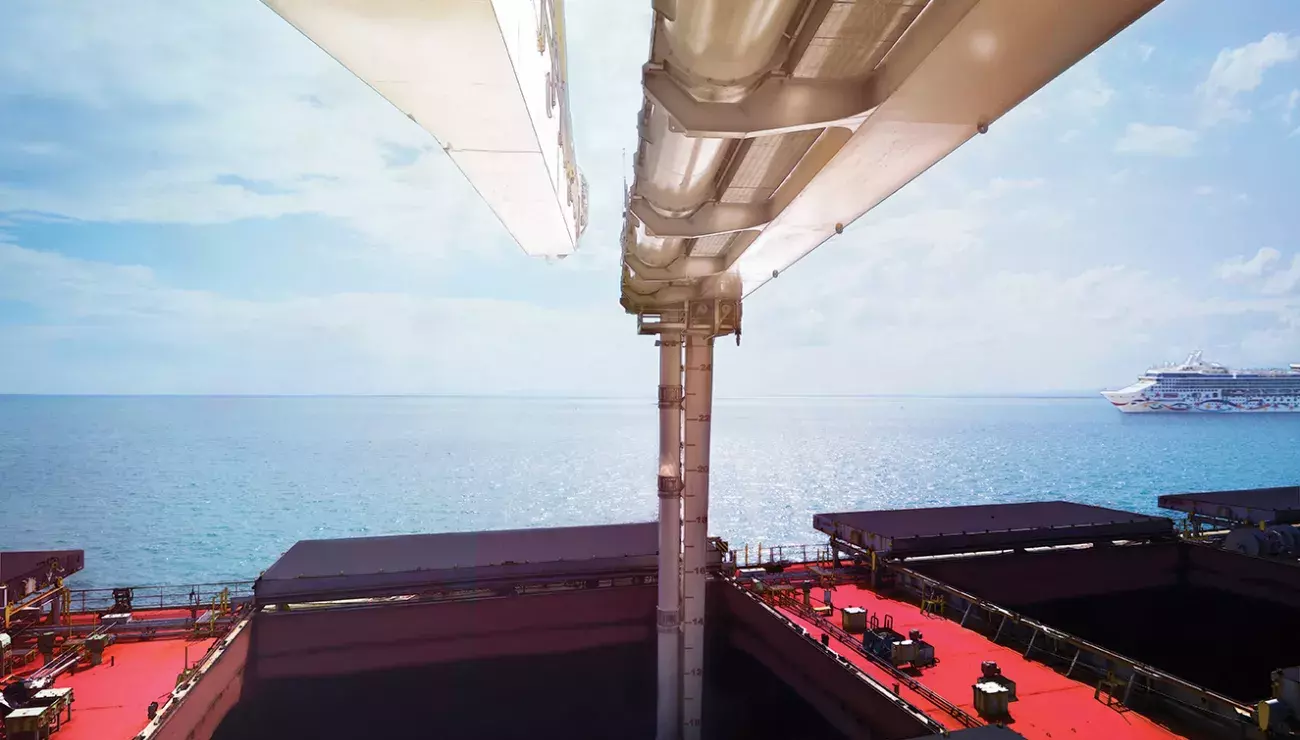
First-hand feedback from Vietnamese steel plant
18 Jun 2019First-hand feedback from Vietnamese steel plant
Long River’s first experience of operating a Siwertell ship unloader is going well. The Vietnam-based company, Long River Engineering Co Ltd, part of An Chi Invest, is operating and maintaining a notable pair of Siwertell ship unloaders for Formosa Ha Tinh Steel Corporation (FHS), owned by Formosa Petrochemical Corporation (FPC), and has done so since they were commissioned in 2016.
They are unique for two reasons, firstly because they represent a breakthrough change for the steel industry and secondly, they are the largest Siwertell ship unloaders delivered by Bruks Siwertell to date.
