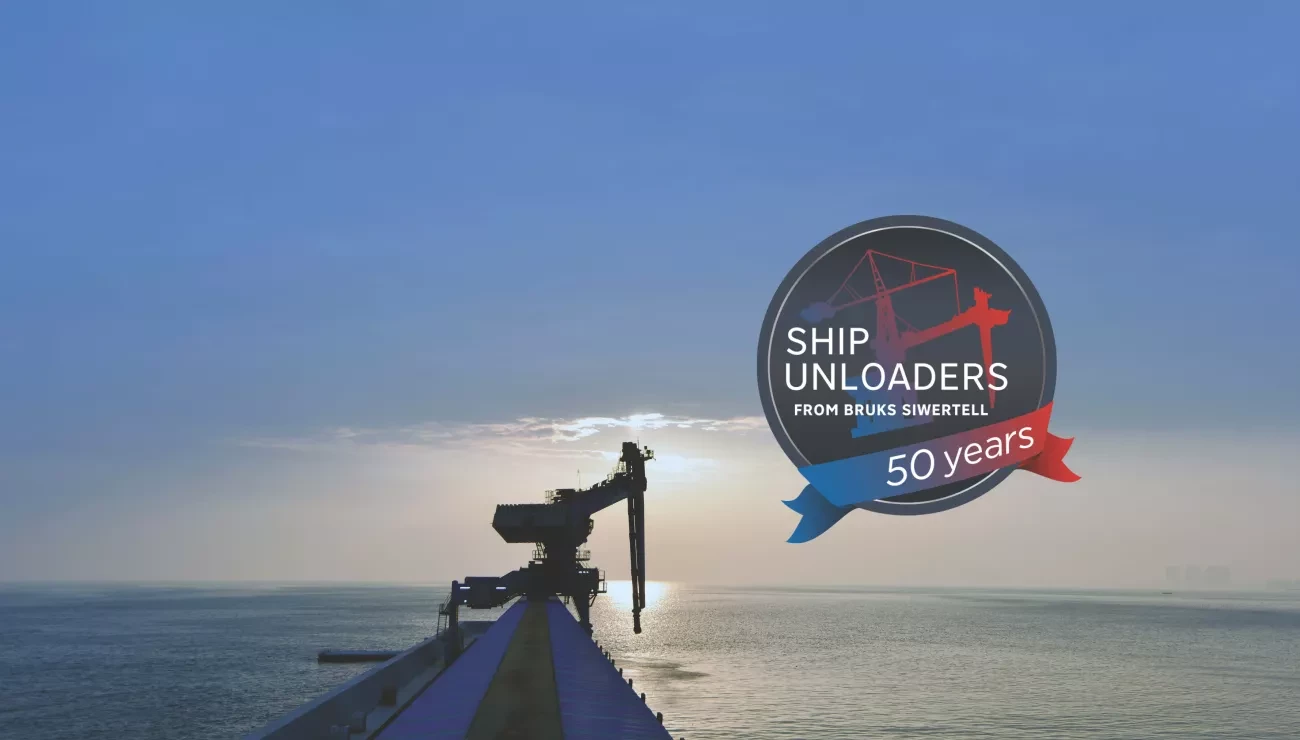
50 years of innovation, set for a new era
10 Jan 2024Siwertell technology has revolutionized the dry bulk handling industry, with unmatched capacity, environmental credentials and through-ship performance; Jonas Fack, President of Bruks Siwertell AB, explains how it is keeping its market-setting pace.
For fifty years the Siwertell brand has been synonymous with the dry bulk handling market. Established in 1974 to develop continuous, efficient, enclosed ship unloading equipment, the Siwertell brand is now part of the Bruks Siwertell Group.
Since merging in 2018, two world-leading brands, Bruks and Siwertell, have combined their complementary strengths. Both brands have their roots in Sweden and have successfully grown through the development of pioneering industry solutions.
Bruks technology is central to a renowned product portfolio of wood-processing, conveying, storage, and stacking and reclaiming systems, and is a mainstay of the American and European timber industry. Siwertell technology, comprising screw-type ship unloading systems, versatile road-mobile and port-mobile unloaders, loaders, and bulk terminal solutions, leads the global dry bulk handling industry.
