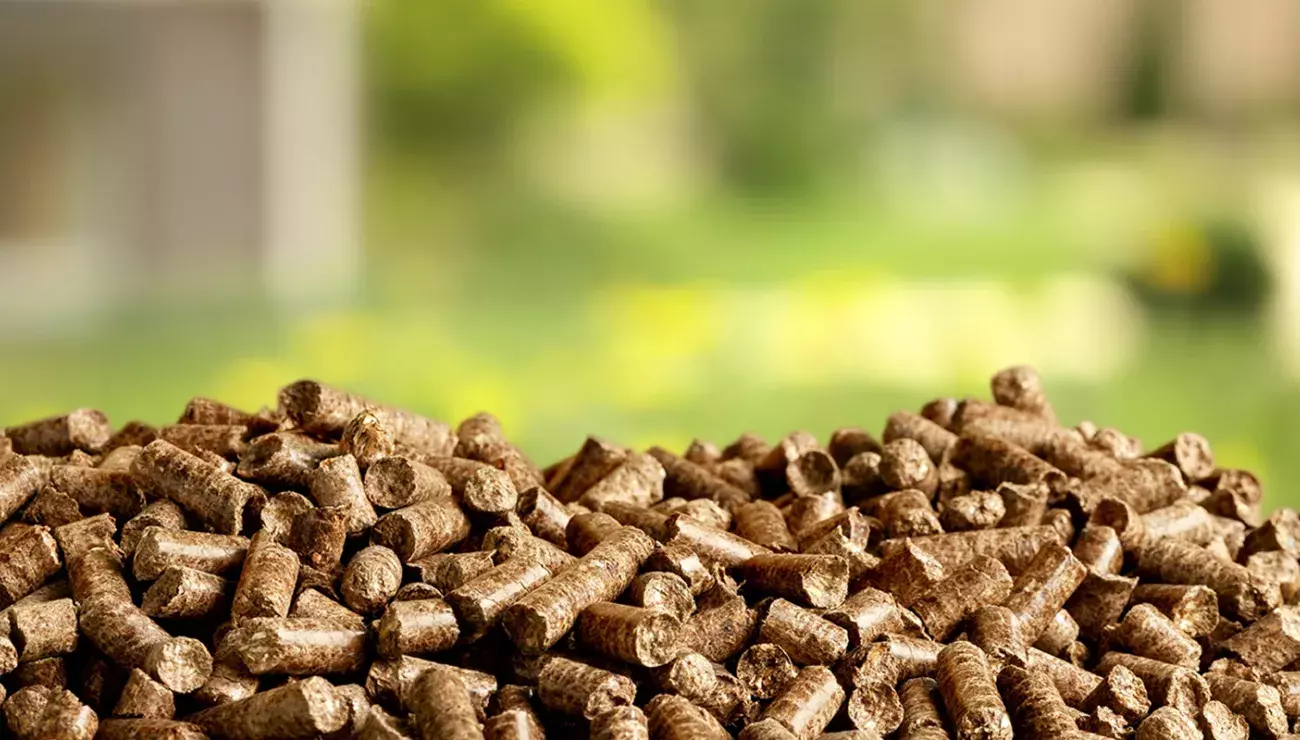
Pellet power: unlocking waste wood potential
17 Apr 2020Increasing global energy requirements, coupled with sustainable development goals to reduce greenhouse gas (GHG) emissions, are propelling the demand for renewable alternatives to fossil fuels. Biomass is showing considerable promise as a sustainable energy source and decarbonization tool.
Derived from animal or plant material, biomass can be purely grown in the form of an energy crop, or is often generated from waste, either from wood or forest residues, food crops or food processing.
It is this waste where the most value lies. While millions of metric tons used to head to landfill as an untapped resource, it is now being compressed into pellets, or used in a raw form by specialist boilers for heat and energy generation.
Biomass continues to boom
Of the huge quantities of second-generation biofuel sources, refined wood pellets – commonly produced as a waste product from sawmills or end of life timber – are a major contributor.
According to global data analysis company, Statista, global wood pellet production has steadily increased from about two million metric tons in 2000 to around 28.5 million metric tons in 2016 and in Western Europe alone, it is predicted to reach 13 million metric tons by 2020.
Statista notes that in 2018, biomass power plants in the USA had the largest capacity in the world at 16.7 gigawatts and in the same year it consumed approximately 5.13 quadrillion British thermal units of energy derived from biomass. In 2018, the global capacity of biomass power plants totaled 130 gigawatts.
Burning biomass is not without its complexities, and often material needs pre-treatment prior to combustion. Its use, however, is providing significant benefits, ameliorating investment costs and extending the lifetime of existing power stations, and their expensive infrastructure, originally constructed to burn coal.
The importance and the growth of the wood pellet industry in North America and Europe is well-recognized, and their mature markets are setting a benchmark for the rest of the world.
Ensuring the best end-product
Compressed pellets have their moisture squeezed out so that they burn consistently, which ensures the best results for power producers. However, these pellets are delicate and therefore unstable. While they are resistant to some impact, grinding or crushing movements can cause them to decompress and split, shedding dust and reducing their combustion efficiency.
The more numerous the modes of handling, the more likely it is that some of the cargo will have degraded, and be unusable at its destination boilers. It is therefore essential that the managers of each link in this chain take the utmost care to use material handling equipment that provides the lowest possible spoilage rates, to maximize the value of the end product for their customers.
Following the merger last year of Bruks and Siwertell, the combined capabilities of the Bruks Siwertell Group now comprises a portfolio of products that reflects all phases of this value chain, making it able to offer end-to-end solutions for customers.