Turning the tide on tradition
Up until they were delivered, large steel plants have traditionally used the same unloading equipment for the iron ore and coking coal used in the steel production process, missing out on the efficiency gains that operating a Siwertell unloader offers. The world-class Ha Tinh steel plant in Vietnam’s Son Duong Port, now experiences these benefits first-hand.
“As long as there is coal on a vessel, the Siwertell continuous ship unloaders discharge it,” says Long River’s Vice Director, Nguyen Thanh Long.
When asked if the unloaders functioned exactly as anticipated when they began operations, Mr Long replied: “Yes, the unloaders have functioned well, as anticipated. Their performance is smooth and the efficiency of the Siwertell continuous ship unloader is good.”
“Their capabilities have now been proven in operation many times,” adds Per Hansson, Siwertell Contract Manager.
In addition to their primary function of handling the steel plant’s coking coal demands, the pair of rail-mounted Siwertell ST 940-DOB coal unloaders are also used to discharge thermal (steam) coal for Ha Tinh’s 2,150 MW power-generating plant.
Currently, on average, each unloader runs for around 50 hours per week. In terms of their operating schedules, in February 2019, the total running time for one ship unloader had reached around 3,000 hours and the second unloader in the region of 2,600 hours.
Superior track record
“The main reason for FPC opting for this unique arrangement of dedicated coal unloaders was because of Siwertell’s superior track record for handling coal, and for the commercial advantages that it would deliver,” highlights Mr Hansson. “FPC trusts our judgment when it comes to material handling; we have mutual respect.
“From the outset, the company was quite clear of the benefits of our equipment used in this arrangement and our primary discussions for this project related to technical solutions and additions.
“I believe that the unloaders have proved to be as cost effective as anticipated and in light of experiences at Ha Tinh, I would anticipate that other steel producers will follow suit. The advantages are there in terms of flexibility and capacity, but most importantly from an environmental perspective. With dust and emissions eliminated with our totally enclosed conveyor system, we are not only an effective solution, but also a very green one.”
Passing performance criteria
Siwertell’s contract with FPC guaranteed a through-vessel capacity equal to 70 percent of the rated capacity, meaning a discharge rate of 1,680t/h per unloader, or 3,360t/h for both. On average it will take about 60 hours to unload a 200,000 dwt Capesize vessel.
The first vessel berthed at Son Duong port on the 22nd of February 2016. The discharge process started at 16:12 pm and by 17:12 pm the Siwertell unloaders had already passed the first two performance tests for rated capacity and power consumption in handling coal.
To date, the largest vessel to be discharged is a 160,000 dwt Capesize bulk carrier. Long River says that for the popular-sized 80,000 dwt vessels that it receives, through-ship time is around two days. “This confirms our continued capabilities of maintaining an equivalent through-ship operating efficiency of 70 percent for these smaller vessels,” says Mr Hansson.
Impact of moisture content
The last three years in operation at Ha Tinh have only proved the unloaders’ capabilities even further.
“They continue to perform very well,” Mr Hansson highlights. “The original design was for all varieties of coal, but with some of the extremely wet and sticky coal types that the plant receives, we have needed to enhance the transfer section on both unloaders to improve operations and avoid all clogging issues.”
The main challenge when handling coking coal is quality. “The coal comes in many different forms, which can vary significantly from vessel to vessel, and within the load on one vessel,” says Mr Hansson. “Everything from powder to more normal chunky coal is found, and the coal can be extremely wet.
“Moisture makes the coal very sticky and build-ups are easily formed during unloading within a short period of time. This only gets worse the further down in to the hatch you dig. The client buys coal from all over the world, so one vessel can contain at least two types of coal. Regardless of type, we handle it with our continuous ship unloaders without any adjustments or actions needed,” he says.
