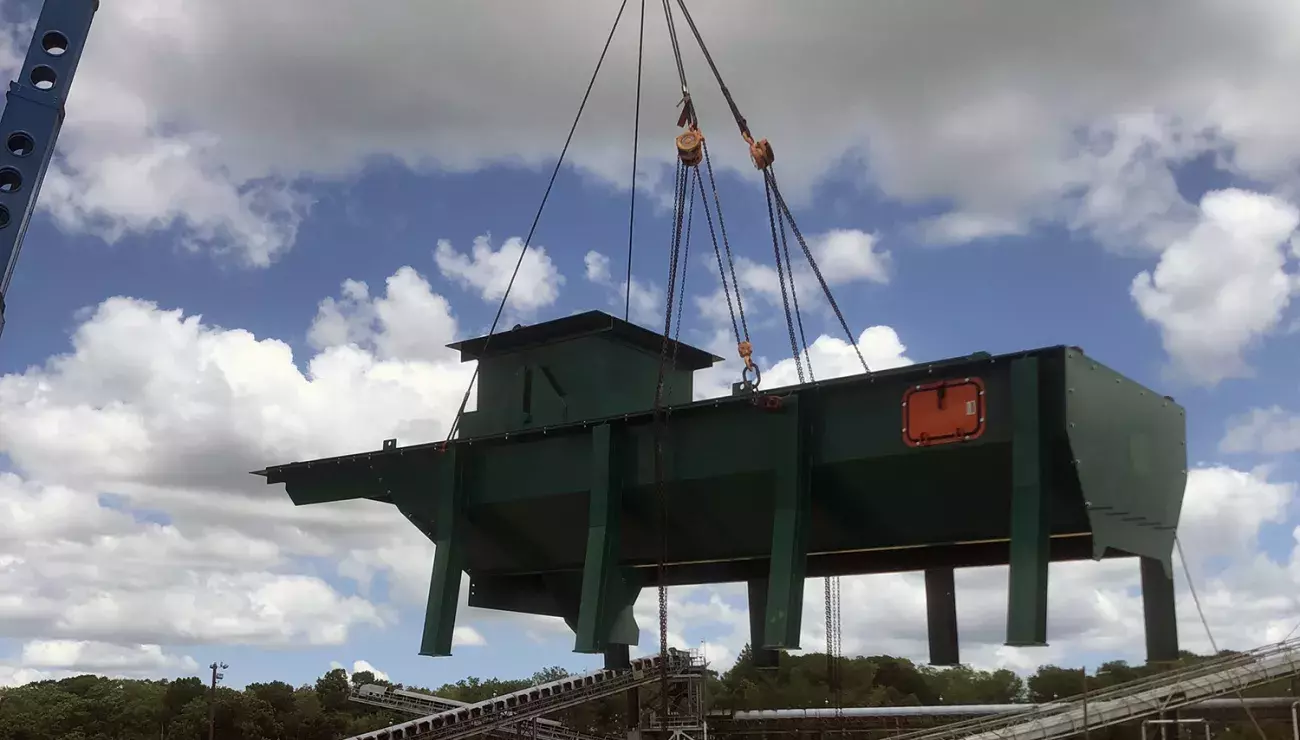
Hopper upgrades can offer more than dust control
24 Jan 2020A recent infeed hopper upgrade for North American pulp and paper mill, Domtar Plymouth, has significantly reduced dust emissions, improved material handling efficiency and strengthened Domtar’s sustainability drive
As well as improving a specific area of focus, machinery upgrades can have far-reaching positive implications for an entire material handling operation. Existing systems can operate more efficiently, gain from an extended service life and provide greater environmental protection.
A recent beneficiary of such an upgrade is Domtar Plymouth Mill, large-scale producer of softwood fluff pulp and one of 13 North American pulp and paper mills owned by leading fiber-based products manufacturer, Domtar.
Since 2010, Domtar has cut its greenhouse gas emissions by 15 percent. The US corporation continues to prioritize sustainability goals, and in line with this, Domtar Plymouth Mill, based in North Carolina, is building a sustainable future by conserving resources.
Through a combination of capital investments and continuous improvement projects, Domtar indicates that its Plymouth Mill is building a sustainable future by increasing energy and resource efficiency. The mill has finalized initiatives to reduce fuel and water consumption, and is looking to reduce environmental impact and improve efficiencies in other processes as well.
Upgrades ensure greater sustainability
Earlier in the year, Bruks Siwertell’s Americas division was contacted by Domtar Plymouth Mill for expert input about ways to reduce dust emissions from its large-scale wood-fiber stacking and reclaiming system, originally delivered by Rockwood International in 2005; Rockwood was acquired by Bruks in 1998 and has since been absorbed into the wider Bruks Siwertell organization.
The main issue faced by the company was the excessive production of dust, particularly during luffing movements of the stacker boom. “Dust was building up over the hopper cover, which meant that the operator had to dedicate personnel to continuously clear it,” explains Jason Scott, Service Manager, Bruks Siwertell.
“Domtar approached us for a solution as we have a good working relationship and ongoing conversations with the company,” he says. “We have also successfully carried out upgrades on similar machines.”
Benefits of improved designs
“Infeed hoppers are always supplied with the stacker boom,” continues Mr Scott. “However, over the years, we have developed substantial design improvements and our latest generation of infeed hoppers incorporate several enhancements. These are particularly effective for dust control and offer other advantages too.
“Deflector plates, located inside the hopper, control the flow of material onto the conveyor, directing wood chips to the center of the stacker belt. This gives a greater level of material management to optimize the efficiency of the system, allows for a smooth motion of the luffing boom and that important reduction in dust emissions,” he adds.
A very satisfied customer
“The new infeed hopper was installed onto the stacker boom and has eliminated the vagrant dust issues entirely, which is not only good for the company, but also the environment,” highlights Mr Scott. “Importantly, it also does not interfere with the boom’s luffing motions or impede the flow of wood chips through the system.”
The upgrade project took six weeks from receiving the order to completion in mid-May this year. “The timescales were tight and required 10-hour working days to meet the operational needs of the plant, but it was worth it,” he notes.
“Domtar is extremely happy with the results. Fewer personnel are needed to clean the stacker boom and dust emissions have been reduced. The company is so satisfied that it plans to carry out the same upgrade on an identical stacker reclaimer that it has onsite in mid-2020. This speaks volumes.”
More systems could benefit
Bruks Siwertell offers one of the most comprehensive stacker reclaimer portfolios on the market. “Our knowledge of these systems and the material that they handle means that we can often find solutions to overcome issues that operators are experiencing,” he says. “Our aim is to ensure that they operate in the most efficient and environmentally responsible way.
“There are numerous stacker reclaimer systems that are still fitted with their original hoppers, and these could therefore benefit significantly from an infeed hopper upgrade, incorporating our latest design improvements.”
For more information, please send an email to sales@bruks.com