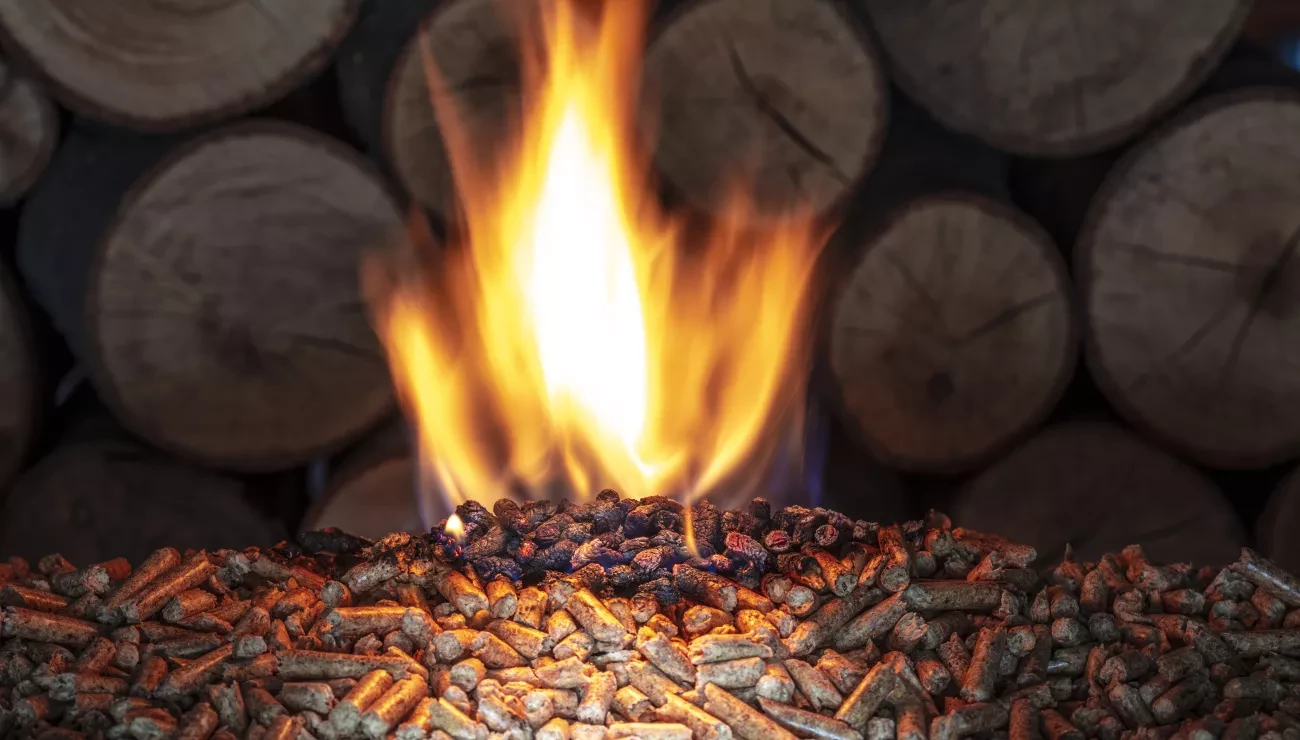
Roll away fire risks with air-cushion conveying
8 Apr 2024Operators understand the importance of maintenance, but the responsibility for thousands of rollers beneath the conveyor belt is quite a task; eliminating them can reduce maintenance burdens and the risk of friction fires, explains Zack Hood, Manager Conveyor Projects, Bruks Siwertell.
Vast volumes of dry bulk materials are conveyed on traditional roller or idler-can belt conveyors. They are robust, extremely efficient, offer high capacities and are generally very reliable, quickly transferring dense and abrasive bulks, across long distances in demanding conditions.
Bruks Siwertell offers many types of these conveyors. However, they have one major requirement, that of maintenance. The belt itself requires regular inspection, and then all the idlers beneath it have to be properly greased and serviced to ensure that they do not seize up, or the phenomenon known as a friction fire is a real possibility.
Prioritizing fire prevention
With large facilities having tens to hundreds of thousands of idlers in action, and vast lengths of rubberized belts, the task and cost of maintaining these systems becomes evident. Add to this, the volatile and innately combustible nature of some dry bulk materials, for example, grain, sulfur and biomass, including the rubberized belt, and the enormity of the fire risk is revealed.
For example, in the UK, a fire in a biomass-handling power station in 2012 was found to have been started on a conveyor belt operating within a pellet storage dome. Although fairly contained and power-generation resumed relatively quickly, incidents like these, and there are many, some with devastating consequences, are cause for significant concern.
While there are situations like jetty conveying systems in ports that serve large-scale ship unloaders and loaders, where traditional belt conveyors are often the main choice, there are now many opportunities for operators to switch to alternative conveying technology, particularly well-suited for the transfer of dry bulk materials within facilities.