Long River agrees that the water content of the coal poses one of the biggest challenges. “Water makes the coal sticky and can cause blockages in the horizontal conveyor, hopper and sometimes in the inlet feeder, triggering the unloaders’ autoguard feature. After removing the damper, blockages have stopped,” explains Mr Long.
Flexibility on the quay
“Like all installations, Siwertell unloaders ensure flexibility,” notes Mr Hansson. “In this case, not only by handling coking and thermal coal, of all qualities, but also iron ore; so the client has a solid back-up if the bucket-type unloaders should breakdown. We are planning to test and prove this function for the client within the first half of 2019.”
Currently, the conveyor arrangement on the quay consists of four belts, all situated underneath the unloaders. Extension plans are in motion for an additional two belts to be built behind the unloaders, in parallel with the existing conveyor system. This will ultimately deliver the ability to handle coal on three belts and iron ore on a further three.
“The unloaders’ existing shuttle belt configuration discharges coal onto the first two conveyors closest to the ship, but in line with future extension plans, it is designed and prepared to be able to discharge coal onto a third dedicated coal-handling belt, which will run in parallel to the existing arrangement,” explains Mr Hansson. “It will also be able to discharge iron ore onto a fourth conveyor when capacity requirements expand.”
Ready to meet growth requirements
Ha Tinh’s annual intake of coal is around five million metric tons; 90 percent of this is coking coal, of which eighty percent comes from Australia, with the remainder from Canadian imports. The plant’s thermal coal is mostly imported from Russia.
The plant is increasing its production steadily, and according to plan, the port handled 30 vessels during the first two months of 2019. Eventually, FHS hope to treble capacity at the Ha Tinh site and are awaiting government approval for its expansion plans; the Siwertell unloaders are expected to meet this anticipated rise in demand.
PLEASE CONTACT US FOR MORE INFORMATION
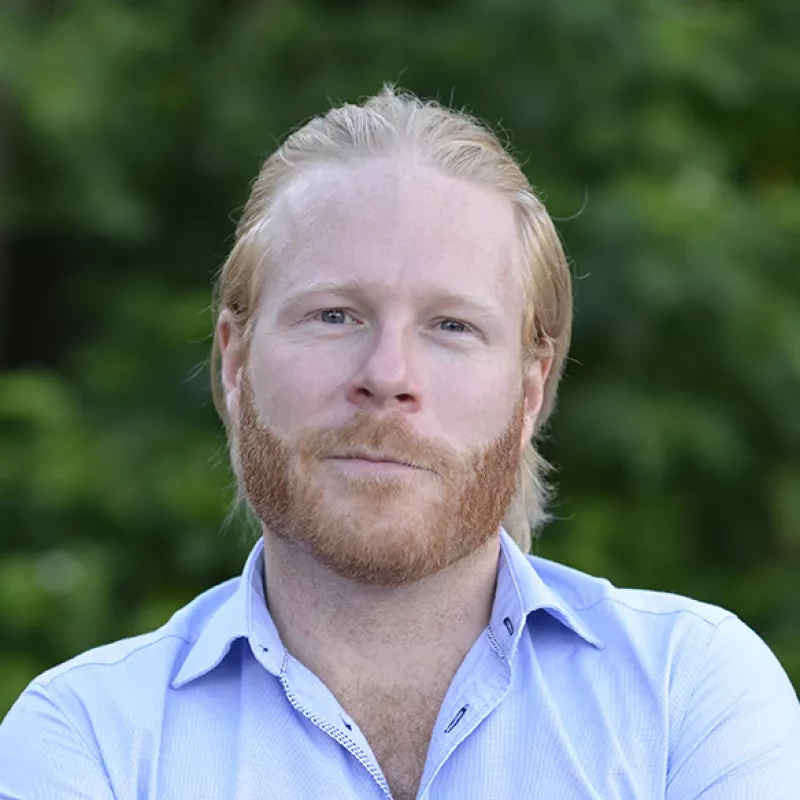
Categories: Bulk unloading