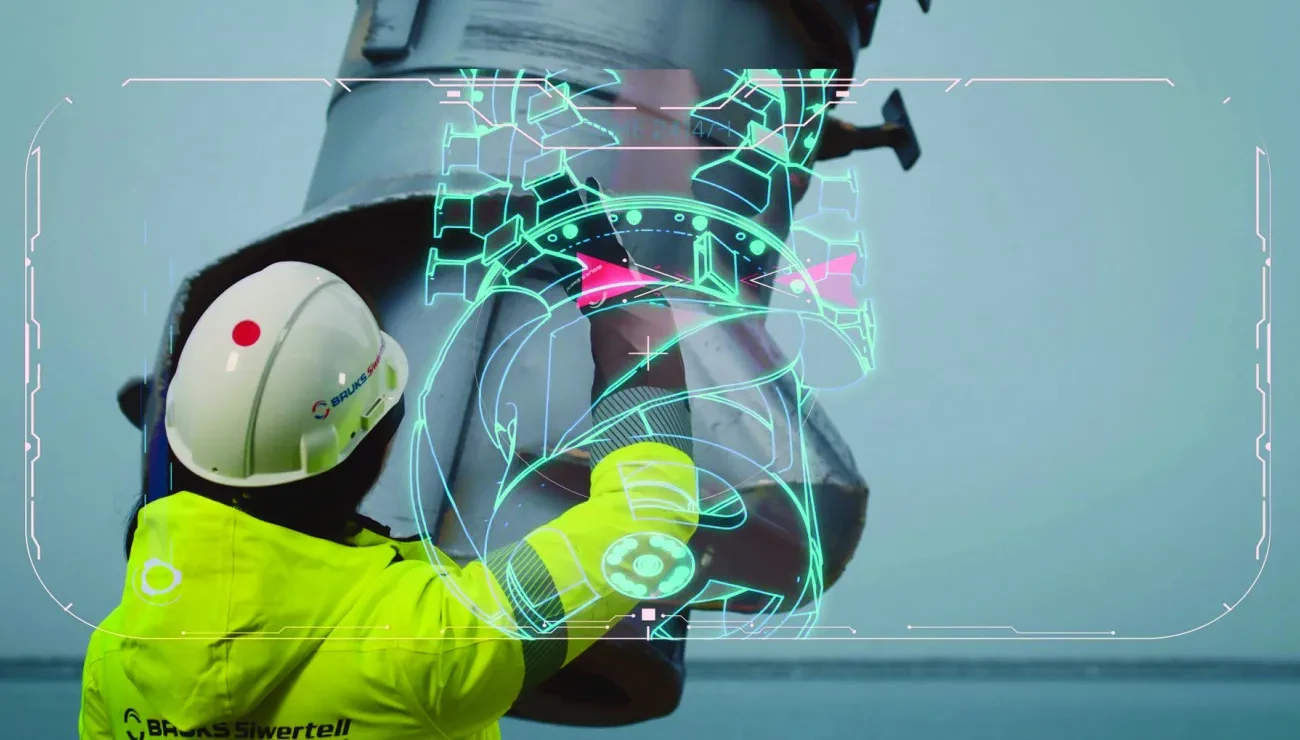
Early adopters set to ride the wave of digitalization gains
3 Feb 2025There are three good reasons why dry bulk handling operators should not shy away from digital advances: safety, cost-savings and market competitiveness. “There are a lot more, but these are key to highlight,” says Daniel Frostberg, Sales Director, Bruks Siwertell.
“The digital arena is developing at such a pace that if you blink for too long, things change, so how do operators combine new digital advances with mechanical systems that are designed to last for decades?
“Essentially, they have to look to a dry bulk handling equipment supplier that is already thinking steps ahead,” Frostberg continues. “There is no room for complacency in this market. We are ensuring that both new and existing customers can benefit from the application of information and operational technology as innovative as our actual equipment.
“Our digitalization strategy is integral to our equipment development programs, and our focus is on real-world gains,” Frostberg stresses.
