Wood processing - Sweden
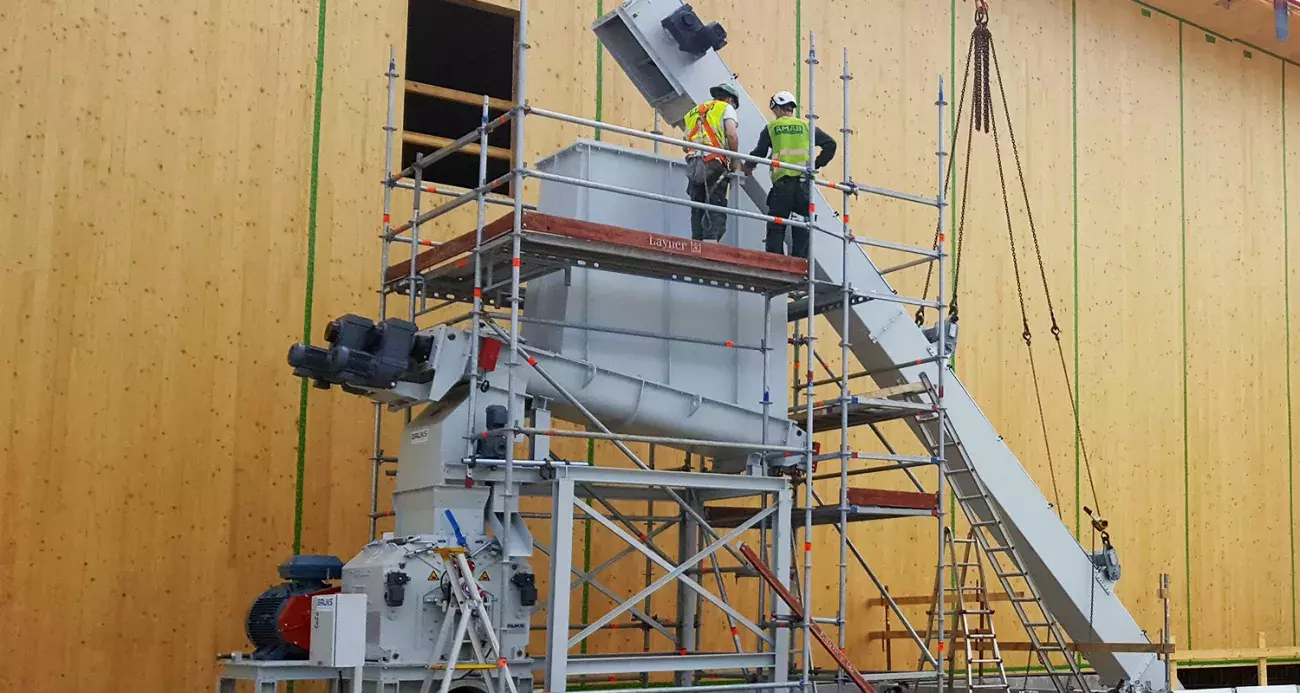
Bruks by-product disposal line underpins Swedish sawmill success
Scandinavian renewable materials company, Stora Enso, knows what to expect from Bruks equipment, having first-hand experience since 1987. When it needed a new by-product disposal line to serve its new production unit, transporting, handling and milling waste wood, it once again turned to Bruks Siwertell.
Customer need
Leading global provider of renewable packaging, biomaterials, wood products and paper, Stora Enso, built a new production unit for cross laminated timber (CLT) at its Gruvön sawmill in western Sweden.
Raw material for the sawmill includes pine and spruce logs, which are locally sourced from the company’s significant land resources. With an annual capacity of around 370,000m³ of sawn timber, 150,000m³ of processed timber, 100,000 metric tons of pellets, and made-to-order wood products for the construction industry, the mill is one of the company’s most advanced production facilities.
Activities at the plant naturally produce waste by-products, and to make the best use of them in line with the company’s sustainability approach, the sawmill needed a by-product disposal line to support the new production unit. It also needed any new equipment to fit into a tight footprint. Furthermore, installation work had to be carried out alongside other contractors working at the site to ensure that specific timeframes for related components were met and that overall operational deadlines came in on time.
Our Solution
In 2018, Bruks Siwertell delivered and installed a by-product disposal line to transport and handle the mill’s production of by-products. Components include a high-capacity 110kW hammer mill, with the capability of processing up to 3t/h of waste wood, a cleaner system and a magnetic drum, to remove scrap ferrous material. Screw conveyors and over 200m of belt conveyors were also delivered. Prior to entering service, operator training was received including practical sessions on-site.
“The cooperation during the conception and planning phases was very productive and solution-oriented,” says David Rameder, Technical Project Manager, Stora Enso. “In case of adjustments, there was always a quick reaction with a solution. Thanks to the prefabricated machine elements, assembly could be carried out quickly despite the limited space available. The high availability of the equipment allows us to guarantee a trouble-free transport of residual wood.”
Stora Enso is a long-term customer, with its first Bruks Klöckner delivery in 1987. Other Bruks equipment includes drum chippers, chain conveyors, belt conveyors, and hammer mills. Stora Enso knows what to expect, high availability, maintenance-friendly, and good service and support.
- Wood processing
Customer
Stora Enso Timber AB
Product
Wood processing machines³
Model
Hammermill