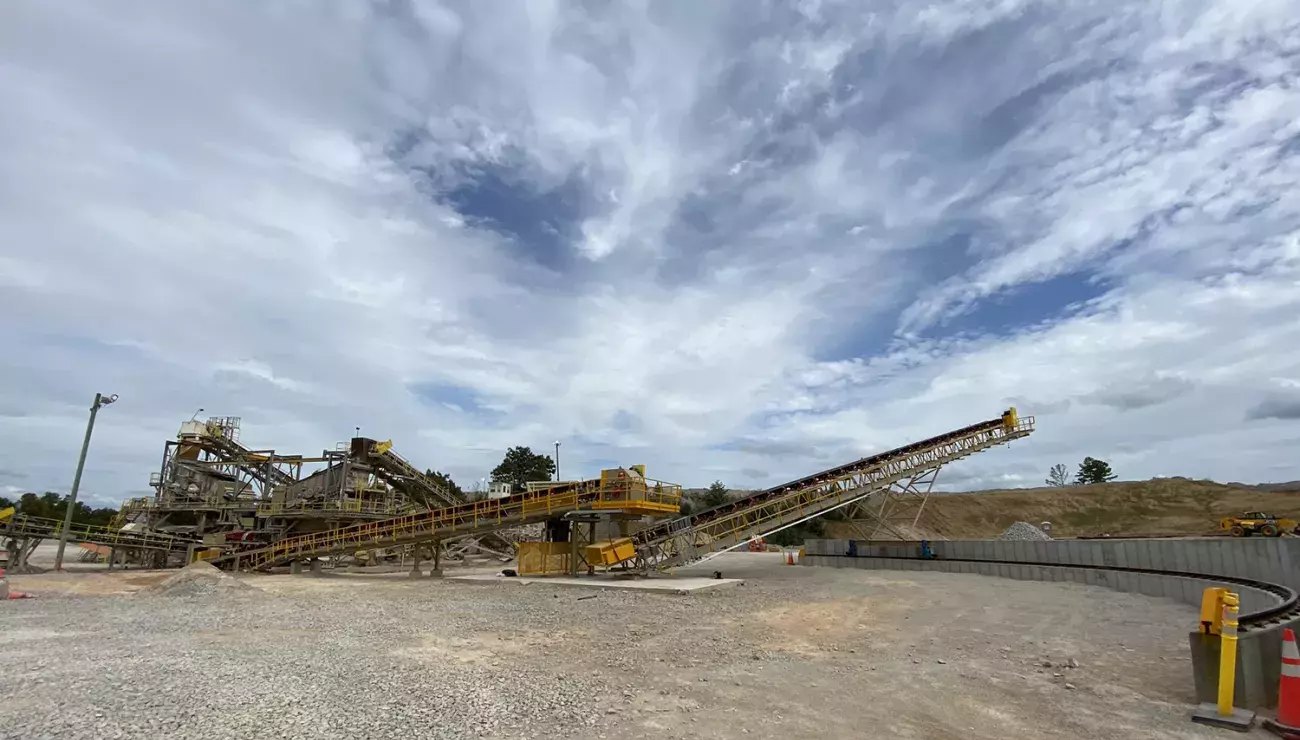
Aggregate stockpile system increases production capacity at Alabama mine
16 Jun 2021Reputation is everything; each supplier in the chain needs companies and equipment it can rely on, recently benefiting from the quick delivery of a tailored dolomite stockpiling system is Lhoist Group subsidiary, Lhoist North America.
Lhoist Group knows a lot about aggregates. The company has global status as a leading producer of lime, dolime, sometimes known as dolomitic lime, and minerals. Lhoist understands what it needs from the dry bulk handling equipment that keeps these caustic, alkaline materials flowing from mines to end users.
Commencing operations in Belgium in 1889, the company has undergone a series of expansions, and now operates around 100 facilities, including lime, limestone and dolomite plants, in more than 25 countries. Lhoist’s development has also seen an international spread, and in the 1980s, it established, Lhoist North America.
Lhoist North America also has a reputation firmly placed as a major supplier of lime, limestone and clay products throughout the US and into Canada. One of its key locations is the Brierfield quarry, near Brierfield, in Bibb County, Alabama. This active stone mine specializes in crushed, broken limestone, and for the past few months has been seeing the benefits of new aggregate handling equipment from Bruks Siwertell.
Keeping up with demand
“The mine opened several years ago and has been steadily increasing its production capacity ever since, but to keep up with current demand, it needed a new stockpile solution,” says Zack Hood, Vice President, Conveyor Technology Solutions, Bruks Siwertell.
“Mines and quarries require robust, high-capacity equipment, particularly those that handle very abrasive or corrosive materials,” continues Hood. “It has to keep pace with the mine’s production goals and also onward demand. Stockpiling is therefore a critical aspect of these facilities and ensures that there is enough of a buffer between supply and demand.”
Bruks Siwertell offers a range of handling and storage options for aggregate materials, and mines, such as Brierfield, often prefer the advantages that radial stacker equipment offers.
“Radial Stackers are really effective at helping operators maintain inventories, and maximize storage volumes with minimal handling and mobile equipment,” explains Hood. “Dry bulk material is received from a conveyor to an in-feed hopper, which moderates and optimizes flow. It is then fed onto a conveying arm that is supported along its length on rails or on a rubber tire gantry. This conveying arm pivots at one end, enabling it to slew in a circular motion so material can be distributed in a radius around the stacker forming kidney bean-shaped storage piles. Conveying arms can be telescopic, so the radius of the storage pile can be increased.
“Although this is our first aggregate install in America, as a company we have a great deal of experience with aggregates and delivering their different handling and conveying systems, including storage and reclaiming equipment,” he says.
18 weeks: start to finish
“Lhoist worked with one of our representatives early in 2020 to consider a solution that had the potential to increase production capacity at its Brierfield quarry, and manage its stockpile more effectively,” notes Hood. “Our ability to take on the full scope of the project, so the entire stockpile system, along with our competitive pricing and delivery within 18 weeks, meant that Lhoist placed an order in May 2020, we delivered in August 2020, and the plant was fully commissioned by September.”
Bruks Siwertell supplied the equipment, installation, and foundations. Its scope of supply included all new chute work for wet and dry screens, new access platforms for the site’s existing screens, a new idler conveyor, and a new radial stacker. The entire system has a rated capacity of 240t/h and predominantly handles the mine’s main aggregate, dolomite.
“This is a very versatile and widely used material,” adds Hood. “Not only as a source of magnesium oxide, and as a concrete aggregate, but it is used in very significant volumes in the production of float glass. So, an important aggregate.”
Positive early results
“The system has now been operational for several months and the owner is extremely satisfied with the results. It has not only achieved its original aim of improving the mine’s stockpile arrangements, and reduced the need for manual operations, but it has also achieved the desired increase in production capacity of the facility as a whole,” he concludes.
Following this installation at Brierfield, Bruks Siwertell is currently working on the delivery of three new idler belt conveyors for Lhoist’s Marble Falls plant in Texas, which was commissioned in 1983 as part of Lhoist’s original expansion across the Atlantic from Belgium. This system is scheduled to enter operation by the end of summer 2021.
For more information, please send an email to sales.atlanta@bruks-siwertell.com