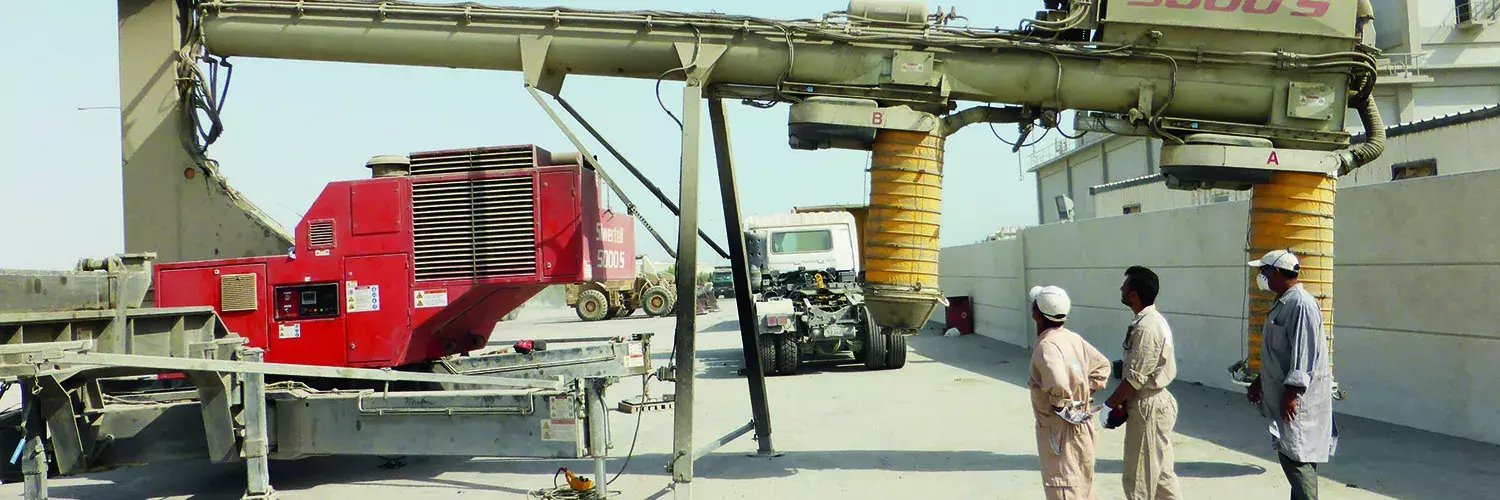
Acico Construction Co Kuwait signed a planned maintenance agreement that delivers operational reliability and maintenance support for the company’s two Siwertell road-mobile unloaders operating in Shuaibah Port, Kuwait.
Planned maintenance
Siwertell’s planned maintenance packages are delivered through its Siwertell CARE agreements. These consist of five modules and three service levels, which flexibly combine to create the ideal service arrangement. “It is understandable that people often think of service agreements only in terms of large, fixed industrial installations,” says Bengt Estberger, Siwertell Manager Mobile Unloaders. “But these agreements are equally important for our road-mobile units.
"In common with all our products, road-mobile units are well designed and constructed and in consequence they are inherently robust and reliable. However, expert attention delivered on a timely, planned basis is the ideal way to ensure maximum uptime, a long service life and good cost control.”
OEMs know their products best
Acico’s 5 000 S and 10 000 S road-mobile unloaders support the company’s large cement production facility in the Shuaibah industrial area. Arundeep Singh Ahluwalia, in charge of maintenance for Acico Cement, said that when the company’s first road-mobile unloader was delivered, his staff had no previous experience of operating or maintaining the machine and he wanted to ensure that it remained in excellent condition.
Just as with cars, he said, the best solution is to have an agreement with the original equipment manufacturer (OEM), because they know their machines better than anyone else. The three-year agreement provides a call-out based service, delivering operational reliability through inspections and supervision work on an as-needed basis. However, Siwertell has suggested a basic time-frame to ensure that inspections take place on a regular basis.
Flexibility ensures optimum service
The CARE agreement includes a rolling training element for Acico's maintenance staff, covering mechanical and electrical systems and instrumentation. "The most important point is that this agreement offers great flexibility,” says Mr Estberger. "Flexibility allows us to fine-tune this tailor-made agreement in a mutually agreed manner.”
Siwertell engineers undertook the first inspection of the 5 000 S model in October 2015 and both machines were inspected during a second visit in March 2016.
Fully satisfied with Siwertell service
Mr Arundeep Singh Ahluwalia says he is fully satisfied with the service delivered by the Siwertell engineers. “Our expectation is that once the service engineer is at our site, he should provide us with a clear plan of the jobs he will be performing. This helps us in scheduling our operations in a better way. Siwertell staff are always helpful and their replies to our queries are clear and concise.”
The road-mobile nature of these units means that – depending on location – it may be convenient for a unit to travel to Siwertell facilities for service work, particularly for any major upgrades or overhauls later in its working life.
“Operators appreciate the benefits of smooth, reliable operations and predictable costs,” says Mr Estberger. “We expect to see more road-mobile operators taking advantage of our service capabilities.”