Conveying - Sweden
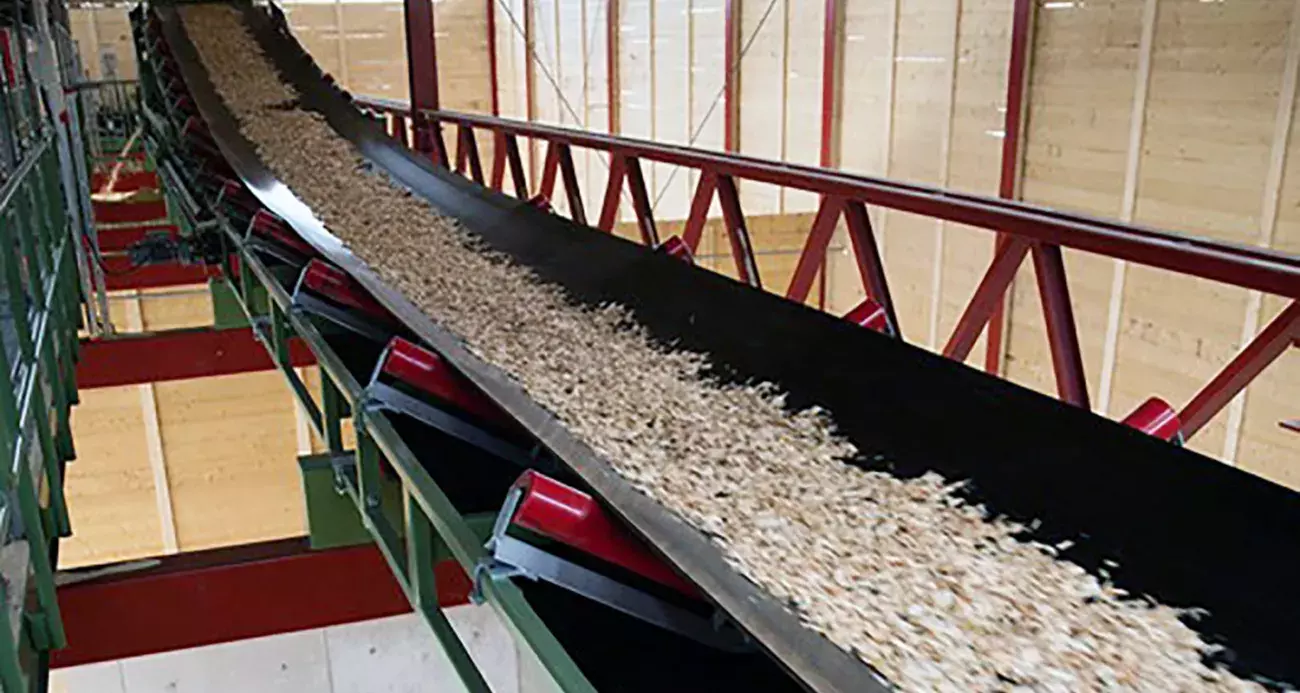
Dust-free waste wood residue handling under Tunadal sawline
Swedish forestry, processed wood and renewable energy company, SCA, has invested more than SEK 1 billion in its Tunadal sawmill over the last decade, increasing production capacity and processing capabilities, and environmental improvements. Part of this development was a new by-product processing and handling system.
Customer need
SCA’s business is focused around 2.6 million hectares of slow-grown Nordic pine and spruce forests in northern Sweden, with expansion into eastern Europe. Renewable raw material is at the heart of the company’s portfolio of packaging, print and pulp wood products.
SCA is also one of Sweden’s largest biomass pellet manufacturers, predominantly using wood residues from its own sawmills, including the sawdust from its Tunadal facility, in Sundsvall, Sweden. Other by-products from the mill are fed into SCA’s diverse processed-wood operations.
Ensuring that nothing is wasted at any point in wood-processing supply chains is essential to the environment and is also commercially valuable. As part of this strategy, SCA needed a by-product processing and handling system that could collect waste wood resides, namely wood chips and sawdust, from beneath its new sawline at Tunadal, and also ensure a dust-free environment.
The sawline replaces three older ones at the facility and in combination with other developments, makes Tunadal one of the largest, most advanced sawmills in Sweden. Production is growing, with the company looking to expand capacity to a maximum of 900,000m3 of solid-wood products per year.
Our solution
The sawmill’s operations are supported with a by-product processing and handling system from Bruks Siwertell. The entire solution is based upon Bruks Siwertell’s lengthy experience of this type of plant and was developed in close cooperation with SCA. Several proposals were developed during the consultation process, with the final one chosen as the most suitable and cost-effective for its needs.
Contracted at the end of 2014 and installed in 2016, the complete delivery includes two 120m-long air-supported, low-friction Tubulator conveying systems, type CT1000SL and CT800SL. They form the sub-floor beneath the sawline, where enclosed separate plate chutes transfer wood chips and sawdust directly onto their corresponding conveyor.
One Tubulator transports sawdust at a rated capacity of 600 m3/h and the other wood chips at 1,000 m3/h. Wood chips are transferred, via a screw conveyor, to a screening system, prior to storage, which sorts material into four fractions: oversized, acceptable-sized wood chips, sawdust and pin chips. Oversized chips are processed in a Bruks drop-fed drum chipper. Larger offcuts are processed by a second Bruks drum chipper and also fed into the screening system via a Tubulator type-CT518 conveyor, prior to storage.
- Conveying
- Biomass
Customer
SCA Wood AB
Product
By-product processing and handling system including a Bruks drum chipper and Tubulator type-CT1000SL and CT800SL conveyors; vibratory conveyor, handling offcuts from the green sorter, a Bruks drum chipper and a Tubulator type-CT518 conveyor
Materials handled
Sawdust at a rated capacity of 600 m3/h and wood chips at 1,000 m3/h