Conveying - USA
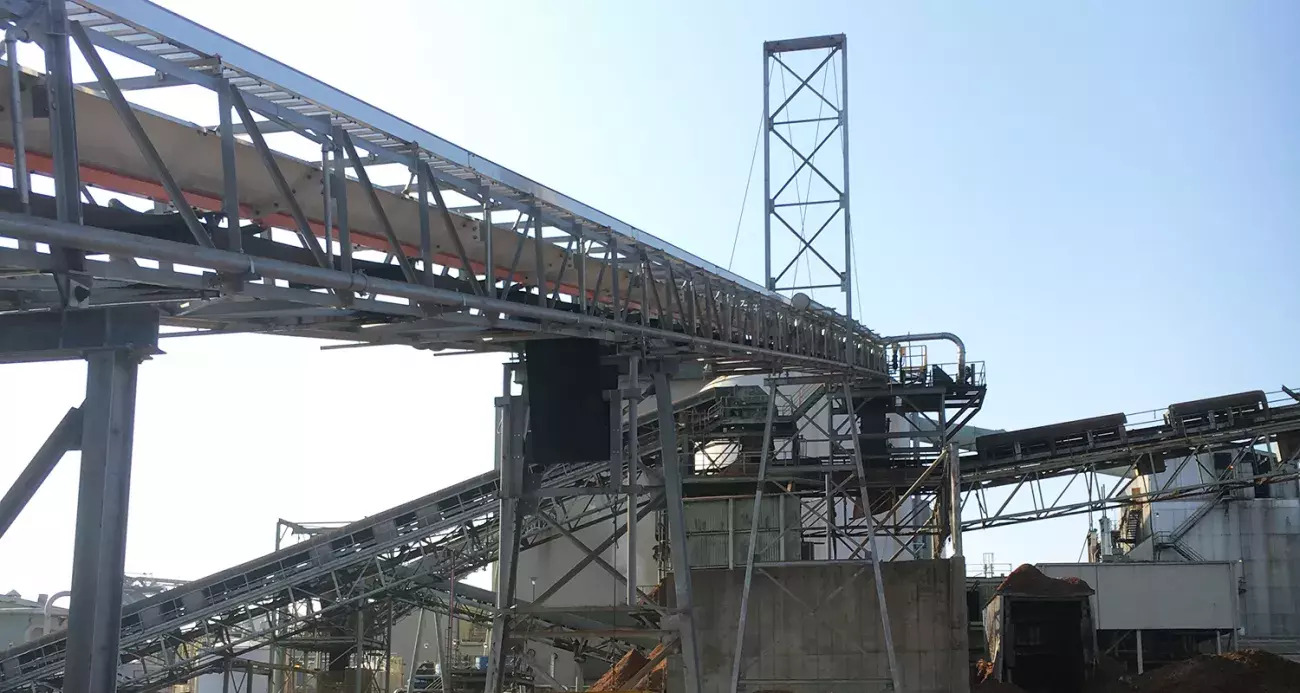
Low-friction conveying reduces US mill's operating costs
An air-cushioned conveyor installation at a high-volume mill in the USA, was delivered as part of a new log-line to increase capacity and reduce operating and maintenance costs at the containerboard plant. It offers the very efficient handling of processed wood.
Customer need
The US-based, high-volume containerboard plant uses processed wood, including bark and wood chips, in the production of paper and lightweight linerboard.
As part of a plan to increase the capacity at the plant, the operator was looking for an innovative approach to its new log-line conveyors.
Although flexible and efficient, the main area of concern with conventional conveyors is idlers; the unpowered rollers underneath a conveyor belt which support the weight of the belt and material as it goes along. Unless well maintained, the risk of friction fires, caused by idler cans seizing up, is significant. The operator was hoping for a solution that would eliminate this risk and also greatly reduce maintenance operating costs.
It also needed a conveyor system that was enclosed, to protect the environment from dust emissions, and one that could handle three different types of processed wood material, hogged and unhogged bark and wood chips.
Our solution
Bruks Siwertell offered a solution that would be the first-of-its-kind, and early feedback is very positive. It delivered a new type of conveyor, The Belt Conveyor, which combines the use of air-cushion technology with a standard Bruks belt conveyor, ensuring low friction, high capacity conveying that offers minimal equipment wear and very low operating costs.
The new fully-enclosed conveying system was delivered in 2019 and comprises a 1.4m (54in) wide x 122m (400ft) long conveyor for handling wood chips at 550t/h; and two further conveyor units, one 1.0m (36in) wide x 39.6m (130ft) long and one 1.0m (36in) wide x 91.4m (300ft) long, for handling hogged and unhogged bark at a rate of 60t/h.
In addition to eliminating the use of idler cans and therefore the fire risk, The Belt Conveyor offers a smoother ride for materials. The belt glides on a cushion of air which is generated by a pressurized air-enclosure system underneath the belt. With a rolled plate that matches the profile of a 35-degree idler cross-section, each 3m section of the belt has access to a common header of pressurized air.
- Conveying
- Biomass
Customer
Undisclosed
Product
Air-supported conveyors
Model
The Belt Conveyor
Supplied sizes
Three The Belt Conveyor: one 1.4m (54inc) wide x 122m (400ft) long; one 1.0 (36in) wide x 39.6m (130ft) long; and one 1.0m (36in) wide x 91.4m (300ft) long
Material handled
Wood chips at a rate of 550t/h and hogged and unhogged bark at a rate of 60t/h