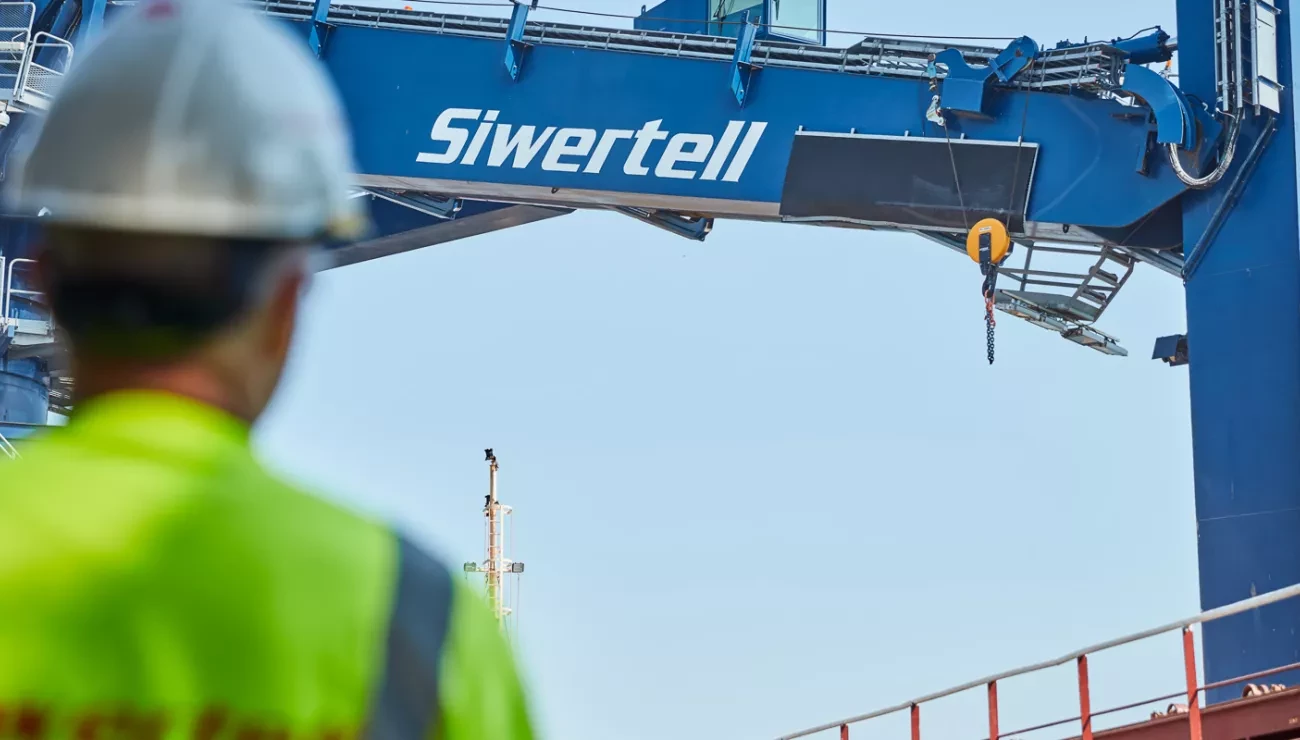
Save money, plan maintenance stops
17 Feb 2020Unplanned maintenance stops, emergency repairs, reputational damage and the long-term impact on efficiency are valuable reasons why wise operators plan equipment downtime.
Despite knowing that emergency repairs are almost always more expensive than the planned replacement of spare parts, it is still a risk some operators are prepared to take.
“There are so many advantages to planning maintenance stops,” says Kari Leppänen, Field Service Manager, Bruks Siwertell. “If cost control is a primary reason for holding off on maintenance, this strategy rarely pays off, and almost always costs a business more. Not just from emergency expenses either, but from less obvious sources such as reputation loss and the diminishing efficiency of equipment.
“Whether an owner has a single piece of machinery as the backbone of its operation, or multiple systems serving a complex operation, effective maintenance regimes will deliver the best return on investment,” notes Mr Leppänen. “Owners financially benefit from the optimal performance of equipment, its ongoing reliability and its availability to serve the operation, reducing the lifetime cost of ownership.”
Minimizing maintenance costs
Mr Leppänen explains that there are other reasons why is it more cost-effective to plan maintenance stops. “The timely replacement of wear parts prevents consequential damage to equipment. This can often be far more cost-impactful than replacing the wear part itself. Having a robust service strategy makes it easier to plan for the availability and purchase of the spare parts that are needed, which makes budgeting easier.”
Other elements to consider are demurrage costs. “These are almost entirely avoidable if incurred by unplanned equipment downtime,” he continues.
“Scheduled maintenance means that work can be carried out during the day with regular personnel, rather than emergency teams, potentially at night. The need for larger resources, including the required number of personnel, is much better managed.”
“Good service management is essential for the smooth running of all operations. It enables owners to keep track of what needs to be done and when,” he adds. “If mobile cranes and other large equipment are needed for major maintenance work, their availability can be negotiated at a good price. The replacement of parts can be planned for so that the work can be carried out with minimal disturbance. Cost savings are delivered, not from delaying or putting-off maintenance all together, but by carrying it out in the right way.”
Smooth project management
Time-savings can also be gained when an operator plans maintenance stops. “These are delivered by having the right work crews and experts on hand and all the parts and equipment in place, ready. Everyone can be briefed on the work; everyone knows what their tasks are. It streamlines projects, not only minimizing the time that it takes to carry them out, but also minimizing the time that equipment is offline, unable to contribute to the business.
“Furthermore, personnel are an expensive resource, their planned deployment on other tasks while equipment is offline is an effective business strategy. This time can also be used for training, which in itself delivers far-reaching benefits to an operator.”
Benefits of expert knowledge
There are also substantial advantages to choosing original equipment manufacturer (OEM) parts and labor. “To put it simply, we know the equipment best,” he says. “Our knowledge means that we can quickly assess its condition and determine which parts need attention. This ensures that nothing is replaced unnecessarily. Our experts can also make relatively small adjustments to operational parameters that deliver significant performance benefits.”
All equipment, if left unchecked, will gradually deteriorate in performance and ultimately fail. These failures impact safety and fundamentally increase the potential for accidents. “There really are no benefits to reactive, last-minute maintenance and economizing on service-related activities or buying non-original parts.
“However, we understand that managing maintenance is a significant task for any operator. We are able to work closely with customers to carry out service effectively and offer planned maintenance agreements that can take care of the burden, allowing an owner to focus on its operations,” concludes Mr Leppänen.