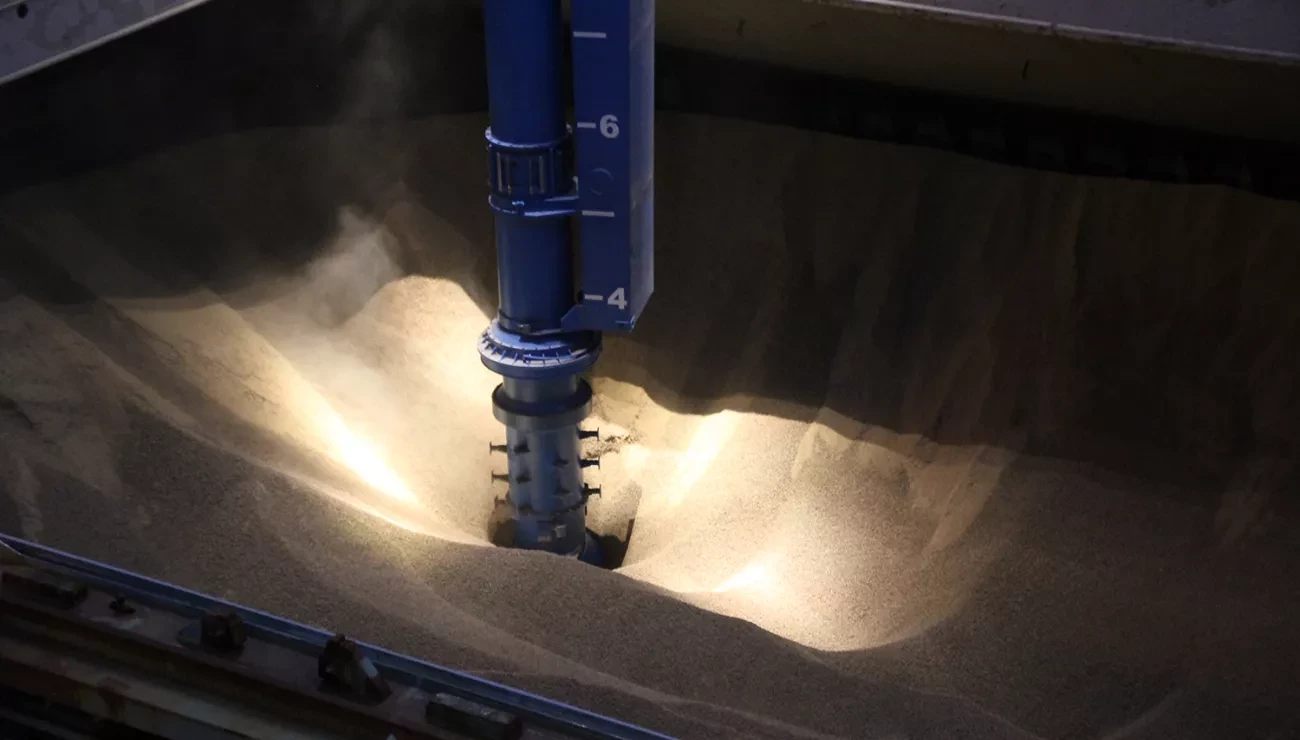
Sustainable supply chains: from pellet to power
7 Dec 2020Although slower in some corners, the world is searching to find the best solution for sustainable energy production and shifting its focus away from fossil fuels. While a carbon-neutral or even negative profile is the ultimate aim, many power plants are adapting to burning renewable fuel sources, such as biomass, to offset their carbon footprint. Some are going a step further and also employing carbon capture.
Biomass makes great use of forestry and agricultural by-products and waste, and adds value and sustainability along supply chains. When supplied as high-quality pellets, it also offers generators a consistent burn profile, making it a desirable fuel. For power production, however, vast volumes are required, so efficient, high-capacity unloaders, loaders, conveyors and storage and reclaiming systems are an absolute necessity.
Bruks Siwertell supports renewable energy production. Our equipment ensures that all types of wood are handled and processed carefully and efficiently, including the sustainable harvest of timber from forests to the processing of wood residues into pellets and beyond into their handling during import, export and storage.
US pellet production to UK power
These are global journeys; pellets produced on one continent are transported for use on others. For example, the UK-based Drax power station in Yorkshire uses millions of metric tons of imported biomass every year to generate electricity. Drax is actually the largest generator of renewable power in the UK, with a target to be carbon negative by 2030.
A significant proportion of the pellets used by this UK power station are produced by Drax Biomass’ facilities in the US; one in Bastrop, Louisiana, one in Urania, Louisiana, and one in Gloster, Mississippi.
Headquartered in Monroe, Louisiana, Drax Biomass prides itself on the production of pellets from sustainably managed working forests. It is no stranger to Bruks Siwertell, and material processing and handling equipment for the company covers ship loading, wood yards, truck receiving, conveying, and screening, sizing and storage equipment.
One example installation is at Drax’s Amite BioEnergy plant located in Gloster, southwestern Mississippi. It helps to produce up to 525,000 metric tons of biomass pellets annually and was commissioned in August 2015.