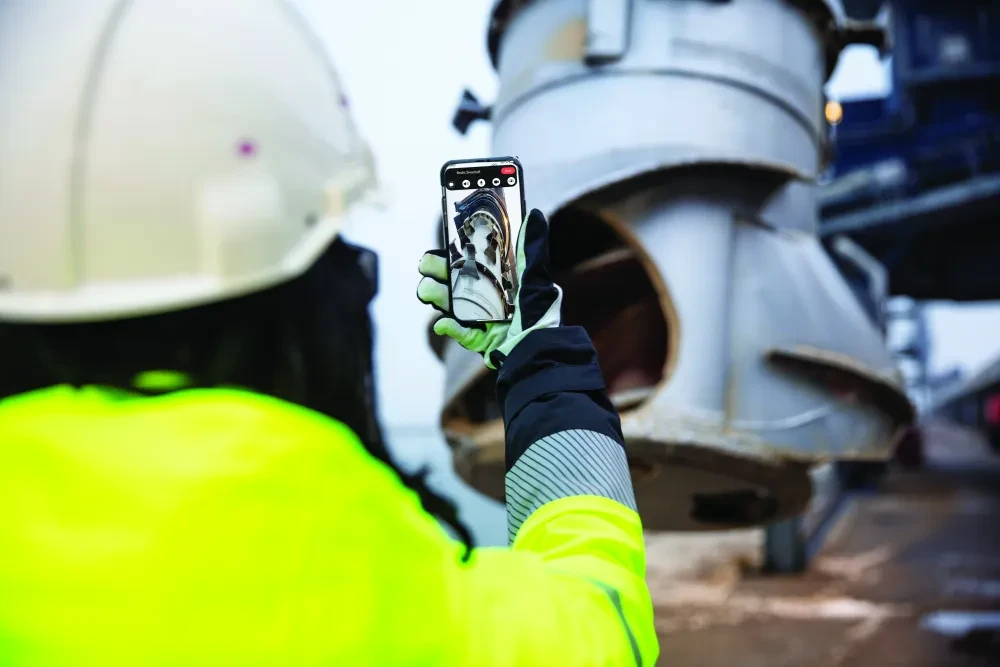
Working within the hatch
“We understand that hatch cover leaks account for around a third of large cargo claims by value, making this part of a ship critical to both vessel and dry bulk shipment integrity,” he explains. “Siwertell ship unloading and loading systems operate in this key area, with users skillfully loading and discharging layers of cargo throughout the hold, often working close to ship structures. Our ship unloaders can extend their reach beneath the hatch coaming, a feature that is central to their market-leading through-ship efficiency.”
The intensive use and importance of a bulk carrier’s hold opening is a frequently discussed industry topic, for example, a sector report from the UK P&I Club, notes that of 170 vessels inspected over a three-month period almost 50 percent presented with serious hatch cover related problems that would affect weathertightness, including knocks and dents to hatch coamings.
“Safety and operational performance, reduced insurance claims and the knock-on impact of equipment damage, are just some of the benefits that can be gained with the introduction of optional anti-collision systems on our dry bulk handling equipment,” says Frostberg.
“Laser-based anti-collision systems were developed several years ago, but more recently, we have introduced a radar-based anti-collision system. The use of radar means that even in challenging environmental conditions such as dust, fog, and snow, digital image generation is still possible.”
Both systems create a real-time 3D representation of the hold and cargo surface, including the identification of low-speed zones. When the vertical unloader arm, for example, approaches the hatch coaming and enters a low-speed zone, the anti-collision system slows the equipment’s movements for a more precise touch. If the system detects that a collision is imminent, it will stop the unloader’s movement entirely to prevent impact.