Bruks Siwertell offers these conveying systems as well, which pose a much lower fire risk, and offer far reduced maintenance costs. These include highly efficient, low-friction air-cushion conveying systems that eliminate roller and idlers all together, namely the Tubulator™ and The Belt Conveyor™.
As neither of these air-supported systems use idlers along their conveyor lengths, the risk of friction fires from rollers jamming whilst in operation has been eliminated, along with the need for maintenance walkways and the huge associated costs of idler maintenance.
Perfect for biomass
Other advantages are that they are enclosed, so prevent fugitive dust emissions from impacting the environment, as well as keeping the product dry, which is important for many dry bulk materials, such as biomass pellets.
Air-supported conveyors also ensure the quality of the material in terms of degradation. The belts on traditional conveyors are supported by the rollers beneath them, but, as they are spaced at around 1.2m apart, the belt sags a little in the middle, causing a series of fractional bumps to the cargo as it travels along. The interference is minor, but over long distances, cargo, which is particularly sensitive, such as biomass pellets, can break down and degrade.
There is no such degradation on air-supported conveyors. The current climate emergency demands that no raw material should be wasted, and given the rise in demand for biomass, it is imperative that industries have access to conveying systems that not only address the risk of fire, but also that of degradation. In fact, the higher the levels of material degradation, the higher the chance of fire, so overcoming both of these is a win-win.
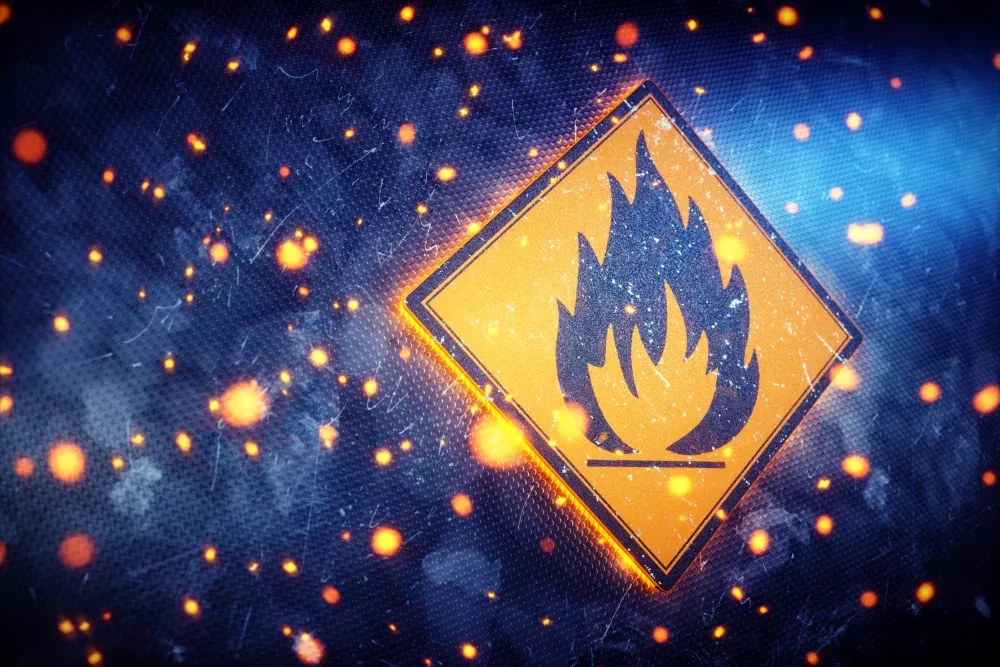
Air under the belt
In terms of their designs, the Tubulator and The Belt Conveyor offer something different. The Tubulator is an air-supported belt conveyor, built as a closed system of steel tubes. Inside the tube, a rubber belt runs at high speed on top of an air cushion created by a series of in-line fans. With less inertia and friction to overcome, the Tubulator can reach angles that would not be possible using traditional idler conveyors.
It can very effectively handle almost any low-density material, such as cement, shredded waste, grain, and sugar. Because it uses a cushion of air instead of idlers, there is no product degradation. Fragile materials are transported more easily and gently, creating less dust in the process. If any dust is generated, Tubulator conveyors are totally enclosed so emissions do not become an environmental or safety hazard; a key benefit for ports handling potentially explosive dusts.
Tubulator systems are sectioned into 12m-long pipes, designed to fit into a 40ft standard shipping container. Because of their structural integrity and low weight, they can be installed over existing equipment. Conveyors are self-supporting up to 25m, and have a free-span of up to 80m when using cable towers, or up to 30m between standard supports.
Bruks Siwertell has hundreds of Tubulator installations worldwide, particularly serving the processed wood sector such as wood-processing plants, sawmills, paper mills and pellet production.
