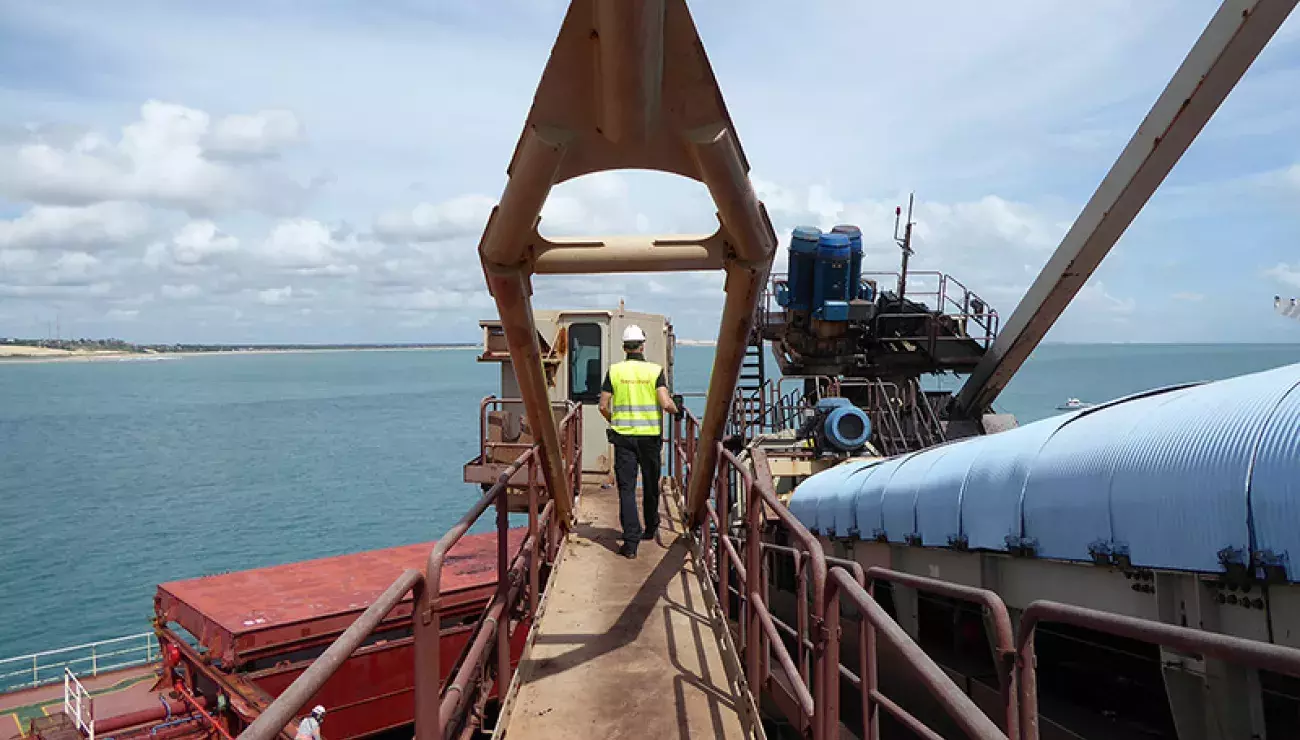
Experts at your service
23 Aug 2018Experienced surveyors deliver many benefits to customers; they can rapidly assess a machine and can often keep it up and running while waiting for parts, explains Örjan Westerberg, Siwertell surveyor with over a decade of service under his belt
Many operators of Siwertell equipment take their maintenance regimes seriously and either undertake service work themselves or call upon the original equipment manufacturer or third-party companies to help maintain their bulk handling equipment. This regular maintenance means that operators get to know their machines and how they respond, and any abnormal noise or vibration can therefore be quickly identified and evaluated.
So what advantages are available to an operator turning to the original equipment manufacturer for help with maintenance?
Efficient service decisions
The fundamental aim of our work is to ensure that our customers have a safe, efficient dry bulk handling system that they can rely on. The core of this work depends on our expertise. Siwertell surveyors are trained to very high standards and our lengthy experience of the entire Siwertell equipment range means that we can inform a customer about every aspect of their machine and make efficient decisions about its service.
Experience delivers many benefits to a customer during a service or inspection. Not only does it enable a surveyor to rapidly assess a system, but that surveyor can quickly determine its condition. It also means that we are often able to help a customer with temporary repairs that can keep a machine up and running until new spare parts arrive.