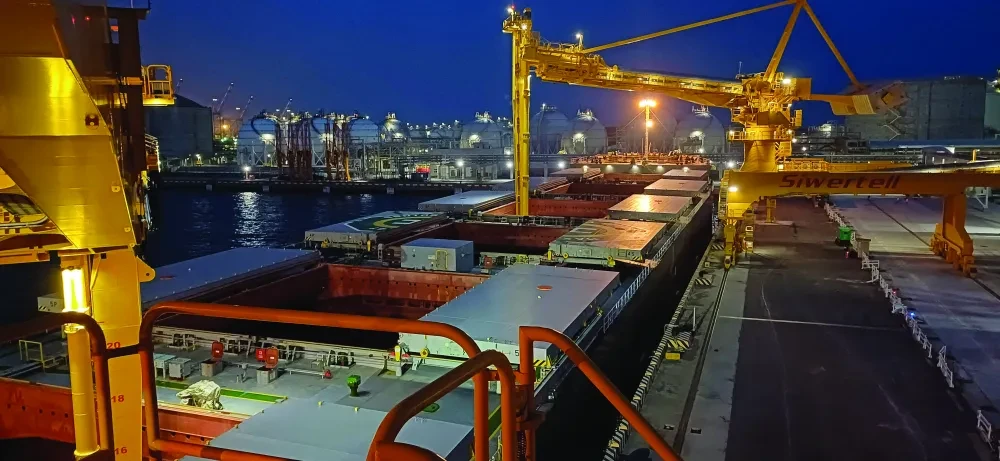
Getting closer to the edge
“This provides assurance that operators can confidently get closer to the edge of the hold, without impacts that could damage the unloader’s inlet feeder, or the ship’s hold or coamings, for example,” he notes.
Both the laser- and radar-based systems also enable semi-automatic unloading and loading. “When the anti-collision system is activated, along with the program for automatic speed reduction of movements; the PLC is able to take control of the movements and follow a pre-defined sequence. The system enables intelligent pathfinding, enhancing efficiency and environmental protection, but operations should always be supervised, at all times,” Frostberg says.
In semi-automatic unloading mode, the unloader’s counter-rotating inlet feeder is precisely positioned, maintaining best practice in terms of submersion level beneath the cargo surface. It also defines the optimal path for the vertical arm while minimizing overall movement. The system focuses on the areas with the most cargo, reducing the number of repositioning maneuvers required, and streamlining the unloading process. This ensures the surface of the cargo within the hold remains flat and consistent, maximizing through-ship efficiency and reducing the possibility of cargo avalanches within the hold.
The system also has a built-in threshold for torque on the inlet head, which reduces the speed of the screw conveyor should it exceed a pre-programmed limit. Likewise, if the force load on the vertical arm exceeds a pre-programmed value, slewing and luffing movements will be slowed to ensure the safety of the equipment. Apart from contributing positively to cargo throughput, this has the potential to significantly increase the lifespan of unloader wear parts, by eliminating strain on the components.
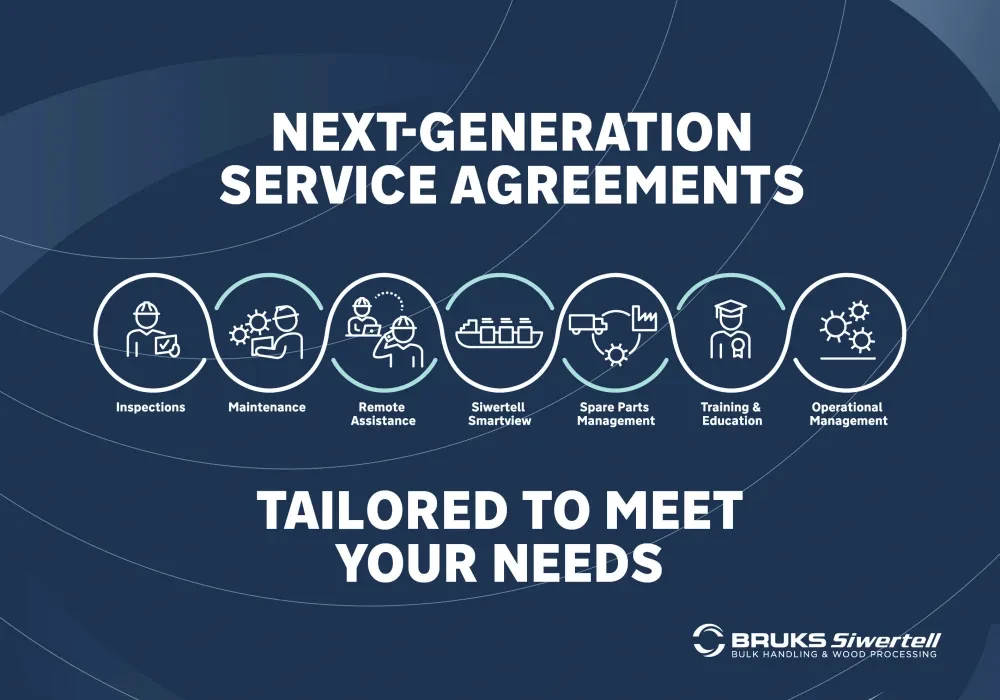
Leveraging digitalization in service
