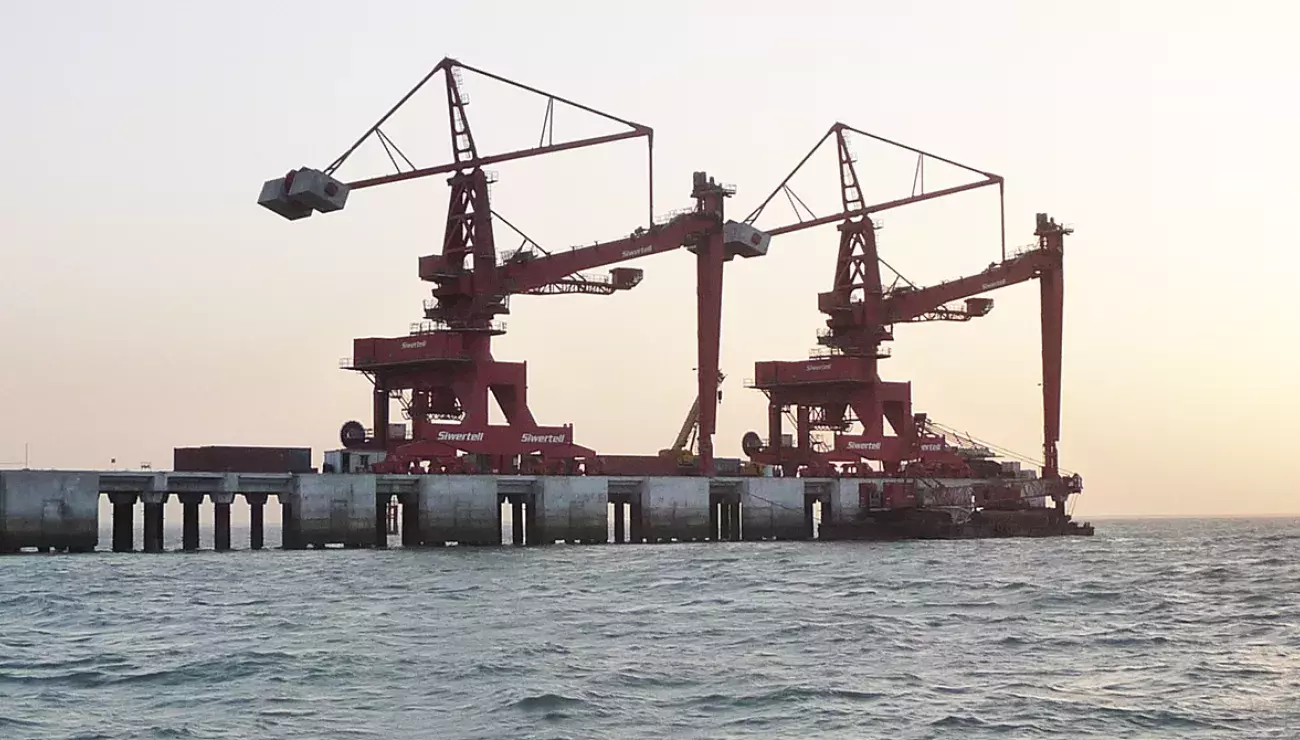
Not all ship unloaders are created equal
18 Jul 2018Choosing the right unloader for your bulk operations could make a substantial difference to your bottom-line, as well as protecting the environment; Ola Jeppsson, Siwertell Sales Manager, offers some practical advice about making a sound purchasing decision
All ship unloaders serve the same basic principle, to unload dry bulk from a ship as efficiently as possible, so how does an operator decide upon which system to use?
First of all, the type of cargo to be handled will disqualify some types of unloaders, for example, unloading dusty materials with grab cranes or bucket chain unloaders is not recommended, because of its environmental impact, and unloading coal and other non-free-flowing materials is not possible or too inefficient with pneumatic or chain-type unloaders.
Also, annual cargo intakes may exclude some types of unloaders, for example, if the annual intake is small, it may not justify a big investment.
So, after broadly selecting the possible types of unloaders, a comparison can then be made, taking into consideration factors such as investment costs, efficiency, environmental impact, power consumption and maintenance costs.
Historic choices may not be the best
As most industries are conservative when it comes to selecting equipment, historic choices often dictate many operator decisions. If they have previously used one type, operators tend to favour the same type again, or look into what competitors are using. However, this may not be a prudent approach.