Parts that work mechanically close to each other need to be a perfect match. Genuine parts are very important as any specification discrepancies or overly-high wear rates, can affect the whole bulk handling operation. Original Siwertell parts can also be more easily inspected, serviced and replaced.
Preventing potential failures
All bulk handling equipment needs preventative maintenance. Expert service ensures that a machine is safe, as well as efficient. If maintenance is not followed up as per a schedule, there is a real risk that this will affect safety standards and damage equipment, potentially causing failure and ultimately stopping the entire unloading or loading process.
A service contract will keep the customer fully informed about the status of its Siwertell system, and for emergencies we also offer on-demand, reactive services.
Aside from safety, I believe that the most important role that regular maintenance plays is making sure that a machine and its parts have a long service life. This fundamentally affects an operator’s profits, so this has to be our concern also.
Keeping up with maintenance intervals ensures lifetime trouble-free cargo handling, and while there is no such thing as a good time for downtime, a regularly maintained Siwertell machine can still offer unbeatable performance after decades of continuous use.
Profile of a service engineer
Although two days are almost never the same for a service engineer, we pride ourselves on our customer dedication. We are the interface between the customer and Siwertell, so we not only represent our company, but also bear the responsibility of maintaining or bringing a machine into good working order, often to a tight deadline and sometimes under difficult conditions.
We start the day early to see what has come in overnight and once on site, we get organising.
A Siwertell surveyor supervises and manages projects and works out how repairs and servicing tasks are going to be efficiently achieved by the various work teams.
Days are often long as work needs to be completed and in some cases we work at night to avoid downtime, carrying out tasks such as aligning screw conveyors. Because we tend to work under these tight deadlines, it is crucial that we are efficient and pay close attention to detail.
If I think about the things that we must personally excel at to deliver service quality, then I believe these attributes must be patience, flexibility and the ability to effectively communicate even complicated concepts. It is essential that we help customers understand what is going on, clearly explain a problem and convey how it is going to be rectified.
Surveyors often have to deal with challenging situations, so patience in all situations is crucial. This is particularly evident in the field. Events are not always text-book, engineers often come across non-documented problems, and therefore they need to be flexible and inventive, using their toolkit to solve problems that arise in real-world situations. As the industry is constantly changing, an engineer’s training and knowledge must be ever-expanding too; we must be willing and able to learn new technologies and skills.
PLEASE CONTACT US FOR MORE INFORMATION
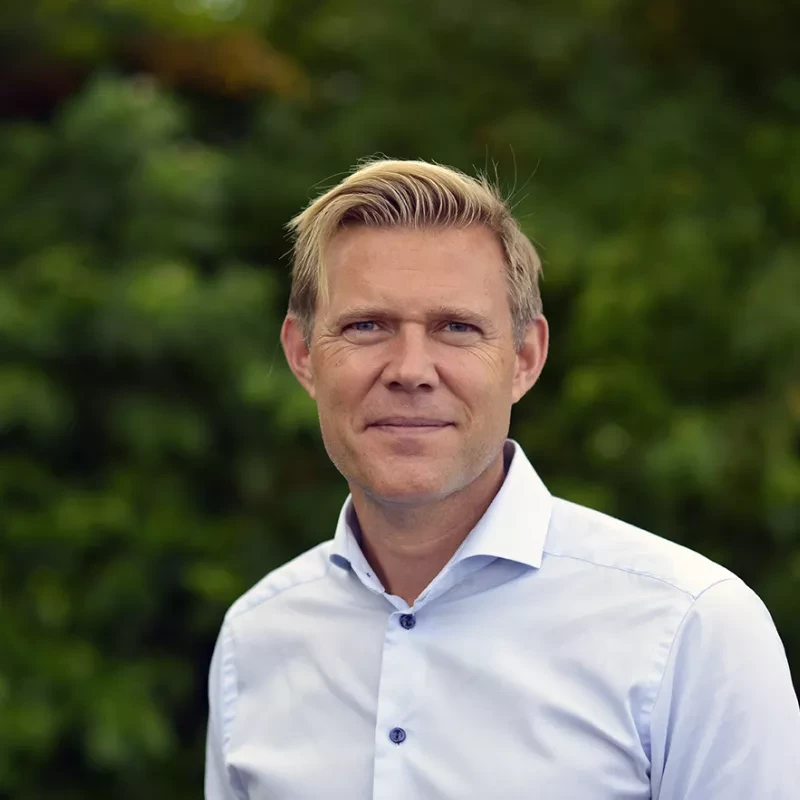
Share:
More Blogs
Previous:
Consign crushed grains to the pastNext:
Keeping the noise down