When support is needed, Bruks Siwertell has recently launched customizable, next-generation planned service agreements that include advanced digital tools. These are designed to enhance customer care, bring expert service quicker and closer to global installations, whilst minimizing maintenance costs and environmental impact.
Next-generation agreements can include remote connection to the equipment’s programmable logic controller (PLC) for easy troubleshooting, and Siwertell Smartview, which is a cloud-based industrial Internet of things (IIoT) system. Siwertell Smartview is being integrated into Siwertell dry bulk handling technology and can monitor real-time operational parameters such
as tons of material handled.
The agreements also allow customers to leverage the advantages of augmented reality (AR), which has the advantages of reducing service costs, while enabling operator personnel to participate more closely in the maintenance of their equipment. “Most people are familiar with virtual reality (VR), where a user can stand inside a virtual environment and interact with virtual objects, which does find use in industrial settings, for immersive training simulations, for example,” Frostberg explains. “Where AR differs, lies in the concept of blending reality, overlaying a layer of interactive virtual elements in someone’s visual field.
“Our AR glasses are equipped with a microphone and earpiece, forward facing camera, and a projector which allows elements to be displayed on the lens of the glasses, akin to the head-up display in a fighter pilot’s helmet,” he adds.
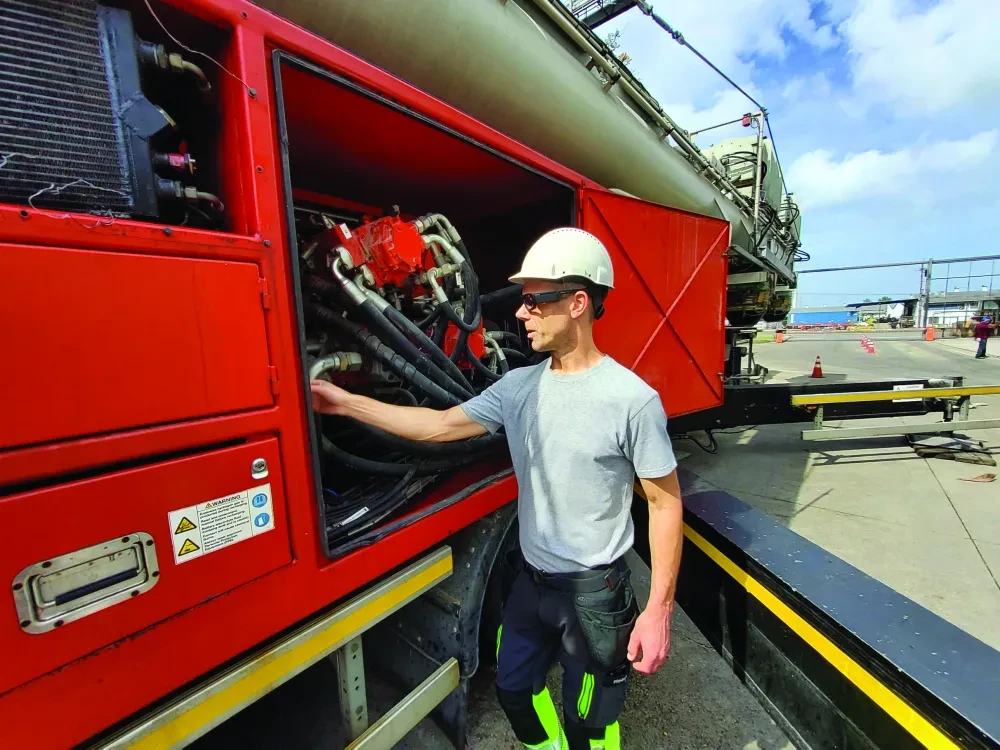
Instantly available expertise
“When personnel put on the glasses, they are connected with a Siwertell expert remotely and can be guided verbally through tasks, and with on-screen cues managed by the engineer. AR can make an operator’s personnel capable of more advanced in-situ engineering, and is increasingly popular, allowing operators to bring experts onboard at a time that suits their needs.