A ship unloader is a big investment for any port or terminal, and therefore the comparison and selection process is usually very thorough; in general customers are willing to listen to our recommendations.
If a customer has no previous experience of Siwertell as a supplier or screw-type unloaders, understandably it may be a bit reluctant to switch to a totally new system. A great asset to us is our broad base of existing installations. We are often able to find similar operations and are able to let potential customers talk to existing owners and operators and their maintenance staff, so they can get a well-rounded opinion about our unloaders.
Under scrutiny: operating and environmental costs
In almost every case, Siwertell units offer low operating costs in comparison with all other systems including continuous-type unloaders, pneumatic systems or grab cranes. We quantify these operating cost comparisons by looking at personnel costs, power requirements, shipping costs, and loss of cargo.
The reasons for our low operating costs include the fact that a Siwertell unloader only requires one operator. Furthermore, in comparison with pneumatic systems, it can offer lower power-consumption demands and its efficiency means shorter times for the ship at the berth, delivering lower shipping costs. Also, as Siwertell units are totally-enclosed, there is no spillage or loss of cargo.
Environmentally, I believe that Siwertell offers the most comprehensive ship unloader on the market. We see an increasing worldwide intolerance for bulk handling systems that do not protect the environment and I think concern is accelerating. More and more grab cranes are simply not allowed to operate in some areas because of their potential environmental impact. Again, as our systems are totally-enclosed, we excel in this area.
Furthermore, anyone buying a ship unloader currently must consider not only today’s laws and regulations, but also those of tomorrow; what level of environmental impact will be allowed in the coming 20 to 25 years, throughout the whole lifespan of the unloader?
Weighing up the options
Weight and dimensions are often factors when an operator is choosing an unloader, but we should divide this into two areas for consideration; the first is when a new unloader is to be installed on an existing jetty and the other is for a new unloader being installed on a new jetty.
In the first case, the jetty has been designed to withstand a certain load, which is normally expressed as the maximum allowed wheel load. Any supplier must then design its unloader to be within the allowed loads and this is typically not a problem for us. To reinforce a jetty to cope with higher loads is normally very costly and often not an option.
Our second scenario, when a new jetty is being constructed, the allowed wheel loads of the unloader are still an important factor and I will explain why: by choosing a lightweight machine with low wheel loads, such as a Siwertell unloader, construction costs for the jetty can be considerably reduced.
When considering dimensions and the overall footprint of an unloader, Siwertell often requires just a narrow rail span, typically less than in comparison with grabs and bucket-chain unloaders, which means that the actual width of the jetty can be reduced, also cutting jetty construction costs.
Multi-cargo capabilities
There are many operators that handle only one commodity, like a coal-fired power plant. Dedicated grain and cement terminals also only handle one material. However, there are ports and terminals that handle a great variety of dry bulk cargoes and here the flexibility of a Siwertell is a great advantage, as it can seamlessly switch between commodities. At these general bulk facilities, the type of dry cargo may also shift from one year to another and therefore a multi-cargo unloader provides great flexibility for these operators.
Avoiding the demurrage curse
Another element we should touch upon is capacity and how important continuous high-capacity handling is to an operator. In general, operators want to minimise the time any vessel spends at the berth, due to operating costs and the cost of the vessel in particular. Very few operators would deviate from this. Therefore, the higher the capacity, in combination with efficiency, the faster the ship can be emptied. Most unloading operations are limited to a maximum number of days and if exceeded, operators will be penalised with demurrage costs.
Siwertell systems offer some of the highest capacities on the market and are also able to unload vessels with different shaped holds; we never demand that holds should have any particular profile. Contrary to most other types of unloaders, a Siwertell machine can reach under hatch coamings and into corners of the holds which minimises final clean-up times, adding to efficiency and yet again savings costs.
Through-life costs
Last, but not least, we should highlight reliability and through-life costs as these affect an operator right the way down the line.
Reliability is obviously very important, even though most operators have some kind of intermediate storage facilities to keep cargo flowing, for example a coal yard, grain silo or flat storage area for cement.
I believe that the vast majority of operators are aiming for the most efficient, reliable unloading operation as possible. Therefore, if operations are frequently interrupted by machinery downtime, the entire business will be affected – and not for the better.
