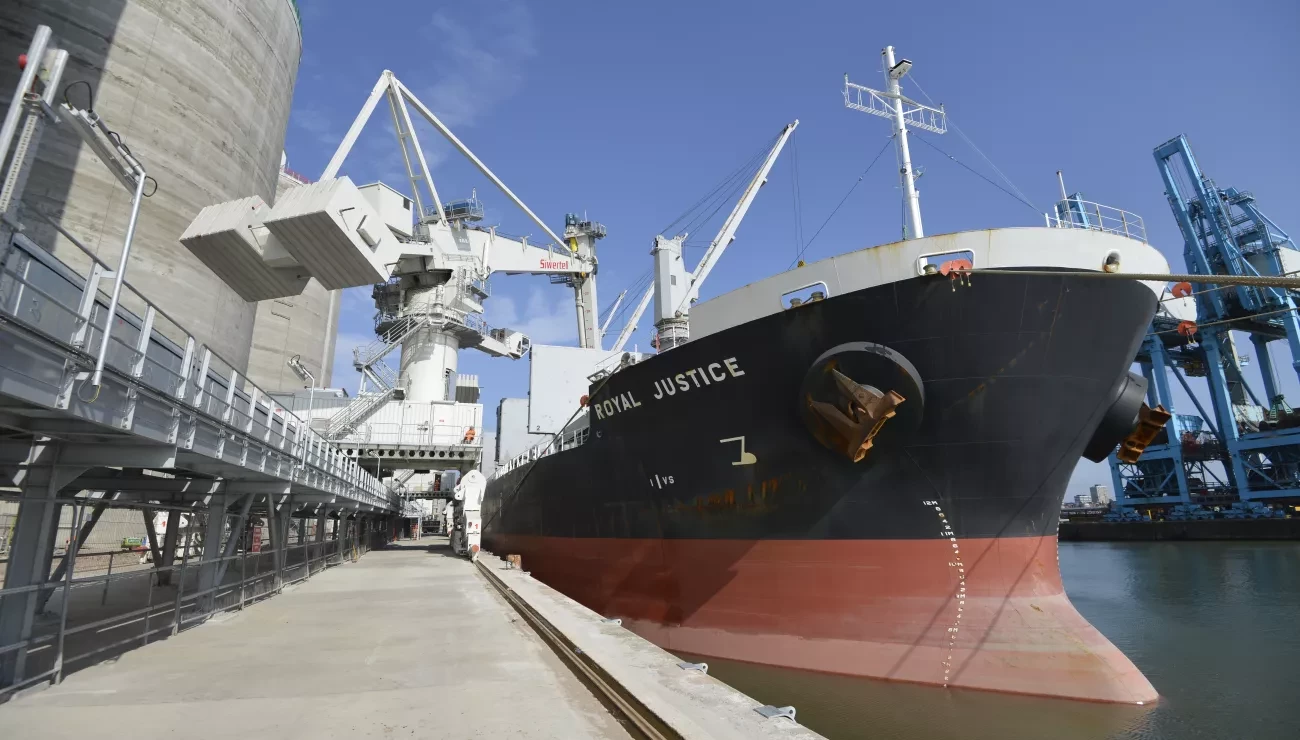
100,000 hours of biomass unloading expertise
5 Feb 2024It may come as no surprise that fossil fuels continue their energy market dominance, accounting for around 80 percent of total primary energy supply, according to the World Bioenergy Association report, Global Bioenergy Statistics 2022. However, little by little, around 0.9 percent in fact over the previous year, renewable energy sources, including solar, wind, hydro, and biomass are encroaching on this domination.
Looking at these figures in more detail, the World Bioenergy Association report separates electricity and heat production, which is helpful in understanding where different renewables are making their largest impact.
In 2020, 26,833 TWh of electricity was generated globally, 35 percent of electricity production was from coal-based sources, with renewables having a share of 29 percent, mainly driven by the increasing use of solar and wind, as well as significant contribution from hydropower and biomass.
In 2020, 15.7 EJ of heat was produced globally via heat only and combined heat and power (CHP) plants. Coal and natural gas have a combined share of more than 85 percent in the global heat production. However, World Bioenergy Association notes that renewable energy technologies, including biomass, geothermal and solar thermal have doubled their share in the global heat production over the past 20 years. Currently, 96 percent of all renewable heat produced was from biomass with minor contribution from geothermal and solar thermal technologies.