“The use of AR has huge benefits for maintenance operations, but beyond this for commissioning systems, especially when they are in challenging locations and Siwertell engineers cannot access them,” highlights Frostberg.
“We see AR-based maintenance and commissioning capabilities playing an increasingly important role across global business plans. We should all be concerned about reducing our scope 3 carbon emissions, those created by partners and supply chains, and envision that AR can be used to great effect in this arena. All our digitalization advances address real issues. We are only at the beginning of realizing the full potential of integrating digital technology into dry bulk handling solutions, and its promise of a new era in efficiency, safety, and sustainability,” Frostberg concludes.
PLEASE CONTACT US FOR MORE INFORMATION
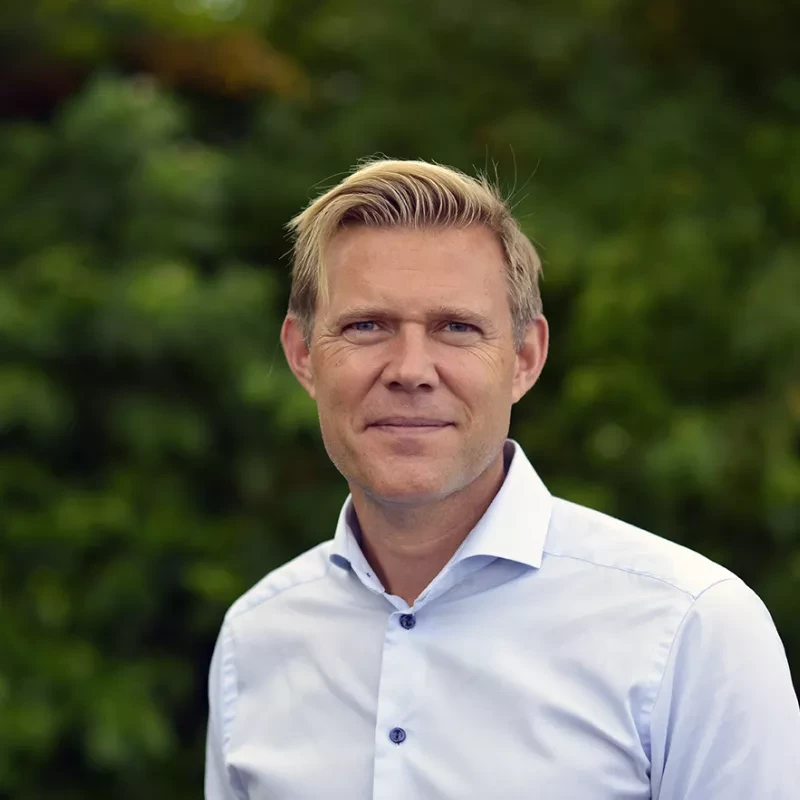