Wood processing - USA
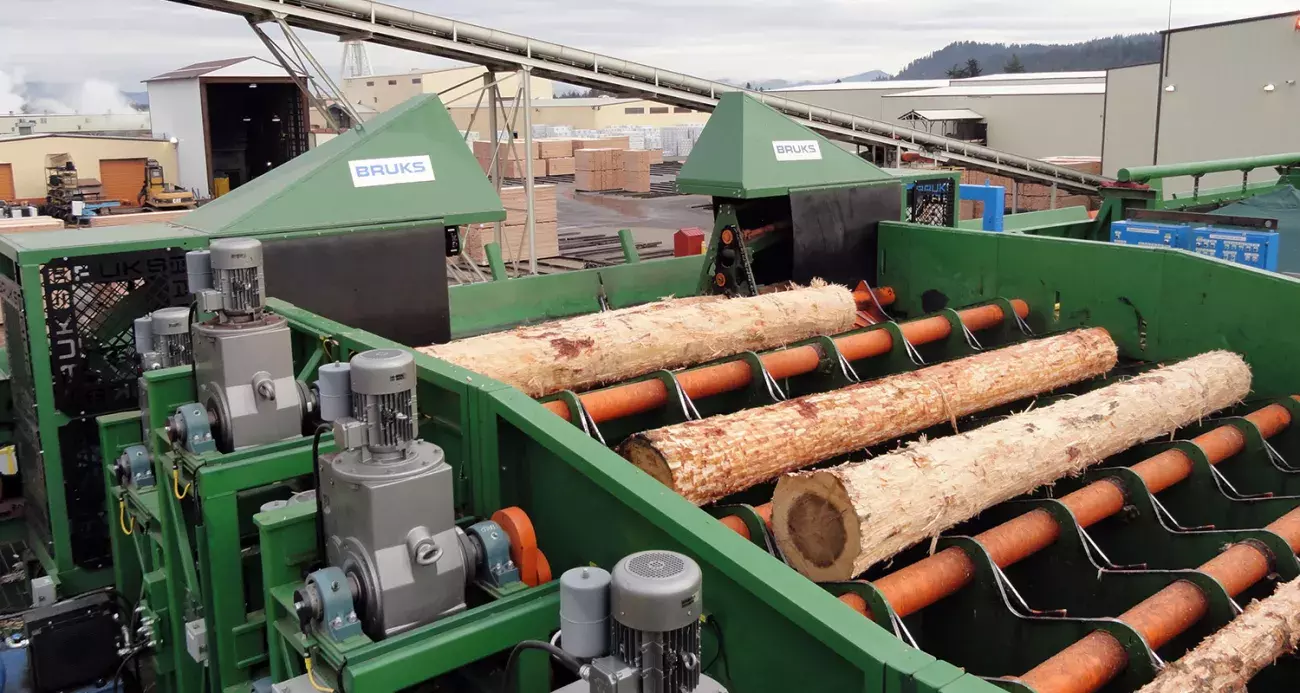
Wood-processing technology boosts sawmill yields in Idaho
Idaho, USA, has around 85,000km² (21million acres) of forest and for every harvested tree in the region, seven more are growing in its place. Forestry is Idaho’s key industry and with multiple active sawmills, reliable wood-processing and handling technology is essential.
Customer need
Around 80 percent of Idaho’s 85,000km² forestlands are owned and managed by the US Government. It is a booming industry and one that places sustainability at its heart. The region’s forestry operators are part of a network overseen by the Idaho Forest Products Commission, set up to ensure the sustainable management of the area’s public and private forests and its wood-processing industries.
The region hosts some of the most automated, advanced sawmills in the world, with its by-products, such as bark, being used as a renewable fuel, and wood chips destined for use by the pulp and paper industry.
A key player is Idaho Forest Group. Its Chilco facility in Athol, north of Coeur d’Alene, stands on a site of around 1km2 (248 acres) and is one of the Group’s most technically advanced facilities, producing up to around 85 million board meters (280 million board feet) of lumber a year.
When it needed new butt-flare reducers for its log line, and a new conveying system for handling cutting by-products, such as wood chips, bark and sawdust, it turned to Bruks Siwertell.
Our solution
During Chilco’s upgrade project, Bruks Siwertell was contracted to supply a range of wood-processing and handling technology including two Bruks butt-flare reducers and its air-supported conveying technology, Tubulator.
Logs arrive at the mill needing machining prior to cutting. Removing the butt-flare of a log yields distinct advantages for sawmills, not only improving handling and positioning of the log, but also the butt-flare reducer removes any debris within the root bones that could damage machinery. Bruks butt-flare reducers automatically machine down any protrusions, without any adjustments needed for different sized logs, processing as many as 30 logs a minute.
The air-supported conveyors were needed to bridge a high, long span from the cutting house to storage. Tubulator conveyors offered three main advantages in this installation: they needed minimal supports because of innovative suspension cable tower technology, so left much of the working yard space free from obstacles; the system is totally enclosed protecting the environment from dust emissions; and air-cushion conveyors remove the need for idlers under the conveyor belt, not only delivering capacity increases, but significantly reducing operating and maintenance costs.
- Wood processing
- Biomass
Customer
Idaho Forest Group
Products
Tubulator type-CT830 conveyors and two Bruks butt-flare reducers
Materials handled
Harvested logs and wood chips, bark and sawdust