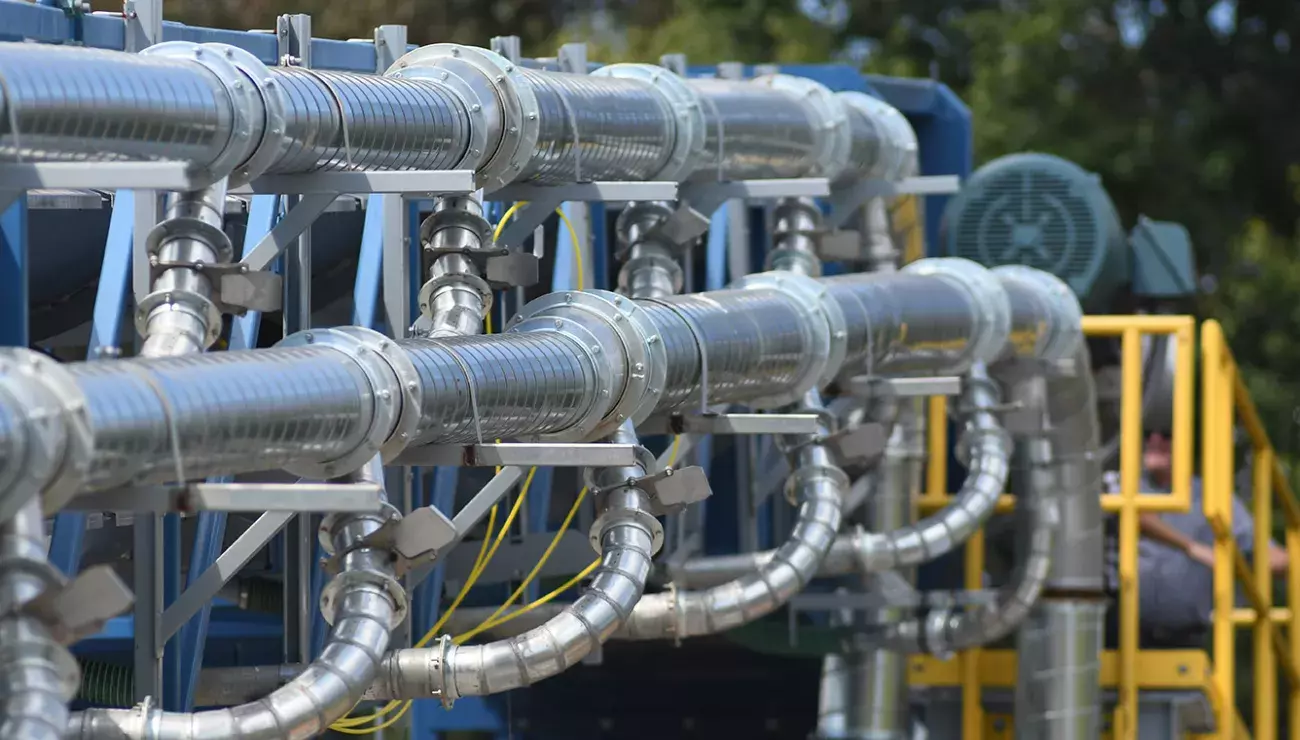
Low-friction conveying offers considerable commercial rewards
20 Aug 2019It has been three years in development, but Bruks Siwertell can now offer a conveying system that stands significantly apart from any others on the market. Known as ‘The Belt Conveyor™’, it innovatively combines the use of air-cushion technology with Bruks’ standard belt conveyors, ensuring low friction, high capacity conveying that offers minimal equipment wear and very low operating costs.
“This development is long overdue,” says Steve Bennett, CEO and President of Bruks Siwertell Americas. “Belt conveyors are some of the most widely used systems in the world and are found in just about any manufacturing and processing facility. Fundamentally, little has changed with the technology for years, but that does not mean to say substantial improvements cannot be gained from rethinking the basics of the belt conveyor. This was the driver for our new air-supported conveyor system.”
Key areas ready for improvement
“There were four key areas that we identified as opportunities for improvement: safety, maintenance requirements, running costs and environmental impact. Any new development had to tackle these,” continues Mr Bennett.
“These areas are interlinked, because a design resolution for one aspect can have a far-reaching impact. For example, a fundamental element of the new conveyor is that it does not use idlers to support the belt over the conveying distance; therefore significant gains can be made. In terms of safety, many companies have faced idler cans seizing up and creating friction fires, with them removed, the risk of fire is almost eliminated.
“Their absence creates other advantages,” he explains. “Maintaining hundreds of idlers to ensure that they do not seize is a fairly continuous task, by removing them from the system, including belt sag, pull cord switches, and lights, maintenance costs are radically reduced.
“Maintenance savings, in addition to minimal energy-consumption requirements, translate into extremely low running costs,” Mr Bennett notes.
Extremely smooth ride surface
The elimination of idlers, in favor of an air-cushioned belt, offers other advantages as well, namely an extremely smooth ride surface, ensuring material is discharged in exactly the same condition as when it was loaded onto the belt. It virtually eliminates the production of fines, which are common with other conveying methods, and negatively impact downstream processes.
New technology in a familiar form
Unlike other air-cushion conveyor systems, rather than using a pipe as the key containment method, the belt conveyor uses a simple modular cradle that supports a formed carrying trough and covers, and a central air manifold provides the air pressure to suspend the belt. Basic components include the head and tail unit and three meter-long intermediate sections. The only moving parts are the head and tail pulleys.
The shape of the pan also mimics the geometry of a 35-degree idler conveyor, but without the rollers, therefore it still meets the industry-standard calculations for the USA’s Conveyor Equipment Manufacturers Association (CEMA).
Innovative pressurized air delivery
Unlike other air-assisted conveyor technology, including Bruks’ Tubulator systems, which predominantly use a series of in-line fans to generate the cushion of air, Bruks’ the belt conveyor uses a patented pressurized air enclosure system.
Each three meter section has access to a common header of pressurized air, and under the carry-side pan is a pressurized air enclosure system, otherwise known as a plenum. Each independent plenum delivers air through a series of holes at an exact pressure and airflow to lift the belt and ensure almost frictionless travel. Air pressure sensors and flow meters are installed to monitor and maintain optimum pressure.
The plenums of air can be individually set for each installation, so they can exactly match the delivery of air for each application. This patented air delivery method allows the Bruks air-supported belt conveyor to carry a wide variety of materials with diverse physical properties.
Far-reaching rewards
The environmental gains that the air-supported belt conveyor offers are also far-reaching. Low-friction conveying means that its energy consumption demands are minimal in comparison with traditional systems, but more directly, a fully enclosed cover and integrated air-supported return, provides dust-free operations, eliminates product losses and minimizes any noise production. It also means that dry bulk material is protected from the weather.
The air-supported conveyor is tailored for each application, including specific air flow and pressure, so that a wide range of materials can be carried. It can also be easily incorporated into a wide variety of structural support systems, including elevated positions, making installation simple and quick. “Installation and commissioning times are significantly reduced in comparison with idler conveyor systems,” Mr Bennett says. “This is largely due to the fact that there is virtually zero belt training required.
“Conveyors are essential elements for many processing facilities and power-generation plants and their reliable, continuous smooth running is the most important focus of any new development. In part, this goes hand-in-hand with a commitment to high-quality manufacturing. For this reason Bruks Siwertell has built a unique test facility to not only showcase its capabilities, but also demonstrate its performance in comparison to other available systems,” he highlights.
FORE MORE INFORMATION, PLEASE CONTACT sales@bruks.com
Categories: Bulk unloading