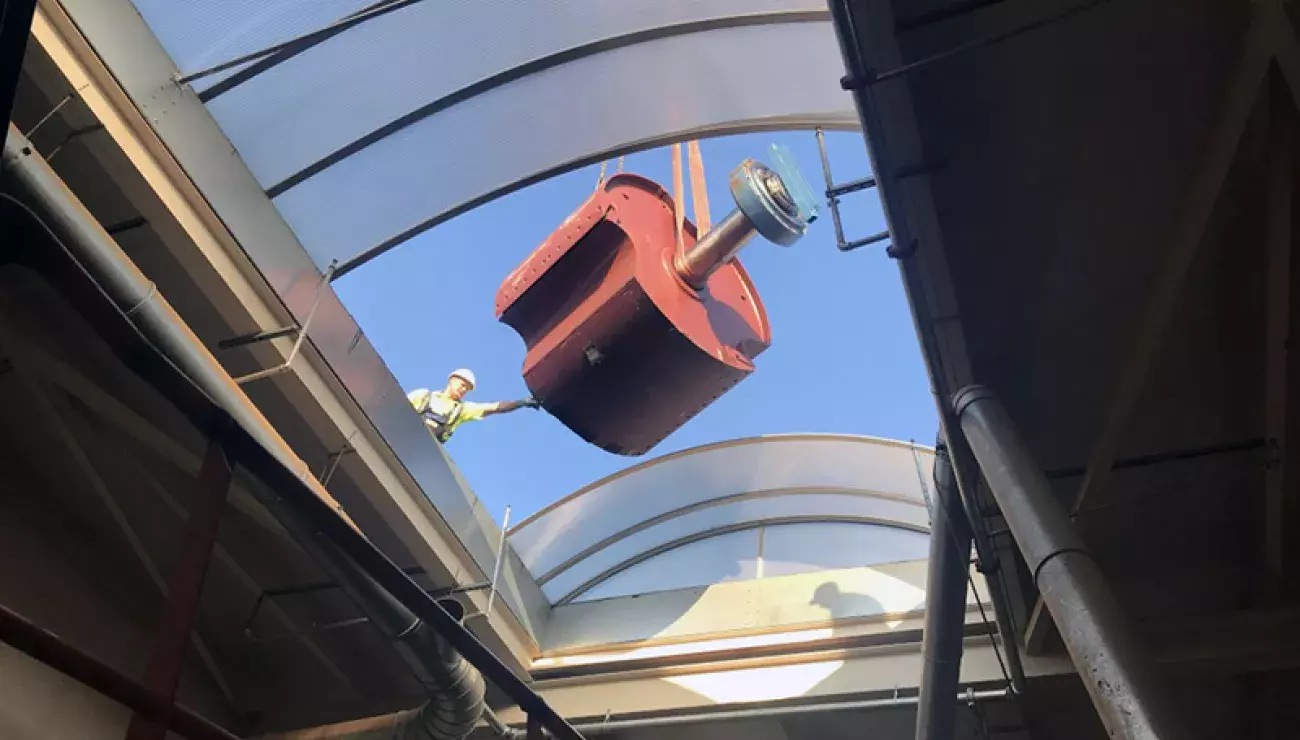
No unwanted surprises: preventative maintenance pays
14 Jul 2021The phrase, ‘an ounce of prevention is worth a pound of cure,’ is more relevant today than at any other time in living memory, but it applies to machinery as well. Preventative maintenance is less costly both from a material and downtime perspective; it is every bit as effective as replacing equipment every few years, but vastly preferable in terms of budgeting, operational availability, and the implications for the environment. Simply put, there should be no economizing on maintenance, because maintenance is itself a form of economy.
Bruks Siwertell has equipment that has been successfully running for more than 30 years, thanks to a conscientious approach to service. Every machine has parts that wear faster than others; but a framework of preventative maintenance ensures that there are no surprises for equipment owners.
The introduction of predictability and planned service means that, in many cases, wear parts can go for longer intervals without being replaced. But, when the time comes to replace them, the downtime is a fraction of what would have been incurred if the machine develops a fault, or malfunctions whilst in operation. With experienced personnel keeping close track, servicing remains a steady, foreseeable background cost, rather than a sudden spike.
Unforeseen benefits
“With a conscientious approach to maintenance, it is quite feasible that the life of parts will be extended, requiring fewer replacements overall,” explains Christoph Bender, Head of Service, Bruks Klöckner, part of Bruks Siwertell Group, in Hirtscheid, Germany. “In many cases, parts have incurred less wear than might otherwise be expected. If we feel that a piece of equipment can go for a longer period without a complete overhaul, it is our responsibility to alert the customer to that fact.