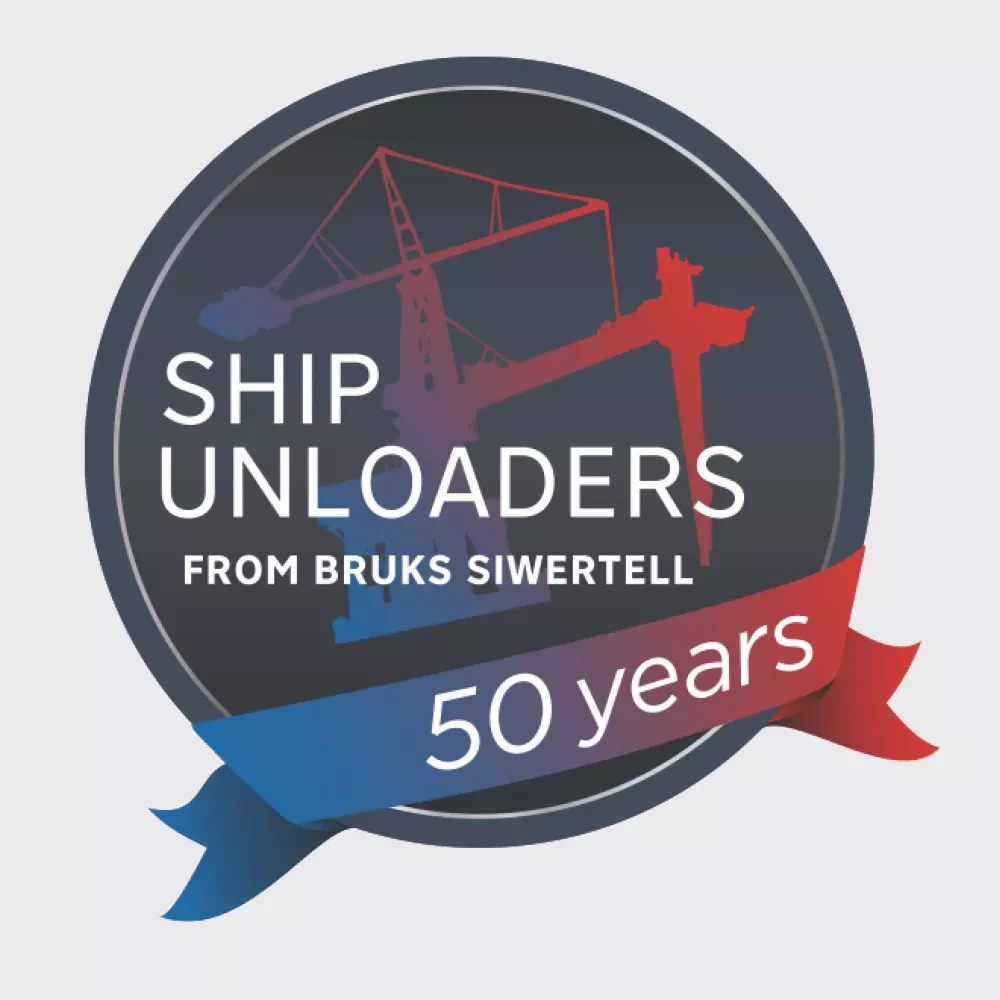
Unmatched on the market
With the Group now celebrating the 50th anniversary of its Siwertell ship unloaders, it also celebrates its incredible industry success. No other continuous mechanical ship unloading system can discharge dry bulk materials from a vessel faster, and with less environmental impact than a Siwertell ship unloader. It is also the only enclosed ship unloading system that can safely handle biomass and sulfur at very high capacities.
For some operators, compared with switching from traditional dry bulk handling equipment, such as a grab crane, the high-capacity capabilities of a Siwertell ship unloader have meant a reduction in unloading days of 50 percent, translating into a 50 percent reduction in berth occupancy and the possibility of higher annual intakes; with return on investment achieved in less than two years. These are familiar stories within Bruks Siwertell.
A year after its market introduction, Siwertell technology made one of its biggest industry impacts; it began to transform global cement handling installations. The first screw-type Siwertell ship unloader was supplied to the cement industry in 1975. In 1980, a new standard for the industry was set by introducing the 800t/h Siwertell unloader to the market and since then, it has continuously set the highest bar. Today, Siwertell cement unloaders offer continuous
rated capacities in excess of 2,000t/h.
The main reason for their high overall efficiency is that Siwertell screw-type unloaders maintain continuous unloading at a steady discharge rate, regardless of the level of cargo in the hold, right up to the hold clean up stage. Further adding to its efficiency, is hold reach, right into the corners. This results in quicker vessel turn¬around and reduced berth occupancy. Siwertell screw-type ship unloaders deliver efficiencies of 70 percent or more, while most alternative unloading systems offer efficiencies of between 50 and 60 percent.
