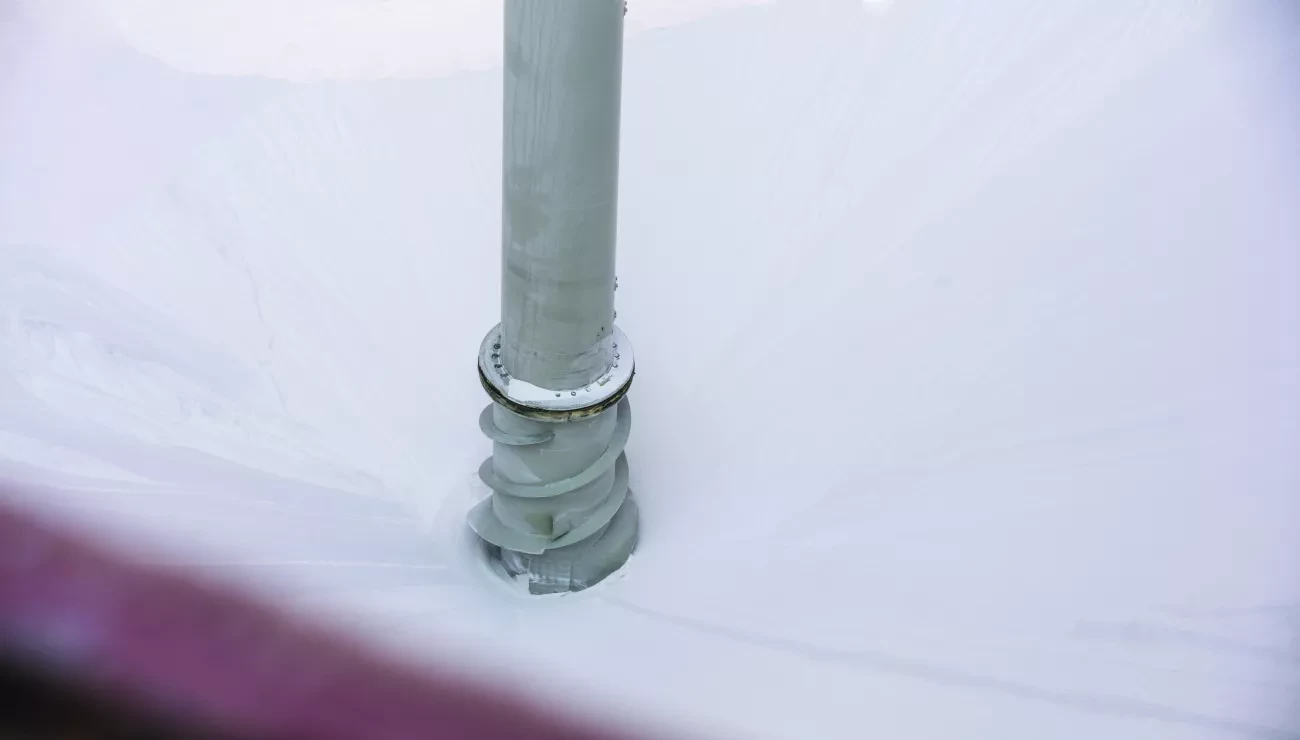
Shipment quality underpins alumina trade
1 Jul 2024What do a phone, a plasma television, a lithium-ion battery, and a light-emitting diode (LED) have in common? They all rely on the purest form of alumina to make synthetic sapphire. Essentially, alumina underpins the development of modern technology and its growth.
Global trade in alumina is booming. According to leading strategic market insight company, Precedence Research, the global alumina market size stood at around USD 41 billion in 2022, with around half of that attributed to the Asia Pacific (APAC) market. By the end of 2032, the global alumina market is anticipated to reach around USD 64.59 billion, with the compound growth rate predicted at 4.7 percent during the forecast period 2023 to 2032.
The global drivers behind the dynamic trade in this white crystalline material, aluminum oxide, are many, particularly as there are so many end products that rely on its supply. From the usual domestic and industrial demands including sheet aluminum to food packaging to the less obvious, but critical, semiconductors, lithium-ion batteries, and LEDs, which all require the highest purity alumina.
