Conveying - USA
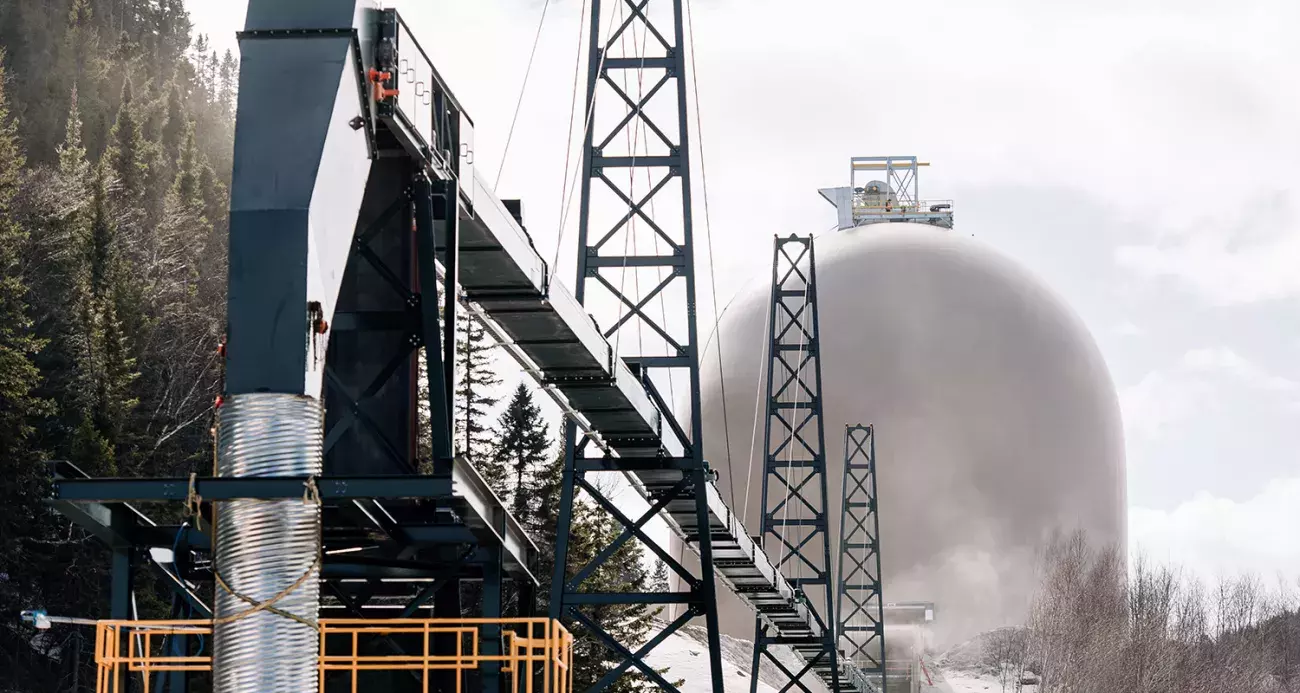
Air-cushion conveyors ensure efficient, dust-free pellet handling
Integral to operations at Barrette-Chapais’ pellet production plant, Granule 777, in Quebec, Canada, is a new air-supported conveyor system from Bruks Siwertell. It combines the use of two types of low-friction conveyors, The Belt Conveyor and the Tubulator, offering highly efficient, dust-free pellet transfer.
Customer need
Barrette-Chapais was looking to implement extraordinary levels of efficiency and environmental protection at its new 210,000 metric tons/year wood pellet production plant, Granule 777. Here, offcuts and residuals from Canada’s sawmills, which would have been regarded as a waste product as little as a decade ago, are being converted into usable biomass pellets which can offset the use of fossil fuels at power stations.
Granule 777 required a conveyor system to carry processed wood pellets from the facility’s two pellet storage domes and to the dock where the pellets are loaded onto bulk carriers bound for Europe. The conveyors needed to span a considerable distance over difficult terrain. The plant also needed an enclosed system to protect the environment from dust emissions and the pellets from external moisture.
Crucially, Barrette-Chapais also needed to ensure the quality of its pellets. Transporting biomass pellets over long distances can be difficult without causing material degradation. The consistent quality of biomass fuel is essential for destination boilers, as degraded pellets do not burn evenly and reduce the efficiency of the combustion process.
Our solution
Bruks Siwertell’s enclosed air-supported conveyor systems were seen as a very effective option. With a rated capacity of 800t/h for carrying wood pellets, the conveyor system comprises a 100m-long The Belt Conveyor and a 250m-long Tubulator. The Belt Conveyor carries material from the facility’s pellet storage domes, before transferring it to the Tubulator that feeds the pellets to the dock.
The Belt Conveyor shares the geometry of a 35-degree idler conveyor, but combines the use of pressurized air with standard Bruks belt conveyors. This removes idlers from under the belt and delivers low-friction, high-capacity conveying with minimal equipment wear and very low operating costs. As for the Tubulator, it also uses air support to deliver low-friction conveying, achieving capacities up to 40 percent higher than conventional belt conveyors.
To create the air cushion, The Belt Conveyor uses a header of pressurized air for each 3m section and the Tubulator uses a series of low-pressure fans. The Tubulator also uses innovative suspension cable tower technology. For Granule 777, long spans were easily managed and only three cable tower supports were used over the entire length.
- Conveying
- Biomass
Customer
Barrette-Chapais, Granule 777
Additional facts
Product
Air-supported conveyors
Model
The Belt Conveyor and The Tubulator
Supplied lengths
One 100m-long Belt conveyor and one 250m-long Tubulator
Material handled
Wood pellets