Anti-collision systems enable semi-automatic ship unloading
When Siwertell ship unloaders are fitted with optional anti-collision systems, it is possible to enable semi-automatic dry bulk material ship unloading.
Once the anti-collision system is activated, along with the program for automatically reducing the speed of movements, including traveling, slewing, luffing and pendulum, the dry bulk handling equipment’s programmable logic controller (PLC) is able to take control and follow a pre-defined sequence. The system enables intelligent pathfinding, enhancing efficiency, safety and environmental protection.
It is imperative that any equipment is supervised at all times whilst in semi-automatic unloading mode.
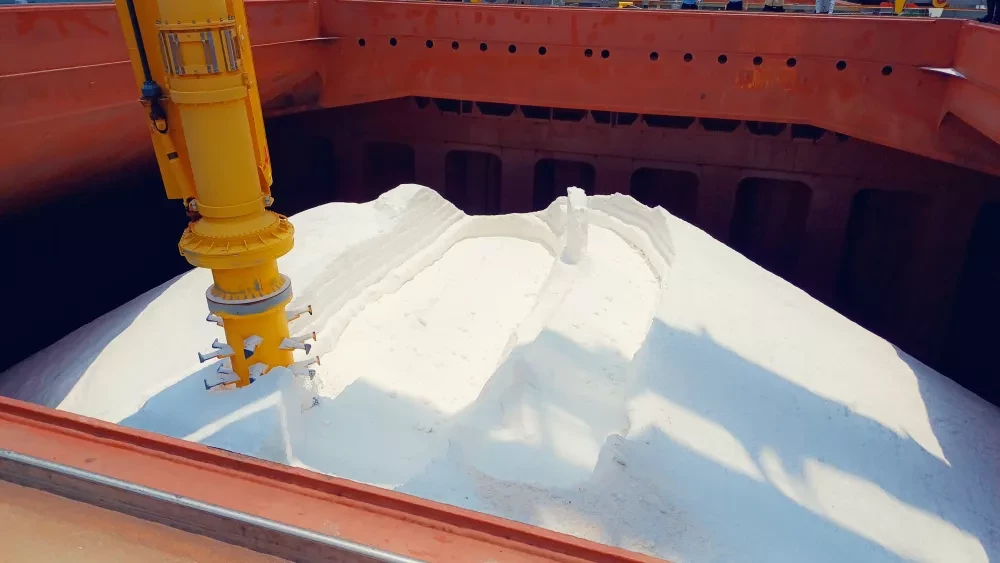
DESCRIPTION
In semi-automatic unloading mode, for example, the unloader’s counter-rotating inlet feeder is precisely positioned, maintaining best practice in terms of submersion level beneath the cargo surface. It also defines the optimal path for the vertical arm while minimizing overall movement.
The operator selects the unloading starting point, and then, with the system engaged, the number of repositioning maneuvers required are reduced, streamlining the unloading process. This ensures the surface of the cargo within the hold remains flat and consistent, maximizing through-ship efficiency and reducing the possibility of cargo avalanches within the hold, and therefore dust emissions.
The semi-automatic unloading system also has a built-in threshold for torque on the inlet head, which reduces the speed of the screw conveyor, should it exceed a pre-programmed limit. Likewise, if the force load on the vertical arm exceeds a pre-programmed value, slewing and luffing movements will be slowed to ensure the safety of the equipment. Apart from contributing positively to cargo throughput, this has the potential to significantly increase the lifespan of unloader wear parts, by eliminating strain on the components.
Automatic controls:
- If the operator’s capacity setting is lower than the set point, the speed of the movements will increase, if the capacity is higher, the speed will decrease.
- If the torque on the inlet head is higher than the set point, the speed on the movements will reduce until the torque is below the set value, then the speed off the movements will increase again.
- If the force load on the vertical arm is higher than the required value, the speed of the movements will reduce until the force is below the requested value, the speed of the movements will then increase again.
These automatic controls must be in operation to reduce the forces on and possible damage to the steel structure of the equipment. All settings are individually calibrated for each application based on equipment size, material handled, and the total loading or unloading capacity.
When semi-automatic mode is enabled, the low-speed area dictates a change in direction. The sequence is programmed to initially use the traveling motion, when the unloader arm, for example, reaches a low-speed zone on the left or right side, it relocates to a new row and starts traveling in the opposite direction. When a low-speed zone has been reached on either the sea-facing or shore-side, the arm relocates to a new level. The distance for new rows and levels are preset values that are set in the equipment’s human machine interface (HMI).
Parameters for semi-automatic unloading set in the HMI:
- Distance between rows
- Depth of each layer
- Length of horizontal arm
- Length of vertical arm
- Offset between hinges
Pausing operations
If the operator moves any joystick or turns the switch into pause mode, the sequence will be temporarily stopped. The operator can then adjust the unloader to another position or manually change the digging depth. Once finished, the operator can then continue the unloading sequence.
Changing direction
If the operator wants to change the active movement direction of the unloader, the traveling joystick can be moved in the opposite direction. It will then automatically stop and when the semi-automatic unloading mode is started again, the unloader starts moving in the opposite direction.
BENEFITS
Semi-automatic unloading offers a number of benefits. These include:
- improved operational efficiency
- improved cargo throughput
- increased jetty utilization rates
- improved profitability
- significantly increases the lifespan of wear parts
SCOPE OF SUPPLY
- anti-collision system
- programming