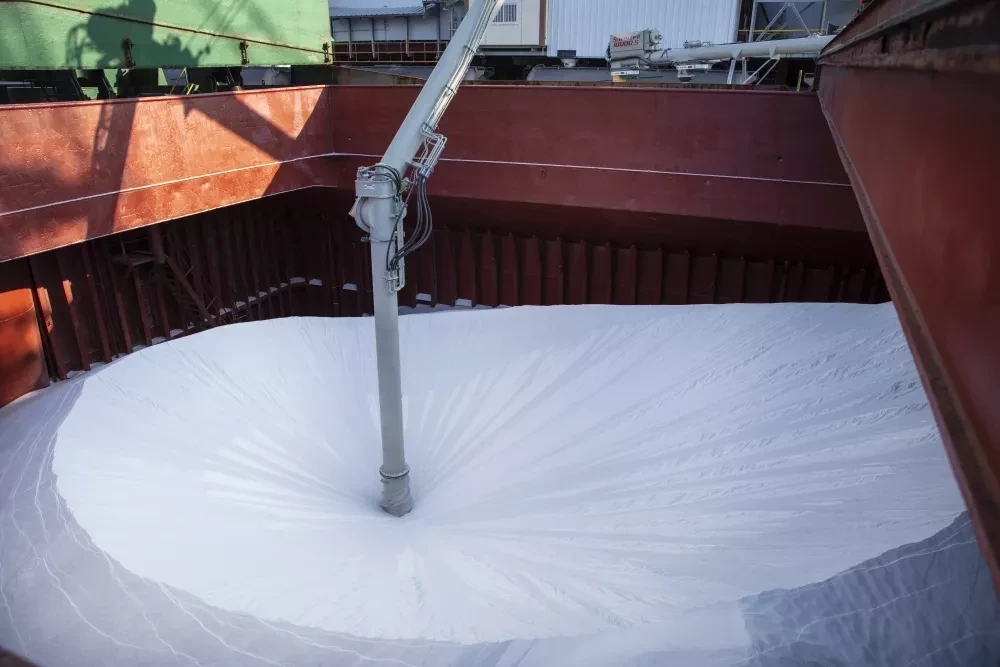
No substitutes available
High-purity alumina (HPA) stands at a minimum purity of 99.99 percent, otherwise known as 4N HPA, rising to purities of 5N and 6N. This purity means that it can manufacture the much sought-after material, synthetic sapphire. Currently, there is no substitute for HPA in the manufacture of synthetic sapphire.
The global trade in 4N HPA runs at a different pace. With Global Market Insights estimating the HPA market predicted to grow at a compound growth rate of over 13 percent through to 2032 and its value standing at over USD 1.7 billion in 2022.
In the context of the increasingly digitized world, it is no surprise that this specific alumina trade is almost treble that of bulk alumina in general, and with there being no other raw material alternatives to synthetic sapphire on the horizon, the global trade in alumina shows no signs of slowing.
Too expensive to waste
So where does Bruks Siwertell fit into this picture? Firstly, fines should be considered, the tiny particles created by degraded materials. Alumina processing is incredibly sensitive to the level of fines in a shipment. Secondly, spillage needs to be scrutinized. All forms of alumina are very expensive, and the higher the level of purity, the higher the cost, no part of a bulk alumina shipment should be wasted through spillage.
If these two elements alone are considered, Bruks Siwertell has estimated that it could save the bulk alumina industry a fortune if it switched to Siwertell ship unloading technology. These savings are applicable if switching from both pneumatics and grab cranes. This is because Siwertell technology addresses the two main points of material degradation and spillage.
Let us look at them in more detail, starting with grab cranes. Because alumina is a high-value dry bulk material, spillage associated with this traditional unloading method costs the industry millions of dollars every year.
Our customers report that, depending on the type of grab crane used for unloading, one to three percent of the entire shipment can be lost during the discharge process from spillage. In contrast, independently-observed tests with Siwertell ship unloaders showed no loss of bulk material. This is because Siwertell ship unloaders offer a totally enclosed conveying line, from the ships’ hold through to the jetty conveying system or awaiting bulk trucks. This ensures no spillage and minimal dust emissions.
Preserving particle sizes
Pneumatics are enclosed, so do not incur spillage, however, they are associated with much higher levels of material degradation, with the ensuing production of powdery fines.
Any reduction in fines throughout the industry has a huge impact on downstream processing of alumina, including the extraction of aluminum from its oxide during the energy-intense process of smelting. The lower the percentage of fines, the lower the temperature required in the smelting process, which dramatically reduces a smelting plant’s energy consumption. Bruks Siwertell estimates that minimizing cargo degradation by using Siwertell screw-type unloaders across the industry would see annual savings into the hundreds of millions of dollars.
Feedback from a Siwertell ship unloader customer, comparing its experience with a pneumatic unloader and a Siwertell unloader, notes that alumina discharged with its pneumatic unloader had a fines content, with a particle size of less than 45 µm, of up to five percent. Its Siwertell unloader consistently returns average fines values of between 0.2 and 0.3 percent.