“Siwertell unloaders have long-served the biomass industry, with high capacity unloading installations securing pellet fuel supplies to power-generation facilities globally, including biomass for Ørsted’s Avedøre power station in Denmark and the Drax power station in the UK,” says Ken Upchurch, Vice President Sales and Marketing, Bruks Siwertell Americas.
“Meanwhile, Bruks has been closely connected with the growing North American timber trade for more than 30 years. Today, there are Bruks installations all over the continent dedicated to unloading, processing and transporting wood products like bark, wood chips and sawdust.
“The Bruks and Siwertell brands, each with their own experiences from different sides – opposite ends, you might say – of the business, have come together and experts have shared their insights,” Mr Upchurch continues. “So, when it comes to the biomass trade, our knowledge and value proposition is unmatched in the rest of the market.”
Combining products at all stages
Effective pre-processing solutions such as managing moisture content, limiting contamination and ensuring a consistent particle size for energy production systems can help give value to biomass resources. Bruks wood chippers, milling machines and waste wood-processing hammer hogs were well-established in the global timber market before the merger, and remain at the forefront today.
The size and the volume of the required wood particles dictates which machines are suitable; Bruks Siwertell’s range can chip wood from the forest through to complex high-capacity wood-processing arrangements using multiple machine types.
A flexible and efficient way to transport the huge volumes of processed wood chips or other free-flowing materials such as bark, sawdust, shavings, peanut hulls for onward use is via bulk trucks. When they arrive at a facility full of biomass, a range of Bruks truck dumper systems could be there to meet them, including back-on or drive-over truck dumpers; these consist of a tipping platform, outfitted for different bulk truck trailer types, as well as a variety of receiving hoppers. The trucks are unloaded as the tipping platform pivots up to tip the contents of the truck into a receiving hopper.
“Most producers opt for an end pivot system to provide a gentle feed truck-tipping platform. This reduces the dramatic plume of dust generated when this type of material free flows out of a chip trailer,” he notes. “The tipping platform allows producers to use a variety of trailer types; it is important to have the ability to receive materials when available regardless of trailer type, and keep unloading cycle times to a minimum.”
Hoppers are typically designed to store at least two truckloads of material and can have articulating or static covers, specially designed to prevent any dust escaping into the surrounding environment. They might also have dust collectors, which can reclaim and collect material to form more biomass pellets. Key to the dust collection process is keeping the environment dry, as introduction of moisture at this stage could compromise pellet production later.
As with many Bruks Siwertell installations, they are most frequently on ‘brown-field’ sites so space and flexibility are at a premium. Compact, efficient and fully-enclosed systems are therefore prized by the biomass-handling industry, including conveyors.
Bruks Siwertell has the most comprehensive range of conveyors on the market. This includes the new, ‘The Belt ConveyorTM’, which is an air-supported system that eliminates idlers – the rollers underneath a traditional conveyor belt. The belt conveyor delivers highly efficient, low-friction material transfer with dramatically reduced maintenance and operating costs. Biomass production facilities almost always employ a screening system, which sorts the larger pieces from the usable material and removes debris that can damage downstream processing equipment.
“The screening process is a vital step,” Mr Upchurch explains. “We’ve seen many odd materials turn up in a pile of woodchips – boards, large slivers; even machine parts and hard hats!”
After screening, material could be elevated into a fully-enclosed storage silo. This can be accomplished with high angle drag chain conveyors or bucket elevators, both of which have been employed successfully. Storage silos can range in size, typically around 1,400m3 (50,000ft3) and are equipped with a reclaim mechanism similar to a circular screw. This allows the operator to monitor the material as it returns back into the system when needed.
The journey continues
If the pellets are destined for export, they can be carried by rail or road to a port’s receiving facility and from there loaded onto a bulk carrier, all accomplished with Bruks Siwertell equipment. Ship loaders are specified to suit the operation, including those for handling biomass. These systems feature an angled chute, which reduces the velocity of the cargo, to mitigate the impact and crushing forces that might otherwise cause it to break up as it reaches the hold.
When the vessel arrives at its destination, a Siwertell screw-type ship unloader is waiting. Using a counter-rotating inlet feeder, the biomass pellets are taken up into the machine, ensuring high-capacity, gentle material handling that delivers market-leading performance. Siwertell unloaders, installed at many terminals around the world, have been selected precisely for their ability to handle delicate cargoes such as grains, alumina, and biomass without causing degradation, and maintaining material quality for the end user.
Because biomass is organic and dry, it presents an inherent fire risk. Siwertell unloaders mitigate this with a fire safety system originally designed for handling sulfur – the Siwertell Sulfur Safety System (4S) – which shuts down and seals the machine in the event of a fire, stopping the blaze from spreading. In the event of an explosion, the system is designed to vent the blast away from personnel and property, minimizing damage.
Future opportunities
Bruks Siwertell is in a rare position to offer insight on the biomass trade and to deliver the best combination of handling products the market has to offer, now, and in the future.
“Our range of equipment ensures an end-to-end supply chain, producing the best possible results in the processing, manufacture, transportation and eventual burning of biomass cargoes,” says Mr Upchurch. “We provide both pellet producers and end users with the means to maintain lower material costs and maximize efficiency.
“With chipping technology in the forest, truck dumper systems at receiving facilities, new technology such as the belt conveyor, and existing and new ship loaders and unloaders, Bruks Siwertell is in a prime position to share in the opportunities presented by this growing market,” he adds.
For more information, please send an email to sales@bruks.com