are also a key source. Sawdust and wood chips, once little more than the waste of wood production, are now valuable resources.
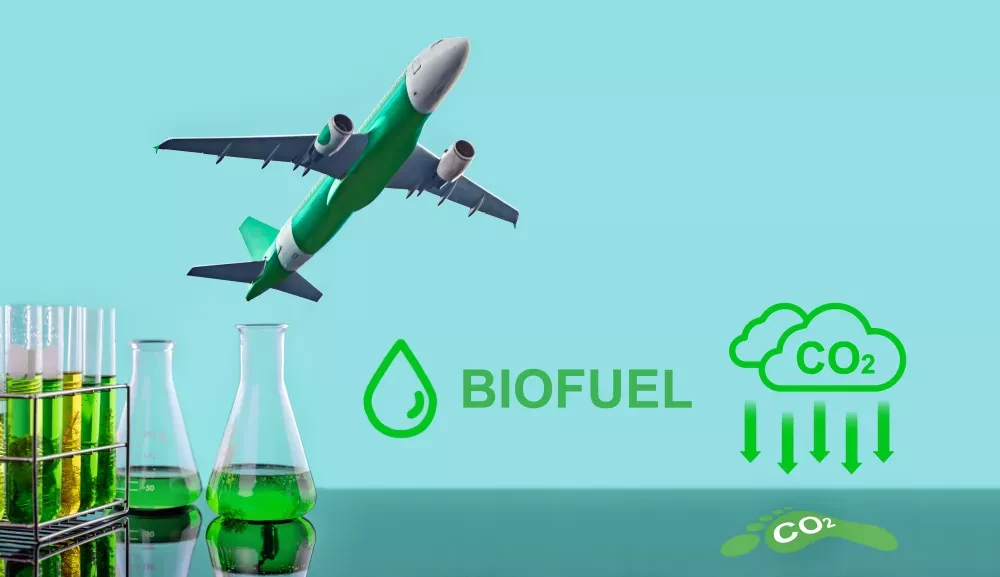
We know about wood
“Wood is the material that Bruks Siwertell handles the most of,” explained Upchurch. “Every part of a tree has value potential, and waste wood residues such as wood chips, bark, hard-to-handle forestry by-products and end-of-life timber, are no exception. These capabilities extend to agricultural waste as well.
“The biomass, bioenergy and biofuel sectors can directly benefit from Bruks Siwertell technology, and our capabilities have been extended even further in this sector with the recent acquisition of the North American engineering and manufacturing company, West Salem Machinery (WSM),” he continued. “WSM’s waste-processing capabilities, which includes high-capacity shredders, hammermills and green and food recycling systems, strengthens our portfolio of specialized waste wood residue and wood-processing equipment. This puts Bruks Siwertell Group in a great position to ensure that SAF stakeholders can get the highest yields from this sustainable energy source.”
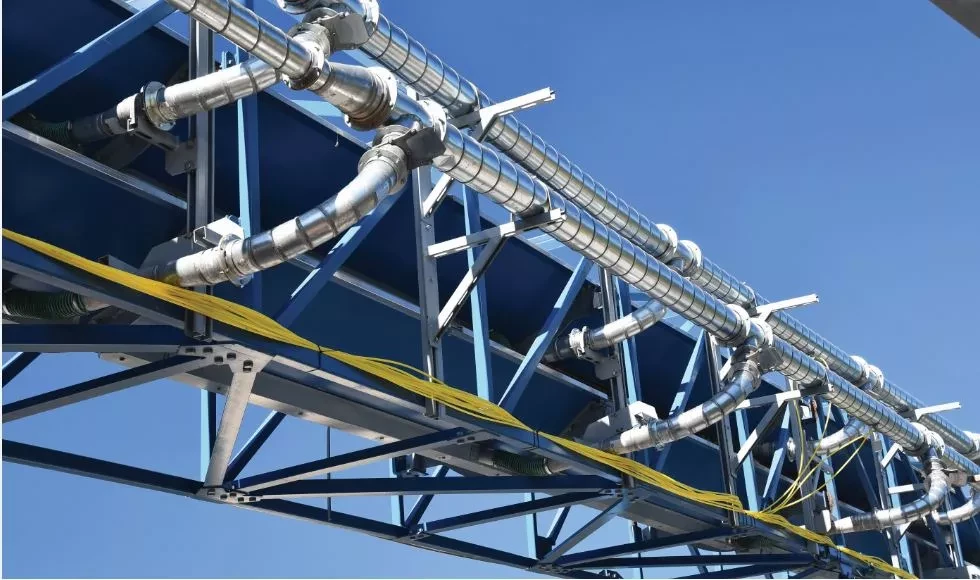
Charting the course
Bruks Siwertell’s wood-processing range also includes some of the market’s most powerful wood chipping machines, providing a basic feedstock for SAF. Transforming wood chips into SAF involves combining them alongside other solid elements like bark, corn husks, and pine kernels with oily substances like waste cooking oil and sewage sludge. Together, these fibrous materials are broken down in a bioreactor, using microbes to digest them into liquid; a process which also generates usable heat on-site.