This extremely low fines level is the direct result of smooth material flows within the screw conveying system. There are no major forces acting on the particles, which means that they are drawn up from the ship into the conveying system with minimal disturbance and therefore are exposed to minimal particle collisions. This preserves the shipment quality.
Operators already benefiting
Bruks Siwertell has numerous global ship loader references for handling alumina including serving Hydro Alunorte alumina refinery located in the city of Barcarena, state of Pará, Brazil. It is the world’s largest outside China. Bulk alumina is handled by a Siwertell A1800 1 aeroslide ship loader fitted with a cascade chute, loading vessels at a rated capacity of 2,500t/h.
Ship unloading references include a Siwertell 10 000 S next-generation road-mobile unloader for Trímet France, part of Germany-headquartered, Trimet Aluminum SE. It serves the company’s alumina import facilities in France’s largest port, Marseille, which had an intake of around 50,000 metric tons of alumina in 2022.
The road-mobile ship unloader was commissioned in 2021 and discharges shipments of alumina to silos, ready to be sent in rail wagons to a long-established aluminum-producing factory in Saint-Jean-de-Maurienne, south-east France.
At the time of commissioning, a spokesperson for Trímet France noted that: “One of the biggest challenges for us has been to reduce the time that a vessel stays at the berth. The faster vessels can be turned around the higher the utilization rate of the jetty, delivering better profitability for the terminal.”
Trímet France’s road-mobile unloader has a designed rated capacity of 130t/h for discharging vessels up to 10,000 dwt. It also features advanced digital capabilities and is fitted with the Industrial Internet of Things (IIoT) device, CompuLab, which provides customers with remote access to extensive monitoring, follow-up support, diagnostics and troubleshooting.
Cost-driven markets
Trímet France leased an older Siwertell road-mobile system prior to it ordering its own. This speaks positively about the direct benefits that this technology offered one operator. Beyond this, road-mobile systems enable operators to respond dynamically to a market that is heavily cost driven, moving between ports located close to customers and offering discharging options dependent on market drivers.
Siwertell technology offers distinct advantages to the global alumina industry as a whole. Prerequisites for commercial success are proving to be heavily intertwined with managing rising energy costs and environmental impact.
Screw-type ship loaders and unloaders are very cost-effective options for alumina operators looking to tackle both of these issues with a single approach. Their gentle cargo handling, no spillage, and minimal dust emissions, together with market-leading through ship efficiencies, may just prove to be the solution that the alumina industry needs for a sustainable future.
PLEASE CONTACT US FOR MORE INFORMATION
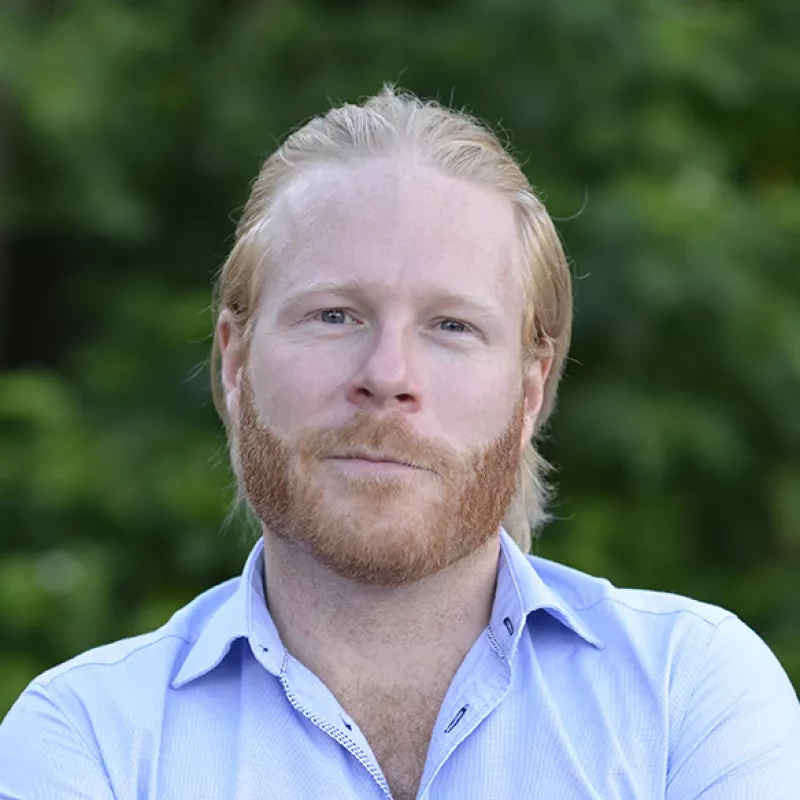