Ship loader - Ireland
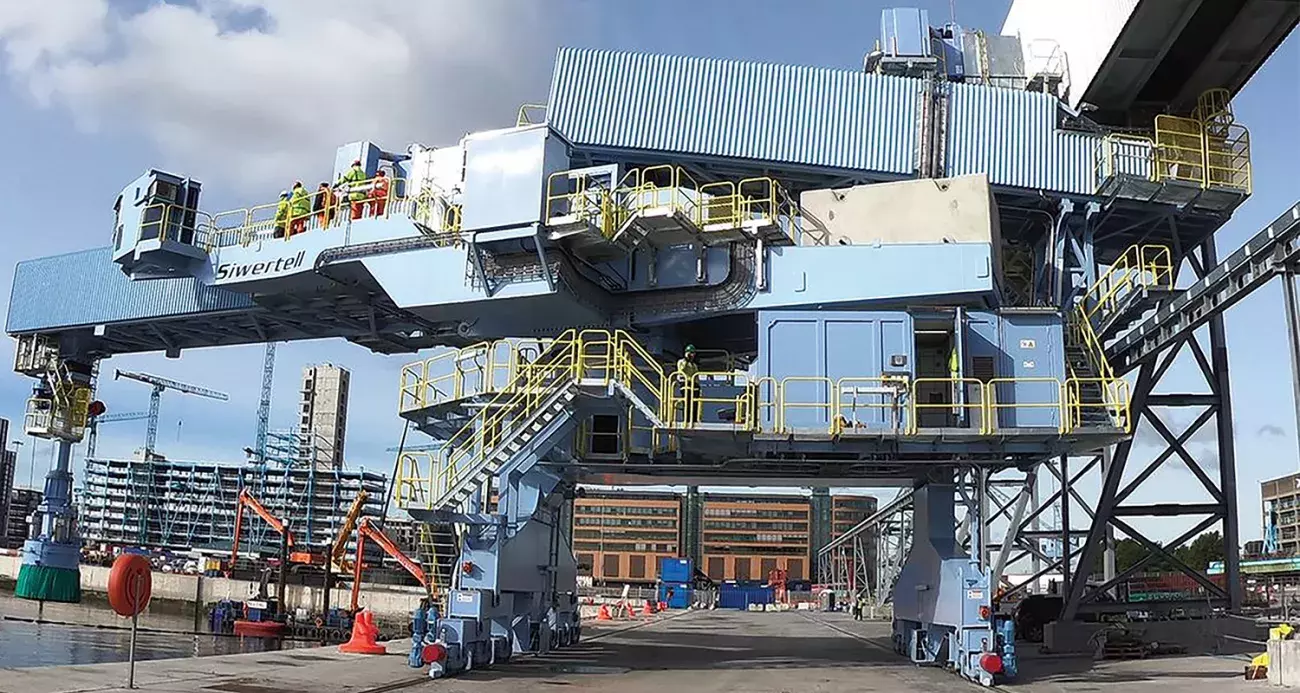
Loading innovation delivers absolute environmental protection
Swedish company, Boliden, is gradually automating its mining facilities and driving advances in environmental protection, safety and production. As part of this, its Boliden Tara Mines facility in Ireland features Bruks Siwertell’s first fully automatic loader and conveyor coupling technology with enhanced environmental protection measures.
Customer need
Around 2.6 million metric tons of ore is mined annually for the production of zinc and lead concentrates at Europe’s largest zinc mine, Boliden Tara Mines, Ireland. The 1,000m-deep facility has been in production since 1977 and was acquired by Boliden AB in 2004.
In 2018, the mine processed 2,200 kilotons of ore into metal concentrates containing zinc, lead and silver. In the same year, Boliden approached Bruks Siwertell for its expertise in developing a unique material handling system for the company’s new terminal in Dublin’s Alexandra Basin. A number of key prerequisites for any system had to be met, including architectural restrictions.