Inlet feeder advances
From an outsider’s glance, Siwertell unloaders look much the same as they did 50 years ago, with key operating principles remaining unchanged. The single most significant innovation on a Siwertell ship unloader is still the originally patented, counter-rotating inlet feeder. It was designed and developed by the two Swedish inventors, Olle Siwersson and Gunnar Tell, who combined their surnames to give the brand its name.
Inlet feeders ensure efficient cargo pick-up and a high filling rate of the vertical screw conveyor, and can with¬stand significant digging forces, break up compacted material and reach high unloading efficiencies. They pick up material under the cargo’s surface, minimizing dust emissions, unloading layer-by-layer and avoiding cargo avalanches, therefore providing a safe operation with limited dust emissions in the cargo hold.
Bruks Siwertell is always looking to improve its tech¬nology to deliver the most commercial benefits to its customers. As part of this, the company has recently introduced a new inlet feeder for its large-scale Siwertell ship unloaders.
The new inlet feeder was a customer-driven develop¬ment, designed to deliver very high through-ship capacities and the overall efficiency of unloading operations, particularly as material gets lower in the hold. Developed using advanced simulation techniques, and tested in real-world conditions, through-ship capacity test results exceed expectations.
Importance of R&D
In terms of other mechanical advances, following a series of research and development (R&D) programs, which started in the 1990s, Bruks Siwertell has continually increased the lifetime of screw conveyors through the use of new materials. Most recently, from a new program that started in 2021 focused on the agri-bulk sector, significant improvements in the lifetime of the vertical screw conveyor, and its wear parts, were realized.
The developments are applicable to Bruks Siwertell’s entire portfolio of screw-type equipment including Siwertell ship unloaders, loaders and conveyors.
The Siwertell Sulfur Safety System (4S) was also a significant development, which has continually been refined. All Siwertell unloaders, delivered to handle sulfur, are fitted with the 4S. It detects and extinguishes fires early, shutting down the system to stop their spread, and safely containing them. An automatic system lubri¬cates and cools the end and intermediate bearings to reduce the risk of ignition, and explosion-proofing is also included, with vents and reinforced casings.
Although, originally intended for safe sulfur handling, the 4S has now been adapted to accommodate the enclosed conveying of other hazardous, and potentially self-igniting dry bulk materials, such as biomass wood pellets. Its presence on a Siwertell unloader enables operators to make sustainable energy switches from coal to renewable biomass.
Volumes continue to grow
In terms of the dry bulk market, a lot has happened over the past five decades. Volumes have increased and with that, so have vessel sizes. Fifty years ago, a Handymax-sized vessel was large, at around 50,000 dwt, twenty-five years ago Panamax vessels, up to 80,000 dwt were standard, and we now have new Panamax at 120,000 dwt. Today, we see a lot of dry bulk materials shipped in Capsize vessels, up to around 170,000 dwt.
With these increases in vessel size, higher unloading and loading capacities were and are required, together with demands for higher efficiency, increased reliability and improved availability. Today, Siwertell ship unloaders can be delivered with rated capacities of up to 3,000t/h, and new high-capacity Siwertell loaders can deliver rates of up to 12,000t/h, serving the world’s largest ore carriers of up to 400,000 dwt and 230,000 dwt coal carriers.
A digital future
As for the future, digitalization will probably provide the most opportunity and present the greatest challenge. Data collection, data analysis, with machine learning and artificial intelligence (AI)-driven solutions are not a distant dream any longer. The industry is very likely to move towards autonomous operation, troubleshooting and maintenance, with the automatic replenishment of spare parts, for example.
Bruks Siwertell is already working on launching remotely operated unloaders and loaders. This will be followed by autonomously operated machines and ultimately a synchronized autonomous operation with a combina¬tion of Siwertell technology and payloaders, absolutely minimizing environmental impact and providing highly efficient, safe, and healthy operations.
Just in the last few years, numerous digital develop¬ments, including Siwertell Smartview in 2022, have been introduced. Siwertell Smartview is a cloud-based industrial Internet of things (IIoT) system, which will be initially integrated into new Siwertell technology. It is designed to offer a better understanding of operational and component performance through enhanced data visualization and analysis.
Siwertell Smartview collects data during unloading and loading operations, which provides detailed analysis of equipment performance, availability and reliability. The tool can monitor real-time operational parameters such as tons of material handled, average capacity, tons of material remaining in the vessel’s holds during unload¬ing, and the overall duration of operations.