Uniformity enhances combustion
Bruks Siwertell is interested and investing in renewable technologies as part of meeting its sustainability targets, which include reducing the carbon emissions from its operations by 50 percent in comparison to levels recorded in 2019, and switching to 100 percent renew¬able electricity by 2030. However, the company’s major contribution to changing the face of the global energy market is biomass handling.
In all its forms, wood is the largest material that Bruks Siwertell handles across its technologies. Systems accommodate biomass in raw states, such as wood chips and agricultural waste, including husks and palm kernel shells, to its refined, familiar pelletized profile.
Pellets are produced by pressing and squeezing wood fibers through a die, and make good use of very small wood and agricultural waste fractions, such as sawdust. Typically, they are about 6mm in diameter, but can be larger and formed as briquettes. The extreme pressure placed on the wood-based material as it is forced through the die, increases its temperature. This forms a natural glue and holds the pellet together as it cools, however, some pellets make use of binders and additives.
The final product is a dense, low-moisture content pellet, typically below 10 percent, which then allows them to be burned with a very high combustion efficiency. Biomass pellets also have an advantage over wood chips in that their combustion profile and burning consistency are more similar to coal, and wood chips require about two to three times more storage space than pellets.
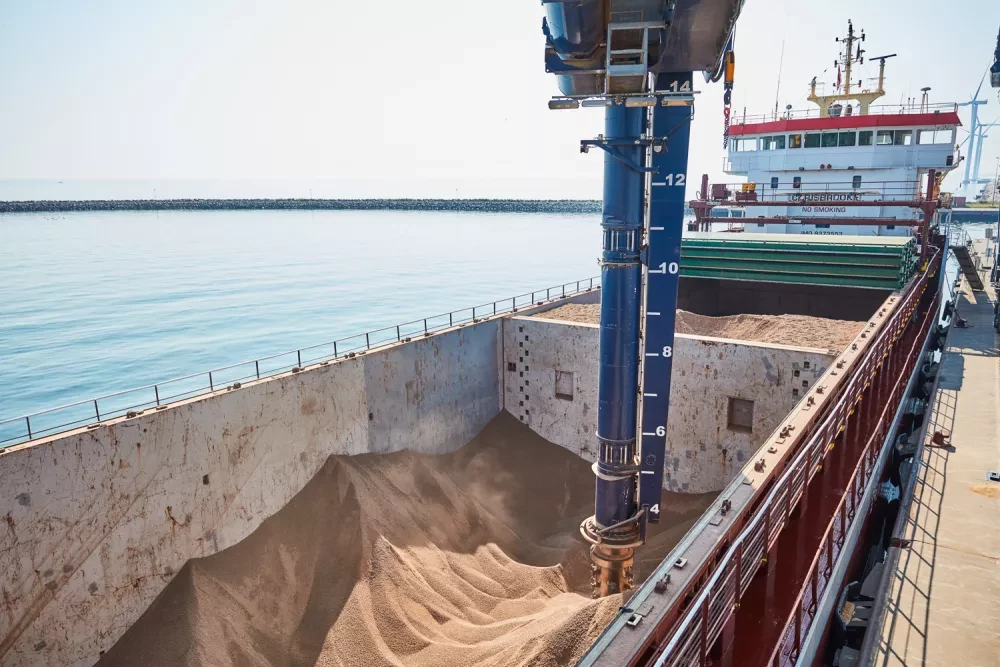
Not without challenges
All biomass, pellets, wood chips or otherwise, have three significantly challenging characteristics that arise during transportation, handling and storage. They are oxygen-depleting, delicate and can self-ignite. As biomass handing is a growth industry, these factors need careful consideration.
The safety of the maritime industry comes under the umbrella of the International Maritime Organization’s (IMO) International Convention for the Safety of Life at Sea, 1974 (SOLAS Convention), which also includes the International Maritime Solid Bulk Cargoes Code (IMSBC Code). The shipment of biomass wood pellets is noted in the IMSBC Code, which distinguishes between wood pellets that use binders and/or additives or not. Those that use them can develop flammable gases when wet, but both are classified as Group B commodities.
The main hazards relating to wood pellets being confined in a ship’s hold in bulk form are oxygen depletion and carbon monoxide development. With any organic material, the risk of microbial action has to be considered. This is particularly problematic when moisture content rises over 15 percent.
As pellets are usually shipped at lower moisture levels, and gas concentrations resulting from fermentation tend not to reach flammable levels, according to the Code, there is no requirement for any documentation certifying moisture content to be provided to the vessel.
