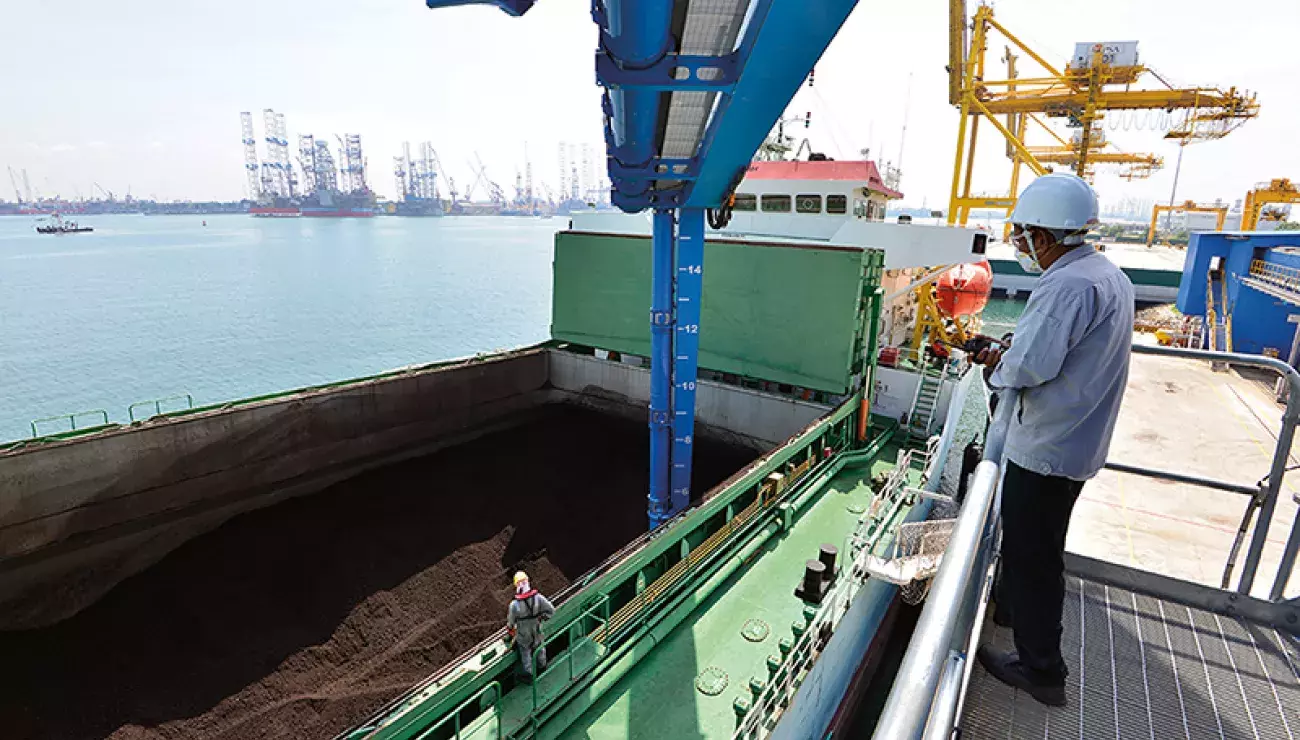
As good as new: how is your bulk handling operation performing?
10 Jan 2019A Siwertell unloading efficiency analysis ensures that your bulk handling solution performs to the best of its capabilities, maximizing profits through relatively minor adjustments; Tony Aronsson, Area Manager Services Asia-Pacific (APAC) explains how
When Siwertell commissions an unloader, it ensures that peak performance is achieved. However, after some time in operation, the actual capacity can differ from the unloader’s design capacity. For this reason, Siwertell recommends that a year after the unloader enters commercial operation, it is wise to carry out an efficiency study, not only to further optimize the unloader, but also to benefit from an additional training opportunity, both from an operational and maintenance perspective.
Regular maintenance regimes are extremely important to secure the long-term operative availability of an unloader. However, performance indicators are not usually checked during annual services and inspections, essentially because both the mechanical, as well as electrical systems are checked, during which time the unloader needs to be out of operation.
Unloading studies provide a different service to these ongoing maintenance regimes. Typically, an unloading study embraces the complete unloading operation, because this is the only way to get an overall picture of the setup and its present efficiency, and to evaluate the unloading process specifically.
Nothing remains the same
Conditions change over time, everything from new personnel operating the unloader to the characteristics of the material being unloaded. Take coal, for example, coal qualities can differ widely from supplier to supplier, and furthermore coal quality has generally dipped over the last six to seven years; it has become moister and stickier, and the ash content, as well as other contaminants that were previously removed by the coal supplier, tend not to be.