The installation is located near a popular docklands area and cruise ship port. Low noise requirements and very high environmental standards were required, with close-to-zero dust emissions stipulated in the contract.
Zinc and lead are extremely hazardous to the environment and humans; any system had to limit physical contact with the materials. A high loading capacity, combined with easy system operation and low service and maintenance costs, were also significant factors for the company, along with the ability to comply with best available technology (BAT) and reference document (BREF) regulations.
Our solution
Working together, Bruks Siwertell developed a totally new system. It comprises a triple-enclosed belt-type ship loader, with luffing and slewing capabilities, a reversible shuttle-belt conveyor, with double-embedded covers, and dual remotely-operated connection points, as well as a triple-enclosed jetty and overland conveyor. The conveyor and its walkways are also embedded.
For the dust extraction system, which was tailor-made for the application, a new two-stage filtration process was developed, with special high-particulate air (HEPA) filters forming the final stage of the process. The clean air released to the atmosphere from this filtration process contains no measurable particles.
Lead and zinc are very sticky, requiring specialist machinery to handle them. To prevent ore build-up, the loader features different angles and rounded corners. A stainless-steel base plate, with low friction liners together with vibrators and heating elements, also keep the material flowing.
The zinc and lead concentrates are transferred from the mine in rail wagons to a receiving storage warehouse. From here, a conveyor belt leads to the new quayside facility. Siwertell units are well-suited to sticky and hard-to-handle materials and the new system is capable of loading ships of up to 10,000 dwt at a continuous rated capacity of 600t/h.
Boliden also has a spare parts package and a two-year planned service agreement in place.
For more information, please contact us
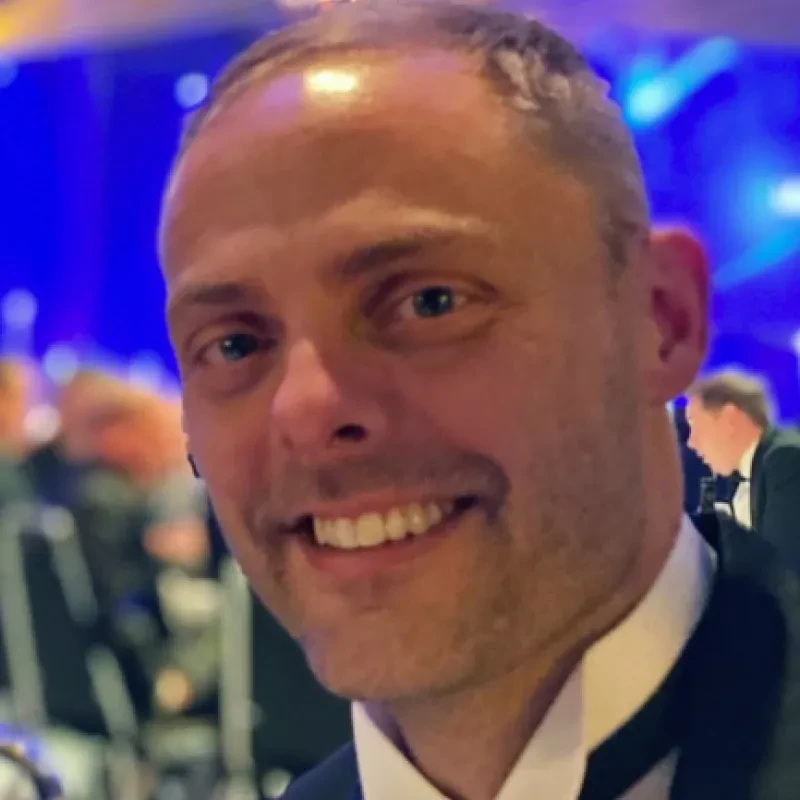
- Ship loading
- Other
Customer
Boliden Tara Mines, DAC
Additional facts
Loader modell
Siwertell 800 1A
Loading capacity
600t/h
Maximum ship size
10,000 dwt
Total weight
250t
Material handled
Lead/Zink concentrate