Keeping cool in the holds
However, wood pellets can also generate heat by oxidation of their fibrous material. This is a natural result of their manufacturing process, which exposes wood fibers to the air, slowly facilitating the oxidation process. It is this process that depletes oxygen from the hold. Fines, generated from pellet degradation during handling, are also more prone to oxidation.
Furthermore, the oxidation of wood pellets or fines releases heat. If heat is generated relatively slowly, the cargo temperature rises a little, but will stabilize. It is, however, possible for wood pellet heating to become self-accelerating to the point of fire.
Wood pellets are generally shipped without any venti¬lation in the hold, which means that any self-heating tendencies, and its consequences, including carbon monoxide production and oxygen depletion, is usually self-limiting, as the amount of oxygen in the hold is limited. The IMSBC Code notes that extreme caution should be taken when opening and entering the hold.
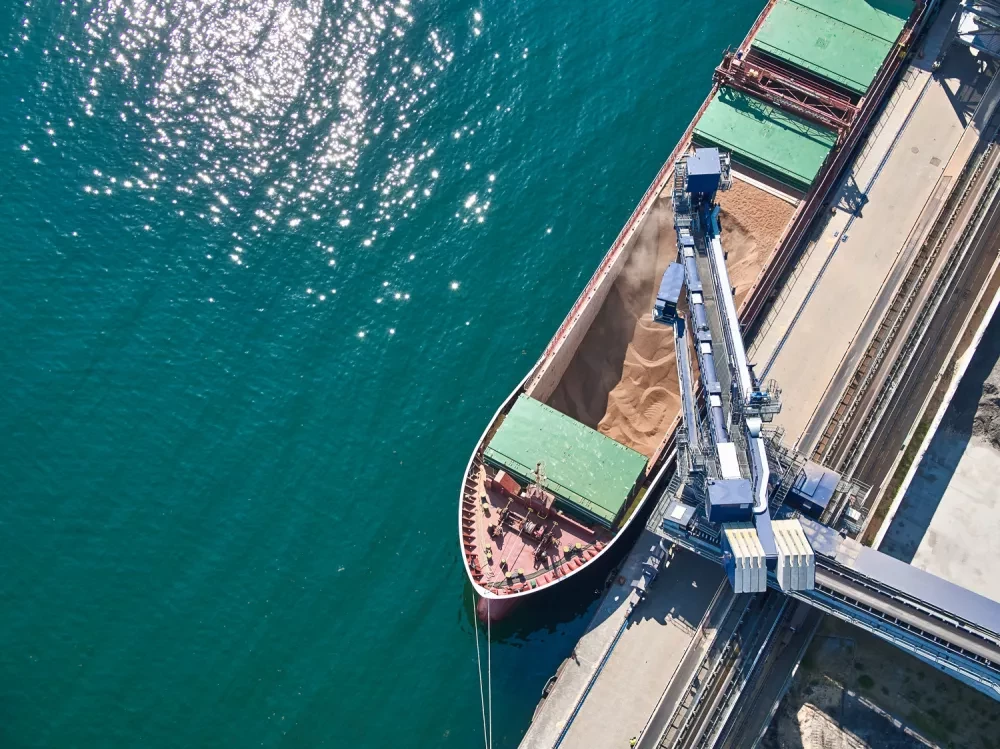
Mitigating enclosed risks
When the holds are open, it is Bruks Siwertell’s turn to add its expertise and safely complete the ship to shore link, transferring the biomass, with minimal material degradation, for the next leg of its journey. To put this knowledge in perspective, Siwertell ship unloaders have now clocked up almost 100,000 operational hours of discharging biomass in ports.
Central to this capability is the Siwertell ship unloader, ranging from road-mobile models, up to large-scale unloading systems.
All have been designed to handle biomass safely and are equipped with a sophisticated, in-house-designed safety system, which has the capacity to suppress and withstand dust explosions and mitigate the risk when handling biomass in an enclosed space.
Bruks Siwertell has a lot of experience handling self-igniting dry bulk materials, developing the Siwertell Sulfur Safety System (4S) many years ago in response to ensuring the safe, enclosed handling of sulfur. The capabilities of both the biomass and sulfur safety systems mean that Bruks Siwertell offers the market a continuous, high-capacity ship unloading system that can enclose volatile dry bulks safely.
Siwertell systems also protect the delicate pellets from degradation through steady conveying velocities and careful handling, and they minimize environmental impact by enclosing fugitive dust and eliminating cargo spillage.