The totally-enclosed Bruks Siwertell dry shavings receiving system ensures material flow consistency and protection from any external moisture. This is particularly beneficial to all pellet plants as it delivers a material stream that can bypass the ‘bottleneck’ of the plant – the dryer. Ultimately it means that plants can expand their pellet-making capabilities without having to upgrade their dryers.
A Trans-Atlantic crossing
Once the biomass is in pellet form, it is transferred, via rail, to Drax Biomass’ US east coast Baton Rouge port facility in Louisiana. Here, a Bruks ship loader efficiently and carefully loads the holds of vessels up to 50,000 dwt for transport across the Atlantic to the Drax power station in the UK.
The pellets arrive at two separate port terminal locations in the UK, both are served by Siwertell multi-fuel screw-type ship unloaders.
Two rail-mounted ST 790-D-type units are used for unloading the imported biomass pellets at Associated British Ports’ (ABP) Immingham Renewable Fuels Terminal (IRFT) on the north-east coast. At full capacity the terminal can handle about six million metric tons of biomass per annum. It may also be called on to handle coal. When the terminal is at full capacity, the unloaders are in almost constant operation.
ABP opted for Siwertell unloaders because it needed a clean, safe, efficient, high-capacity system, able to handle both biomass and coal. Minimal cargo degradation was also an important requirement, because the combustion process is adversely affected by the powdery fines content of the pellets.
The unloaders each have a rated capacity of 1,200t/h, handling the biomass pellets arriving from the US in dedicated self-trimming bulk vessels of between 25,000 and 50,000 dwt.
Drax power station is also served by two further Siwertell ST 790-D-type multi-fuel ship unloaders operated by Ligna Biomass Ltd, part of the Peel Ports Group, in Liverpool, UK. The Ligna Biomass terminal can store up to 110,000 metric tons of biomass and handles up to three million metric tons of wood pellets a year for Drax.
These unloaders also have rated capacities of 1,200t/h, supplying the power station with up to ten train loads of pellets per day. This accounts for up to 40 percent of the total biomass consumed by Drax each year.
Once in Drax power station itself, Bruks silos, with mechanical screw reclaimers, are used for storing the pellets, and then delivering them to the boiler.
End-to-end solutions
Siwertell unloaders have long-served the biomass industry, with high-capacity unloading installations securing pellet fuel supplies to power-generation facilities globally. Meanwhile, Bruks products have been closely connected with the growing North American timber trade for more than 30 years. Today there are Bruks installations all over the continent dedicated to unloading, processing and transporting wood products like bark, wood chips and sawdust.
So, when it comes to the biomass industry, Bruks Siwertell’s knowledge and value proposition is unmatched in the rest of the market. Drax’s story is a great example of this, showcasing how our broad equipment portfolio offers products that reflect all phases of a supply chain, making it possible to offer true end-to-end solutions to operators.
The video is showing a full chain of products installed by Bruks Siwertell, from tree harvesting in the US to energy production in the UK.
PLEASE CONTACT US FOR MORE INFORMATION
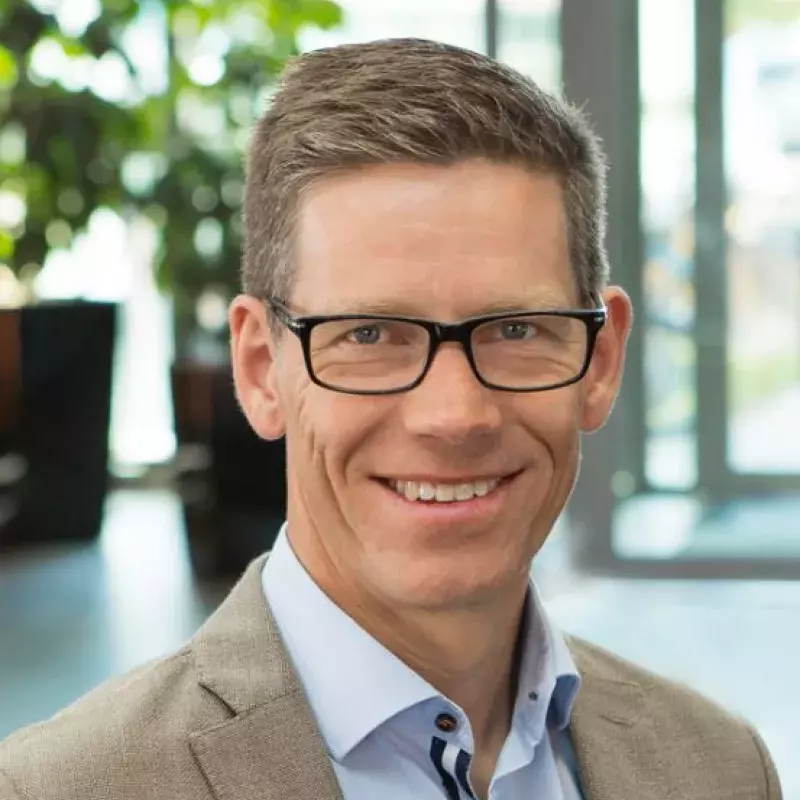