Keeping the unloader tuned perfectly for an operator’s current conditions is a good investment. Therefore, an efficiency study every third year could prove to be very profitable for operators, and not just coal handlers, every bulk commodity handler would benefit.
Peak performance, greater profits
In terms of quantifying these benefits we typically see unloading efficiency improvements in the region of 10 percent, but have seen as much as a 30 percent deviation from an unloader’s original peak handling efficiency.
During an on-site efficiency analysis, we not only focus on the ship unloader, but also highlight bottlenecks and shortcomings with downstream conveyors and equipment, even if that equipment is not supplied by Siwertell. We have also been asked for help evaluating operations that do not use any Siwertell equipment. Of course, there are limitations to this as it is difficult to advise ways to improve equipment or undertake on-site adjustments, but our capabilities extend way beyond this and can identify major to minor issues and faults throughout the entire operation.
Our ability to pinpoint issues, and provide recommendations on how to improve them, can offer substantial additional savings to an operator.
An example of a recommendation we can provide following an unloading analysis on an older Siwertell unloader, is to implement settings for several bulk material choices. It is the same concept that Siwertell uses on its multi-purpose unloaders, but it can also be used on a Siwertell unloader where cargo varies in quality. This enables an operator to choose up to five different settings for the varying qualities of a commodity, such as coal. This fantastic function is now standard on our new Siwertell unloaders, but it does need to be optimized for each quality and cargo.
Siwertell collects a great deal of data during the study, including capacity measurements from the belt scale, power consumption of the vertical conveyor, power consumption of the horizontal conveyor, angle of horizontal arm, speed of the inlet feeder, set values from the potentiometer to the controller, shifting time between cargo holds, other key values, and capacity.
An area that often requires greater analysis and sometimes separate consideration is the clean-up stage – the final phase of the unloading process. This part of the operation demands combined skills and cooperation between the Siwertell unloader operator and the operator of auxiliary equipment such as excavators and payloaders. Our customers, especially new ones, often ask for help and advice regarding this phase of an operation.
Many operations are already benefitting
As customer profit margins come under ever greater scrutiny, Siwertell is on hand to ensure that every aspect of a bulk handling operation runs as smoothly and efficiently as possible. The first evaluation of this type in Asia was performed more than 15 years ago in the Philippines with very good results. On a global basis, numerous operations have benefitted from this service and in Asia alone in the past five years, Siwertell has performed at least 10 unloading efficiency evaluations mostly in Taiwan, Korea and the Philippines.
PLEASE CONTACT US FOR MORE INFORMATION
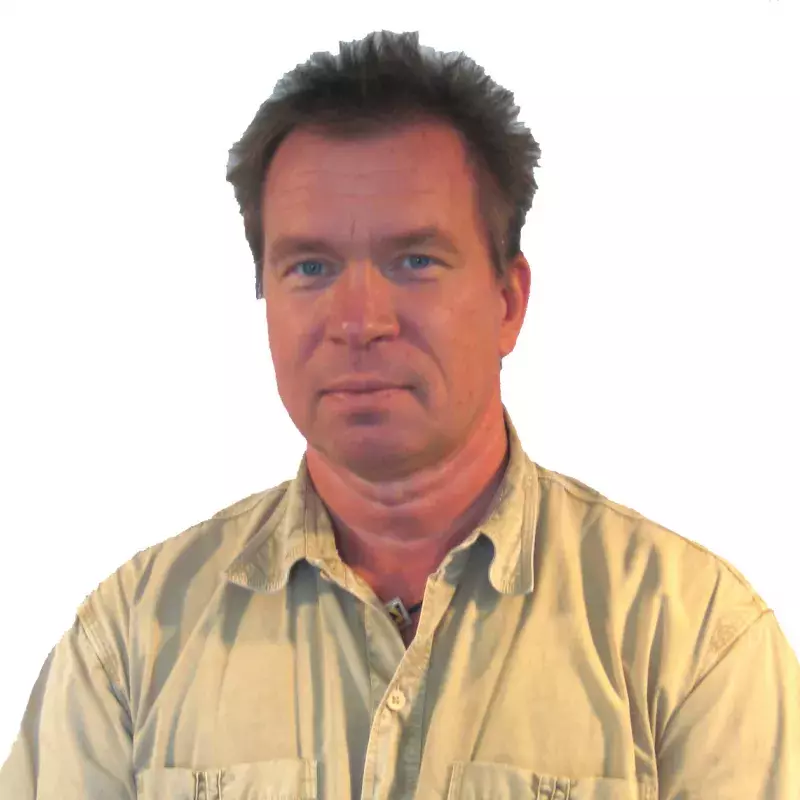
Categories: Bulk unloading
Share:
More Blogs
Previous:
Working hard in the tropics