Biomass handling Siwertell ship unloaders are located around the world, supporting the phaseout of coal and helping power stations make the switch from fossil fuels to renewable sources.
A final farewell
Last year, global renewable energy company, Drax, announced that almost 50 years of power generation from coal at its North Yorkshire power station in the UK has come to an end. Drax Power Station was once Western Europe’s largest coal-fired power station but, over the years, has been transformed into the UK’s single-largest generator of renewable electricity; its four biomass units generated 12.7 TWh of electricity in 2022.
It is now in discussions with the UK government, where biomass accounted for 8.6 percent of energy supply in 2022, to employ bioenergy with carbon capture and storage (BECCS) to permanently remove millions of metric tons of carbon dioxide from the atmosphere.
The lion’s share of wood pellet supply for Drax’s boilers are US imports, which are processed and handled using Bruks wood-processing equipment, truck receiving and ship loading systems.
Once their transatlantic journey is complete, Drax receives biomass unloaded at several UK locations including the Immingham Renewable Fuels Terminal (IRFT), operated by Associated British Ports, where the US wood pellets arrive on dedicated self-trimming bulk vessels of between 25,000 and 50,000 dwt. Since 2014, these cargoes have been discharged by two rail-mounted ST 790-D Siwertell ship unloaders and prior to that they handled coal.
In 2016, the Ligna Biomass terminal in Liverpool, UK, came online. Operated by Peel Ports, the material terminal can store up to 110,000 metric tons of biomass. Like IRFT, Ligna is equipped with two ST 790-D high-capacity unloaders, which supply the power station with up to ten train loads of pellets per day and account for up to 40 percent of the total biomass consumed by Drax each year.
Also in the UK, following an agreement with the Spanish-Korean consortium, TR-Samsung, a Siwertell ship unloader was ordered to support a new 299MW biomass-fueled power plant in Teesside, Middlesbrough, UK. Delivered in 2018, the tailor-made, rail-mounted ST 790-type D Siwertell unloader is located close to the plant.
It is designed to discharge wood pellets and wood chips to a matched Siwertell jetty conveyor with a movable transfer trolley, supplied as part of the contract, and has a rated average capacity of 1,200t/h and a maximum rate of 1,320t/h, which are designed to meet the plant’s requirements of 16,000 metric ton/day. It is equipped with a dual truck loading system for continuous direct truck loading at a rate of 300t/h. This is a redundancy feature that allows operations to continue if shore conveying is interrupted.
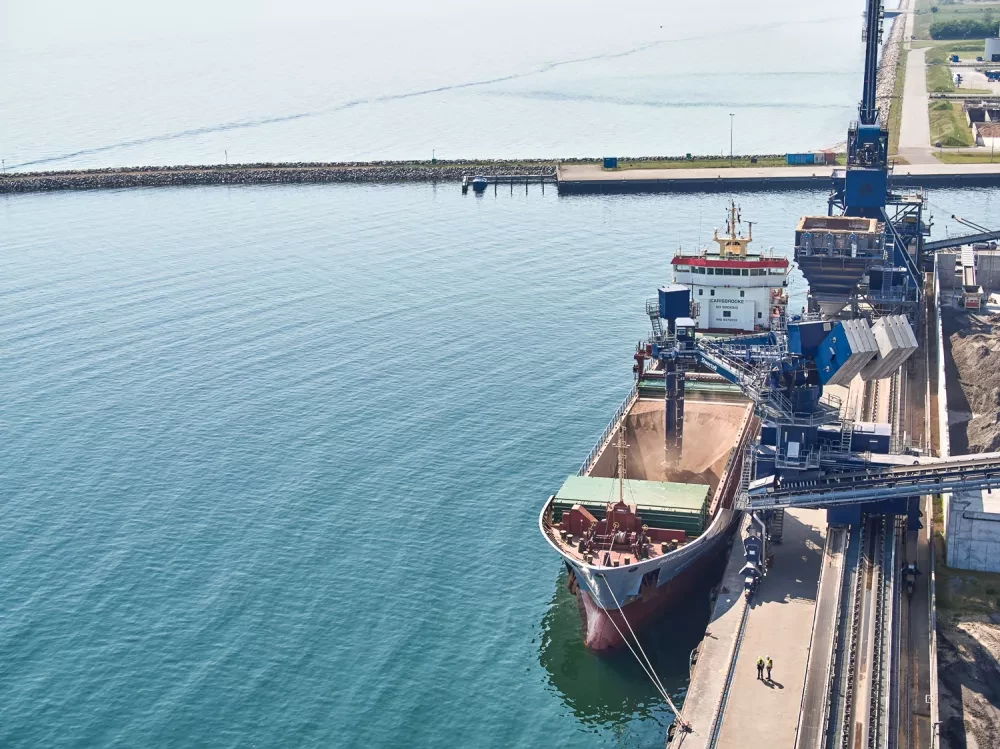
Combining heat and power
Other notable references include securing fuel for Denmark’s Avedøre combined heat and power (CHP) station. It is one of the most efficient in the world, able to burn coal with as much as 94 percent efficiency by converting 49 percent of its potential energy into electricity and distributing the other 45 percent as residential and industrial district heating.