Once these processes are performed, the resulting crude biofuel can then be refined, cracked or blended into different grades, in much the same way as fossil fuels are today. SkyNRG estimates that some 150 such facilities are needed in Europe, and 250 in the US, to generate enough SAF to meet with aviation fuel demand in these countries. But not only this; an extraordinary formalization of what is currently an informal and decentralized market – that of waste collection and recycling – will be necessary, to allow humanity to make better use of its waste.
Bruks Siwertell has helped various operators to make better use of their resources. Throughout North America and the world, Bruks Siwertell’s machinery is already directly involved in the handling and processing of wood and agricultural waste for the biofuel, bioenergy and biomass pellet sectors; and within ports, ship loaders, unloaders and conveying systems securing the environment-friendly transfer of this material for onward use.
“The SAF industry, fortunately, does not have to start from scratch,” said Upchurch. “Bruks Siwertell has been assisting the power-generation sector in ramping up its use of biomass for co-firing, and for complete transitions to biomass only fuel. So, whether this is destined for aircraft engines or power plants, the principles of processing and handling biomass remain the same; minimizing waste, dust emissions, and material degradation, and maximizing yields.”
PLEASE CONTACT US FOR MORE INFORMATION
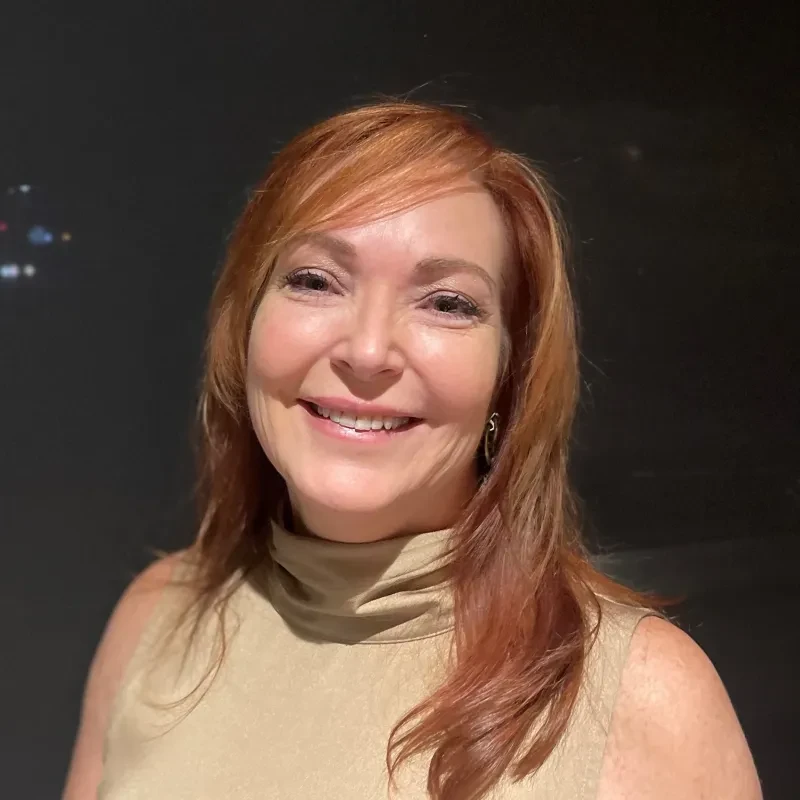