A significant element of Siwertell Smartview is report generation, and the ability to identify areas that can be improved, leading to widely achievable enhances in effi¬ciency and therefore a terminal’s potential profitability.
Enhanced service capabilities
The use of IIoT-enabled equipment delivers benefits to customers in terms of service as well, with many new Siwertell road-mobile dry bulk handling unloaders featuring advanced digital technology for diagnostics and troubleshooting.
The use of digital technology in service is also evidenced with the recent introduction of new Siwertell Care plan-ned service agreements for Siwertell road-mobile ship unloaders, with augmented reality (STC-AR).
STC-ARs are next-level planned service agreements and involve AR glasses, which can be purchased so that customers can wear them and remotely connect with experts, enabling surveyors to see what maintenance personnel can see. Technical issues can be addressed even more quickly, along with streamlining communica¬tions. They can also mean that more complex mainte¬nance tasks can potentially be carried out in-house, and that the cost and frequency of engineer call-outs can be reduced.
Tomorrow, not just today
The past twenty years have also seen much closer envi¬ronmental scrutiny within the dry bulk material industry, and in more recent years, this has been accelerating. In line with this, Bruks Siwertell has developed its own sustainability targets, publishing progress through an annual sustainability report.
The sustainability targets that Bruks Siwertell Group has set are of course extremely important, not only for the company, but also for the world, and for generations to come. In relative terms, the easiest targets are the ones that the company can directly control, such as: zero waste; 100 percent renewable energy; 100 percent compliance with Codes of Conduct; and 100 percent updated work processes. Good progress is already being made with these.
Our sustainability work builds on the environmental credentials of our technology. Investing in a Siwertell ship unloader is the most cost-efficient and environmen¬tally responsible choice that an operator can make for its dry bulk handling needs. Long lifetimes, low operational costs and equipment weights, high nominal unloading capacity, and unparalleled unloading efficiency, along with low noise levels, minimal dust and no spillage, make our machines outstanding from an operational, environ¬mental and health and safety perspective.
The industry landscape is rapidly changing and Siwertell technology will not just keep pace, but will continue to set the standard, just as it has done in the cement handling market; a position that is still held. Over fifty years, Siwertell technology has revolutionized dry bulk unloading operations worldwide, and with eyes to the future, will continue to do so.
PLEASE CONTACT US FOR MORE INFORMATION
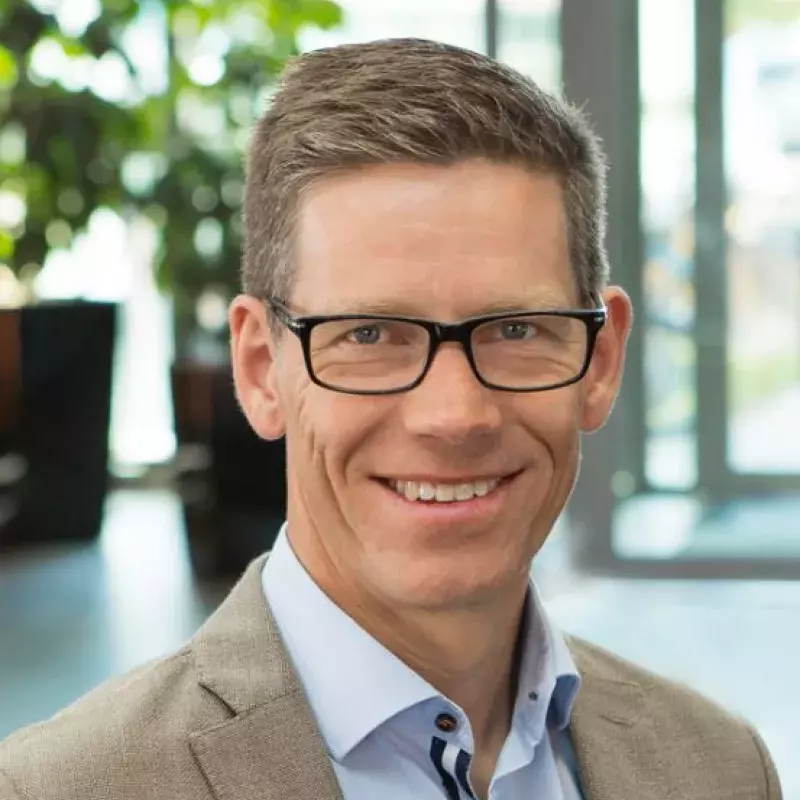