Avedøre’s operator, Ørsted, formally Denmark Oil and Gas (Dong Energy), has reduced its coal use by 73 percent since 2006, replacing it at its various power plants with biomass, as part of its target to ultimately phase out coal power completely by 2023.
For this installation, a rail-mounted high-capacity Siwertell ST 790-D unloader has operated in the Avedøre harbor since 2013. Again, originally ordered for unloading both coal and biomass cargoes interchangeably. It now handles 100 percent biomass, after Ørsted con¬verted the plant for full-biomass operation in 2016.
In Asia, biomass often takes the form not only of wood pellets, but also palm kernel shells from Indonesia and Malaysia. In southeast Asia, at the Tembusu Multi-Utilities Complex (TMUC) on Jurong Island in Singapore, a combination of energy production, desalination, and wastewater treatment is powered using coal and palm kernel shells. Two ST 640-M rail-mounted Siwertell unloaders, TUAS and TUAS II, have served TMUC since 2012, seamlessly alternating between unloading coal and palm kernel shells.
Biomass continues to boom
According to Research and Markets, the global biomass power generation market is estimated to grow from USD 91.3 billion in 2023 to USD 105.7 billion by 2028, with much of the demand being driven by the industrial sector. Most analysts are predicting similar demand increases, which leaves the sector needing to meet huge rises in demand. Siwertell ship unloading systems are ready, tailored for the task and will meet capacity demands in a sustainable way, further enhancing biomass’ renewable credentials.
PLEASE CONTACT US FOR MORE INFORMATION
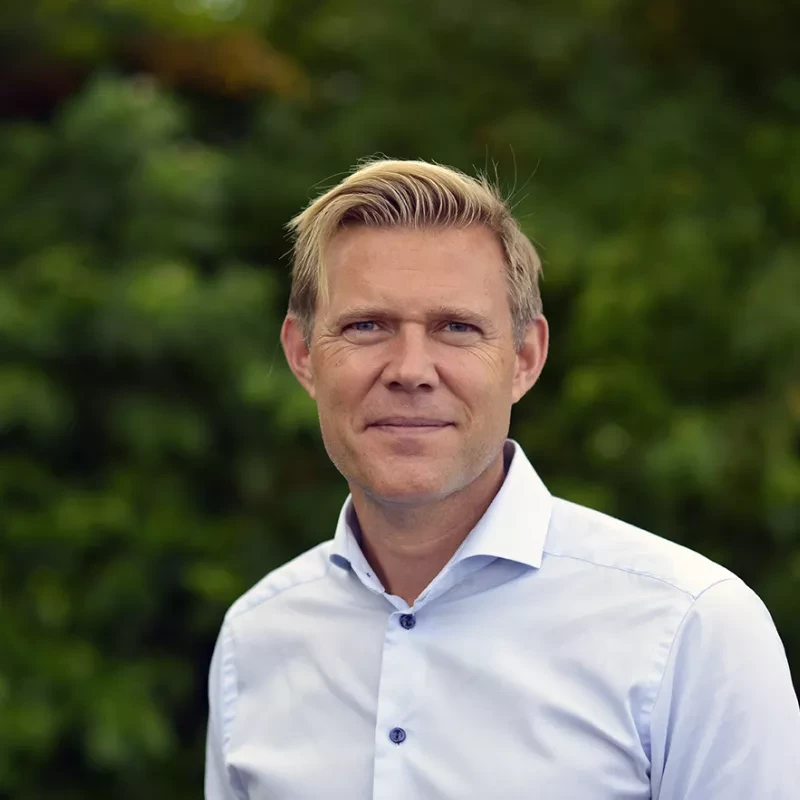