Description
Bruks Siwertell offers Service agreements for its full range of ship unloaders, including road-mobile units. These are available for new and existing unloaders, and deliver a number of advantages.
Our preventative and planned service products make it easier to schedule services and plan and spread the cost of equipment maintenance. They offer a fixed cost for a set number of surveyor visits and guarantee that parts are in place. Agreements are also extremely cost-effective for the operator, with favorable discounts on spare parts included.
An agreement includes regular inspections, carried out by a certified Siwertell surveyor, to efficiently and accurately assess an unloader’s condition, safety and performance. They also include training that covers mechanical, instrumentation and electrical maintenance. Training occurs on a regular basis, topping-up operator maintenance knowledge at each visit.
To ensure that each agreement meets every operator’s need, they are modular, flexible, and tailor-made to respond to individual requirements. The frequency of surveyor visits is a key consideration and is why we suggest specific timeframes, depending on the operation and unloader type.
Each visit generates a report, which covers an overview of the maintenance training and work carried out. It can include any requirements for special attention, maintenance, repair or upgrade, and recommendations for any further investigation, assistance or training needs. Spare parts and guidance with regard to obsolete components or systems is also covered.
Our next-generation road-mobile unloaders are now being fitted with the Gateway, an Internet of things (IoT) device, which enables extensive monitoring, follow-up, support and trouble-shooting through safe, remote access.
If an unloader is fitted with such a device, remote, web-based support can be included as part of the maintenance agreement.

Main Features
- Regular mechanical and electrical inspection of road-mobile unloaders.
- Opportunity to supervise any work being carried out during a planned visit.
- Opportunity to discuss operational or performance queries.
- Ongoing operator maintenance training, which builds in-house knowledge.
- Fixed cost for an agreed number of planned service visits per year.
- Potential for web-based, remote support.
- Discount available for spare parts.
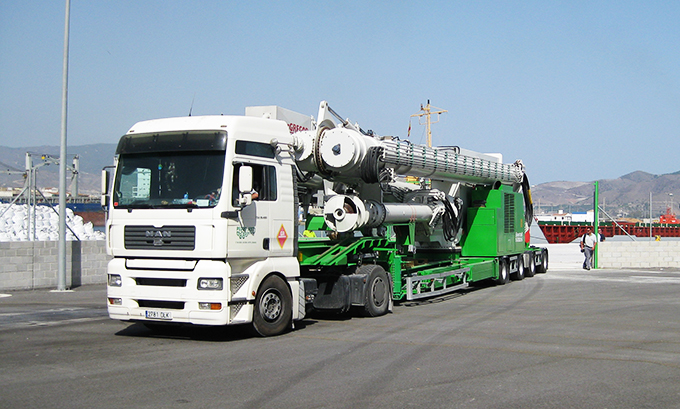
Benefits
- Planned maintenance is significantly cheaper than unplanned, with fixed, predictable costs and administration requirements.
- Work is carried out by expert Siwertell surveyors.
- Web-based, remote access support can be arranged.
- Wear and tear can be attended to effectively and prior to component failure.
- Service labor and spare parts discounts are included.
- Spare parts guidance ensures spares are ordered well ahead of critical replacement dates, which will reduce costs.
- Unplanned downtime is minimized.
- Drive settings can be adjusted in accordance with a machine’s design criteria.
- Equipment performance is improved by ensuring that machine settings are optimal and that the highest possible unloading/loading capacity can be maintained.
- The safety of the unloader is reviewed.
Next-level service
Service agreements with augmented reality (AR) are next-level digital services that complement regular mechanical, hydraulic and electrical inspections and maintenance work on your road mobile unloader.
When AR glasses are purchased as part of these, their additional capabilities mean that our customers can remotely connect with experts, enabling surveyors to see what your maintenance personnel can see. Technical issues can be addressed even more quickly, along with streamlining communications. They can also mean that more complex maintenance tasks can be carried out in-house, and that the cost and frequency of engineer call-outs can be reduced, delivering environmental benefits too.
Cost-saving benefits
Planned service agreements offer significant customer benefits. They ensure peak operational performance, substantial cost savings and budgeting advantages, and minimize equipment downtime.
Response times and our capacity to meet urgent requests for support are also enhanced. We understand that everybody wants an immediate response when equipment experiences an unplanned stoppage.
As part of Service agreements, road-mobile unloader customers have access to regular equipment inspections as standard.
Advantages of Service agreements with augmented reality
- Bruks Siwertell experts can remotely supervise any work being carried out, which can speed up tasks and ensure that they are correctly performed
- Opportunity for evaluations and discussions about operational or performance queries
- Fixed-cost agreement for the number of support hours required per year/period
- Spare parts discount
We work with you. You know your equipment and as original equipment manufacturers (OEM), we know how to help rapidly assess it and determine its condition. This ensures that parts are not replaced unnecessarily and we can advise you on the most cost-effective strategy for repair and renewal. OEM surveyors can also help you to make relatively small adjustments to operational parameters, which deliver significant performance benefits.