Innovative conveyor options
The Tubulator is often specified for niche applications, and in 2018 Bruks Siwertell introduced The Belt Conveyor into its portfolio, to offer customers a new type of air-cushion conveyor that could carry a wider variety of materials and incorporate features of both the Tubulator and conventional conveyor design.
Instead of using a pipe enclosure, like the Tubulator, The Belt Conveyor uses a formed pan to support the belt. A fully flanged cover makes it dust tight, protecting the environment and eliminating any material losses through spillage.
The shape of the pan has the same geometry of a 35-degree idler conveyor, but without the rollers, therefore it still meets the industry-standard calculations for the USA’s Conveyor Equipment Manufacturers Association (CEMA). Third-party components, like weigh-scales, metal detectors, magnets and material sensor areas, can all be incorporated into the design.
Like the Tubulator, The Belt Conveyor benefits from a modular design that can easily be shipped and constructed. Each 3m section of the belt has access to a common header of pressurized air, and under the carry-side pan is a 3m pressurized air enclosure system, otherwise known as a plenum. Air pressure sensors and flow meters along the length of the belt ensure the optimum amount of air is delivered for the weight of the given cargo, reducing running costs.
Delivering a commercial advantage
A notable example of a facility that uses both of these technologies is Canada’s Barrette-Chapais, at its 210,000 metric tons/year wood pellet production plant, Granule 777, in Quebec. The facility uses offcuts and wood waste residuals from sawmills in the production of biomass pellets.
Within Granule 777 is an air-supported conveyor system with a rated capacity of 800t/h for carrying wood pellets. It comprises a 100m-long The Belt Conveyor and a 250m-long Tubulator. The Belt Conveyor carries material from the facility’s two pellet storage domes, before transferring it to the Tubulator system which feeds it to the dock where the pellets are loaded onto bulk carriers bound for Europe.
The Tubulator employs Bruks Siwertell’s innovative suspension cable tower technology, reducing foundation requirements and minimizing construction costs. For this application, Bruks Siwertell was able to span 250m down to the dock over very difficult terrain. These long spans, up to 75m, are easily managed with the Tubulator and meant that only three cable tower supports over the entire length were used. This is also a downhill conveyor, so it is regenerative in nature, requiring a new braking system on the drive unit.
Fire risk is a serious concern in the dry bulk and wood-processing industries, and especially so when handling materials that are ultimately destined as fuel. But these materials have to be transferred and transported, and sometimes high-capacity traditional belt conveyors are the only practical option, but there are many opportunities, like Granule 777 notably demonstrates, where an alternative option could be considered, transforming fire risk, and offering much lower maintenance costs, without compromising on efficiency and performance.
PLEASE CONTACT US FOR MORE INFORMATION
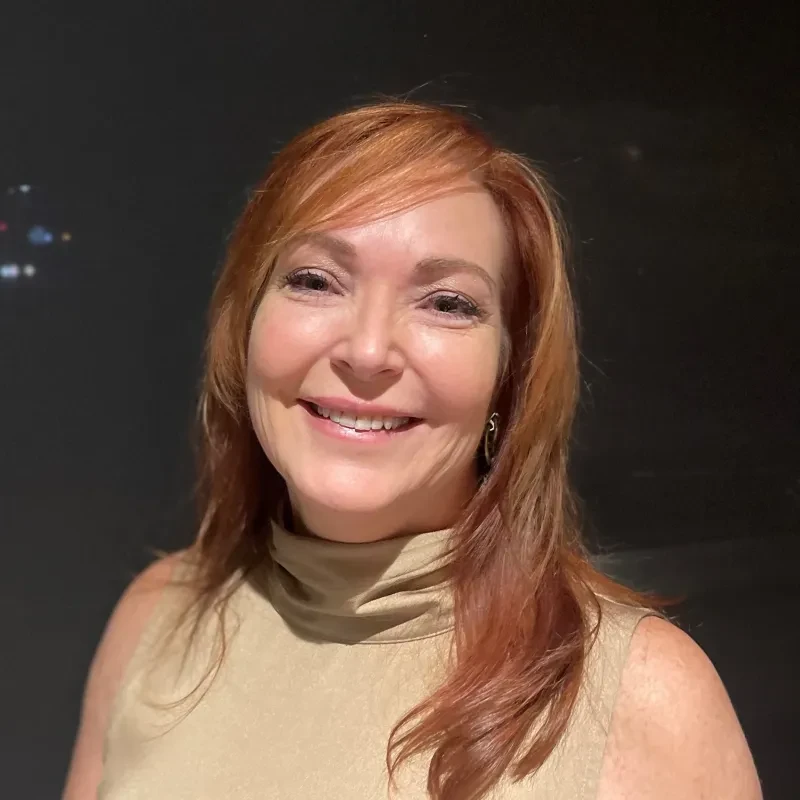