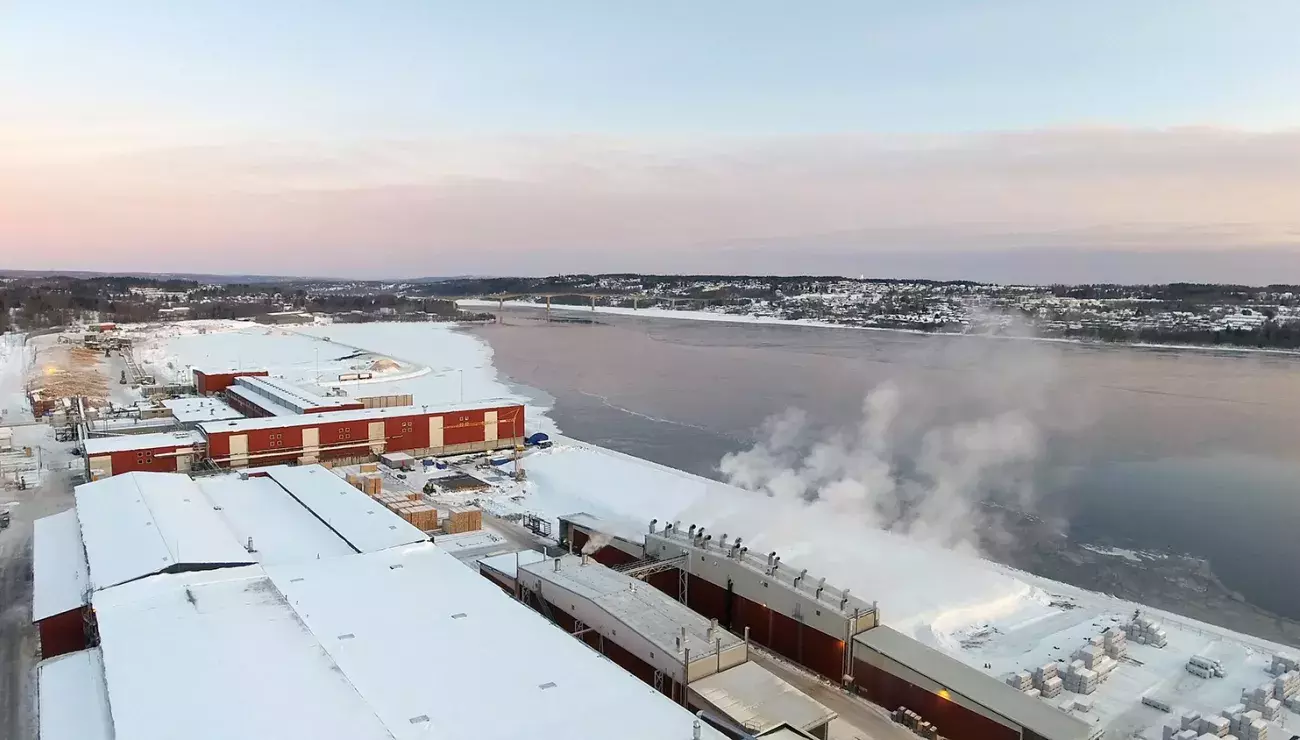
Blossoming sawmill business boosted by innovative waste wood residue solution
18 Nov 2020Following a ten-year development plan that has seen a new sawline inaugurated in 2016 and a new planing mill in 2018, SCA’s Tunadal Sawmill, in Sundsvall, Sweden, is going from strength to strength.
In fact, over the past decade, the Swedish forestry, processed wood and renewable energy company has invested more than SEK 1 billion in the Tunadal Sawmill; one of SCA’s five sawmills. Focusing on increased production capacity, higher processing capabilities and environmental improvements, SCA has made Tunadal one of the largest and most modern sawmills in Sweden.
Production is growing at such a pace that last year its owners applied for a new environmental permit to expand capacity to a maximum of 900,000m3 of solid-wood products per year, as the maximum volume allowed by its existing one had almost reached its annual capacity of 600,000m³.
SCA plans to be able to continue developing Tunadal, with capacity gained from increasing the use of current facilities and potentially investing in more; energy production from wood biomass is also being considered. SCA says that there is plenty of room for the expansion, and points out that the sawline stands on land that was actually sea only ten years ago.
Innovation beneath the sawline
Underpinning the activities of the mill is a byproduct processing and handling system from Bruks Siwertell. Contracted at the end of 2014 and installed in 2016, the complete delivery includes two 120m-long air-supported, low-friction TubulatorTM conveying systems, type CT1000SL and CT800SL. They form the sub floor beneath the sawline, where enclosed separate plate chutes transfer wood chips and sawdust directly onto their corresponding conveyor.
One Tubulator transports sawdust at a rated capacity of 600m3/h and the other wood chips at 1,000m3/h, giving the system a total wood residue handling capacity of 1,600m3/h. Air flow in the conveyors is optimized so that the pressurized air-cushion carries the belt with or without material.