When ordering a new unloader, operators frequently ask about maintenance costs, service regimes, and ongoing customer care and we again have a lot to offer in this area. Every customer is given thorough maintenance training during the commissioning of the unloader. We also offer a whole range of service packages. Furthermore, easy maintenance is always considered during our design processes.
Very little compares to a Siwertell screw-type unloader
Siwertell invented the screw-type unloader and introduced it to the market in 1974; holding a worldwide patent for 20 years. Only after this expired in the early 1990s did a few other companies start producing screw-type unloaders.
During the two decades that the patent existed, Siwertell delivered many unloaders for various dry bulk material installations and by using experience from these first references, its knowledge expanded. New technology was introduced and used to improve the function of the unloader, including control of the inlet device.
Over the years, Siwertell has also conducted considerable research and development into how different materials respond in a vertical screw, for example, cement and coal demonstrate completely different behaviours.
In terms of new patents, in general we do not take them out to protect the value of our research and development work, the main reason being is that we do not want to highlight how we have solved different problems. We do not have any patents currently.
Although other companies offer screw-type unloaders, these are mainly limited to handling cement, as it is a relatively simple material to convey from a technical perspective; unloading capacities also tend to be limited to around 800t/h.
Their basic concept is the same, but our lack of competition for the first 20 years means that we have considerably more experience, which is why, excluding China, Siwertell’s total market share of all delivered screw-type unloaders is close to 90 percent, and for some cargoes it can be even closer to 100 percent.
If a potential customer decides that it wants a screw-type unloader, we have many advantages over our competitors, boiling down to performance, quality and reliability all based on our experience and knowledge. We also offer extensive global support, which I think would be difficult to beat.
This leads me onto the subject of spares. There are companies offering non-original spares for Siwertell unloaders. We find that an operator usually only orders them once. They then find out that ‘you get what you pay for’, which can mean a comparatively poor quality, low-performance product.
A good example is replacement screws; these typically have a much lower lifespan than original Siwertell screws, and they are not necessarily cheaper if you consider their service life. Customers must also consider that using this type of non-original spare part affects the Siwertell warranty and in worst case scenarios, can cause damage to the unloader, particularly if a non-original screw is used with Siwertell original screws.
PLEASE CONTACT US FOR MORE INFORMATION
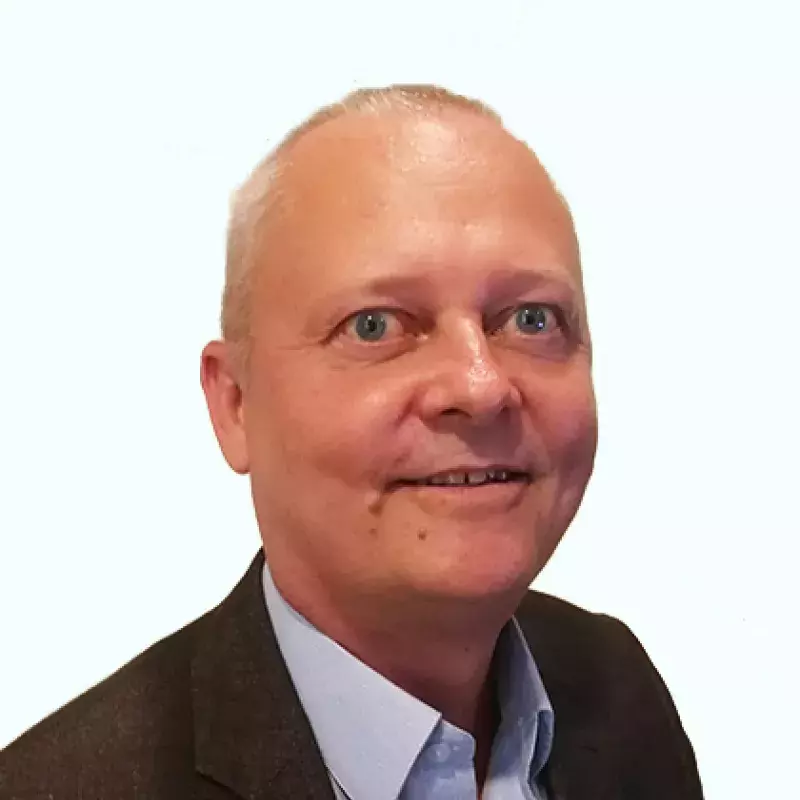
Categories: Bulk unloading
Share:
More Blogs
Previous:
Keeping the noise downNext:
Sulfur Safety System