“A recent example of this was with one of our long-term sawmill customers in France,” Bender continues. “After Bruks Siwertell signed a maintenance contract, we dispatched a technical surveyor to the mill, to inspect the Bruks Klöckner machines and systems installed there before the facility’s annual seasonal shutdown period.
“Over the course of a two-day visit, the equipment was reviewed and the surveyor then developed a comprehensive maintenance plan, taking inventory of the necessary wear, replacement and spare parts, and a schedule for maintenance at the plant. With advance warning, the necessary original equipment spare parts, even those with typically longer delivery times, were made available in time for the shutdown, allowing all repairs and maintenance to take place during this period, and incurring no additional off-hire time whatsoever.
“All required maintenance was carried out during a period when the mill would not otherwise be trading, meaning that all machines were up and running when it was time to resume, and the customer lost no time to maintenance at all,” he notes. “This is what can be achieved with preventative and planned maintenance.”
Minimal downtime
In fact, consulting with the customer, it was discovered that by implementing this strategy, the mill owner could reduce any faults and failures, and the associated downtime, by around 60 percent.
Bruks Siwertell offers customized maintenance agreements and full transparency in terms of the staff, equipment, and spare parts.
“We offer tailor-made service packages that take into account machine-specific conditions and individual operational scenarios, including the materials handled or processed and machine running times,” says Bender.
“At Bruks Siwertell, we not only see ourselves as a competent and reliable partner to the dry bulk handling and processed wood industries in terms of the development, production, installation and commissioning of individual machines or complex systems, but we stand by these deliveries for their lifetimes to guarantee continuous productivity and minimal downtime.
“When an organization invests in our products, it not only obtains the nuts-and-bolts, but also taps into generations’ worth of specialist, expert knowledge. But by taking the next step and entering into a maintenance agreement, we are able to offer the very best advantages of this knowledge throughout the life of the equipment, keeping it running for as long as possible, with spare parts and personnel on-hand as soon as they are needed, resulting in maximum operational time and controlled, predictable costs,” Bender concludes.
Bruks Siwertell offers tailor-made service packages that take into account machine-specific conditions and individual operational scenarios
We have equipment installations that have been successfully running for more than 30 years, thanks to a conscientious approach to service
Christoph Bender, Head of Service, Bruks Klöckner: “With a conscientious approach to maintenance, it is quite feasible that the life of parts will be extended, requiring fewer replacements overall”
PLEASE CONTACT US FOR MORE INFORMATION
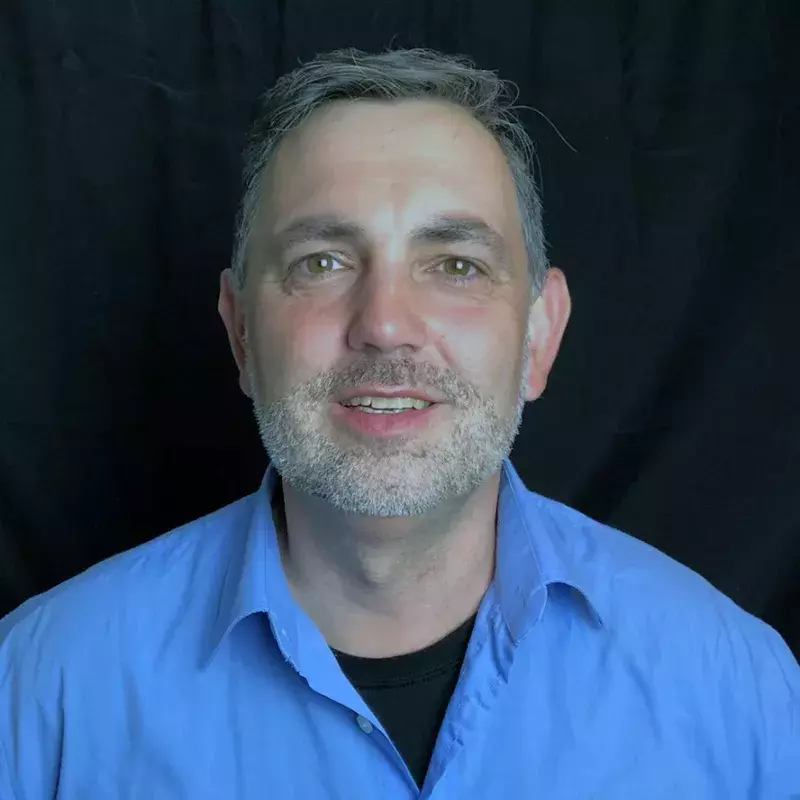
Head of installation and commissioning, Bruks Klöckner, Gmbh
Christoph Bender
+49 2661 28157