Although the materials have been initially separated, the wood chips still contain a certain amount of sawdust and pin chips. Therefore, from the Tubulator conveyors, wood chips are transferred, via a screw conveyor, to a four chip-screening system, which has a total capacity of 1,000m3/h; 250m3/h per screen. It sorts material into four fractions: oversized, acceptable-sized wood chips, sawdust and pin chips. Oversized chips are processed further in a Bruks drop-fed drum chipper and the pin chips are distributed between the sawdust and the acceptable-sized chips.
The desired wood chips are transported via conveyor belts, a bucket elevator, roller conveyors and a distribution rack to storage. The sawdust is transferred directly to storage from the Tubulator conveyor under the sawline and a vertical screw conveyor. The mill has the capacity to store 600m3 of sawdust and 1,000m3 of wood chips.
Larger offcuts from the mill’s ‘green sorter’ feed a vibratory conveyor and are processed by a second Bruks drum chipper. The processed chips are then raised in a vertical screw-lift, and also fed into the four-stage screening system via a Tubulator, type CT518, conveyor, prior to storage.
Air-cushion advantages
“Our Tubulator conveyors deliver significant operational advantages to SCA in comparison with conventional trough conveyors under the sawline and throughout the system,” explains Bo Sjöstedt, Area Sales Manager, Bruks Siwertell. “They are enclosed, which ensures a dust-free environment and have high conveying capacities, in relation to their size. Also, their energy consumption and maintenance requirements are significantly lower.
“The entire wood residue handling system has been designed to ensure very low levels of atmospheric dust,” he continues. “As well as the enclosed Tubulators, there are dust covers and brush seals at the screen stations, and an extractor and ducting over the screening system, drawing dust away.
“Tunadal really showcases the capabilities of our technology, plant design and project management,” notes Sjöstedt. “It was complex, but resulted in one of the most powerful, cleanest and efficient waste wood residue solutions possible. Four years on, and SCA is still extremely satisfied with its performance.”
Sustainability: a million seeds a day
SCA’s business is focused around 2.6 million hectares of slow-grown Nordic pine and spruce forests in northern Sweden, with expansion into eastern Europe. A total of 100 million seeds will be planted this year by SCA’s seedling operation, NorrPlant; sowing an average of a million seeds a day at its two nurseries. SCA note that its cultivated seedlings produce up to a 25 percent growth improvement compared with natural rejuvenation, producing a forest that grows well and binds carbon dioxide to counteract climate change.
Renewable raw material is at the heart of SCA’s portfolio of packaging, print and pulp wood products and renewable energy. Ensuring that nothing is wasted at any point in the supply chain is essential to the environment and is also commercially valuable. The company is one of Sweden’s largest biomass pellet manufacturers, predominantly using wood residues from its own sawmills, including the sawdust from Tunadal. Other byproducts from the mill are fed into SCA’s diverse processed wood operations.
PLEASE CONTACT US FOR MORE INFORMATION
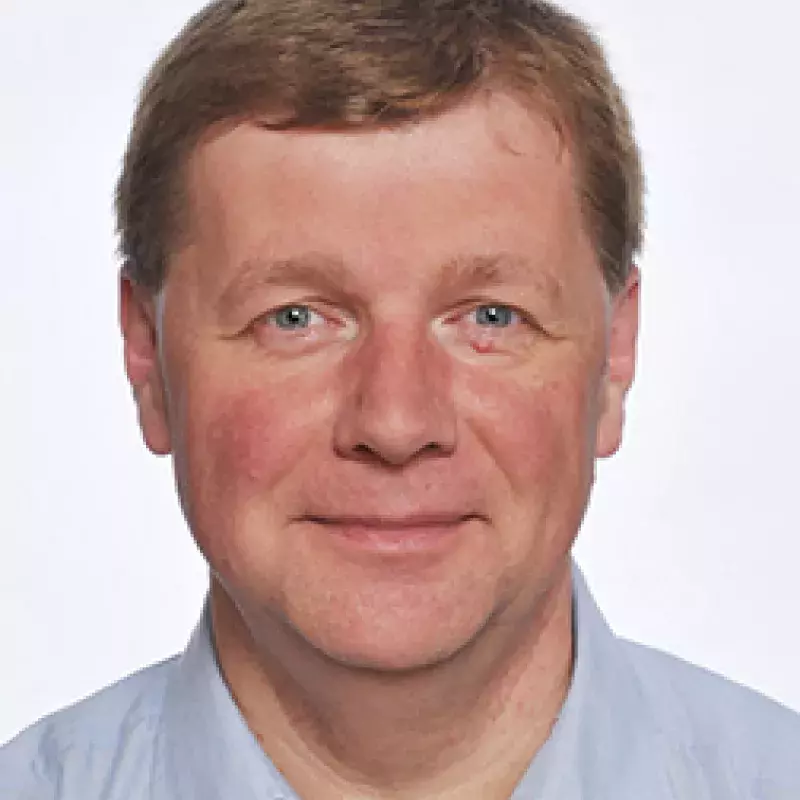